
Waterjet cutting | Info on waterjet technology
Waterjet cutting is a cold cutting technology. With the help of a waterjet, the material is separated without thermal influence. Either filtered water is used or an abrasive agent (e.g. sand) is added.
Waterjet cutting history
The water breaks through whole mountain ranges, single drops hollow out massive rocks. In nature, the power and hardness of water has stood out for thousands of years. Waterjet cutting technology has been exploiting this power since the beginning of the 20th century, first for digging gravel and clay, and in the 1930s for mining ore and coal using a high-pressure waterjet. In the 1960s, the aircraft manufacturer Boeing finally provided the decisive impetus for using the waterjet as a cutting technology. In 1971 the first machine for waterjet cutting was eventually produced. At that time, pressure intensifiers were mainly used, which generated the cutting jet in their high-pressure cylinders. Later, piston pumps were also used, which generated the jet with a direct drive. The start took place with so-called pure water cutting; thus, the first industrial application was the cutting of disposable diapers. At the same time, research was pursued to cut metals and composites as well, using various additives. The breakthrough for the waterjet cutting process came with the addition of abrasives. The following decades saw double-digit annual growth rates in machine sales.
Advantages of waterjet cutting
- High quality of the cut edges
- No thermal influence
- Versatile
- Suitable for a wide range of materials
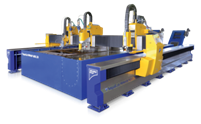
Waterjet cutting systems are used when thermal influences on the material are unwanted and highest precision is required. They convince with flexible processing options for a multitude of cutting tasks on a wide variety of materials.
Waterjet technology
Schematic illustration of the waterjet cutting technology
But let's take a closer look at today's process: A high-pressure pump ensures that the waterjet in a modern cutting machine is compressed to up to 6,000 bar and then forced through an orifice. As a result, the jet reaches outlet speeds of up to 1,200 m/s. Compared to air, this is approximately four times the speed of sound. This jet velocity and the addition of abrasive creates the cutting jet for material removal. In industry and cutting operations, pressures of 4,000 bar have established themselves as the ideal compromise between performance and durability. Today, manufacturers are continuously working on concepts to save water and energy. In this context, each waterjet cutting system is in itself a contribution to environmentally friendly, modern manufacturing. Since only natural materials such as water and sand are used in this cutting technology, neither toxic gases nor vapors are produced. The waste from processing, the dirty water and the broken grains of sand are not critical for the environment and can be fed into the recycling system.
Components processed with waterjet
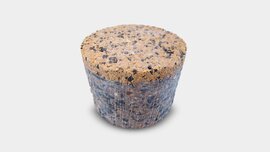
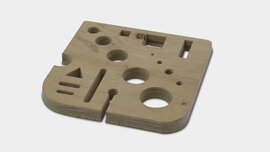
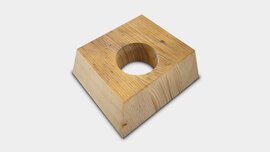
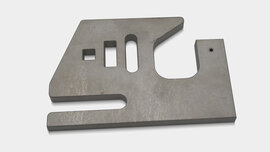
With pure water or additional abrasives
Two variants of waterjet technology are predominantly used in industry: pure waterjet cutting or abrasive cutting. Micro waterjet cutting and suspension waterjet cutting are technologies that also work with abrasive waterjet; in sheet cutting, these two technologies play only a minor role.
Pure waterjet cutting is used for soft materials. With a diameter of a few hundredths of a millimeter, the pure waterjet cuts the material like a knife. As opposed to abrasive waterjet cutting, no material is ground out of the kerf here, but only a fine cut is produced. Pure water cutting is used for cutting seals, rubber, leather, fabric and thin plastics. Metals, on the other hand, can only be cut in the form of extremely thin foils. Pure water cutting usually requires a very fast machine, as the cutting speeds are considerably higher than with abrasive cutting. The typical materials that are cut with pure water also require an additional support surface to support the thin and soft material during cutting. Here, aluminum, stainless steel or polypropylene combs have proven to be a very good solution. When purchasing a waterjet cutting machine, the possibilities of pure water cutting should be included in the decision. Not all machines are suitable for this cutting process due to their design and the achievable speeds. With pure water cutting, the abrasive medium can be dispensed with. The cutting head is modified accordingly so that the focusing nozzle can be dispensed with and the orifice is the final element. Pure water applications require less water volume and often lower cutting pressure. A machine in which these possibilities have already been taken into account in the design can more than halve the operating costs for pure water cuts.
