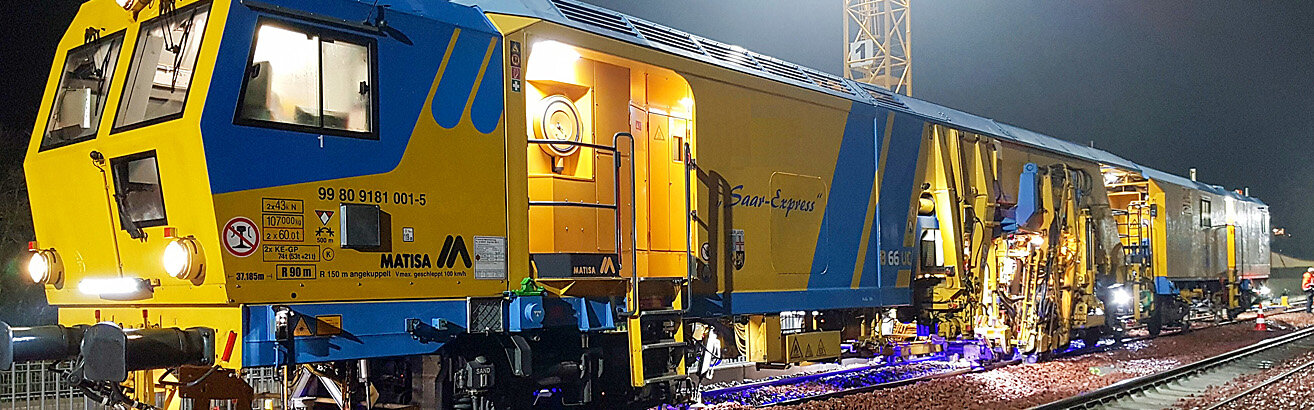
Track construction machines from Switzerland for the whole world
One machine, many advantages: "The quality is exceptional"
Matisa Matériel Industriel S.A., manufacturer of track construction machines, invested in an MG plasma cutting system for multifunctional 3D processing of sheets, pipes and profiles
Published 03.05.2021 | Erich Wörishofer
Company profile:

Matisa Matériel Industriel S.A.
Boulevard de l'Arc-en-Ciel 25
1023 Crissier
Schwitzerland
Matisa Matériel Industriel S.A. is a global manufacturer of track construction machines. Headquartered in Crissier, north of Lausanne, Switzerland, the company has subsidiaries in Europe, South America, Asia and Australia. The renowned company was founded in 1945.
The Swiss manufacturer of track construction machines – Matisa Matériel Industriel S.A. – was looking for a multifunctional cutting solution. After a long decision-making process, the company invested in an MG plasma cutting system from MicroStep for 3D processing of plates, pipes and profiles.
Many metalworking companies are responding to the increasingly complex demands of the market by investing in new technology. Multifunctional cutting solutions in particular combine a number of advantages. The Swiss company Matisa Matériel Industriel S.A., a manufacturer of track construction machines, was also looking for a flexible system to process a combination of sheets, pipes and profiles. They chose MicroStep's MG series with technologies for contour cutting, bevel cutting, drilling, tapping, countersinking and more. "The performance and efficiency of the system is beyond our expectations," says Patrice Mesnage, Electrical & Automation parts and Services Purchase Manager at Matisa.
In the past decade, the requirements for metalworking companies have changed significantly: The market is increasingly demanding more and more individual products. The challenge of being able to produce economically and efficiently with ever smaller batch sizes is correspondingly great. Top quality and fast delivery are essential. In order to master this balancing act, production requires appropriate possibilities and the right interaction between man and machine.
