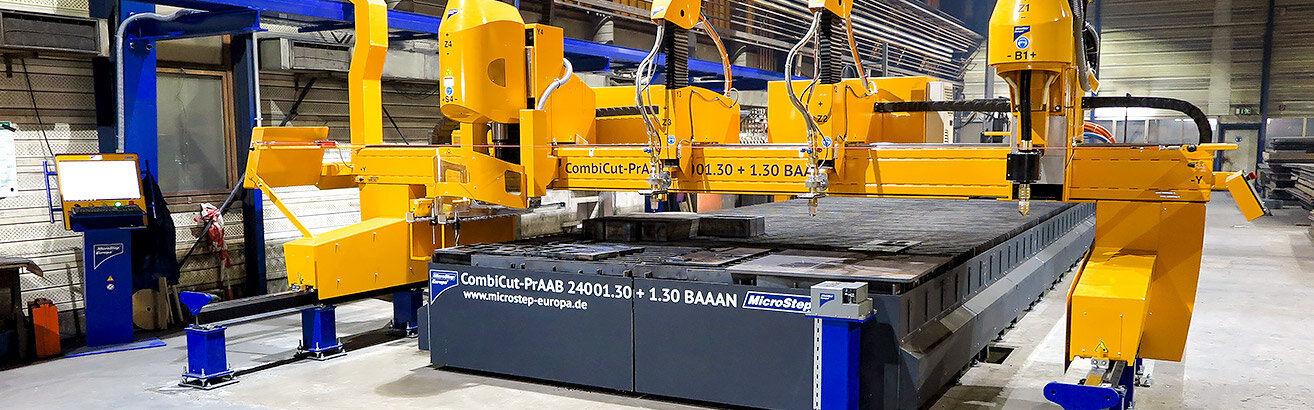
MAP Prinzing Brennschneidtechnik relies on multifunctional cutting center with two gantries
"3D cutting head and drilling rig tipped the scales for MicroStep"
For maximum flexibility in production, Prinzing Brennschneidtechnik GmbH invested in the CombiCut series with two gantries for bevel cutting, oxy-fuel cutting, drilling, tapping, countersinking and marking
Published 03.09.2018 | Erich Wörishofer
Company profile:
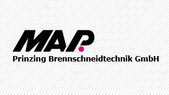
Prinzing Brennschneidtechnik GmbH & Co. KG located in Gingen an der Fils in southwest of Germany specializes in the
production of custom parts using plasma and oxyfuel cutting technologies. Annealing, sandblasting, edging and welding
are all part of the extensive range of Prinzing’s services that small locksmiths as well as large companies can rely on thanks
to the company’s speed and flexibility in manufacturing.
Machine profile:
CombiCut series- Working area 24,000 x 3,000 mm
1. Gantry
- Plasma rotator for weld preparation up to 50° with auto-
calibration feature (ACTG®) - 2x 2D oxyfuel
- Drilling up to Ø 40 mm and tapping up to M33
2. Gantry
- 3x 2D oxyfuel
- Drilling up to Ø 40 mm and tapping up to M33
- Micro-percussion marking
In order to renew its machine park and to become faster and more flexible in production, the Baden-Württemberg based company MAP Prinzing Brennschneidtechnik GmbH was looking for new cutting machinery. The job cutting business found their solution at MicroStep – and invested into a complex CombiCut machine. This multi-functional system enables bevel cutting with plasma, 2D oxyfuel cutting, drilling, tapping, countersinking and marking with a powerful combination of two gantries.
About 50 kilometers east of Stuttgart in Germany lies the Baden-Württemberg municipality of Gingen an der Fils. Here, a modern job cutting company is operating their production facility. Small-sized locksmiths as well as large steel construction companies rely on the products of MAP Prinzing Brennschneidtechnik GmbH. Thanks to decades of experience, the contractor produces parts from small batches of 1 up to 500 pieces. All this with innovative machines that make Prinzing Brennschneidtechnik ready to handle even the most urgent orders. These are usually handled with a two-shift operation and, if necessary, a third shift may be added on short notice.
The most common tasks for this sheet metal service include production of custom parts using plasma and oxyfuel cutting technologies. On average, 300 tons of raw material are processed every month. Prinzing Brennschneidtechnik has recently invested into a multi-functional cutting system which offers a multitude of processing options. After an extensive search for the right cutting solution, Hans Prinzing‘s management has decided to purchase a combined plasma and oxyfuel
machine with supplemental drilling technology. “We looked at the entire market and also attended several technology demonstrations. All the technology combinations were known beforehand. The decisive factor for MicroStep was the bevel cutting equipment and the drilling unit. The drill was the most powerful among all competitors,“ Hans Prinzing looks back.
