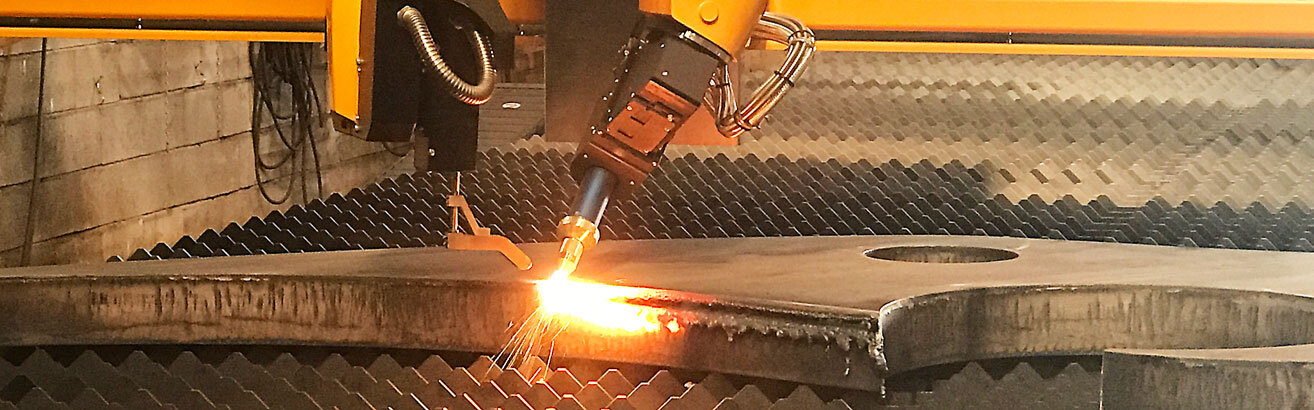
Automated welde edge preparation with CNC machines
Process reliable 3D processing (bevel cutting) with plasma, laser, waterjet and oxyfuel technology
According to field studies, up to 50 percent of the parts produced worldwide using CNC machines must be provided with weld edge preparations. At the same time, however, only a much smaller percentage of the machines used are equipped with technologies for weld edge cutting. One reason for this could be the investment costs for modern technological equipment. More obvious, however, is the assumption that decision makers in many companies simply have too little information about the possibilities of modern technologies for weld edge preparation on gantry cutting machines. Those who deal with the subject more intensively will soon find out: Higher acquisition costs are amortized in a very short time. Because the comparative advantages of modern, up-to-date solutions are considerable. For example, almost no reworking is necessary thanks to high precision. In addition, there are immense savings in production time and resources because, at the end of the day, less material handling is required between different processing stations. And when it comes to the automated processing of weld edge preparations for domes, pipes, rectangular or IPE profiles, the integration of a bevel cutting tool on gantry cutting systems is even considerably cheaper than the purchase of a robot that has been commonly used for this application up to now.
MicroStep's aspiration is to supply cutting machines that can produce weld edge preparations of the highest quality and precision. Therefore, since the introduction of the MicroStep plasma rotator in 2000 and the MicroStep waterjet rotator in 2001, great efforts have been continuously made to establish automated bevel cutting as a common and highly efficient production technology for preparing weld edges on various types of material. Over the years, further developments in the mechanics and motion control of our rotary- and 3D tilting tool stations have also been accompanied by the continuous development of plasma and laser technology by MicroStep suppliers. Against this background, MicroStep can now offer solutions for 3D cutting for an extremely wide range of different materials and material thicknesses. Thanks to an automatic calibration system and adaptive bevel angle compensation, our system solutions enable our customers to cut bevels easily and using plasma, waterjet, oxyfuel or laser technology. Depending on the cutting technology used, bevels can be cut in a material thickness range from 5 to 300 mm. In addition, MicroStep systems are able to combine different technologies (e.g. plasma and waterjet) within a single cutting plan – thanks to unique features of the CyberFab control system developed by us and a profound knowledge of the different cutting technologies.
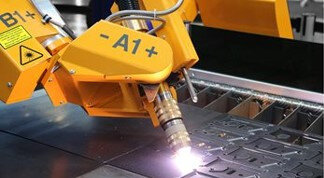
PLASMA ROTATOR
Bevel cutting/ weld edge preparation with plasma technology up to 52°
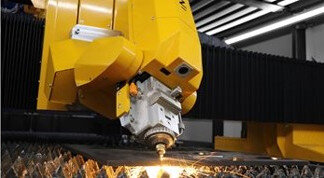
LASER ROTATOR
Bevel cutting/ weld edge preparation with laser technology up to 45°
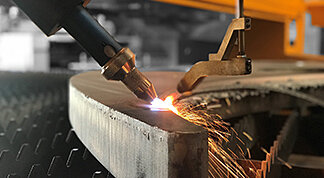
OXYFUEL ROTATOR
Bevel cutting/weld edge preparation with oxyfuel technology up to 60°
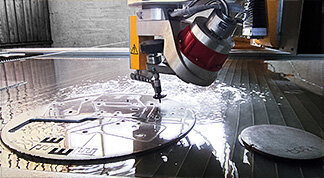
WATERJET ROTATOR
Bevel cutting/weld edge preparation with waterjet technology up to 45°
MicroStep machines offer two types of bevel cutting processes:
DBP – Direct beveling process – represents the classic type of weld edge preparation, where the bevel is cut directly into the raw material (sheet metal, pipe, profile or dome). The desired bevel – A, V, Y, X or K – is created via multiple consequent transitions of the cutting tool (at different angles) along the cut edge. MicroStep gantry cutting systems with two rotators also enable the parallel cutting of two identical parts using two rotary heads at once.
ABP – Additional beveling process – enables the subsequent beveling of parts that have already been cut by plasma, laser, oxyfuel or even waterjet.
"When it comes to bevel cutting quality, MicroStep has a unique selling point in complying with the tolerances required for robot welding.“
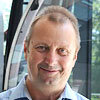
Walter Eberle
Production Planning
Doppelmayr Seilbahnen GmbH
"Right from the start we had the impression that we were getting the bevel tool, which is state-of-the-art and technologically leading. The system is very productive and it is also process reliable – it has met all expectations."
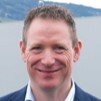
Marcel Meier
Head of Procurement & Corporate Development
stürmsfs AG
Technologies for reliable and precise results successfully in use
In general, the accuracy of bevel cutting is determined by the mechanical precision of the cutting machine, the precision of the cutting technology used and the quality of the algorithms for controlling the torch distance from the cut material. In addition to the consistent use of high-quality components, the mechanical precision of MicroStep bevel cutting machines is guaranteed by several innovative technologies.
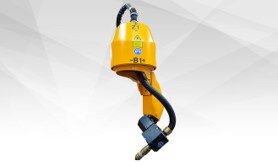
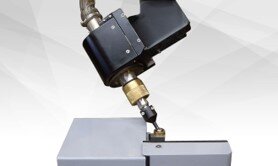
The accuracy of the cutting technology is also enhanced by eliminating naturally occurring beam deviations once the torch is in an inclined position in relation to the material, causing an unwanted difference of the cut angle from the theoretically programmed slope.
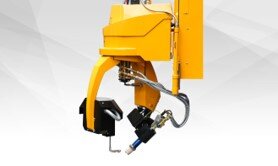
STHC – Self-teaching height control – a combination of 3D motion control, self-teaching algorithms and adaptive height control according to the plasma arc voltage. STHC ensures positioning of torch in the correct height.
All the described functions contribute significantly to improving the accuracy of the bevel cutting process. More than 700 MicroStep beveling tool stations are currently in use worldwide, about half of which are equipped with the patented ACTG technology – excellent cutting results inspire hundreds of users around the globe.
Bevel cutting in action
Rytz AG: 3D laser with multifunctional equipment
MicroStep's oxyfuel rotator: ABP with oxyfuel
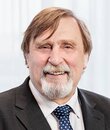
Head of R&D department
MicroStep
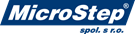
„When developing our chamfering units, we have always focused on maximum precision, process reliability and repeat accuracy.“
Criteria for the ideal bevel cut
In order for cutting systems to deliver optimum results and at the same time enable exact repeatability, a number of criteria must be met. In recent years, innovative manufacturers have developed a range of systems to ensure reliable and precise operation, depending on the cutting technology used (plasma, laser, oxyfuel, waterjet). MicroStep is the pioneer in the industry when it comes to process reliability in weld edge preparation. Below are three criteria for the ideal bevel cut in plasma cutting.
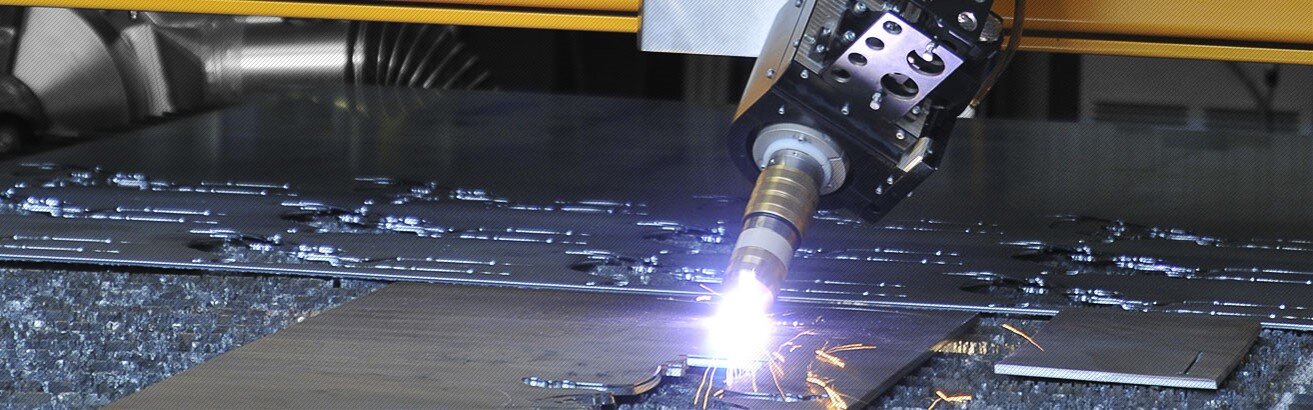
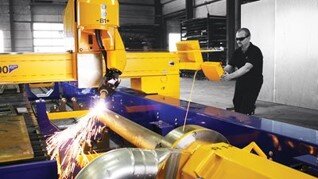
Precisely calibrated tools form an absolutely necessary basis for precise bevels. There is often the misconception that it is sufficient to collect measurement data and calibrate the tools based on this data either mechanically or solely by manually entering the corresponding correction values into the machine control. However, with this procedure, angular deviations of the torch can hardly be brought below the 0.5 mm limit – not to mention the high expenditure of time involved in purely mechanical adjustment.
This is where the MicroStep plasma rotator comes in. The entire calibration process is fully automated and eliminates deviations in the hundredth of a millimeter range. The automatically retensioning torch holder of the bevel cutting head already ensures that the deviation is not greater than 0.5 mm even after a torch collision.
The rest is done by the control of the calibration station: For this purpose, the exact end points of the torch tip are measured at different rotation (X, Y and Z coordinates). Based on the measured deviations, the control system calculates all necessary correction values, which are automatically applied during the next cutting process. This automatic calibration system (ACTG® – Automatic calibration of tool geometry) ensures a completely new quality with regard to bevel cutting. It significantly improves the precision and dimensional accuracy of the cutting process, eliminates the need for time-consuming mechanical adjustments and significantly increases the productivity of the system.