Against this background, companies in the industry are relying more and more on multifunctional machine solutions in order to be able to meet the increasing requirements of existing and potential customers in an efficient and high-quality manner also in the future. In the field of cutting, CNC cutting systems should be able to combine a variety of processing technologies fully automatically – regardless of whether it is a matter of processing sheets, pipes, profiles or domes. After all, this saves time during production and also creates the urgently needed flexibility to be able to adapt to constantly changing customer requirements at short notice. In concrete terms, modern cutting solutions offer a wide range of options: cutting of precise holes and contours, application of weld seam preparations as well as drilling, countersinking, tapping, marking, punching or scanning.
A modern and flexible system is supposed to replace the aging cutting system
Searching for such a solution was also the Swiss company Matisa Matériel Industriel S.A., a renowned manufacturer of track construction and maintenance machines, founded in 1945 with branches on several continents.
"Our old machine has reached the end of its life; after many years of very good service. Maintenance costs have gone up dramatically and constantly with age. In order to improve our production efficiency, we defined a new production strategy that required new production processes with new tools that were not available on our old machine. In addition to cutting plates, we now also have to cut bevels, holes, tapped holes as well as pipes and profiles. So we came to the conclusion: We are looking for a machine that combines all these possibilities," Patrice Mesnage looks back. He is purchase manager and responsible for electrical & automation parts and services at Matisa.
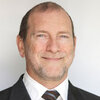
"The system allows us to eliminate most of the manual handling such as for instance beveling. The quality of the work is much higher than with manual operations. The performance and efficiency of the machine is beyond our expectations."
Patrice Mesnage,
Electrical & Automation parts and Services Purchase Manager | Matisa Matériel Industriel S.A.
Machine profile:
MicroStep MG series
- Working area 10,000 x 2,000 mm
- Cutting of pipes Ø 30 – 500 mm up to a length of 6,000 mm
- Plasma rotator for weld preparation up to 50° with auto-calibration feature (ACTG®)
- 2 x 2D oxyfuel
- Drilling up to 40 mm and tapping up to M33
Not only precise, flexible and fast: process reliability is essential
Looking for the right solution, he took a close look at the market and came across the MicroStep brand. The manufacturer of plasma, laser, oxyfuel and waterjet cutting systems quickly aroused interest. After all, multifunctional gantry cutting systems require more than just precision, flexibility and speed. The decisive factor is to be able to master the various processing options in a process-safe manner for the entire life of the machine. For this purpose, MicroStep has developed quite a few technologies, such as the automatic, patented ACTG® calibration unit, which have been operating successfully worldwide for many years. "MicroStep offers a machine that is completely customized to our needs. The quality is exceptional," says Patrice Mesnage. He and his team chose an extremely flexible version of the MG series, MicroStep's all-rounder. This enables 2D and 3D processing of plates, pipes and profiles. A plasma rotator for automated weld seam preparation, two oxyfuel torches and a support for drilling, countersinking and tapping were integrated.
Several advantages: Lower costs, shorter delivery times, reduced manual operations, and increased quality at the same time
Matisa mainly processes steel and aluminum. Large-format sheets from at least 2,000 mm to 8,000 mm in length, as well as pipe profiles with a diameter of 500 mm or square profiles up to 6,000 mm in length, are processed with the MG series. Matisa is enthusiastic about the possibilities of the multifunctional solution. "The system allows us to eliminate most of the manual operations such as for instance beveling. The quality of the work is much higher than with manual operation. It also allows several processing operations to be carried out simultaneously at a single workstation, helping to reduce delivery times, save costs, and improve safety by reducing material handling," enumerates Patrice Mesnage.
Commissioning took place right on schedule in July 2020, and the start went according to plan. "The implementation went perfectly, just as planned from the beginning. The sales and project team was very receptive to our ideas and responded flexibly to our requirements. The performance and efficiency of the machine is beyond our expectations," says Patrice Mesnage.
