Increasing production with automation solutions

Automation technologies are an important factor in creating efficient production processes. With suitable material handling systems, for example, the utilization and, as a result, the output of a processing machine can be maximized.
Automation solutions from MicroStep Europa
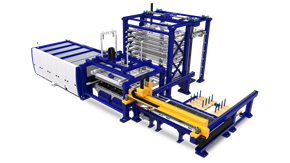
MSLoad, MSTower, MSSort
Reliable technologies: Storage, loading and
unloading of sheets l Sorting of cut parts
- Sheet processing
- Material handling
- Plasma
- Laser
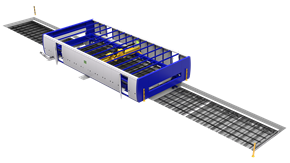
MSLoop
Multiplier for processing
of sheet metal
- Sheet processing
- Material handling
- Plasma
- Laser
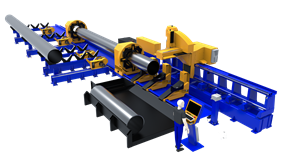
MSFeed
Automated loading and unloading of
pipes, profiles and beams
- Pipe & Profile processing
- Beam processing
- Material handling
- Plasma
- Laser
Advantages of automation solutions
- Reduction of heavy physical or monotonous work for the employees
- Time saving during loading and unloading
- Increase in machine utilization and higher output capacity
- Increase of the production quantity
- Reduction of unit costs e.g. by saving on personnel costs
- Homogenization and, if necessary, improvement of the product quality
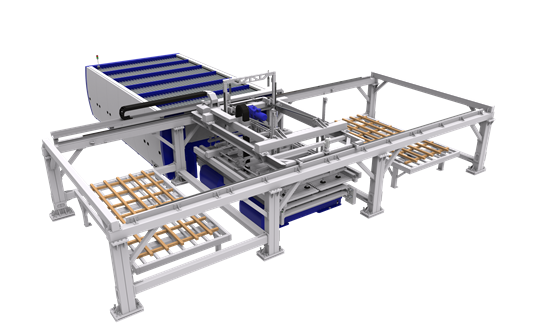
Up to date
With our newsletter you will be informed about all the latest novelties.
Automation at MicroStep
Origins of MicroStep in the fields of control and automation have been organically present in its activities and helped shape the product portfolio already since the early days, when the company was designing its first CNC system. The idea of minimizing and automating material manipulation via multifunctionality and integration of handling equipment into the cutting machines was understood as a logical step towards cost reduction and saving of production time. In line with these requirements, MicroStep developed and implemented a number of automation solutions and machine-to-machine interfaces, integrating several cutting machines and automated material handling units into larger production systems, especially in large-scale production. The universal and modular nature of MicroStep's products lays groundwork for future industrial interoperability.
In essence, MicroStep offers a modular solution concept for the processing of metals (cutting/drilling/marking) as well as for material handling. This is customized to the actual space conditions of the customer and integrated into his production workflow. Cutting systems can be extended by various options for material loading as well as technologies for automatic unloading of large and small components and precise sorting of the latter.
Available options include shuttle tables, fork feed systems, chain and belt conveyors, cutting tables with built-in rollers or cutting tables combined with load manipulators that transport material using vacuum or magnetic lifters. These solutions are developed and manufactured in-house at MicroStep. Our engineers work closely with the departments of our customers to achieve the best possible optimization of the system functions, the control software and the production flow.
In addition, many customers rely on MicroStep's expertise and wealth of experience in networking cutting systems with handling technology and third-party storage solutions (automatic cranes, sorting manipulators, storage towers). MicroStep owes this to a unique selling point: the development and design of machines, control systems and CAM software are all under one roof. This means that special solutions can be implemented more efficiently - our own teams of specialists design the tailor-made systems regarding modularity, interoperability and integration requirements.
MicroStep recognized the trend towards automation and digitalization early on and can rely on great expertise in both areas. Find out more about some of our numerous reference projects below: