Press brake
The right solution for every bending task
Buy a CNC press brake and achieve high precision and efficiency when bending sheet metal!
Bending technology from MicroStep Industry offers maximum precision and process reliability, is equipped with high-quality components throughout and can be almost completely automated. The hydraulic press brakes are characterized by state-of-the-art control technology, ease of operation and numerous configurations.
- Press brakes from MicroStep Industry
- Advantages of press brakes from MicroStep Industry
- Design and components of a CNC press brake
- Equipment of the press brakes
- Challenges and solutions in the bevelling process
- Press brakes in various industries
- Press brake and laser cutting system: the perfect duo
- FAQ
Press brakes from MicroStep Industry
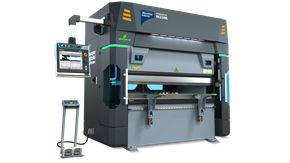
eB ULTRA
The 100% electric press brake from the eB ULTRA series is highly efficient, extremely precise and incomparably fast.
- Sheet processing
- Material handling automated

EUROMASTER
The EUROMASTER series from MicroStep Industry is economical to purchase and works precisely and reliably. It is extremely flexible in terms of pressing force, working range and degree of automation.
- Sheet processing
- Material handling automated
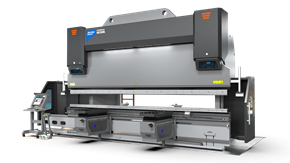
GENIUS
The GENIUS series from MicroStep Industry can be customized exactly to the user's needs: from compact bending cells to fully automated press brakes with a bending length of up to 9 m and a pressing force of 1,250 tons.
- Sheet processing
- Material handling automated
- Tandem, Tridem
Advantages of press brakes from MicroStep Industry
- The most advanced 3D CAD modelling techniques minimize stresses and deformations right from the design stage
- Equipped with high-quality components throughout for particularly high process reliability
- Press brakes from MicroStep Industry can be flexibly configured and automated
- State-of-the-art software and intuitive CNC controls
- Precise drive systems and CNC-controlled crowning systems compensate for deformations and ensure a constant bending angle
- Equipped with up to six axes in the backgauge for optimum positioning
- CNC-controlled bending aids for handling large and heavy sheets
- Highest bending accuracy thanks to fully automatic, laser-supported bending angle measurement and correction systems
- Safety laser for maximum safety during the bending process
Features of the press brakes from MicroStep Industry
CNC control technology
The press brakes from MicroStep Industry are equipped with state-of-the-art CNC controls from Delem as standard: cutting-edge technologies that allow users to get the most out of their press brake and are easy and intuitive to operate. Alternatively, the machine can also be equipped with control systems from ESA or Cybelec on customer request.
Software
With regard to programming a press brake from MicroStep Industry, we recommend the Libellula.BEND software: The solution makes it possible to check created production programs using simulations – including the detection of collision risks in relation to tools or machine parts, for example. The DXF files for nesting on a cutting system can be automatically generated from the production program for cutting the sheets to be bent. And, of course, it is also possible to use programming software from alternative quality providers.
Backgauge
The CNC-controlled backgauge of the press brake guarantees optimum positioning of the part to be bent. When purchasing the standard version of the press brake, it is equipped with at least two axes – or four, five or six axes accordng to the series or on request. The backgauges can be equipped with pneumatically retractable sheet supports to prevent large thin sheets from sagging between the bending line and the backgauge. Double-guided backgauges have a stabilizing effect and promote precision during the bending process.
Tool holders
Press brakes from MicroStep Industry are already equipped with Promecam quality clamping systems as standard. Alternatively, the manufacturer's bending systems can also be equipped with products from WILA – manual as well as pneumatic or hydraulic solutions are also available for the upper and lower tool clamping.
Front support consoles
Every press brake from MicroStep Industry is already equipped with support consoles as standard. Depending on the equipment option, the front supports also have a parking space outside the bending line. The manufacturer also offers CNC-controlled bending aids for handling large sheets.
Safety equipment
Maximum safety with minimum loss of time: A safety laser protects the operator of the press brake from the risk of crushing between the upper and lower tool. The traversing speed is controlled dynamically; the machine only moves at a reduced speed within the danger zone, which saves a considerable amount of time.
Do you already have a specific configuration in mind? Then let us know your requirements and we will provide you with an appropriate quote!
Challenges and solutions in the bending process
During the bending process, stresses and deformations occur due to the sometimes immense forces acting on the machine structure. One of the consequences of this is that the upper structure (upper beam) of the press is further away from the lower structure (lower beam) during the bending process than would be the case without the described deformation effect. As a result, the tool does not plunge deep enough into the die to achieve exactly the desired angular result.
