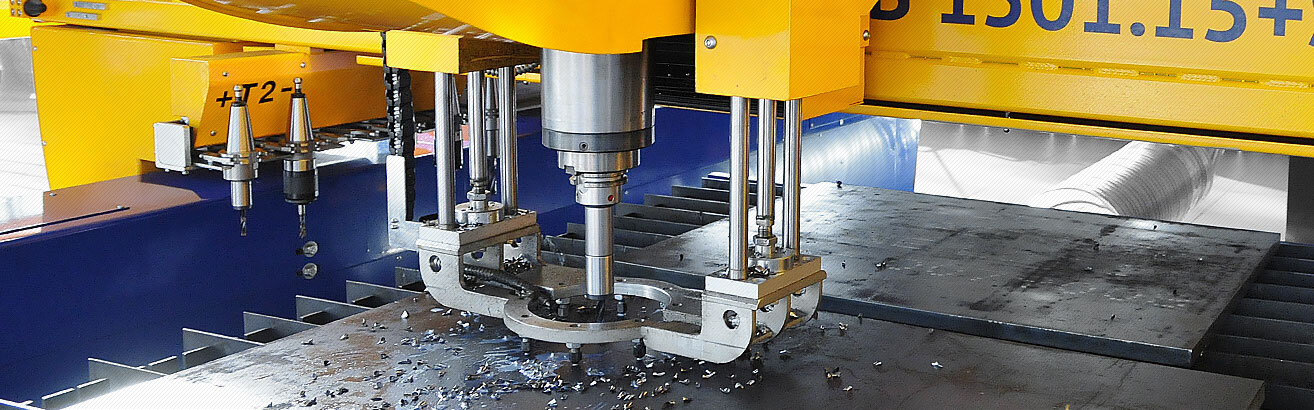
Drilling, tapping, countersinking
Drilling, tapping and countersinking on modern CNC cutting machines
CNC-controlled drilling is used in industrial manufacturing to produce precise cylindrical holes. With a cutting-drilling combination, sheet metal can now be drilled, countersunk and then cut with just one machine. In this way, for example, head plates, saddle plates or flanges can be produced. Typical application fields are industrial sectors in which drilled components are processed to constructions or finished products.
Drilling, countersinking, tapping, cutting: MicroStep cutting systems can combine all of these processes in just one system without compromising on the quality of the components to be produced. The advantages of such a combination of different processes are obvious: no time-consuming component handling to the next system, no further clamping and no reprogramming of the component on the cutting system – the entire processing takes place on one system.
This is made possible by the future-oriented cooperation between MicroStep and technology leader Kennametal. Users benefit from this in many ways: short distances and the optimal coordination of the CNC cutting system and tool components ensure a high degree of accuracy and enable the implementation of special solutions.
For fast process and tool changes, a 6-, 8- or 16-station tool magazine is available, in which the tools are safely protected from cutting dusts and damage. After drilling, the system automatically switches to the cutting tool (e.g. plasma) and cuts all planned contours (2D and 3D).
Two things are particularly important for the high precision of the finished component: firstly, the width of the kerf must be taken into account when measuring the distance between the drill hole and the outer contour – an exact measurement of the torch tip is necessary for this. Secondly, the control system must precisely determine the offset between the torch and the drilling tool. Both are carried out using the patented ACTG® calibration unit from MicroStep.
DRILLING & COUNTERSINKING
With the combinable tool systems, the MicroStep system can drill and countersink between 4 and 60 mm in diameter, depending on the equipment. The drilling components from the manufacturer Kennametal enable through-holes, blind holes and flat-head countersinks. In addition, systems can be integrated to deburr and prepare defined bevel cuts simultaneously during the drilling process.
TAPPING
In addition to blind hole and through-hole taps, taps from M5 to M30 can be cut into the material, depending on the system.
SPECIAL CUSTOMIZED SOLUTIONS
In order to increase the process speed to a maximum, it can make sense to integrate and use a step drill for numerous applications. This is individually manufactured by the drilling expert according to customer requirements and the drilling job. By integrating several defined tools into one, not only process steps but also tools can be saved.
About Kennametal
Kennametal is recognized as a leader in the development of quick change systems for versatility, speed and accuracy. Kennametal is an original American manufacturer of high quality tools. For more than 100 years, the company has acquired extensive expertise in the field of workpiece processing and uses this knowledge to manufacture carbide tools for tool machines and mining and road construction. Kennametal has also been developing and producing in Fürth (Bavaria, Germany) since 1993.