MicroStep Europa | Principles of our quality strategy
Continuously improving: According to the principle of small steps, we are constantly working to improve the process quality in our company
„MicroStep's history is characterized by the drive for continuous improvement and development – We apply the highest standards to our work.“

Johannes Ried,
Management of MicroStep Europa GmbH

Customer orientation
MicroStep accompanies its customers holistically throughout the entire product life cycle: from finding technological solutions in the sales process to close support during project planning as well as in support and after-sales to extensive training courses for the constant optimization of production processes at the customer's site.
This customer proximity is firmly anchored in our mission statement and is lived by the entire MicroStep team every day. Here you go
Mission statement
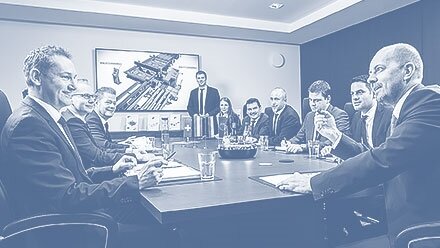
Management
Since MicroStep was founded by scientific staff at the Bratislava University of Technology, the company has relied on flat hierarchies and short decision-making processes. The ideas of our employees and the joint design of goals are the basis of the success story of the past decades and allow us to take the path to a successful future.

Employee engagement
The quality awareness and quality standards at MicroStep run through all levels. The employees form the foundation for successful work and excellent contact with customers and partners. Every employee is aware of their contribution to the company's overall results. Ideas from our employees form a fundamental innovation engine for MicroStep.

Process-oriented approach
Every employee at MicroStep sees themselves as part of a cogwheel that drives the company process forward as a whole. Regulated processes and fixed structures form the basis for consistently high quality in all areas and thus ensure that customer requirements are optimally met. Thinking in processes is firmly anchored at MicroStep; every employee is aware of the importance of their work on downstream processes.

Continuous improvement
We always want to offer our customers the best possible solution: constant innovation is what drives us. We rely on the principle of small steps – a philosophy that is even reflected in our company name. This pursuit of innovation is anchored in MicroStep's DNA and is part of its mission statement. “Research and development will always play a central role in our successful group of companies,” affirms Dr.-Ing. Alexander Varga, founder and head of development at MicroStep.

Relationship management
A long-term successful business model is based on close cooperation between people – also for a machine manufacturer. We value openness, honesty, objectivity and trust for a constant and solution-oriented cooperation. This applies internally to interactions among colleagues. But also externally for dealing with customers, suppliers, specialist retailers, research institutions, trade associations and all other partners: Here we also maintain close cooperation and partnership on an equal footing in order to move forward together towards an innovative and successful future.