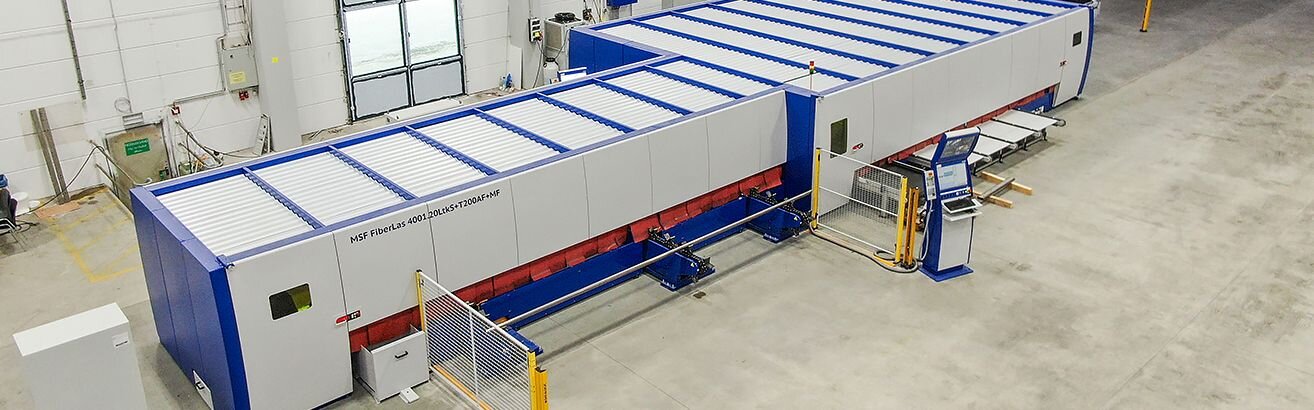
Sealpac GmbH more flexible and faster with automated 3D laser solution
Flexibility for the requirements of today and tomorrow
Sealpac GmbH, global manufacturer of automated systems for food packaging, invests in a multifunctional fiber laser for 3D processing of sheets, pipes and profiles including material handling systems with a high degree of automation
Published 11.01.2021 | Erich Wörishofer
Company profile:
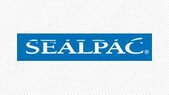
An der Kolckwiese 1026133 OldenburgGermany
The German company Sealpac GmbH is one of the world's leading manufacturers of solutions for automated food packaging.
Sealpac GmbH invested in a flexible laser cutting system of the MSF series from MicroStep. This combines technology options for pipe, profile and sheet metal processing with a high degree of automation for loading and unloading the material.
The German Sealpac GmbH is one of the world's leading manufacturers of systems for the automated packaging of food. In order to create production capacities and increase flexibility, the innovative medium-sized company invested in a fiber laser cutting system of the MSF series from MicroStep. The wide range of technologies in only one system played a major role in this investment. Because the new multifunctional 3D laser has a high degree of automation. By means of a laser rotator, sheets, pipes and profiles can be processed – material handling technologies included. For certain components, the company is four times faster in production in the first weeks after installation.
During the daily walk to the supermarket or to the butcher's shop, one very often comes into contact, at least indirectly, with the precision machines of Sealpac GmbH, a company based in Lower Saxony, Germany. The globally active high-tech company from Oldenburg develops and manufactures systems for food packaging. The employees of Sealpac follow the maxim to set new standards in automated food production and always offer the best solution. According to Sealpac, these are not only characterized by high performance and flexibility, but also by tested and reliable quality and maximum efficiency. This means: innovative spirit and precision work are part of the daily work – right from the start.
More than 33 years ago the starting signal was given in the domestic garage. Today, 250 employees work at the Oldenburg site alone, and the products are available in more than 60 countries worldwide. Industry giants such as Edeka, Wiesenhof or the Tönnies group of companies rely on Sealpac systems – but also small butcher shops, bakeries and food processors for meat, baked goods, fruit, vegetables and more. In October 2018, the sustainable and material-friendly FlatSkin® system received the ECMA Award (European Carton Makers Association) in the category "Save the Planet".
Trained and autonomous personnel at the equipment, practical experience in management
"In addition to the well-trained staff, humanity in the company is one of our strengths. Everyone knows each other by first name, the official channels are very short, the hierarchies very flat," says Samir Ramadan. He is in the production planning department at Sealpac and, like production manager Sascha Westphal, started as a machine operator. "Our managers all come from the field. That helps with all challenges. Our people program themselves; we have well-trained and autonomous personnel," says Ramadan. And this is also necessary, because often the systems have to be individually adapted to the customer's requirements – this involves accuracies in the thousandth of a millimeter range. The machine park is set up accordingly, investments in modern systems are made on an ongoing basis, and purchases must also meet production requirements for the longer term.
In 2017, managing director Jörg von Seggern, Sascha Westphal and Samir Ramadan set out to find a suitable laser cutting solution for cutting pipes and profiles. Milling machines and other technologies were to be released for other tasks and the dependence on contract cutters was to be reduced. "The aim of the new acquisition was to create free capacities", Samir Ramadan looks back. The decision makers took their time in analyzing the laser cutting systems that were available on the market. "The basic idea was a pure pipe and profile laser. We looked at many of them and the idea was born to include the processing of flat material. But we primarily process pipes and profiles," says Ramadan. After weighing up all the parameters and comparing the laser systems offered, the decision was made in favor of a multifunctional solution from MicroStep with a high degree of automation. The reason: the wide range of technology options and the resulting flexibility for the development and manufacture of the current and future product portfolio.