Abrasive cutting is the most widely used process in the field of waterjet cutting. The orifice diameter, the pressure and the cutting medium influence the achievable jet power. As with pure water cutting, the waterjet from the high-pressure pump is forced through a sapphire, ruby or diamond orifice at pressures of up to 6,000 bar. However, this jet does not hit the workpiece directly, but is mixed with an abrasive in a ceramic mixing chamber. The abrasive is sucked into this cutting head via the Venturi effect and emerges – mixed with the water – from a focusing nozzle. This focusing nozzle is made of extremely hard and wear-resistant tungsten carbide. Nevertheless, even this focusing nozzle is washed out after a certain time by the abrasive jet. For modern cutting heads, these focusing nozzles are available in different diameters, lengths and qualities, so that the user can choose the most economical solution for himself. There are also cutting heads on the market in which the two components, orifice and mixing chamber, are permanently installed. These heads are more expensive to operate because they have to be completely replaced as soon as one of the components is worn out. The abrasive used is usually garnet sand or a similar hard, ground rock. The abrasive is also available in different qualities and grit sizes. The 80 mesh grit has become the standard in the industry. This grit is currently the best compromise in terms of cutting performance and surface quality. For glass or plastic applications, 120 mesh is also often used to improve the surface quality and thus produce silky smooth cutting surfaces. In micro waterjet cutting (microcutting / microwaterjet), grit sizes of 300-400 mesh are even used. This abrasive material produces optimum quality during cutting and reduces surface roughness; however, it is very expensive. In individual cases, other abrasives such as salts, quartz or garnet/corundum mixtures can also be used. In this case, however, a number of points must be taken into account. In order to carry out special applications in the best possible way, expert advice from experienced waterjet technicians is recommended.
Cutting range
Cutting head during waterjet cuttingThe main application fields of abrasive waterjet cutting are metals, natural stones, ceramics or composite materials. However, abrasive waterjet cutting can be used to cut virtually any material without – as opposed to flame cutting or laser cutting – heating the workpiece and changing the material structure in the heat-affected zones. Since the temperatures in the cutting zone are only around 50 °C, this cutting process is classified as a cold cutting process. Where no structural changes at the cut edges are desired, waterjet cutting is used. In addition, it is possible to cut any contours and to start and end at any point on the material surface. It is even possible to drill and cut a hardened steel plate with the abrasive waterjet without any problems. There is no need to drill or erode a starting hole. The surface of the workpiece is of no interest to the waterjet. A steel plate can even be cut cleanly and accurately if the surface is corroded, dirty or scaled. Only the nozzle distance must be maintained during waterjet cutting. On the other hand, polished stainless steel sheets or mirrors can also be cut without the optical reflection having any influence on the process.
Waterjet cutting is often mistakenly perceived as a slow and dirty cutting process. In reality, things are different. Modern systems provide the possibility to raise the water level and flood the material during the cutting process. When cutting below the water surface, the pollution of the machine and the surrounding area is drastically reduced. The noise level is also noticeably reduced – without having a negative impact on productivity.
Where is waterjet cutting used?
Waterjet cutting systems are machines for every material, every thickness and every contour. They score with the widest range of applications, with precision and of course the advantages of the cold cutting process. If thermal input does not play a role and materials suitable for laser, plasma and oxyfuel cutting systems are to be cut, then these cutting processes have the upper hand compared to waterjet technology. They are then significantly faster and therefore more economical. When it comes to thin sheets, laser cutting and plasma cutting have a clear advantage. For extremely thick sheets, oxyfuel cutting is the faster alternative. The range in which waterjet cutting offers the higher economic efficiency can be precisely determined by calculation. However, this comparison is limited to the materials that can also be cut by the thermal processes.
A modern waterjet cutting machine also offers a range of technology options for bevel cutting, drilling, tapping and countersinking and also allows the integration of supports for plasma cutting. This combination of technologies unites the strengths of the different cutting processes and creates a valuable assistant in the machine park, providing companies with a highly productive system for a wide range of applications.
Waterjet cutting with a MicroStep AquaCut waterjet cutting machine
How does CNC waterjet cutting work?