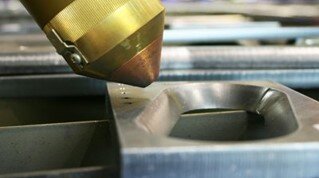
In order to achieve the highest possible precision on the cut component, it is important to maintain the exact distance from the torch tip to the surface of the material to be processed during the cutting process. The so-called cutting height is controlled by the arc voltage – which works easily and reliably for simple 2D cuts.
When bevel cutting, however, other factors come into play that influence the correct distance from the torch tip to the surface of the material to be processed. MicroStep® has developed the Adaptive Torch Height Control (ATHC®) process for this purpose: All the parameters required for weld edge preparation are automatically adjusted by the control software, so that a perfect bevel cut is always achieved.
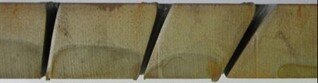
In addition to the factors mentioned above, the precision of the cut workpieces is also significantly influenced by the formation of the kerf, which is created during cutting with the plasma arc. For a better illustration, the adjacent figure shows the shape of the kerf at a current of 260 amperes with different angles of inclination (15°, 30° and 45°).
As can be seen in the figure, the bevel angles on the opposite sides of the kerf are not identical. On the one hand, this is due to the shape of the arc, which does not quite correspond to the ideal cylindrical shape, and on the other hand to the discharge of larger quantities of material on the negative bevel than on the positive one. At the same time, slag is formed and thus the upper edge of the negative bevel is rounded off – in contrast to the lower edge of the positive bevel, which remains sharp. This leads to the need for further corrections – both to the angle of inclination of the torch and to the dimensions of the workpiece, in such a way that the finished cut part has exactly the desired dimensions.
These corrections are correspondingly different when the contours of the positive workpiece or the negative workpiece are involved. Both are influenced by the tilt angle of the torch and the strength of the cutting current. In order to minimize deviations caused by the "natural characteristics of the plasma arc", all cutting systems equipped with a MicroStep rotator are equipped with adaptive Bevel Angle Compensation (ABC®) as standard. Together with the Automatic Calibration System (ACTG) and the Adaptive Height Control (ATHC) described above, this correction system ensures the precision and dimensional accuracy of plasma bevel cutting.
Different bevel types (V-cut, X-cut, Y-cut, K-cut)
V-cut
In the case of a V-cut, the plates on which the welding process is carried out are at an angle to each other which in cross-section is similar to a V. A V-bevel is one of the simplest bevel cutting tasks. Here, the torch must be inclined, but height regulation and angle compensation must be solved by the system in such a way that the cut is true to size and as free of rework as possible.
X-cut
The X-cut, also called double V-cut or DV-cut. Seen from the side, it is the combination of two oppositely oriented V-cuts. Therefore, a root must be inserted from two sides during the welding process. This is a more difficult cutting task for the production of the bevel: First the part to be cut must be provided with a V-bevel and then a negative bevel, i.e. an undercut of the material. This is a challenge for the operator and the cutting system when setting the required angles.
Y-cut
Making a Y-cut requires two cuts: a vertical cut and a diagonal cut. A micro joint remains standing, so that the side view results in a Y when two parts are joined together. The production of the Y-bevel poses a challenge to the system, among other things, in regulating the height of the torch and the angle of the plasma arc. Only with optimum adjustment can the corresponding bevel be produced and a micro joint that is usually predefined with accuracies in the tenth of a millimeter range.
K-cut
The K-cut, also known as HV-cut as well as with micro joint as double H-V-cut or DHV-cut, is the most demanding of the common bevels. One workpiece is cut off vertically, the more difficult counterpart has one positive and one negative V-bevel or two contrary Y-bevels with joint. The K-bevel with micro joint is mainly used where high material thicknesses require a stronger connecting weld.
