Flame cutting system – Powerful machines for big tasks
Flame cutting machines convince by their robust construction, precision and performance with large material thicknesses. Their robust and multifunctional design makes them the ideal production aid.
Oxyfuel cutting systems from MicroStep Europa
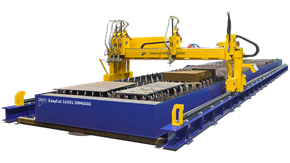
EasyCut
The EasyCut series stands for modern oxyfuel cutting at the highest level. This long-lasting machine impresses with its robust design and produces precise and cost-effective oxyfuel cuts.
- Sheet processing
- 2D cutting
- Marking
- Scanning
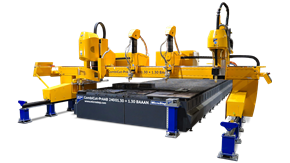
CombiCut
The CombiCut series is the powerful expert and, thanks to its enormous vertical range of manufacture, the cutting solution for almost any task.
- Pipe & Profile processing
- Dome processing
- 2D cutting
- Bevel cutting
- Drilling, Tapping, Countersinking
- Marking
- Scanning
- Automation
What is a CNC flame cutting machine in portal design?
Gantry with tool stations, guideways and cutting table
Portal cutting systems consist of a steel gantry driven on both sides and mounted on guideways, a so-called gantry beam. The tool stations (oxyfuel torch, drilling support, scanner, etc.) are mounted on this beam, which can be positioned vibration-free and accurate to a few hundredths of a millimeter thanks to its solid construction. The cutting table of the oxyfuel cutting machine is positioned within the guideways – on it the cut parts are placed and processed.
With this design, enormous working areas can be achieved on systems with oxyfuel torches. Depending on the requirements, gantry widths of up to 8 meters and cutting table lengths of up to 50 meters are possible.
Gas supply and combination with plasma technology
In order to initiate and perform the cutting process on a flame cutting system with oxyfuel technology, the corresponding periphery is required. The gases necessary for the oxyfuel flame are ensured by a gas supply. For more economical and precise cuts with medium material thicknesses, plasma cutting technologies can also be additionally implemented on an flame cutting machine. In this case, a plasma power source is then required to provide the necessary power and also gases that are supplied via the gas supply.
Touch display with machine control
The external control panel with a large touch screen allows the programming of cutting tasks and the monitoring of current cutting jobs of the flame cutting machine.
Filter system
The dusts, gases and particles produced during cutting with an oxyfuel torch are collected by an extraction system on the cutting table and the air is cleaned in a filter system.
Advantages of CNC flame cutting machines
- Applicable for the medium to large material thickness range
- Low investment costs
- High efficiency thanks to economical parallel cutting operation with several oxyfuel torches
- Lower consumables costs
- Little post-processing necessary
CNC flame cutting machines are particularly beneficial for metal processing companies that regularly face cutting tasks with large material thicknesses or manufacture steel constructions. Increasing batch sizes and orders require an equally increasing degree of automation, so automated flame cutting systems play a major role in the steel construction sector.
- Higher level of precision
- Considerable time saving thanks to efficient parallel cutting operation with several oxyfuel torches
- Multifunctionality thanks to numerous options such as drilling, tapping, countersinking or marking
- Complex cutting of seams on different material thicknesses possible
Up to date
With our newsletter you will be informed about all the latest novelties.
Oxyfuel cutting systems in action

A flame cutting system with several oxyfuel torches in parallel cutting mode enables efficient cutting processes. enable efficient cutting processes.

The CombiCut oxyfuel cutting machine is ideally suited for multi-shift operation and has been designed for cutting tasks in the high material thickness range.

With up to 8 oxyfuel torches on a flame cutting system at the same time, productivity and cutting efficiency can be increased many times over.
Which materials can be processed with an oxyfuel cutting system?
CNC flame cutting is used for thick steel plates and is primarily suited for processing unalloyed or low-alloyed metals. Therefore, the cutting process with a flame cutting system is indispensable in heavy industry and steel construction.
Flame cutting
Multifunctionality & automation
A lot has happened since the beginnings of flame cutting. For example, in addition to technical refinements, modern flame cutting machines are increasingly focusing on multifunctionality and automation. Next to mere oxyfuel cutting systems, modern machines can also combine plasma and oxyfuel cutting technology, the processing of pipes and profiles as well as other options – such as drilling or marking – on one cutting system.
Multifunctionality
Strenghts of MicroStep's oxyfuel CNC systems
MicroStep counts on a resistant and multifunctional construction of the oxyfuel cutting system. This makes the flame cutting systems, especially in heavy industry, the ideal production aid – even under difficult environmental conditions. The flame cutting machines convince with a high degree of reliability and durability.
Multifunctionality is standard with MicroStep: the flame cutting machines impress with a multitude of combinable options. For example, up to eight oxyfuel torches can work in parallel on the solid gantry. Plasma and oxyfuel technology can also be combined or a device for processing pipes and profiles can be integrated. Options such as drilling units up to 40 mm diameter or various marking units can also be realized on the CNC flame cutting systems.
Thanks to the automatic calibration of the used tools with the patented calibration unit ACTG®, MicroStep flame cutting systems achieve permanently precise cuts and are durable and also suitable for three-shift operation due to best components.
Flame cutting systems in various industries
Flame cutting machines – both mechanized and manual systems – are used in all sectors and industries where high cutting speeds with high efficiency and comparatively low investment costs are decisive criteria. Therefore the flame cutting process is suitable for industries and areas such as:
- Vehicle construction: construction and repair of trucks, heavy transporters, agricultural vehicles
- Transport systems: cabin construction, construction of trailers or tankers, prototype construction
- Construction industry: construction of facades, bridge building
- Contract cutting & steel trade: separating and contour cutting for various requirements
- Mechanical engineering: cutting of individual components for component groups
- Metalworking & heavy industry: pipeline construction, crane construction, repair of graders and commercial vehicles
- Shipbuilding & shipyards: cutting of panels and production of parts for hull and keel
- Fire department & THW (Federal Acency of Technical Relief): basic equipment for the fast cutting of metal parts

