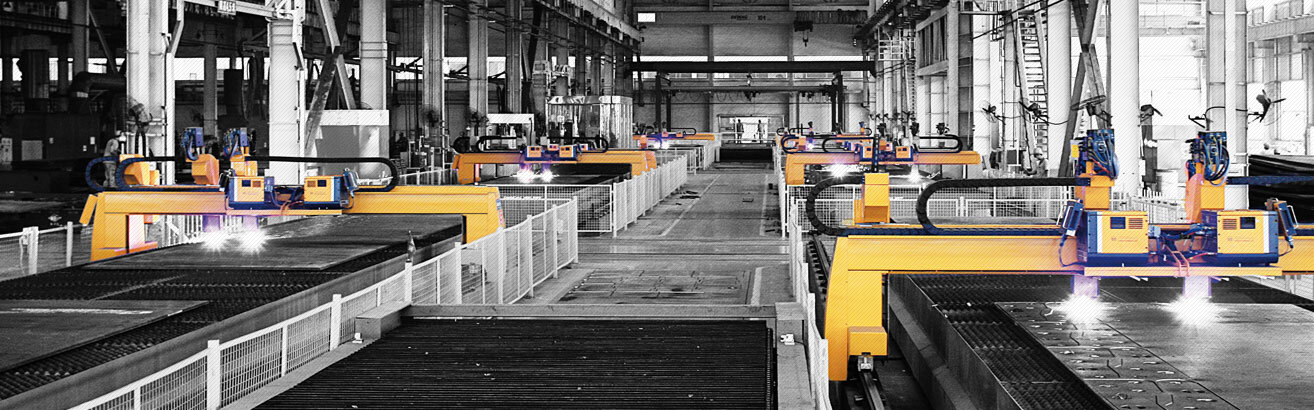
Automation
Automation around CNC cutting systems for plasma cutting, oxyfuel cutting, laser cutting and waterjet cutting
Today, the automation of manufacturing processes is an integral part of efficient production. Certain steps can be replaced by automated workflows, especially in repetitive work and set-up processes. This way, the production flow can be constantly maintained. Automation is possible with CNC cutting systems for plasma cutting, oxyfuel cutting, laser cutting and waterjet cutting.
Automatic loading and unloading of sheets
With a connection to a sheet metal rack storage system, the cutting system equipped with MPM® (MicroStep Production Management) software transmits the command to remove the required sheet metal from storage. A crane with a magnetic or vacuum lifter picks up the sheet and transports it to the relevant cutting table. The cutting system automatically measures the position and alignment of the sheet and begins processing the cutting plan. As soon as the cutting process is complete, the crane removes the cut sheet and transports it to a clearing zone. Here, the employees can then sort the components.
If there is no sufficient overhead crane available, the entire loading and unloading of the cutting system can also be carried out using automatic conveyor tables. To do this, the sheet is simply placed in a loading zone – the conveyor table then transports the sheet to the cutting area. Once cut, the sheet is automatically transported to where the finished parts can be removed and sorted.
Automatic loading and unloading of pipes and profiles
Pipe cutting systems from MicroStep can be equipped with an automatic loading and unloading system to ensure an efficient and continuous material flow during pipe cutting. The pipes or profiles are fed into a pipe magazine by a forklift truck via a loading device. If required, the cutting system is replenished from this pipe magazine. New pipes are automatically clamped in the jaw chuck.
As soon as a pipe segment has been cut, it is discharged by means of a discharge system. If required, it can also be transported on to the next processing station via a connected conveyor system.
Cutting sheet metal directly from the coil
Sheet metal coils are an efficient and space-saving solution for transporting and storing thin sheet metal. Normally, they first have to be unrolled, straightened and then cut to the desired sheet format using coil shears.
With MicroStep's automatic coil solution, the unrolled material can be processed directly on the belt using plasma or laser. This saves time and eliminates the need to manually handle individual sheets to the cutting system. The decoiler unwinds the strip directly onto the cutting table. For an absolutely precise cutting result, the cutting system uses a laser scanner to measure the exact alignment of the uncoiled section of the metal strip and adjusts the current cutting plan accordingly.
The desired contours are then cut out. Once the cutting process is complete, the cutting table, which is equipped with a conveyor system, transports the finished cut section of the metal strip. In the next step, the components cut from the sheet metal strip can then be removed either manually or with the help of a robot. The remaining sheet metal is fed into a guillotine shear, which cuts it into compact, easily disposable pieces.
Multifunctionality
A special machine for every task? This maxim has long been a thing of the past in the metalworking industry. In order to be able to meet the growing demands of existing and potential customers efficiently and with high quality in the future, companies in the industry are increasingly relying on multifunctional machine solutions in addition to automation.
This saves both time and space in production. It also creates the urgently needed flexibility to be able to adapt to constantly changing customer requirements at short notice.
In the product area of CNC-controlled cutting systems, solutions that allow the automated, multifunctional processing of sheet metal, pipes, profiles or domes are particularly in demand. The system manufacturer MicroStep has developed the MG plasma cutting system precisely for this requirement. Depending on the equipment, the cutting system enables a wide range of processing technologies to be combined: cutting of contours, weld seam preparation and holes as well as drilling, countersinking, tapping, marking and punching. You can find more information about multifunctionality here: Multifunctionality expert knowledge
Automatic order and material stock management
To get maximum efficiency from an automated cutting system, a reliable software solution for organizing the cutting process is required – such as MicroStep's Machine Production Management, or MPM® for short:
MPM® manages customer orders and automatically nests components into finished cutting plans according to priority, material type, material thickness and processing method. MPM® then assigns these cutting plans to a technologically suitable cutting system for processing. If there is a connection to a storage system with automatic material loading, the cutting system is immediately loaded with the required semi-finished product and automatically starts processing the cutting plan.
Research cooperation with the Fraunhofer Gesellschaft
The Fraunhofer Gesellschaft, headquartered in Munich (Germany), is considered the largest organization for application-oriented research in Europe. This also includes the Fraunhofer IGCV in Augsburg, with which MicroStep Europa GmbH cooperates. "IGCV" stands for "Institute for Foundry, Composite and Processing Technology".
The mission of the Augsburg institute is, among other things, to provide the SME sector with the know-how of cutting-edge research in the field of production technology. Small and medium-sized companies in particular are to receive expert help with the introduction of new technologies in order to maintain and strengthen their competitiveness.
Research, consulting, training and implementation are offered from one provider in the following areas, among others:
- Intelligent networked production
- Resource efficiency in products and processes
- Flexibilization of production
MicroStep customers can also benefit from this: For example, when it comes to integrating a CNC cutting system into a company's individual production processes, MicroStep works with Fraunhofer to develop the most efficient and innovative solutions possible and, if required, also supports their implementation. If you are interested, please do not hesitate to contact us!