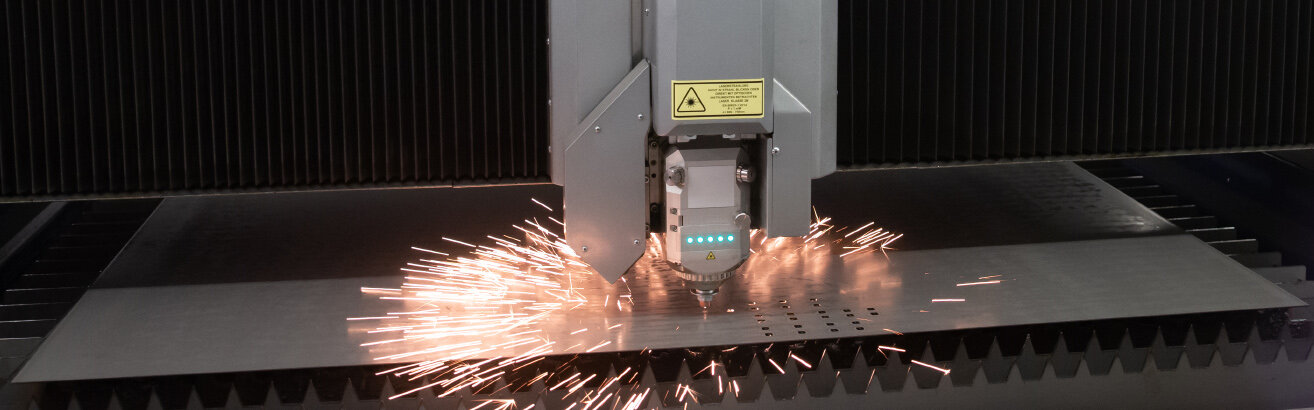
CNC laser cutting: precision and efficiency for your manufacturing solutions
- Advantages of CNC laser cutting
- What is CNC laser cutting?
- CNC laser cutting in three variants
- CNC fusion cutting
- CNC laser flame cutting
- CNC laser sublimation cutting
- Which CNC laser cutting variant is suitable for which application?
- Applications for CNC laser cutting systems
- This is how a CNC laser cutting system works
- Why choose a MicroStep CNC laser cutting system?
- Maintenance and service for CNC laser cutting systems from MicroStep Europa
In modern production, companies are often faced with the decision of whether to purchase laser-cut parts externally or whether it is worth buying their own laser cutting machine. As an expert and manufacturer of highly efficient, high-quality machines, we inform you about all aspects of CNC laser cutting.
Advantages of CNC laser cutting
- CNC laser cutting is suitable for processing a wide range of materials.
- This modern technology enables extremely fine cuts with minimal tolerances and at very high cutting speeds.
- Precision cutting systems produce parts with an accuracy in the single-digit µm range. Industrial laser systems can achieve values in the 0.1 mm range and lower.
- The high precision of the cuts means that the amount of finishing required can be minimized. Narrow kerfs allow for optimal material utilization, which means less waste and conservation of resources.
- Multifunctional CNC laser cutting systems enable the automation of manufacturing processes as well as a wide range of processing options, such as cutting, drilling, tapping, countersinking, marking or bevel cutting. This allows additional work steps – such as weld seam preparation – to be integrated into the manufacturing process.
Tip
With the experts from MicroStep Europa at your side, you save time and money on CNC laser cutting. This is because we not only advise you on the optimal application of our CNC laser cutting systems, but also on possible funding programs for the purchase of energy-saving CNC laser cutting machines. Get advice now!
What is CNC laser cutting?
CNC laser cutting combines the precision of laser technology with the efficiency of computer numerical control (CNC). The highly focused laser beam and the high processing speed ensure minimal heat input, which is limited to a very small area of the material. This means that the thermal stress on the components during CNC laser cutting is extremely low, so that no or only minimal deformation occurs. CNC-controlled laser technology enables the finest cuts in the millimeter range and even significantly below. The result is high-precision components with minimal material loss.
