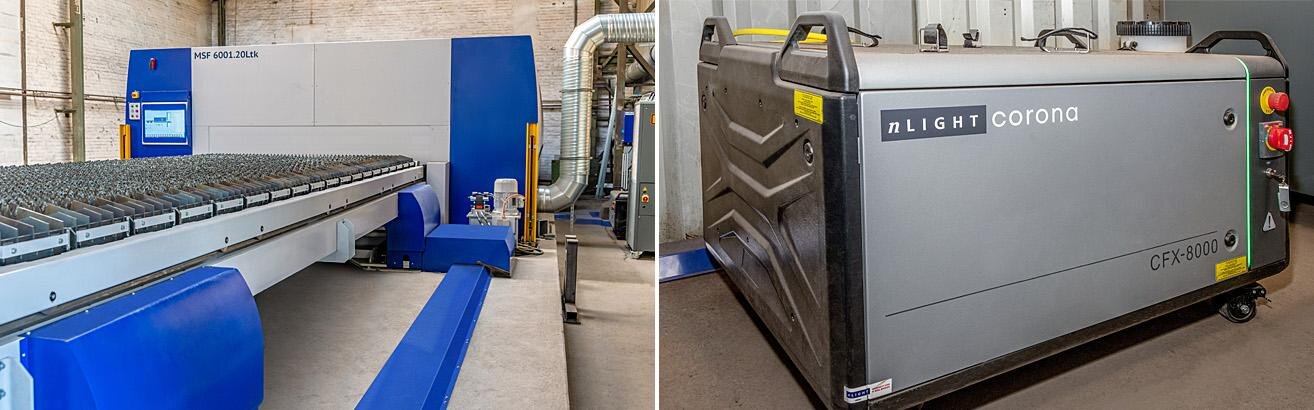
The MSF fiber laser system at Thyrolf & Uhle with rotator technology and a new type of laser source
"MicroStep's performance is top notch"
For processing a wide range of sheet thicknesses with the highest quality and speed, the steel and component manufacturer Thyrolf & Uhle invested in a 3D laser cutting system with an 8 kW laser source from nLight
Published 03.08.2021 | Erich Wörishofer
Company profile:
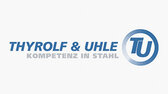
06847 Dessau-Roßlau
Germany
The steel and component manufacturer Thyrolf & Uhle GmbH offers a wide range of services – from design, forming and sheet metal processing to welded constructions, machining or model and mold making. The company, based in Dessau-Roßlau (Saxony-Anhalt, Germany), supplies customized solutions for a wide range of industries such as vehicle construction, the lifting technology industry, building construction, shipyards, the energy sector or tank construction.
Thyrolf & Uhle GmbH invested in the MSF series from MicroStep. A laser rotator for bevel cutting, for example, for weld seam preparation up to 45° with the HighYAG BIMO-FSC3 laser cutting head was integrated. The working area is 6,000 x 2,000 mm.
Machine profile:
MSF series- Working area 6,000 x 2,000 mm
- Laser bevel head for weld preparation up to 45° with auto-calibration feature (ACTG®)
- nLight fiber laser with 8 kW cutting power
- Automatic shuttle table
Thyrolf & Uhle GmbH is a widely sought-after company which realizes specialized, high-quality and complex projects for a long list of steel processing customers. While searching for a replacement solution for an outdated laser cutting system, the decision makers looked at a number of manufacturers. The company was searching for a modern solution that could process different sheet thicknesses quickly and with precision. In the end, MicroStep was chosen based on its offer of the MSF fiber laser cutter paired with a relatively “young” laser source from nLight. The Corona™ CFX-8000 fiber laser source with 8 kW cutting power enables precise cutting for thin and medium-thickness sheet metal.
Thyrolf & Uhle offers a broad range of services. Manufacturing steel products and components requires a lot of specialized equipment in order to be able to meet individual customer needs. “We work in the project business for mechanical and plant engineering companies. Our main business is building specialized machines. We manufacture according to customer requirements and do what is needed. One of our products is basically a large box filled with a wide variety of components which the customer can assemble onsite, although we do of course also offer the assembling together with the cutting,” says Frank Köppe, managing director at Thyrolf & Uhle. The services include activities as construction, forming, sheet metal processing, construction welding, machining and also model and mold making. The customers include companies like AGCO (agricultural machinery), AMMANN Schweiz AG (asphalt plants), Blohm & Voss Repair, Kirow Ardelt GmbH (crane construction), Enercon GmbH (wind turbine construction) or CTA Chemieanlagenbau GmbH (tank construction) all of whom are in need of high-quality specialized components. Thanks to the know how of its employees and well-equipped factory, Thyrolf & Uhle is capable of processing even the most complex requests.
