Plasma cutting system
CNC plasma cutting systems convince with economical and precise cuts and are unrivalled, especially for medium material thicknesses. Modern plasma cutting machines combine efficiency, lasting performance and multifunctionality.
Plasma cutting systems from MicroStep Europa
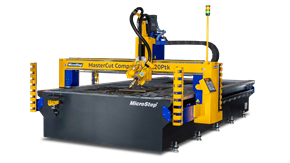
MasterCut Compact
Compact, flexible and versatile: the MasterCut Compact is suitable for 2D and 3D processing of flat material and is available as a complete package with plasma source and filter system.
- 2D cutting
- Bevel cutting
- Marking
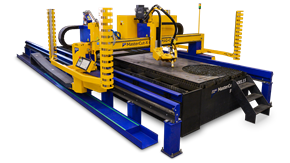
MasterCut
High-quality 2D cuts, precise bevel cuts and efficient weld seam preparation – these are the hallmarks of the MasterCut series. Technologies for processing pipes and profiles can also be integrated.
- Pipe & Profile processing
- 2D cutting
- Bevel cutting
- Marking
- Scanning
- Automation
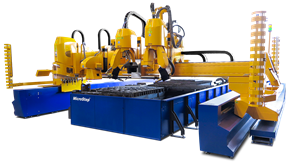
MG
The MG series is MicroStep's 3D all-rounder and a pioneer in the industry in terms of multifunctionality and process reliability. The plasma cutting system enables maximum processing.
- Pipe & Profile processing
- Dome processing
- 2D cutting
- Bevel cutting
- Drilling, Tapping, Countersinking
- Marking
- Scanning
- Automation
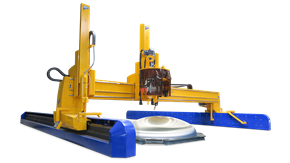
DRM
The DRM series is the strong specialist and, thanks to its enormous vertical range of manufacture, the cutting solution for almost every task: sheet metal, pipe, profile and dome processing, drilling, marking, scanning and more.
- Pipe & Profile processing
- Dome processing
- 2D cutting
- Bevel cutting
- Drilling, Tapping, Countersinking
- Marking
- Scanning
- Automation

DS
The automated process line of the DS series is an efficient cutting and drilling solution. Thanks to the high degree of automation, the focus is on particularly high time and cost efficiency.
- Pipe & Profile processing
- 2D cutting
- Bevel cutting
- Drilling, Tapping, Countersinking
- Marking
- Scanning
- Automation
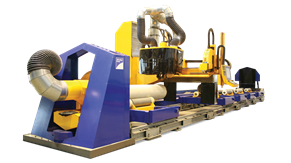
CPCut & PipeCut
The pipe and profile specialist enables a wide range of applications. The CPCut & PipeCut can be optionally equipped with automatic loading and unloading devices.
- Pipe & Profile processing
- 2D cutting
- Bevel cutting
- Marking
- Scanning
- Automation
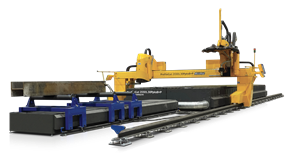
ProfileCut
The ProfileCut series is a true all-rounder in beam processing. Thanks to its robust design, beams of up to 24 meters in length can be cut and marked efficiently and cost-effectively.
- Pipe & Profile processing
- Dome processing
- 2D cutting
- Bevel cutting
- Drilling, Tapping, Countersinking
- Marking
- Scanning
- Automation
What is a CNC plasma cutter in gantry design?
Gantry with tool stations, guideways and cutting table
Plasma cutting systems in gantry design consist of a steel gantry, a so-called gantry beam, driven on both sides and mounted on guideways. The tool stations (plasma torch, drilling support, scanner, etc.) are mounted on this beam. Thanks to the solid construction, they can be positioned vibration-free and accurate to a few hundredths millimetres. A plasma cutting table is positioned within the guideways, on which the cut parts are placed and processed.