OVERVIEW OF THE HIGHLIGHTS OF THE PLASMA CUTTING SYSTEM MG:
Plasma cutting system for bevel cutting up to 50° and with two oxyfuel torches for parallel cutting operation
The track construction machine manufacturer Matisa opted for a complex and extremely versatile version of the MG series, which was specially developed for durable, precise as well as process-safe results and the requirements of the industry. The MicroStep plasma rotator was integrated, which enables 3D bevel cutting up to 50° for weld seam preparation, for example. The patented, automatic ACTG® calibration unit ensures consistently high-precision results. As a plasma power source, a HiFocus 280i neo from Kjellberg with automatic gas console and Contour Cut Speed technology is connected. Two oxyfuel torches have been integrated for processing higher material thicknesses.
Robust and precise gantry cutting machine with a working area of 10,000 x 2,000 mm
The MG is a robust and precise CNC guiding machine. Matisa relies on a system configuration with a working area of 10,000 x 2,000 mm. A belt conveyor table from Beuting was integrated in the gantry cutting system with its guide rails. The system, with a partially integrated extraction channel on one side for efficient extraction, contains a water basin under the table through which two conveyor belts are fed endlessly. The water basin collects slag and accumulated small parts, which are then discharged from the foot of the cutting table on a conveyor.
Fully automatic drilling spindle for drilling up to 40 mm diameter and tapping up to M30
By using a fully automatic drilling spindle, Matisa can apply drill holes, taps and countersinks to components. The drilling support used allows drill holes up to 40 mm in diameter and threads up to M30.
The RSV 30-500 pipe cutting device for processing pipes and profiles | Precise cutting results for profiles with the latest technology from MicroStep
In addition to sheet processing, the flexible cutting solution also enables pipe and profile processing. A pipe cutting device has been integrated in the system, with which pipes up to 500 mm in diameter and a length of up to 6,000 mm can be precisely processed. The company achieves high-precision results in profile processing by using innovative technology from MicroStep. The pipe cutting device rotates the profile into position, and a laser scanner installed on the gantry records the surface geometry in the cutting area of the workpiece. The 3D CAM software mCAM® compensates for the production-related deviations from the ideal contour, corrects the parameters based on the 3D scan and sets the cutting paths accordingly, resulting in a significant improvement in the cutting quality.
ABP® technology: Subsequent weld seam preparation on already cut components
The track construction machine manufacturer opted for MicroStep's ABP® technology (Additional Beveling Process): This system was developed to enable subsequent beveling for weld seam preparation on a cutting system. Using a multifunction laser scanner integrated in the gantry, already cut components are scanned and flexible bevels are applied. This also enables subsequent weld seam preparations for thicker materials.
More precise and faster hole cutting with PowerHole® technology
Cutting holes in flat material is one of the frequently required cutting applications with plasma technology. Especially screw holes have to be cylindrical. The physically-caused angular deviation of the plasma arc makes this difficult and often requires rework or the additional use of a drilling unit. Therefore, MicroStep has developed the PowerHole® technology, which compensates and minimizes the angular deviations by appropriate parameter settings combined with tilting of the plasma torch during hole cutting. PowerHole® not only significantly increases the cylindricity of holes, but also the speed during the cutting process.
Acceleration of the cutting speed thanks to "Smart Z Movement"
The MicroStep "Smart Z Movement" function enables Matisa to significantly speed up cutting processes without sacrificing cutting quality. The solution ensures that the traversing height of the plasma torch is optimized and generates additional time savings through simultaneous, laser-like movement sequences.
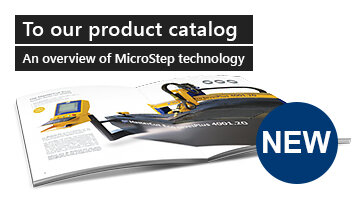
EXPERIENCE OUR SYSTEMS LIVE
in the CompetenceCenter South or North
- All four cutting technologies (laser, plasma, oxyfuel, waterjet)
- Innovative automation systems
- The latest solutions for bending and deburring
- Industry 4.0 demo factory
- Easy to reach: in the south and north of Germany