CNC laser cutting machines from MicroStep Europa
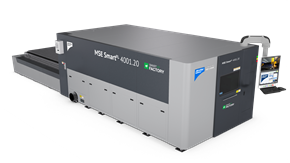
MSE SmartFL
High Power: The MSE SmartFL is a powerful yet cost-effective system for high-quality 2D laser cutting. The series can be equipped with laser sources up to 60 kW and is already ideally equipped for the production of the future!
MSE SmartFL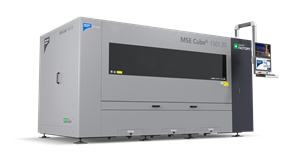
MSE CubeFL
The MSE CubeFL combines maximum precision and efficiency with minimum space requirements. The series can be equipped with laser sources up to 12 kW and is the ideal solution for compact laser cutting.
MSE CubeFL
MSE TubeFL
High-quality 2D and 3D laser cutting of pipes, profiles and beams. With the MSE TubeFL, the finest contours and openings as well as precise bevel cuts can be realized. Depending on the version, the system has an extremely high degree of automation.
MSE TubeFL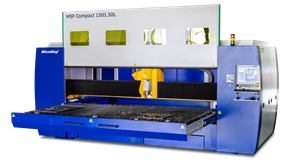
MSF Compact
The MSF Compact combines precise 2D laser cutting with a compact design. The series impresses above all with its small footprint and the usual high cutting quality of the laser cutting system. A manually extractable cutting table enables simple and uncomplicated loading and unloading.
MSF Compact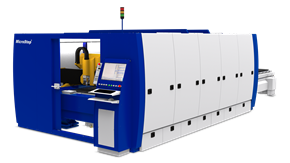
MSF Cut
Reliable and process-safe: this is what characterizes the MSF Cut series. The efficient production assistant is the ideal solution for standard 2D tasks and can be equipped with laser sources up to 15 kW.
MSF Cut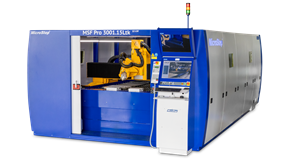
MSF Pro
High speed and flexibility in 3D: the precise all-rounder MSF Pro is a pioneer among laser cutting machines in terms of multifunctionality. No other laser system offers such a high degree of vertical integration for sheet metal processing. Pipes and profiles can optionally also be cut.
MSF Pro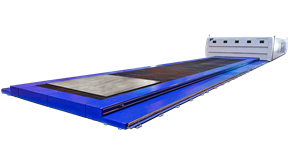
MSF Max
The MSF Max is the giant among laser cutting systems. Developed for processing large-format sheet metal for shipbuilding, it enables precise 3D high-speed processing of flat material. Thanks to the traveling safety cabin, a working area of up to 50 m in length and 6 m in width is available for the laser machine.
MSF Max
MSF Pipe
The pipe and profile specialist: As an option to the high-precision 2D and 3D processing of pipes and profiles up to 12 meters in length, the MSF Pipe can be expanded to include sheet metal processing.
MSF Pipe
CNC laser cutting in three variants
CNC laser cutting can be divided into three main processes: laser fusion cutting, laser flame cutting and laser sublimation cutting.
Fusion and flame cutting are used in particular for metal and steel cutting, which is precisely tailored and produced at high speed. Sublimation cutting is particularly suitable for thin material thicknesses, right down to delicate materials such as paper. Thanks to the high cutting speed and low thermal load, a wide range of materials can be processed efficiently and precisely.
CNC fusion cutting
In laser fusion cutting, the material is heated to melting temperature by the focused laser beam. An inert gas (e.g. nitrogen or argon) blows the molten material out of the kerf.
Advantages of CNC laser fusion cutting
- High precision and fine cut edges
- No oxidation because an inert gas is used
- Little material distortion due to low heat input
- Ideal for thin to medium material thicknesses
CNC laser flame cutting
Laser flame cutting is used primarily for cutting construction steel, with oxygen being used as the cutting gas. The oxygen reacts with the heated metal, oxidizing it and generating additional heat. This heat promotes the cutting process, enabling thicker materials to be processed.