Our partner Accurl® uses the most advanced 3D CAD modeling techniques, including analysis tools such as computer-aided engineering (CAE) software programs, right from the design stage of MicroStep Industry® press brakes. In this way, stresses and deformations can be virtually simulated and reduced to a minimum in terms of design (see graphics). Press brakes from MicroStep Industry are also characterized by a particularly high level of process reliability during operation: Only the highest quality components from well-known brand manufacturers such as Siemens, Heidenhain or HAWE Hydraulik are used.
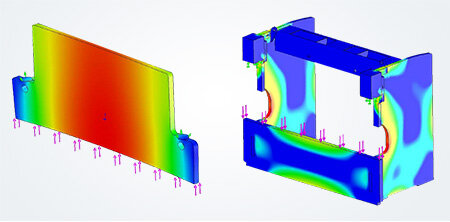
One of the unavoidable phenomena in press brakes is the deformation of the structure. In particular, the upper beam tends to bend in the middle with medium and thicker material thicknesses, which leads to a greater distance between the punch and die in this area. Without compensation for this effect, the bending result in the middle does not correspond to the desired angular result.
The ultra-precise drive systems from Accurl® in combination with the CNC-controlled crowning systems from Accurl® compensate for the deformation of the structure during the bending process and ensure that the desired bending angle is consistently achieved over the entire length of the press brake. These precision systems are already installed as standard on the EUROMASTER and eB ULTRA series.
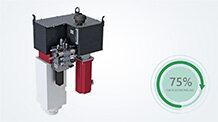
eB ULTRA series:
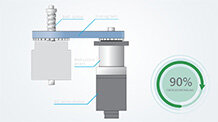
Exact bending of sheet metal is essential for precision sheet metal production, regardless of the bending strength or thickness of the material to be processed.
ACCURL iMeasure® is a fully automatic, laser-supported bending angle measurement and correction system for CNC press brakes. iMeasure enables the exact determination of the bending angle with extremely high accuracy. Alternatively, an angle measuring system integrated into the safety system is available, particularly for systems with shorter bending lengths. IRIS Plus is extremely economical to purchase and ensures real-time angle correction.
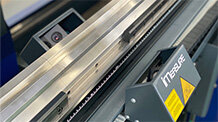
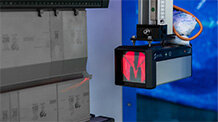
Up to date
With our newsletter you will be informed about all the latest novelties.
Press brakes in various industries
Press brakes are used in all sectors and industries of metal processing where materials such as steel, stainless steel and aluminum are bent. From small bending cells for locksmiths and car workshops to fully automated bending production lines for the automotive or shipbuilding industries, for example. For industries in which particularly long and large components need to be bent, such as light poles, we recommend purchasing a press brake as a tandem and tridem solution.
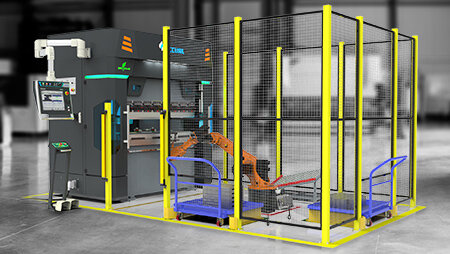
- Increased production efficiency
- Time savings through automatic tool change
- Elimination of time-consuming manual parts handling
- Bending cells individually designed to meet requirements
- Error-free processing of large series and changing order situations up to batch size 1
- Lower production costs
- Design flexibility in terms of shape, size and quantities
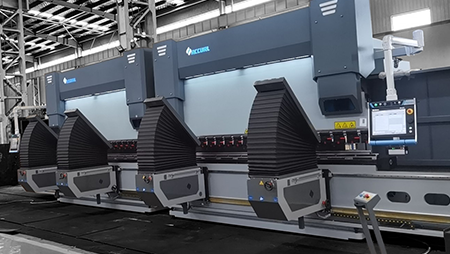
- Reliable and precise processes
- Faster speeds compared to one large single machine
- Individual presses can also be used independently of each other for smaller bending jobs
- Variability in terms of length and press force, depending on requirements
- Uncomplicated programming and control
- As easy to operate as one single machine
The EUROMASTER series from MicroStep Industry is flexibly configurable and can be equipped with an automated material handling system.
Press brake and laser cutting system: the perfect duo
Before the sheets are bent, they are usually cut to size. A combination of laser cutting system and press brake in the company often forms a perfect duo. Laser technology scores particularly well in the thin sheet metal sector, achieving high levels of accuracy at high cutting speeds. Precise and accurate cutting makes the subsequent bending process easier and results in higher quality end products. In addition, the combination of both machines means that sheets can be processed in the press brake directly after laser cutting. This saves valuable time in the production process. The synergy of press brake and laser machine in one company therefore leads to both time and cost savings, making it the ideal combination in sheet metal processing.
FAQ: We answer your questions about press brakes
In which areas are press brakes used?