"We have cutting jobs, for example the processing of bone profiles, where we need
8 minutes now instead of 35."
Samir Ramadan
Production Planning | Sealpac GmbH
Machine profile:
MSF series- Working area 4,000 x 2,000 mm
- Cutting of pipes Ø 200 mm
- Laser rotator for weld preparation up to 45° with auto-calibration feature (ACTG®) + 6 kW fiber laser source
- Scanner for Additional Beveling Process (ABP)
- Automatic shuttle table
Significantly faster and more flexible with new laser cutting solution
The multifunctional laser of the MSF series was put into operation in September 2019. The CNC system with laser rotator and scanning technology for 3D processing of sheets, pipes and profiles, including a handling system for automatic loading and unloading of the material, is used exclusively for the in-house production of Sealpac GmbH.
The automated CNC fiber laser offers options for processing sheet metal on a working area of 6,000 x 2,000 mm, pipes up to 200 mm diameter and profiles up to 140 mm edge length with 6 m length can be automatically conveyed into the cabin, clamped, positioned, cut and output again. "We have cutting jobs, such as processing bone profiles, for example, where we now need 8 minutes instead of 35," says Samir Ramadan, who is also responsible for operating the cutting system. Sealpac uses the laser exclusively to process stainless steel, including single pieces, but also series up to batch size 400. Flat material is processed as standard up to 10 mm sheet thickness, pipes and profiles with a wall thickness of 2 to 6 mm.
OVERVIEW OF THE HIGHLIGHTS OF THE LASER CUTTING MASCHINE MSF 4001.20LtkS+T200AF+MT
Multifunctional laser cutting system with laser rotator for bevels up to 45° and 6 kW cutting power
Due to the solution's flexibility and versatility, Sealpac GmbH invested in a multifunctional laser cutting system from MicroStep's MSF series. The series is a precise laser all-rounder with a high degree of automation that can process sheet metal, tubes and profiles using a laser rotator and provide them with bevels, for example for weld edge preparation. The MicroStep laser rotator, including the Highyag BIMO FSC automatic laser cutting head, enables bevel cuts of up to 45°. For the laser source, the company opted for a powerful version from IPG with 6 kW cutting power. Cameras integrated in the cabin allow the operator to monitor the entire process at the control panel.
Pipe processing up to 200 mm diameter, profile processing up to 140 mm edge length and automatic material handling system for material up to 6 m long
Sealpac GmbH primarily made the investment for the processing of pipes and profiles with 6 m length. The CNC fiber laser makes both possible and combines this with a high degree of automation. Pipes from 21.6 mm to 200 mm in diameter and profiles from 30 to 140 mm edge length can be loaded, cut and unloaded. Handling is performed by the T200 pipe cutting device, including technologies for automatic loading and unloading. The cutting material is conveyed to the safety cabin via a side loading device and clamped there in a special fixture via loading modules. The size of the cut parts is determined in advance by sensor. The loading modules return to their initial position while the clamping device transports the pipe to the actual cutting zone and rotates it to the required position during the cutting process. Cut parts and waste shorter than 500 mm, as well as longer components, are conveyed to two separate containers outside the safety cabin.
Sheet metal processing of flat material in a sheet size of 6,000 x 2,000 mm
In addition to pipe and profile processing, the MSF at Sealpac also enables flat material to be cut to size. Plates with a size of up to 6,000 x 2,000 mm can be processed by laser rotator and thus bevels of up to 45° can be applied. The material is loaded and unloaded via a fully automatic shuttle table system.
Laser scanner for capturing profiles and ABP technology for subsequent weld edge preparation on metal sheets
The company achieves even greater precision in profile processing by using innovative MicroStep solutions. The pipe cutting device rotates the profile into position, and a laser scanner installed on the gantry records the surface geometry in the cutting area of the workpiece. The 3D CAM software mCAM® compensates for the production-related deviations from the ideal contour, corrects the parameters based on the 3D scan and sets the cutting paths accordingly, resulting in a significant improvement in cutting quality. In addition, MicroStep's ABP technology has been added to the system. Using the rotator and the multifunction scanner, which is also used for the 3D acquisition of the profiles, already cut sheet metal parts are scanned and bevels are subsequently applied. This eliminates the need for time-consuming material handling to an additional (robot) workstation and makes it possible to subsequently apply weld edge preparations even for thicker material.
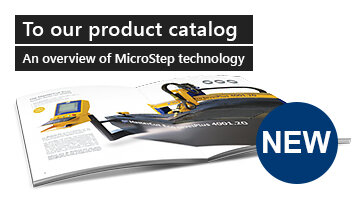
EXPERIENCE OUR SYSTEMS LIVE
in the CompetenceCenter South or North
- All four cutting technologies (laser, plasma, oxyfuel, waterjet)
- Innovative automation systems
- The latest solutions for bending and deburring
- Industry 4.0 demo factory
- Easy to reach: in the south and north of Germany
