
Laser cutting | Info on laser technology
What is laser cutting?
Laser cutting is a thermal cutting process. A laser beam is used to melt or vaporize the material, which is blown away downwards by a gas stream immediately after it is created.
Laser cutting is divided into three different variants: Laser beam fusion cutting, laser beam flame cutting and laser beam sublimation cutting and is primarily used where, for example, metal and steel in relatively thin material thicknesses need to be cut with the highest precision and at the highest possible processing speed. In addition to a wide variety of metals, other different materials such as wood or plastic can also be processed with this technology at high cutting speeds.
- What is laser cutting?
- Advantages of laser cutting
- Everything at a glance
- Latest news
- Where is laser cutting used?
- Pros and cons of laser cutting
- Solid-state laser compared to CO2 laser
- Advantages and disadvantages of the fiber laser
- Laser cutting process
- Cutting range
- Laser components
- Laser technology
- Components processed with laser
- Expert interview
- FAQ
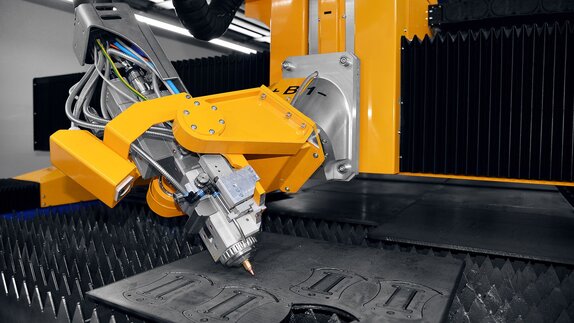
Everything at a glance
- Laser cutting can be used to cut parts from a wide variety of materials, such as metal, wood or rubber, with very high precision.
- To date, laser cutting technology has mainly been used in the smaller and medium thickness range – however, the continuous development of laser technology is making it possible to process ever thicker materials.
- There are different types of high-power lasers – the most commonly used are CO2 lasers (gas lasers) and fiber lasers (solid-state lasers).
- Decisive advantages of the fiber laser are the cost savings for operation and maintenance as well as highly effective laser sources.
- The laser consists of three basic parts: Energy source, laser medium, resonator.
- Laser cutting is used in various industries, such as the automotive industry, mechanical engineering and precision mechanics.
Laser cutting machines from MicroStep Europa
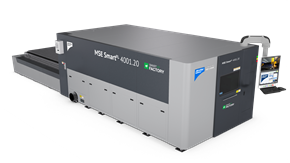
MSE SmartFL
High Power: The MSE SmartFL is a powerful yet cost-effective system for high-quality 2D laser cutting. The series can be equipped with laser sources up to 60 kW and is already ideally equipped for the production of the future!
MSE SmartFL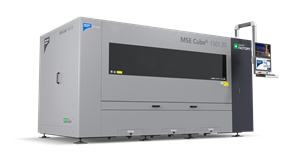
MSE CubeFL
The MSE CubeFL combines maximum precision and efficiency with minimum space requirements. The series can be equipped with laser sources up to 12 kW and is the ideal solution for compact laser cutting.
MSE CubeFL
MSE TubeFL
High-quality 2D and 3D laser cutting of pipes, profiles and beams. With the MSE TubeFL, the finest contours and openings as well as precise bevel cuts can be realized. Depending on the version, the system has an extremely high degree of automation.
MSE TubeFL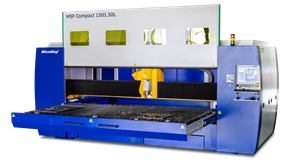
MSF Compact
The MSF Compact combines precise 2D laser cutting with a compact design. The series impresses above all with its small footprint and the usual high cutting quality of the laser cutting system. A manually extractable cutting table enables simple and uncomplicated loading and unloading.
MSF Compact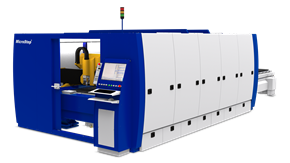
MSF Cut
Reliable and process-safe: this is what characterizes the MSF Cut series. The efficient production assistant is the ideal solution for standard 2D tasks and can be equipped with laser sources up to 15 kW.
MSF Cut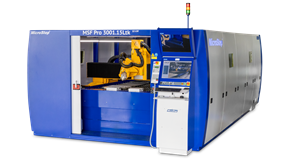
MSF Pro
High speed and flexibility in 3D: the precise all-rounder MSF Pro is a pioneer among laser cutting machines in terms of multifunctionality. No other laser system offers such a high degree of vertical integration for sheet metal processing. Pipes and profiles can optionally also be cut.
MSF Pro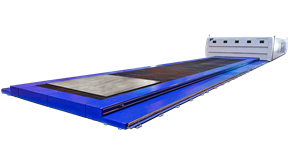
MSF Max
The MSF Max is the giant among laser cutting systems. Developed for processing large-format sheet metal for shipbuilding, it enables precise 3D high-speed processing of flat material. Thanks to the traveling safety cabin, a working area of up to 50 m in length and 6 m in width is available for the laser machine.
MSF Max
MSF Pipe
The pipe and profile specialist: As an option to the high-precision 2D and 3D processing of pipes and profiles up to 12 meters in length, the MSF Pipe can be expanded to include sheet metal processing.
MSF Pipe
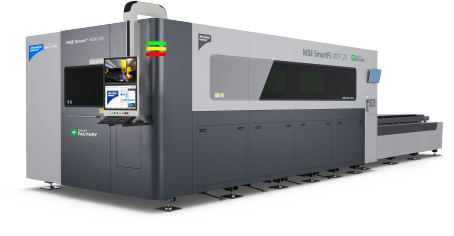
Laser cutting machines are the right solution when it comes to precise cutting with minimum time expenditure. State-of-the-art laser cutting systems combine precision, speed and maximum multifunctionality.
Where is laser cutting used?
Due to the highly focused laser radiation and the high traverse speed, the thermal input into the material is limited to a narrowly defined area. This means that the components do not deform as much during laser cutting, which results in very high precision.
Laser cutting is mainly used in the automotive industry, in precision engineering, the semiconductor industry or by manufacturers of optical instruments. This cutting technology is used in all industrial sectors dealing with metalworking and cutting technology in general. The materials to be processed range from rubber to diamond stone. This cutting technology is mainly used for steel sheets of all types and grades, for stainless steel sheets and for non-ferrous metals such as aluminium and brass. Other suitable materials for laser cutting are titanium, plexiglass or acrylic glass, wood or bronze.
Laser cutting technology is predestined for use on a CNC cutting system. Modern laser cutting systems combine the advantages of the laser with the possibility of multifunctional processing on a CNC machine. Today's CNC lasers offer a wide range of configuration options for processing sheet metal, pipes and profiles. Thus cutting, drilling, tapping, countersinking, marking or bevel cutting – for example for weld edge preparation – is possible on one cutting machine.
Pro laser cutting
- High precision and quality when cutting different materials
- Cutting of small holes, acute angles and complex contours
- High processing speed in the thin sheet area enables the processing of large quantities
- Very good automation capability
- Extremely low heat input, virtually no distortion of the workpieces
- Very small kerf width
Contra laser cutting
- Not all materials can be cut with a laser
- Material grades and surface properties can influence the cutting result
- Unsuitable if no thermal impact on the material is permitted
- Relatively high start-up costs depending on the machine design
Solid-state laser compared to CO2 laser
There are different versions of focused high-power lasers that are used in laser beam cutting. The most frequently used are the CO2 laser (a gas laser) or the fiber laser (solid-state laser). The CO2 laser is the more established cutting technology and has been used successfully for many decades. For some years now, however, the gas laser has been increasingly competing with the fiber laser. This special form of solid-state laser is particularly convincing due to its high efficiency compared to the well-known cutting system. The Nd:YAG laser, which like the fiber laser belongs to the group of solid-state lasers, is also becoming increasingly important in laser cutting. However, it is mainly used for micro-drilling and welding.
Compared to CO2 lasers (carbon dioxide lasers), fiber lasers have significantly lower operating and maintenance costs. Thanks to the most modern and sophisticated technologies, they are at least on par with established lasers in terms of precision with different material thicknesses. However, the fiber laser is being used more and more frequently in laser cutting technology and is competing with the CO2 laser. Compared to the still dominant CO2 lasers, solid-state fiber lasers score with a number of strengths – first and foremost with the cost factor. Thanks to modern and sophisticated technologies, even supposed weaknesses can be eliminated. This makes the fiber laser a more than attractive alternative to the existing system.
The CO2 lasers belong to the group of gas lasers and are also called carbon dioxide lasers or carbon dioxide lasers. They are based on a carbon dioxide gas mixture, which is electrically excited. CO2 lasers score with a very good cutting quality and are mainly used for metallic materials but also for non-metallic materials like wood, textiles, plastics, foils, acrylic, glass, paper and leather. In contrast to fiber lasers, carbon dioxide lasers can also be used to process even thicker stainless steel sheets with good cutting quality – even at high feeding speeds. The CO2 laser is the established laser type that has been used for decades and enables high quality with a wide range of material thicknesses. The disadvantage is the comparatively high operating and maintenance costs for the laser gases as well as for consumables working in the laser source. The efficiency is around 10 percent.
The fiber laser, which is a special form of solid-state laser, is on the advance. It scores with its cost-effectiveness, low operating costs and long service life of the wear parts. Thanks to a beam wavelength that is ten times shorter than that of the CO2 laser, the fiber laser is also suitable for cutting materials that are otherwise difficult or impossible for the CO2 laser to cut, especially non-ferrous metals (NF metals). For higher material thicknesses, a variable focus diameter is necessary to compete with the cutting quality of the carbon dioxide laser. The laser sources are also highly effective and consume significantly less input current for the same power. The so-called socket efficiency of the fiber laser is about 40 percent.
Like fiber lasers, Nd:YAG lasers are solid-state lasers and are also known as crystal lasers or vanadate lasers. Nd:YAG laser is the abbreviation for neodymium-doped yttrium-aluminum-garnet laser. A YAG crystal is used as host crystal. This technology is used less for laser cutting, but rather for engraving, welding and micro-drilling. Metals, metals with coatings and plastics are processed with this solid-state laser. In contrast to fiber lasers, however, this cutting technology has a high wearing of pump diodes. In addition, the lifetime of the neodymium-doped YAG crystal is shorter than that of the fiber laser.
Advantages and disadvantages of the fiber laser
The decisive advantage of fiber lasers is obvious: With this solid-state laser, up to half the costs for operation and maintenance of the CNC laser cutting system can be saved. This fact is of course significant for the increasing popularity of this technology. Not only does this cutting technology require no gases for beam paths, but the laser sources are also highly effective: the nominal power of a 4 kW fiber laser (with a cooling device) is about 14 kW compared to 57 kW for a 4 kW-CO2 laser. Several maintenance costs of a carbon dioxide laser are also eliminated: the costs that depend on the life cycle of the discharge tubes or on the turbine in the cooling circuit of the laser gases or the vacuum pump. These account for an enormous part of the comparatively high maintenance costs of the CO2 laser.
There are, however, other physical characteristics that are advantageous to the fiber laser: Thanks to a beam wavelength that is ten times shorter, fiber lasers can achieve a smaller beam diameter (i.e. a higher energy density) at the center of the cutting head – thus thin material can be cut faster than with the CO2 laser. However, the thicker the material, the more this characteristic becomes a disadvantage due to the very thin kerf and a resulting risk of kerf filling with the discharge material (slag).
It is therefore necessary to have a larger focus diameter for cutting thicker materials. In the interest of industrial use, the laser cutting head should be able to change the focus diameter automatically – without the intervention of operating personnel, e.g. by manually changing lenses. In order to meet the versatile requirements of the market – i.e. to enable cutting over the entire material thickness range – MicroStep uses laser cutting heads from leading manufacturers such as Highyag, Precitec and Thermacut, tailored to the customers' needs, for maximum productivity in 2D cutting and bevel cutting of sheet metal, pipes or profiles. Due to the possible fully automatic control of focus position and focus diameter in combination with fast focus movements on the material, materials up to 50 mm thickness and significantly more can be processed with a single fiber laser, depending on the laser source. The cutting heads do not require changing the ocular lens – only the cleaning of the protective glass is part of the operator's tasks.
The quality of fiber laser technology has improved considerably in recent years. Depending on the laser power and material, modern fibre lasers can now cut materials up to 50 mm thick and far beyond. For example, a 20 kW laser enables the precise cutting of mild steel with a thickness of more than 40 mm, stainless steel up to 40 mm, aluminium up to 40 mm, brass up to 25 mm and copper up to 15 mm. However, the available laser power is constantly increasing.
Laser cutting process
- Focusing of the laser beam using optical elements within the cutting head
- Piercing process: Punctiform penetration of the material to be cut
- Start of the cutting process: Absorption of the beam at the cutting front, creating a melt
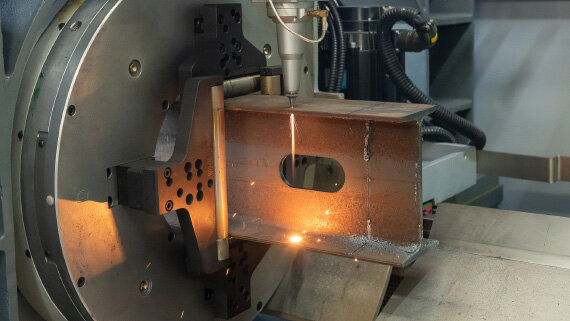
Cutting range
Laser cutting technology has undergone enormous development in recent years. It is still used mainly in the smaller and smallest thickness range. The cutting range in modern laser cutting is from 0.5 to 50 mm and significantly more, depending on the material and the power of the beam source, with optimum environmental variables.
Laser components
A laser consists of three basic parts:
- Energy source
- Laser medium
- Resonator
The energy source, also called pump or pump source, has the task of "pumping" energy into the system. This creates a population inversion. The source can be electrical, but also light, heat or even another laser. Sufficient energy must be transferred into the laser medium to achieve population inversion – this means that the number of particles in the excited state must be higher than the number of particles in the ground state. The light of the laser is produced by spontaneous emissium in the excited laser medium and is amplified by stimulated emission. The resonator consists of two curved mirrors, one of which is partially transparent. Radiation originating from spontaneous emission and having the correct wavelength, phase and direction is reflected back and forth between them. Part of the radiation escapes as a focused laser beam through the partially transparent mirror and the other part is reflected back for further amplification.
Laser technology
In laser cutting, also known as laser beam cutting or CNC laser cutting, the focused laser beam is absorbed at the cutting front and thus generates a melt and metal vapour which is blown away downwards by a gas stream immediately after it is generated. A cutting gap remains, which can take on any contours depending on the feed direction of the laser beam.
You might also be interested in:
What are the advantages of laser cutting compared to plasma cutting?
Lasers can cut thin materials much faster and with much higher precision than is possible with plasma. Laser cuts are generally nearly vertical and have a much smaller heat-affected zone compared to plasma. Sharp corners, acute angles and complex contours can be cut, as can holes or inner contours with a ratio far smaller than 1 (hole diameter: material thickness).
What are the main components of a fiber laser cutting system?
The main components of a fiber laser cutting system are:
- Gantry system with at least 3 controlled axes (xyz)
- Laser beam source with beam guidance (processing fiber)
- Laser cutting head
- Extraction system with filter technology
- Suitable safety equipment (safety cabin, circuit breaker, etc.)
- Gases for the cutting process (mostly N2, O2 or air)
Which geometries and contours can be cut with laser cutting?
There are virtually no limits to the geometries that can be achieved with laser cutting. Small holes, narrow webs, acute-angled geometries, rounded or curved contours can always be cut with almost perfect right-angled cutting edges. The limiting factor is the optical design of the system, the system itself, and the laser cutting process used.
Which other cutting processes can be combined with laser cutting?
