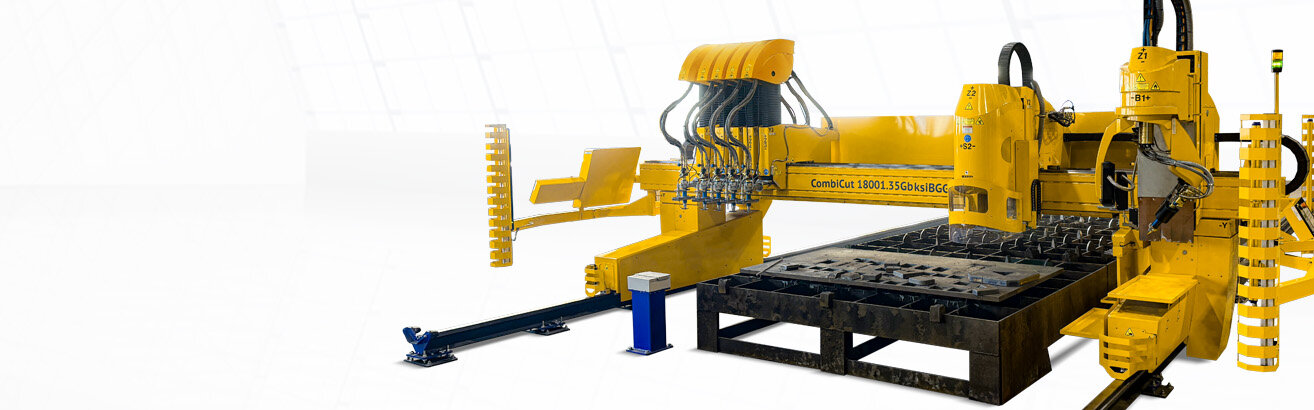
The CombiCut series
Built for the most extreme environmental variables
The CombiCut series | Reliable & flexible
The CombiCut series is a cutting machine that can combine numerous technologies and torches on one portal. Due to its extremely resistant and robust design, it is the ideal production helper even under hard environmental variables and impresses with its enormous reliability even in three-shift operation. Designed for precise oxyfuel cuts, it enables the cutting of material thicknesses up to 300 mm and can also be extended with an additional support for plasma cuts. If required, up to 8 oxyfuel torches can work on the robust portal for the fastest possible parallel cutting operation.
Additionally, the CombiCut can be equipped with the technologies plasma rotator for bevel cuts, 3-torch unit (oxyfuel), drilling units up to 40 mm diameter or various marking tools. The processing of profiles, beams and domes is possible optionally.
"We were convinced by the combination of pipe and sheet metal cutting machine. Of the technology, we liked MicroStep best. We are satisfied with the system, it runs very well," says Pierre Ruble, Production Manager Mecasem – Groupe MM.