And so, in order to achieve maximum flexibility in production, the company Prinzing opted for a special solution which integrates two gantries in one cutting
machine over a table sized 24,000 x 3,000 mm. The first gantry is equipped with a plasma rotator for bevel cutting and two straight oxyfuel cutting heads for parallel
cutting of thicker materials. The drilling spindle enables drilling of holes up to 40 mm in diameter and tapping up to M33. At the request of the company, a fully
automatic tool magazine for 16 tools has been added to facilitate the wide range of jobs to be done on the machine.
The second gantry also contains a drilling unit for drilling up to 40 mm, tapping up to M33 and countersinking. In addition, there are another three 2D oxyfuel
cutting heads and a punch marker. “There were no problems with the commissioning even though our existing table was integrated together with our suction system. We are satisfied with the performance, the drilling works great,” concludes Mr. Prinzing.
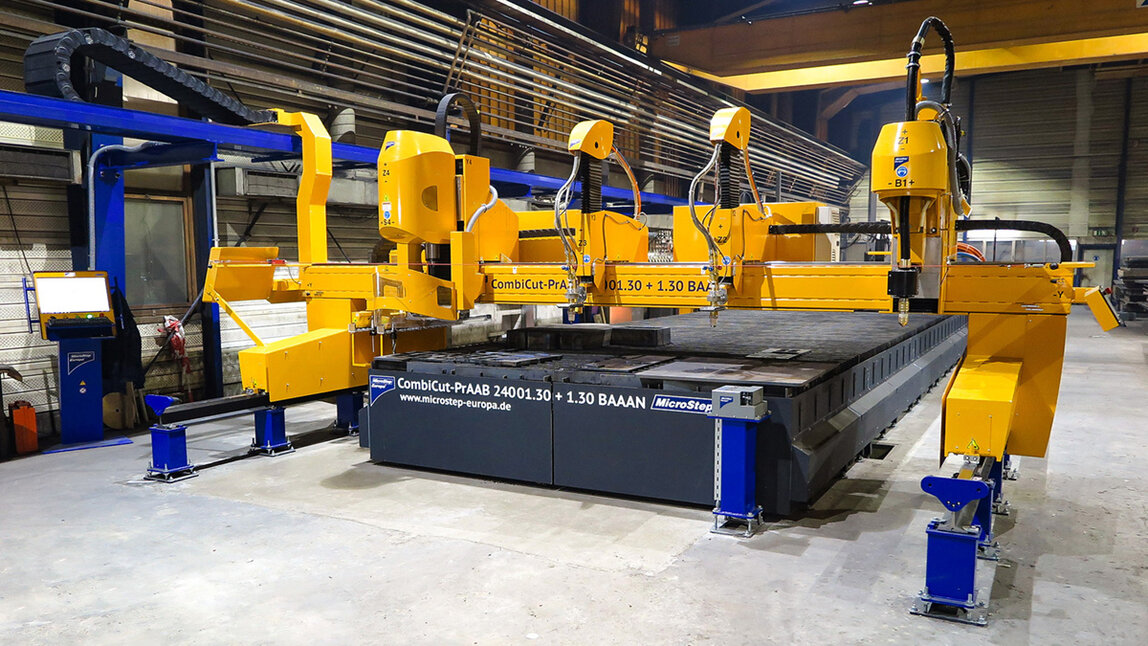
MAP Prinzing Brennschneidtechnik GmbH, based in Baden-Württemberg, decided to use a plasma-autogenous combination of the CombiCut series. The flexible cutting system allows plasma bevel cuts, oxy-fuel cutting, drill holes, threads and markings on two gantries.
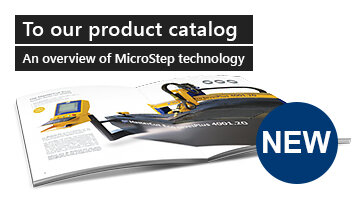
EXPERIENCE OUR SYSTEMS LIVE
in the CompetenceCenter South or North
- All four cutting technologies (laser, plasma, oxyfuel, waterjet)
- Innovative automation systems
- The latest solutions for bending and deburring
- Industry 4.0 demo factory
- Easy to reach: in the south and north of Germany