Previous model no longer profitable – search for replacement solution launched in spring 2020
The machine park at Thyrolf & Uhle is being constantly modernized and growing all the time. The youngest member of the “family” is the MSF, a fiber laser cutting system from MicroStep. It is the fourth laser in operation replacing an outdated CO2 laser. “It was no longer able to earn its maintenance costs and was out of date in terms of maintenance and supplies,” says Frank Köppe. So, in spring 2020 a decision was made to replace it. “We had to invest. We spoke to multiple manufacturers, asked for advice on sizes and strengths that would fit us best. We have seen many machines and made a clear picture, what is important and MicroStep was in the lead,” the former production manager looks back. After detailed consultation, the decision was made to invest in an MSF fiber laser cutting system with a laser rotary head ideal for weld preparation up to 45° and with a working area of 6,000 x 2,000. The machine also includes an automated shuttle table system consisting of two individual, interchangeable cutting tables which enable simultaneously cutting on one and unloading and loading on the other.
Excellent laser source convinces in combination with MicroStep's rotator
The endless rotation head has become a kind of gold standard for MicroStep and turns cutting beveled edges like V or X cuts and even complex Y and K cuts into a “routine venture”. This is mainly due to the patented ACTG® (Auto-calibration of Tool Geometry) technology which converts the standard several hour calibration into a 5-minute automated process. What makes this solution special even in terms of MicroStep is its laser source. The Corona™ CFX-8000 is produced by the American technology manufacturer nLight. It is the first fiber laser source with programmable beam profile. Different beam profiles are suitable for different materials, thicknesses, etc. "This means that Thyrolf & Uhle can process a wider range of thicknesses than before with just one laser source – and with high-quality results in both thin and thick sheet metal," emphasizes Matthias Korn, application engineer laser technology at MicroStep Europa GmbH. This versatility is a great plus for the German company. “This laser source offers us multiple different options for our needs. We process many materials with different characteristics and thicknesses. From thin to thick, from structural steel to aluminum. We want the highest possible quality at high cutting speeds. We want to be prepared for the future,” says Mr. Köppe. The CNC cutting system has been in operation for a few weeks and and the initial results are promising. “I have been with the company for over 20 years. From the performance MicroStep delivered, this was the peak. From delivery to commissioning, we are really completely satisfied,” Mr. Köppe concludes.

"I have been with the company for over 20 years. From the performance MicroStep delivered, this was the peak. From delivery to commissioning, we are really completely satisfied."
Frank Köppe,
Managing Director | Thyrolf & Uhle GmbH
OVERVIEW OF THE HIGHLIGHTS OF THE LASER CUTTING SYSTEM:
MSF series laser cutting system with a working area of 6,000 x 2,000 mm
Thyrolf & Uhle GmbH invested in the MSF series from MicroStep, a fiber laser cutting system for process-reliable multifunctionality with a high degree of automation. The company relies on a version for sheet metal processing with a working area of 6,000 x 2,000 mm. Integrated is a shuttle table system, consisting of two cutting grids, which allows simultaneous processing inside the cutting cabin as well as loading and unloading outside. A conveyor belt for scrap disposal transports small parts and cutting waste from the cutting area into a container for manual disposal.
Laser rotator for weld seam preparation up to 45° and nLight® Corona™ CFX-8000 fiber laser source
A laser rotator for bevel cutting, for example for weld seam preparation up to 45°, has been integrated in the fiber laser cutting system. The bevel unit includes the automatic HighYAG BIMO-FSC3. The robust rotary system can be used to apply simple V and X seams as well as complex Y or K seams with micro joints to the flat material. MicroStep's patented ACTG® automatic calibration unit provides a lifetime of accurate and process-reliable results. To realize high-quality cuts in thin and medium material thicknesses at high cutting speeds, Thyrolf & Uhle relies on the Corona™ CFX-8000 fiber laser source from nLight. This is the first laser beam source with a completely fiber-guided, programmable beam quality that enables maximum performance for a wide range of metals and sheet thickness ranges. The variable adjustability of the beam parameter product (BPP) enables optimal adaptation to the respective application task. This means that when cutting mild steel with oxygen, the maximum thickness that can be cut and the process window available for cutting can be increased while using the same laser power. As a result, a significantly improved edge quality can be achieved.
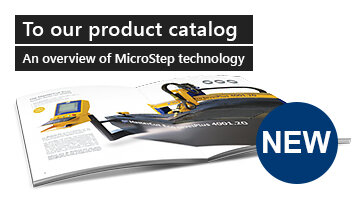
EXPERIENCE OUR SYSTEMS LIVE
in the CompetenceCenter South or North
- All four cutting technologies (laser, plasma, oxyfuel, waterjet)
- Innovative automation systems
- The latest solutions for bending and deburring
- Industry 4.0 demo factory
- Easy to reach: in the south and north of Germany