Plasma power source and gas supply for the plasma cutter
In order to initiate and perform the cutting process in a plasma cutting system, the corresponding periphery is required. A power source supplies the necessary power for the plasma system, the gases required for the plasma beam are provided by a gas supply.
Filter system
The dusts and particles occurring during cutting with a plasma system are collected either by an extraction system directly at the plasma torch or at the plasma cutting table and the air is cleaned in a filter system.
Touch display with machine control
A main monitor is used to control the CNC plasma cutter and program the cutting tasks for the plasma system.
Advantages of CNC cutting systems …
- High economic efficiency through fast and precise plasma technology with unrivalled cost-benefit ratio
- High level of automation
- Extremely flexible when cutting all electrically conductive materials
- High cutting speeds of the plasma torch when processing thin and medium material thicknesses (significantly faster than oxyfuel and waterjet)
- Compared to the laser, shorter processing times for medium and higher material thicknesses
- Nearly post-processing free cutting results
- Multi-torch operation possible for fast parallel cutting
- Only solution for the cutting of aluminium materials and various high-alloy steel grades when processing materials in the thin and medium thickness range
- Individual width and length of the working area from 1 to more than 20 metres wide and 1 to more than 50 metres long
- Depending on the working area, simultaneous loading and unloading during the cutting process is possible (pendulum operation)
- Shorter processing times due to the option of using several gantries on one system
- Higher cutting speeds
- Much more flexible through the use of multiple processing options (2D cutting, bevel cutting, marking, drilling, etc.)
- High cutting quality
- Almost no post-processing
- Multifunctionality: Several processing options can be realized on one system
- Automation capability
Up to date
With our newsletter you will be informed about all the latest novelties.
Which materials can be processed with a plasma cutting machine?
In principle, all conductive materials can be processed with a CNC plasma cutting machine. In practice, CNC plasma cutters are used to process the following materials, among others: Mild steel (fine-grained steel, Hardox), stainless steel (V2A), chrome-nickel steel (V4A), aluminium, copper, brass, titanium, armour steel. The typical cutting range of a plasma system is between 1 mm and 50 mm – here the cutting results are of high quality and economically most efficient.
Plasma cutting
Multifunctionality & automation
Today, a modern plasma cutting system enables much more than just 2D and bevel cutting of sheets, pipes, profiles and domes. Drilling, countersinking, tapping, marking and labeling are also among the options that can be realized on a CNC plasma cutting machine in addition to the cutting technology. Furthermore, technologies for scanning can be integrated, e.g. for reading barcodes or for automatic determination of the position of metal sheets.
Multifunctionality
Strengths of MicroStep plasma cutting systems
For its gantry-guided plasma systems, MicroStep relies on a steel gantry, that is stiffened and driven with AC servo motors on both sides, for high dimensional accuracy and reproducibility of the cutting results with the best dynamics and strong driving power. Due to the modular design of the CNC cutting machines, different technologies can be combined and different geometries (sheet metal, pipe, profile, beam, dome) be processed on one plasma cutting system. Due to the automatic calibration of the used tools with the patented calibration unit ACTG®, MicroStep plasma cutting machines achieve permanently precise cuts and, thanks to the best components, can be used for a long time even in three-shift operation. With the MicroStep QualityHole® hallmark you can also be sure that all decisive factors for cutting small holes and fine contours have been optimized.