FAQ: We answer your questions about flame cutting systems
For which companies are flame cutting systems suitable?
Oxyfuel technology has a wide range of applications. It can be found in all industries that specialise in the machining and processing of steel in the high material thickness range. CNC flame cutting machines are particularly worthwhile for metalworking companies that are regularly faced with cutting tasks involving large material thicknesses. The cutting process is thus indispensable in heavy industry and steel construction. Combined flame cutting machines with additional plasma torches can also be found in metalworking companies outside of heavy industry and are an ideal mix for accomplishing different tasks over the life of the machine.
What is important when buying a high-quality flame cutting machine?
Before purchasing a cutting system, it is essential to consult with the customer to determine their requirements. Through the greatest possible flexibility in the equipment, the machine can be configured in the best possible way for the area of application in the company. In addition, a robust machine that is adapted to the tasks at hand is an essential prerequisite for a long machine life. It is therefore recommended to visit a reference machine. When purchasing a flame-cutting system, care should also be taken to ensure that the tools are calibrated across all torches or even when using an oxyfuel rotator. A comprehensive service & support guarantees the company the greatest possible system availability and should therefore already be included as a decisive factor in the purchase decision. It is also important to offer practical training for the specialist personnel, adapted to the requirements of cutting, in order to get maximum efficiency out of the cutting system.
What are the distinguishing features of the MicroStep flame cutting systems?
MicroStep relies on a robust and multifunctional design. This makes the flame cutting systems the ideal production aids - even under adverse environmental conditions. The systems impress with a high degree of reliability and durability.
Multifunctionality is standard at MicroStep: the flame cutting machines impress with a multitude of combinable options. When it comes to 2D cutting tasks, up to eight oxyfuel torches can work in parallel on the massive gantry. MicroStep's autogenous rotator is a unique option for the uncomplicated creation of various bevel geometries, for example for weld seam preparation even on thicker materials. It is also possible to combine and integrate plasma and oxyfuel technology or a fixture for machining tubes and profiles. Drilling tools for drilling, countersinking and threading or marking systems tailored to the user can also be realised on the systems. Thanks to the automatic calibration of the tools used (by means of the patented ACTG® calibration unit), MicroStep CNC machines with chamfering unit achieve permanently precise cuts. Thanks to the best components the machines are durable and can also be used in three-shift operation.
What is meant by portal construction?
Gantry cutting systems consist of a steel gantry driven from both sides and mounted on guideways, a so-called gantry bridge. The tool stations (oxyfuel torch, oxyfuel rotator, plasma torch, drilling support, etc.) are attached to this, and thanks to their solid construction they can be positioned without vibration and with an accuracy of a few hundredths of a millimetre. The cutting table or the device for machining tubes and profiles is integrated within the guideways - this is where the cutting parts are placed and processed.
With this design, enormous machining areas can be realised in systems with oxyfuel torches. Depending on the requirements, portal widths of up to 8 metres and cutting table lengths of up to 50 metres can be realised without any problems.
For which materials are flame cutting machines used?
CNC flame cutting systems are particularly suitable for cutting tasks with large material thicknesses and primarily for processing unalloyed or low-alloyed metals. For material thicknesses of 20 mm and more, oxyfuel technology can be the right choice. In the area of greater material thicknesses from around 50 mm, there are no economically viable alternative cutting options to date.
What are the advantages of parallel cutting?
Parallel cutting operation with several oxyfuel torches is extremely efficient and offers enormous time savings. Up to eight torches can process identical cutting tasks at the same time and thus generate high economic efficiency through economical parallel cutting operation.
How does the CombiCut series differ from the EasyCut?
The EasyCut series stands for modern 2D oxyfuel cutting at the highest level. It is the ideal system for precise and cost-effective oxyfuel cuts and impresses with its robust construction. The CombiCut series offers a much higher vertical range of manufacture and is therefore the cutting solution for almost any task. The CombiCut can be configured to enable 3D cutting using an oxyfuel rotator or even a plasma rotator. By equipping it with additional tools, processes such as drilling, countersinking and threading or the machining of tubes or profiles can be combined in just one system.
Is there an introduction to the operation of the equipment?
MicroStep systems are state-of-the-art solutions and feature a wide range of technologies to get the best possible results from any material to be processed, regardless of the cutting task. Perfectly trained operators are essential to achieve maximum results on a permanent basis. Despite the ease of operation of our systems, a sound understanding of the cutting system, the cutting processes as well as the production sequences is an important key to more process reliability - and thus also a significant factor for cost savings. That is why the purchase of a MicroStep cutting system already includes a customised, practice-oriented training programme, which focuses specifically on the requirements in your cutting and consists of two blocks:
- Software training before delivery of the system - for this we invite you to our training centres in Bad Wörishofen or Dorsten.
- Technology training on the purchased system at your site.