Expert know-how technologies
Modern cutting solutions require flexibility, precision and efficiency. For optimum results, cutting system, control system and software have to interact perfectly. More than 100 employees work at MicroStep in the in-house research department on the development and construction of CNC cutting systems and software programs. Thus, the components are optimally coordinated for a smooth operation of the systems. Whether 2D or 3D cutting (laser, plasma, oxyfuel, waterjet) or the combination of processing options (drilling, tapping, countersinking, marking, punching) on pipes, profiles, domes and flat sheets. Since control system and software solutions come from MicroStep, the software with its versatile modules can optionally be adapted to the customer's individual requirements.
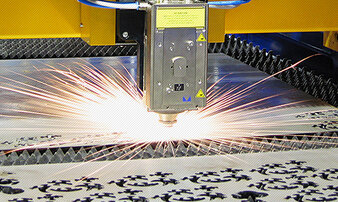
Laser cutting
The idea of the laser already goes back to Albert Einstein. But it took until the 1960s for the idea to become reality. Since then, the laser has become indispensable in many technological and scientific fields. The abbreviation laser stands for: Light Amplification by Stimulated Emission of Radiation.
Laser cutting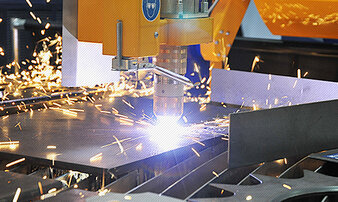
Plasma cutting
With plasma technology, all conductive materials such as mild steel, stainless steel and aluminium in the medium material thickness range can be processed. Advantages of modern plasma systems are high quality cutting results, high cutting speeds, only a small heat-affected zone and the unbeatable cost-benefit ratio compared to other cutting processes.
Plasma cutting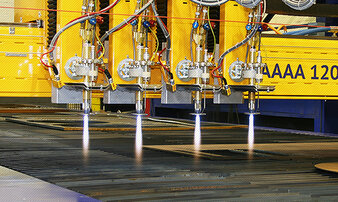
Oxyfuel cutting
Invented as early as 1901, the oxyfuel cutting process - also known as oxyfuel flame cutting - is one of the oldest, yet most important cutting processes in the metalworking industry. In this principle of thermal cutting of steel, the metal, previously heated to ignition temperature, is oxidized with a jet of oxygen and blown out of the kerf.
Oxyfuel cutting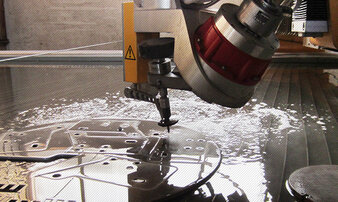
Waterjet cutting
Since the beginning of the 20th century, technology has been using the power of water, first for digging gravel and clay, and in the 1930s for mining ore and coal using a high-pressure waterjet. The first waterjet cutting system followed in 1971, and today's waterjet systems are used in a wide variety of applications. Whenever precision is required and no thermal effects are desired.
Waterjet cutting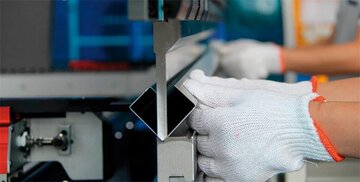
Bending
The first bending machines driven by steam engines were developed in the 1800s. Nowadays, press brakes are driven mechanically, hydraulically or electrically, are much more powerful and can therefore bend thicker sheets. Depending on the configuration and equipment, they are used as small bending cells in workshops through to automated CNC-controlled press brakes in large companies.
BendingFurther processing options on modern gantry cutting machines
A special machine for each task? This maxim has long been a thing of the past in the metalworking industry. In order to be able to meet the increasing demands of existing and potential customers efficiently and with high quality in the future, companies in the industry are increasingly relying on multifunctional machine solutions in addition to automation. This saves time and space in production and also creates the urgently needed flexibility to adapt to constantly changing customer requirements at short notice. There is a wide range of potential processing options that can be combined on a CNC machine in order to produce more efficiently, flexibly and even more economically – down to the smallest batch sizes.
Processing options