Plasma cutting systems in various industries
CNC plasma cutting systems are used in all sectors and industries in which materials such as mild steel, stainless steel and aluminium in the medium material thickness range are required and factors such as high-quality cutting results at high cutting speeds and simultaneously low cutting metre costs are decisive for the cutting process. A selection of industries and possible fields of application for MicroStep plasma cutting systems is given below:

- Energy industry: construction of wind turbines and nuclear power plants, pipeline construction
- Transport systems & vehicle construction: cabin construction, construction of trailers or tank trucks, prototype construction
- Construction industry: construction of facades, roofing, fencing
- Contract cutting & steel trade: separating and contour cutting for various requirements
- Mechanical engineering: cutting of individual components for component groups
- Plant & container construction, ventilation construction: pipe processing, pressure vessels, contour and bevel cutting in containers
- Metalworking & heavy industry: pipeline construction, crane construction, repair of graders and commercial vehicles
- Shipbuilding & shipyards: cutting of panels and production of parts for hull and keel
FAQ: We answer your questions about plasma cutting systems
At what point is it worth buying a plasma cutting system?
What are the advantages of a plasma cutting system from MicroStep?
A stiffened steel portal driven by AC servo motors on both sides ensures high dimensional accuracy and reproducibility of the cutting results with the best dynamics. The modular design of the plasma cutting machines allows them to be configured precisely to the user's needs in terms of table length, tool equipment and the geometries to be processed (sheet metal, pipe, profile, beam, container base). Thanks to the automatic calibration of the tools used by means of the patented ACTG® calibration unit, MicroStep plasma cutting systems with chamfering unit achieve permanently precise cuts and, thanks to the best components, have a long service life, even in three-shift operation. With the MicroStep QualityHole® seal of quality, you can also be sure that all decisive factors for cutting small holes and fine contours have been optimised.
What can be processed with the system?
A plasma cutting system has low requirements on the material´s nature. All electrically conductive materials such as mild steel, stainless steel and aluminium can be cut in 2D and 3D with maximum flexibility. Other conductive materials such as copper, brass etc. can also be processed, in this case Microstep recommends further consultation to ensure the best possible cut quality. The typical cutting range is between 1 mm and 50 mm - here the cutting results are qualitatively very good and economically extremely efficient. In addition, plasma cutting systems can be equipped with further tools for drilling, countersinking, threading, marking or more for even more flexible use.
For whom is a plasma cutting system from MicroStep suitable?
A plasma cutting system is particularly suitable for companies that cut materials in thin to medium sheet thickness range. Regardless of whether it is sheet metal, pipes, profiles or container bases. Plasma cutting is used in a wide range of industries, including metal cutting, mechanical engineering and plant and container construction.
Are there different types of plasma cutting systems?
A distinction is made between manual plasma cutters and automated plasma cutting with a CNC machine or by robot.
Hand plasma cutters are mainly used where precision, accuracy and reproducibility are less important than making a quick cut.
Mechanised plasma cutters are used wherever thermally conductive materials need to be cut with reproducible precision. They score points for thinner and medium sheet thicknesses with very good cutting quality and very high cutting speeds at comparatively low cutting metre costs.
Which plasma cutting systems are available at MicroStep?
At MicroStep we offer you different variants of plasma cutting systems:
- The MasterCut Compact is space-saving, flexible and versatile
- The MasterCut is a flexible and robust 3D cutting system for almost any cutting task
- The MG is MicroStep's all-rounder and meets the highest demands for precision, performance and handling
- The DRM is the strong specialist and enables 3D processing of highly complex tasks or with extraordinary dimensions
- The DS is an automated time- and cost-efficient process line
- The CPCut & PipeCut are the cutting solution for pipes and profiles with large diameters and lengths
- The ProfileCut is a true all-rounder in beam processing and can also be automated
How are the plasma cutting systems controlled?
The control of the CNC plasma cutter as well as the programming of the cutting task is done on a main monitor with touch display. The preparation of the cutting programme (creation of the NC codes) can also be done on a separate office computer and sent to the control system for further processing.
What gas is needed?
For simple plasma cutting, air is sufficient. For more precise fine plasma cutting, oxygen is usually recommended as a cutting gas for mild steel and air as a swirl gas (to constrict the arc for stable cuts). Stainless steel and aluminium are mainly cut with nitrogen, forming gas or argon/hydrogen. The exact composition of the gas mixture depends on the thickness of the material to be cut.