An ultra-high pressure pump generates a waterjet with a pressure of up to 6,000 bar. This waterjet is passed through a diamond or sapphire orifice and mixed with garnet sand. The resulting abrasive waterjet cuts almost any material. A CNC machine moves the jet through the workpiece.
Which materials can be processed with waterjet cutting?
A waterjet cutting machine can cut almost any material. In industrial applications, steels of all types and alloys, all non-ferrous metals, granite, ceramics, glass and plastics are cut. The pure waterjet also cuts fabrics, leather, rubber and seals of all kinds.
How thick can the material be for waterjet cutting?
In principle, you can also cut material up to 500 mm thick. However, the thicker the material, the longer the cutting time. Steel up to about 80 mm and aluminum up to about 120 mm, granite up to 100 mm and ceramics up to about 30 mm can be cut sensibly.
Can waterjet cutting be used on all materials?
The pure waterjet is used to cut soft materials such as rubber, leather and carpets. With the abrasive waterjet you can cut almost any material. In practice, mainly steels, stainless steels, non-ferrous metals, tiles, kitchen countertops, glass and plastics are cut.
Waterjet cutting of wood?
Wood is very suitable for waterjet cutting. Especially in furniture construction, where fine contours have to be cut, waterjet cutting is a widely used technology. The moisture hardly plays a role, as the water at the cutting edge penetrates only a few millimeters into the material where it dries again very quickly.
Does waterjet cutting only use water or is there anything else involved?
Soft materials such as leather, rubber, carpet or sealing paper are cut with a pure waterjet. For hard and brittle materials, metals, glass and plastics, an abrasive cutting agent is added to the water. Garnet sand is predominately used here, but other abrasive materials are also possible in individual cases.
What is abrasive waterjet cutting?
In contrast to pure water cutting, abrasive waterjet cutting also uses an abrasive sand. A pure waterjet separates the soft material, like a cutter knife. The material is compressed and cut through. An abrasive waterjet works like a grinding wheel. The material in the cutting joint is ground out.
Waterjet cutting: Is residual moisture relevant in the process?
For materials with a smooth surface, residual moisture is no problem. The component is blown off with compressed air. Hygroscopic materials such as wood, open-pored foams and textiles should be dried. In practice, blower dryers are used for this purpose. The decisive factor is not the temperature, but the air volume.
Is weld edge preparation possible with a waterjet cutting system?
Yes, with a waterjet cutting machine, all common types of weld edge preparation are possible, provided the machine is equipped with a 3D head.
What is waterjet cutting and what are the advantages of this technology?
Waterjet cutting is a cold cutting process. This has the advantage that no structural change occurs at the cutting line during cutting. A hardened steel plate can be cut without the cutting edge losing its hardness. Any material can be cut with the waterjet and the machine does not have to be retooled to cut steel, plastic or glass alternately.
What are the advantages of waterjet cutting over plasma/flame cutting?
Plasma and flame cutting is limited to a few metals. Waterjet cutting works with almost any material. The surface is slightly rough, but due to the non-existent heat input, there is no discoloration at the cutting edge and the contour accuracy is much better.
Why should I use waterjet cutting instead of laser technology?
Unlike laser cutting, waterjet cutting is not bound to specific materials, but can be used universally. In steel, stainless steel and aluminium, waterjet cutting is more economical than the laser above a certain material thickness. With the abrasive waterjet, thin sheets can be cut in a package. This is not possible with the laser.
Is waterjet cutting an alternative to laser cutting?
This is a question of cost-effectiveness. For thin steel or stainless steel sheets and very large quantities, the laser has an advantage. The thicker the material, the more economical the waterjet cutting becomes. Since the laser is limited to a few metals and waterjet cutting is suitable for almost any material, the waterjet cutting machine is an alternative for anyone who cannot use a laser to its full capacity.
What accuracies can be produced with waterjet cutting and what does the cut surface look like?
Depending on the equipment of the machine, the achievable accuracies are in the low tenth range up to the range of a few hundredths of a millimeter. The surface is slightly rough to semi-matt, depending on the speed and grain size of the abrasives. There is no discoloration at the cutting edge as in thermal cutting processes.
Are there only standard processes for waterjet cutting, or can customer requirements be taken into account?
There are many ways to adapt the cutting process to the customer's requirements. Pressures, abrasive media and many other parameters can be adapted to the needs of the customer. The CNC guiding system, the ultra-high pressure pump, the cutting table and the cutting head technology are configured according to customer requirements.