Subsequent weld edge preparation
(ABP® – Additional beveling process)
TECHNOLOGIES
ADVANTAGES
- Alternative to robots
- No more manual reworking
- Savings in material
- Savings in operating costs
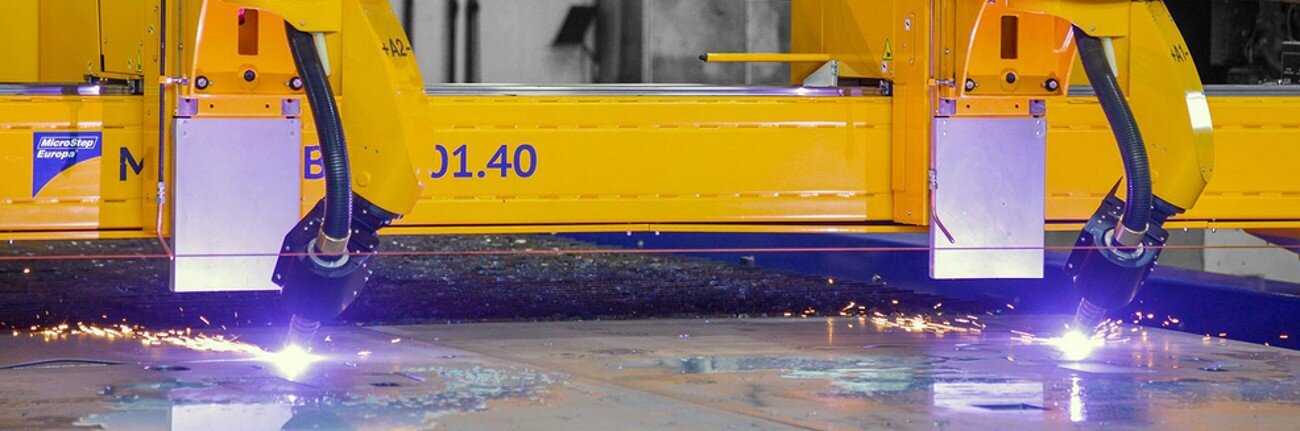
Advantages of CNC cutting systems for weld edge preparation
- Cost-effective alternative to robots
- No more manual reworking
- Savings in material
- Savings in production time
- Less material handling
- Reduced set-up times
- One system for sheet metal, pipe, profile or dome
- High cutting range (length and width modularly expandable)
Bevel cutting in different industries
In general, all common cutting technologies such as plasma, oxyfuel, waterjet and laser can be used for bevel cutting. Not only flat sheets, but also geometric workpieces (pipes, beams, profiles, domes) can be provided with V-, Y- and K-bevels in this way, but also variable bevels, which are necessary for a variety of welding processes. Bevel cutting plays an important role in various applications in the metalworking industry today: for contract cutting of individual parts, for shipbuilding and energy sector constructions, for material processing in the construction and automotive sector as well as for tank and apparatus engineering.
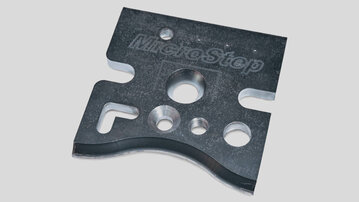
Different geometries with various technologies
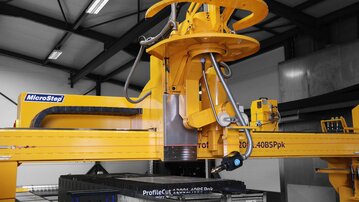
Bevel cutting with different technologies
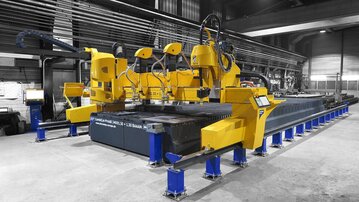
Simple and multifunctional series for weld edge preparation
CNC cutting systems with rotator technology
Whether with plasma, oxyfuel, waterjet or laser: MicroStep has the exact technology for your cutting task: precise and process reliable. Choose your machine!