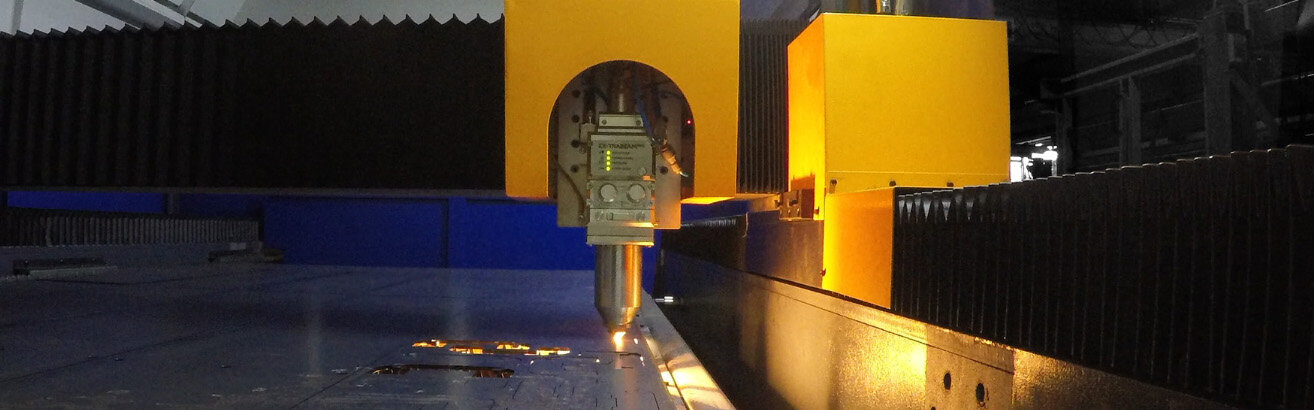
Sheet metal laser cutting and bending | Combined solution from MicroStep Europa
What does sheet metal lasering and bending mean?
Various work steps are necessary in metalworking to produce precise components from sheet metal. The sheet metal is often bent into shape using a laser after it has been cut to size:
- Sheet metal laser cutting: In this cutting process, a laser beam is used to cut the sheet metal. The laser heats the material to such an extent that it melts or vaporizes, resulting in precise cuts. A key advantage of laser cutting, particularly with thinner sheet thicknesses, is the ability to achieve precise cutting edges at comparatively high processing speeds. In addition, complex shapes and geometries can be cut from different types of sheet metal.
- Sheet metal bending: During subsequent bending, the cut sheet metal is bent into a desired shape using a press brake. Bending makes it possible to bend sheet metal parts into specific angles or shapes that are required for constructions or products.
Advantages of the combined solution: laser cutting system and press brake
An in-house combination of laser cutting system and press brake offers numerous advantages for processing customized sheet metal parts. On the one hand, laser cutting enables very precise cuts to be made without time-consuming reworking. Using the press brake, these precisely cut parts can then be bent into defined angles and shapes, which ensures precise and high-quality end products. In addition, by combining both processes in one company, sheet metal processing can be carried out more holistically and there is no need to rely on external service providers for cutting and/or bending. This allows companies to react much more flexibly to customer requirements, significantly expand their value chain and make themselves more competitive as a result. Both laser cutting and bending enable a wide range of material types and thicknesses to be processed, allowing complex, versatile and intricate components to be created in a single work process.
Applications and industries for the laser and bending process
The laser and bending process (laser cutting and bending) is versatile and enables the production of complex metal components with precise shapes and high surface quality. They are therefore used in a wide range of industries and for various applications, including
- Mechanical engineering: production of precision machine parts, housings, cladding and fastening elements
- Automotive industry: production of car body parts, exhaust systems, brackets and interior trims
- Aerospace: production of aircraft parts, structural components and brackets that have to be extremely light and stable
- Construction industry: production of façade cladding, support structures, stairs, railings and roof components
- Electronics industry: production of housings for electronic devices, control cabinets and mounting plates
- Furniture and design industry: production of metal furniture, lamps, shelves and decorative elements
- Agricultural machinery: production of components for tractors and agricultural equipment
- Energy technology: production of components for wind turbines, solar systems and energy transport systems
- Shipbuilding: production of ship components such as reinforcements, panels and structures
- Advertising technology: production of signs, logos, lettering and displays made of metal
Why MicroStep Europa is the best choice for a combined solution
The combination of a laser cutting system and a press brake from MicroStep Europa is a perfect duo. Thanks to IndustryFusion-X, the systems are already well equipped for the digitalized and networked production of the future. In addition, you benefit from the first-class service and support of MicroStep Europa GmbH with both systems.