These customers rely on MicroStep and benefit from the CombiCut

"The system works very well, it really runs great. I would buy it again with the exact same configuration."
Stefan Hacken,
Head of Steel and Vehicle Construction | Truck-Center Backes GmbH
Features
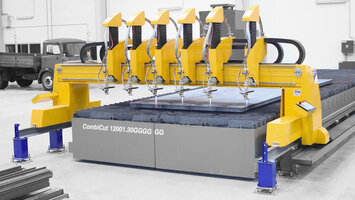
Extremely resistant and robust - even with difficult environmental variables
Extreme conditions are a great challenge for any cutting system. Upon request, MicroStep® has a suitable solution for all...
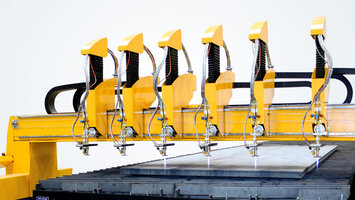
Multi-tool cutting with up to 8 oxyfuel torches
Increase your productivity with parallel cutting operationsPossibility of parallel bevel cutting with several rotator bevel...
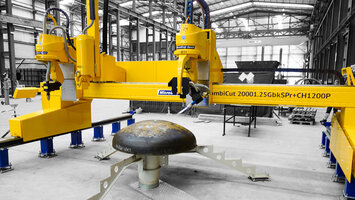
Fast and precise bevel cutting with plasma and oxyfuel
Fully automatic and highly precise bevel cutting up to 50° (plasma rotator) or up to 60° (oxyfuel rotator) Bevel...
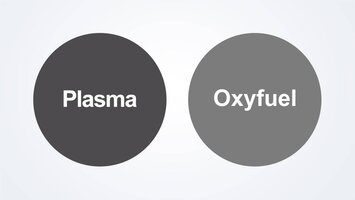
Cutting with plasma up to 800 A and oxyfuel up to 300 mm
CombiCut machines are designed to withstand high workloads in multiple-shift operations including multi-torch parallel oxyfuel...
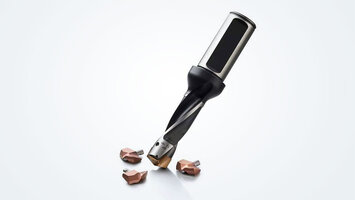
Fully automatic drilling up to Ø 40 mm and tapping up to M33
The fully automatic drilling solution provides a substantial added value for your production. Before the parts are cut, precise...
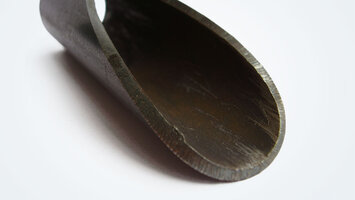
3D pipe & profile processing up to Ø 1,000 mm
Enhance your production range by adding pipe and profile cutting optionConvenient cutting program creation with MicroStep’...
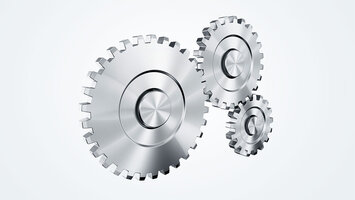
Extremely high reliability even in three-shift production
MicroStep systems are designed for a long machine life – sometimes even under tough environmental conditions. The...
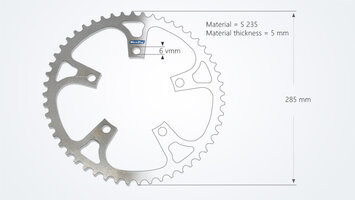
Innovative software solutions: Intuitive and easy operation
So that you can fully concentrate on your production, our innovative software solutions help you to intuitively transform...
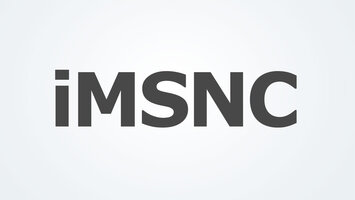
Ergonomic and uncomplicated: The CyberFab® control system
Apart from the externally positioned control console with ergonomic 24" touch screen display, the system has additional...
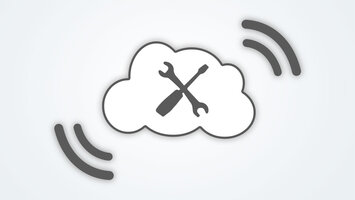
Remote Diagnostics
With CyberFab® and numerous remote maintenance modules, MicroStep offers the best foundation for fast and competent help...
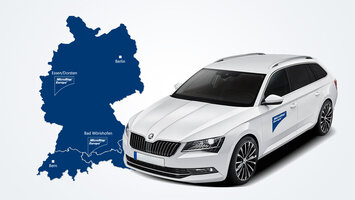
Training & expert support: Guarantee for high machine availability
To get the maximum efficiency out of your cutting system, perfectly trained operating personnel is essential. They ensure...
Technical specifications
Dimensions |
|
Effective length of work area* | 1,500 to 50,000 mm |
Effective width of work area* | 1,500 to 8,000 mm |
* Different configurations on request. The net area of the working zone can be operated with all available tools. | |
Tools |
|
Possible number of tools | 6 (8 oxyfuel) |
Possible cutting processes | plasma, oxyfuel |
Possible cutting processes | 2 |
Maximum material thickness plasma | according to plasma source |
Maximum material thickness oxyfuel | 300 mm |
Precision |
|
Positioning speed | up to 30,000 mm/min. |
Positioning accuracy | according to DIN 28206 / ≤ 0.06 mm/m |
X, Y axis | X axis: milled rails, driven on both sides and helical toothed racks |
Y axis: double linear guides | |
Z axis | ball screw |
Gantry type | massive steel gantry |
Control & software |
|
Control | iMSNC® |
Main control panel | ergonomic 17" touchscreen control panel |
Operating system | Windows 11 Pro (64-bit) |
Additional operating units | 2 operating units on the gantry (one on the left side and one on the right side) |
All specifications subject to change |
Software
Software from MicroStep® – developed especially for cutting
To allow you to concentrate fully on your production, our MicroStep® software solutions, drawings and cutting plans help you to intuitively convert them into finished components. Part of our product range also includes automation solutions for the organization of your entire cutting process.

Asper Basic
Asper Basic is the ideal tool for an easy and fast creation of NC programs for different cutting technologies (plasma, oxyfuel, laser or waterjet).
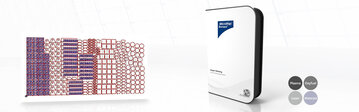
Asper Nesting
With Asper Nesting, you can easily and intuitively nest component drawings into efficient cutting plans.