In principle, combinations with all CNC-controllable cutting processes are conceivable (plasma, oxyfuel, waterjet), but there are only a few combinations that have actually been implemented industrially. The reason for this usually lies in the basic properties of the respective cutting processes. For example, a waterjet cutting system requires a water basin, which is disruptive for a laser cutting system, and so on. The use of a water mist in laser cutting, on the other hand, is a well-known way of cooling the material during the cutting process.
Which materials and material thicknesses are suitable for laser cutting?
In todaya’s metal industry, a wide range of different materials (mild steel, stainless steel, aluminum, high-alloy steels, brass, copper, etc.) are cut. The use of beam sources with ever higher laser powers makes it possible to cut even greater meterial thicknesses. High-power laser sources can therefore also be used to cut 50 mm and more. The main area of application for laser cutting systems is in a material thickness range from 1 mm to 25 mm.
Which cutting widths are possible with laser cutting?
The cutting width or the achievable kerf depends on the design of the optical system and the cutting process used (laser beam fusion cutting, laser beam flame cutting and laser beam sublimation cutting). In industrial cutting of metallic sheets, the cutting kerfs are usually between 0.1mm and 2mm.
Which cutting speeds can be achieved with laser cutting?
The achievable cutting speeds in laser cutting are essentially dependent on the laser power and cutting process used. In general, the thicker the material to be cut, the lower the maximum attainable cutting speed. In the thin sheet range (1mm), speeds of up to about 100m/min (laser beam fusion cutting) are possible with the laser cutting systems available today. At 20mm, the speed is significantly lower at about 1m/min (laser flame cutting).
How powerful (in kW) does a laser need to be to cut metal?
With an appropriate configuration of the cutting system, it is already possible to cut thin metallic materials with far less than 100W. Laser cutting systems used in industry today for cutting metal sheets are on average equipped with beam sources having a laser power between 1 and 6kW. The maximum laser power currently used for cutting is around 20kW.
Which materials are unsuitable for laser cutting?
In principle, materials with absorption characteristics that are too low for the respective wavelength of the laser are unsuitable for cutting. Thus, wood and plexiglass on the one hand can be cut with CO2 lasers but not with fiber lasers. On the other hand, it is possible to cut copper and brass with fiber lasers, which is not possible or only with difficulty with CO2 lasers. Also unsuitable for laser cutting are materials that produce toxic dusts and gases during cutting.
What is important to consider for laser cutting of steel?
The cutting result on a laser system depends to a large extent on the material properties of the steel. Significant influence on the cutting quality have material-specific properties such as: alloying elements (carbon, zinc, magnesium, nickel, silicon and chromium), microstructure (graininess of the structure), material surface (e.g. oiled, pickled, scale layer), surface treatment (foil, layers of zinc, paint or primer). The special material properties of the respective steel can have a positive but also a negative influence on the cutting result and thus on the cut edge.
What is the difference between oxyfuel flame cutting and laser flame cutting?
During laser flame cutting, the heat-affected zone at the cut edge is significantly smaller so that a change in the microstructure of the cut edge area is also much smaller. Depending on the thickness of the material cut, this range is a few tenths. Material distortion due to the cutting process can be almost completely ruled out with the laser. The cut edge is burr-free and vertical with laser flame cutting; almost any contour can be cut with contour accuracy (without rounding). Due to the fact that ever greater laser power is being used for laser flame cutting, the material thickness limit up to which laser flame cutting is usually used is also shifting. Whereas it used to be 30 mm, material thicknesses of 40 mm or 50 mm are now possible. Oxyfuel flame cutting is used from a material thickness of 30 mm.
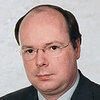
is an application engineer for laser technology at MicroStep Europa GmbH. The technologist has been at the heart of the market for decades and is passionate about the further development of laser cutting technology. In various roles, he has played a key role in ensuring that MicroStep can now offer an impressive portfolio of solutions in the field of laser cutting technology.
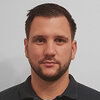
has been working in the Service & Support department at MicroStep Europa since 2016. The trained and qualified metalworker lives for preparing customers for their technology and helping them to get the most out of their system every day. He is one of the in-house specialists in laser cutting technology and takes care of the entire range of technical and customer-related tasks – from commissioning and training to demonstrations and consultations at exhibitions.