You might also be interested in:
FAQ about sheet metal lasering and bending
What does “sheet metal laser cutting and bending” mean?
“Sheet metal laser cutting and bending” describes two key steps in sheet metal processing. In sheet metal laser cutting, a sheet is precisely cut using a laser beam. In the subsequent sheet metal bending process, the sheet metal is bent into the desired shape using a press brake. These two steps are often combined to produce precisely fitting components for various industries.
How precise is the laser cutting and bending of sheet metal?
Sheet metal laser cutting and bending with modern technology from MicroStep Europa is extremely precise. The accuracy of both processes depends on several factors, such as the material and the thickness of the sheet metal. Laser technology is also suitable for fine cuts and complex shapes, for example, and is particularly impressive in the thin sheet metal sector thanks to its high precision and speed. Precise cutting simplifies the subsequent bending process and therefore increases the quality of the end product.
Which industries benefit most from sheet metal laser cutting and bending technologies?
Sheet metal laser processing and bending technologies enable the precise, flexible and cost-effective production of complex components and are used in particular in industries with high demands on precision, stability and repeatability. These include, among others, the automotive industry, mechanical engineering, aerospace and the construction industry.
What role does software play in the control of laser cutting systems and press brakes?
The software plays a central role in the control of laser cutting systems and press brakes. Systems from MicroStep Europa are equipped with user-friendly and highly functional software. In the areas of laser cutting and bending, we recommend programming software from the renowned companies ProFirst and Libellula, among others: This offers smart solutions for the perfect interaction of all systems when cutting sheet metal, pipes, profiles and beams as well as when bending components.
What safety measures must be observed when lasering and bending sheet metal?
When sheet metal laser cutting and bending, there are a number of safety measures that ensure both the protection of employees and the safe operation of the machines. Laser cutting systems from MicroStep Europa are always equipped with appropriate safety equipment (e.g. safety cabin, safety window, safety switch) to protect workers from the dangers of fast-moving parts and any laser radiation. There is a risk of crushing and injury when bending. Press brakes from MicroStep Europa are therefore always equipped with a highly dynamic safety feature – a visible laser barrier.
Are there training courses for the operation of laser cutting systems and press brakes?
In order to develop a sound understanding of the operation of laser cutting systems and press brakes, MicroStep Europa offers both general technology training courses and workshops that are tailored precisely to the customer's needs.
What maintenance work is required on laser cutting systems and press brakes?
Regular maintenance work on laser cutting systems and press brakes is crucial in order to maintain the performance, precision and service life of the machines in the long term. This includes checking for worn or damaged components and tools or checking the safety systems and settings. Well-performed maintenance by MicroStep Europa helps to prevent unplanned downtime and ensure operator safety. The members of the Service & Support team are on hand with their many years of expertise, both via remote maintenance and on site.
What warranty and services does MicroStep Europa offer for its laser cutting systems and press brakes?
MicroStep Europa offers its customers an extensive service and support network throughout the D/A/CH region to get the most out of their laser cutting systems and press brakes! MicroStep Europa's services are characterized by competent and well-trained contact persons, fast response times and excellent wear and spare parts availability.
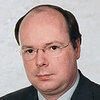
is an application engineer for laser technology at MicroStep Europa GmbH. The technologist has been at the heart of the market for decades and is passionate about the further development of laser cutting technology. In various roles, he has played a key role in ensuring that MicroStep can now offer an impressive portfolio of solutions in the field of laser cutting technology.