MicroStep mCAM
mCAM is an efficient tool for the automated 3D production on pipes, profiles, domes, IPE carriers but also flat sheets with cutting systems of different technologies.

MPM Production Management
MPM forms the basis for automated cutting. It automatically nests complex cutting jobs and projects on the right material and distributes the cutting plans to cutting machines for processing.
Control
Handles even the most complex cutting tasks – the iMSNC® machine control
iMSNC® from MicroStep is one of the most advanced control systems for CNC cutting machines. It was developed to easily, reliably, and efficiently turn cutting plans into finished parts with the help of a clear and modern user interface.
MicroStep CyberFab® machine control
The intelligent solution for multi-technology work
CyberFab® from MicroStep is one of the most advanced control systems for CNC cutting machines. It was developed to easily, reliably, and efficiently turn cutting plans into finished parts with the help of a clear and modern user interface. The system’s hardware consists of a stand-alone control console with a TFT touchscreen and a control panel with an LCD display mounted on the gantry. In order to achieve maximum utilization and flexibility of our machines, the ergonomic control console offers the opportunity to nest new cutting programs and generate new CNC codes during an ongoing cutting process. As the CyberFab® control system and all CAM software solutions come from our company, the software with its versatile modules can be individually customized for your production. Parameter databases for individual technologies enable consistently high quality under various circumstances. CyberFab® comes with multiple efficient evaluation tools for production process optimization. These provide you with the much-needed overview of current cutting orders, cutting times, cost calculations and machine utilization in day-to-day production.
Overview of important performance data:
- 24’’ touchscreen
- Efficient management of tool data
- Very short programming times
- Fast data transfer
- Flexible and easy to use
- Advanced cutting simulation for more work safety
- Convenient contextual help via pop-up bubbles
Media
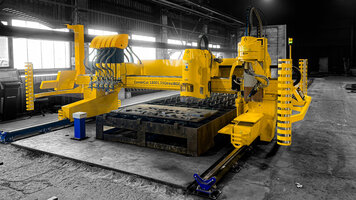
Cutting system
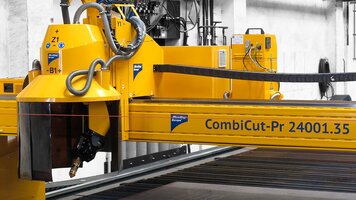
3D cutting
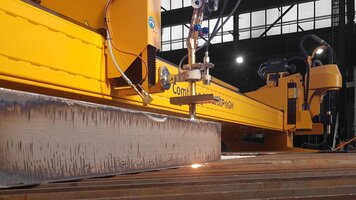
2D cutting
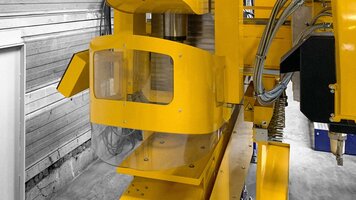
Drilling, countersinking and tapping
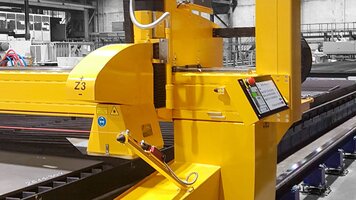
Marking
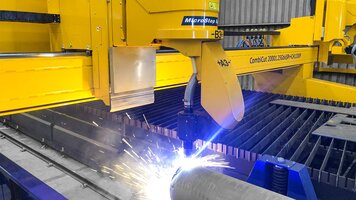
Pipe and profile processing

3D cutting
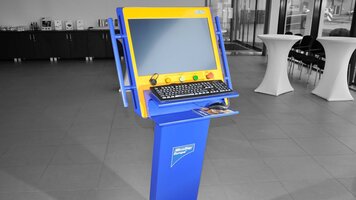
Control and operating unit
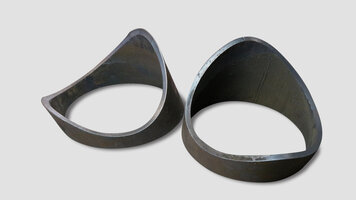
Cutting samples
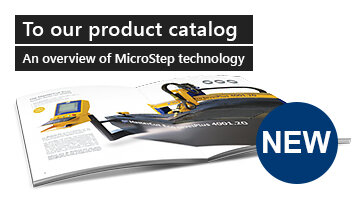
EXPERIENCE OUR SYSTEMS LIVE
in the CompetenceCenter South or North
- All four cutting technologies (laser, plasma, oxyfuel, waterjet)
- Innovative automation systems
- The latest solutions for bending and deburring
- Industry 4.0 demo factory
- Easy to reach: in the south and north of Germany