Press brakes are mainly used in metal processing companies. Manual press brake technologies are mainly used in smaller metalworking shops and automotive workshops – they can only be used to process smaller sheet sizes and material thicknesses. Professional, hydraulically or electrically driven CNC press brakes, on the other hand, can process sheet metal of almost any size and material thickness and achieve far greater precision as a result. Press brakes are used in a wide variety of areas – for example in ventilation and air conditioning technology, automotive engineering, the marine industry, medical technology, the energy sector, plant engineering and many other areas.
What does a press brake "do" in the production process?
Bending is a sheet metal forming process and is often referred to as edging or folding. Using a press brake, pieces of sheet metal of different sizes are bent under the influence of force and formed into a precise 3D shape. The term sheet metal basically describes flat plates made of metallic materials. The permanent deformation of the workpiece to be processed is used to produce, for example, cladding parts, housings for electrical components, machine components or profiles.
Is it easy to operate a press brake?
As a result of further development, particularly over the last 20 years, press brakes are now equipped with the latest CNC controls with corresponding software, which simplify the operation of the press brakes accordingly. The systems from MicroStep Industry, for example, work almost completely automatically and adapt themselves flexibly and in real time to the type of material to be processed and the material thickness. Anyone can operate a modern press brake from MicroStep Industry after appropriate training without any in-depth prior knowledge.
When is it worth using a professional press brake?
Manual, hand-operated press brakes are severely limited in terms of the size and thickness of the material that can be used. As a rule, the maximum sheet thickness that can be processed on manual press brakes is two millimetres. Professional, hydraulically or electrically driven CNC press brakes have practically no technical limits in terms of the shape, size and thickness of the sheet metal. It is also worth using your own press brake in order to be independent of suppliers. MicroStep Industry will be happy to advise you on the area of application and capacity utilization at which the use of your own press brake is economical. More about technology consulting.
How does a press brake work?
A press brake has an upper beam with an upper tool (punch) and a lower beam with a lower tool (die). The sheet metal to be bent is placed between the two beams. By lowering the punch into the die, the workpiece in between is bent into the desired shape. However, the press brake does not cut during the bending process, the sheet metal remains completely intact in terms of size and weight.
What types of bending processes are used on the press brake?
In many cases, the main application of a press brake is air bending (free bending). In this process, the punch presses the workpiece into the opening of the die, but not all the way to the bottom of the die. The bending angle is determined by how deep the punch plunges into the die. This allows different angles to be bent without changing tools.
Another bending process is 3-point bending. Here, the punch presses the workpiece through to the bottom of the die. One advantage of this type of bending is the higher precision compared to air bending. However, the process places higher demands on the technology used, in particular the CNC control and the tools, and is therefore more cost-intensive.
A third process is coining. In this process, the material is pressed into the die until it lies against the walls of the die and takes on its angle. A separate set of tools is required for each angle. As the sheet metal is pressed into the die with great pressure from the punch, the pressing force required is around three times that of air bending.
What materials are the press brakes suitable for?
Press brakes are suitable for all metals in flat form that can be bent. These include aluminum, steel and stainless steel in particular, but also high-strength steels of various strengths. Press brakes from MicroStep Industry are available in different versions and with bending forces ranging from 25 tons to more than 2,000 tons, depending on the type and thickness of the material to be bent. A low bending force is particularly suitable for thin materials, while a high bending force enables thick and hard materials to be bent.
What should I look out for when investing in a press brake?
Before purchasing a press brake, needs-based consulting is essential in order to adapt the system precisely to your own requirements. This is because a different design makes sense depending on the area of application of the press brake in the company. There are also numerous configurations to choose from: For example, an extension of the axes in the backgauge, the use of bending aids and a top control, or hydraulic and pneumatic clamping. The technical equipment of a press brake from MicroStep Industry is optimized for the specific area of application in the company. On the other hand, it is also taken into account that requirements can change over time and users should at least retain a certain degree of flexibility with regard to the area of application. Modern press brakes from MicroStep Industry can also be equipped with innovative assistance systems that reduce the risk of operating errors to a minimum and maximize the precision and quality of the bending result.
Is it necessary to maintain a press brake?
Regular maintenance is essential for the longevity and optimum performance of a press brake. This includes checking for worn or damaged tools, lubricating moving parts and checking safety systems and settings. Following a maintenance schedule will help prevent breakdowns, ensure safety and extend the life of the machine.
What does "MicroStep powered by Accurl" mean?
In the field of press brakes, we work together with our technology partner Accurl, one of the leading Chinese manufacturers of CNC systems for metal processing. The family-owned company has over 30 years of experience in tmanufacturing high-quality and innovative CNC press brakes and operates worldwide. As MicroStep Europa, we are the exclusive partner for the DACH region and, together with our partner, offer our customers state-of-the-art bending solutions and excellent service.