The advantages of CNC laser flame cutting
- High cutting speed due to exothermic oxidation reaction
- Cutting of large material thicknesses (30 – 50 mm)
- For thicker materials, more cost-effective than fusion cutting
CNC laser sublimation cutting
In laser sublimation cutting, the material is converted directly into a gaseous state by the laser (sublimation), without producing a melt. The resulting gas is blown out of the kerf with a cutting gas (e.g. nitrogen). Since the material vaporizes directly and does not leave any molten residue, laser sublimation cutting is also used in the textile and paper processing industries, for example.
The advantages of CNC laser sublimation cutting
- Extremely fine cuts with high precision
- No melting / no burr formation
- Particularly suitable for thin and delicate materials
Which CNC laser cutting variant is suitable for which application?
Cutting process |
Benefits |
Areas of application |
CNC fusion cutting | High precision Oxid-free cut edges Low heat input |
Stainless steel, aluminum, titanium, brass and other materials |
CNC flame cutting | Fast Cost-effective Suitable for thick materials |
Construction steel Mechanical engineering Heavy industry |
CNC sublimation cutting | Extremely fine cuts No melting No burr formation |
Sensitive material or thin material thicknesses |
Applications for CNC laser cutting systems
CNC laser cutting systems are versatile and can be used to manufacture delicate components such as stents as well as large components such as car body parts. Thanks to modern fiber laser technology, it is now possible to realize even oversized formats with working areas of up to 50 m in length and 6 m in width.
The industries in which CNC laser cutting is used are as diverse as the applications themselves. CNC laser cutting technology is used in all branches of industry that deal with metalworking or cutting technology in general, and especially in the area of contract manufacturing. There are virtually no limits to the range of materials that can be processed. They range from glass to textile fabrics to delicate materials such as paper.
In the metal industry, CNC laser technology is used primarily to process steel sheets of all types and grades, as well as stainless steel sheets, non-ferrous metals such as aluminum and brass. It is also possible to cut bevels to prepare for welding.
This is how a CNC laser cutting system works
Fiber laser cutting head for 2D laser cutting
The CNC laser cutting system generates the cutting beam in the laser source. Depending on the application, different types of laser are used:
- CO2 laser
- fiber laser
- solid-state laser (e.g. fiber laser)
The generated laser beam is guided to the cutting head either by mirrors or optical fibers. There it is focused by an optical lens to a point, creating a high energy density. When the laser hits the workpiece, the material is melted, burned or vaporized depending on the cutting process.
A so-called process gas, such as oxygen, nitrogen or air, is directed into the kerf. This gas has various functions:
- Blowing out molten residues or metal vapor
- Influencing the cutting quality (oxide-free edges, higher speed)
- Cooling the workpiece to avoid distortion
The CNC-controlled motion guide ensures highly precise guidance of the cutting head along the specified cutting contour. The CNC system coordinates the laser power, feed rate, gas supply and automatic height control to ensure consistent cutting quality. The workpiece itself either remains stationary while the cutting head moves, or it moves under a fixed cutting head.
Why choose a MicroStep CNC laser cutting system?
We are a manufacturer of CNC laser cutting systems and your expert in the field of CNC laser technology. We have more than a quarter of a century of experience in the field of cutting systems in standard and special machine construction. We are happy to advise you on the advantages and costs of CNC laser cutting based on your actual production needs. We can also inform you about possible funding programs.
Your advantages at a glance:
- More than 25 years of expertise in the field of cutting systems
- European supplier
- Special machine construction & standard machine construction
- Fiber laser technology
- Personal customer service in Germany / Austria / Switzerland
- Practical user training
- Close-knit service & support network
Maintenance and service for CNC laser cutting systems from MicroStep Europa
At MicroStep Europa, service is our top priority! Our service team offers you technical support with fast response times.
Our services at a glance:
- Commissioning & maintenance
- Training on the system
- Telephone support
- Remote maintenance
- On-site service
You might also be interested in: