
The MG can quickly process pipes, sheets, profiles and domes at the company Steg
Decision for highest quality regardless of the application
Metallbau Steg invests in a new CNC plasma cutting machine for a wide range of processing - whether for plate, pipe, profile or dome
Published 27.02.2017 | Erich Wörishofer
Company profile:
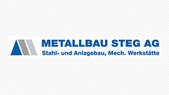
Alustraße 203940 StegSwitzerland
The company Metallbau Steg AG has been active since 1970. The field of activity of the family-owned company ranges from the production of chemical apparatus, the construction and assembly of telecommunication systems, general plant and apparatus engineering to the mechanical production of components.
Metallbau Steg (CH) is investing in a new system for a variety of production requirements: Cutting of contours, weld seam preparations and holes as well as drilling, countersinking, tapping, marking and punching – no matter whether for sheets, pipes, profiles or domes.
Metallbau Steg AG has been active at its headquarters in Steg (Valais) since 1970. The company's field of activity in the southwest of Switzerland ranges from the manufacture of chemical apparatus, the construction and assembly of telecommunications equipment, through general plant and apparatus engineering to the mechanical manufacture of components. In 2013 the company faced the challenges of the local market and decided to invest in a multifunctional CNC cutting system from MicroStep. The guiding machine type MG was able to cope with all requirements without any problems. These were clearly defined from the beginning: Bevel cutting, drilling, pipe cutting as well as the processing of domes – and all this with the highest possible precision.
"We looked at quite a few things," said Ruedi Seiler, Managing Director of Metallbau Steg AG, who contacted the specialist dealer LWB Weldtech AG. MicroStep, partner of LWB Weldtech AG, was finally able to offer the perfect solution for the Swiss company. Together with Stefan Seiler – also Managing Director of Metallbau Steg AG – the concrete key data of the system were fixed. With a total working area of 6,000 x 3,700 mm, almost every common sheet metal panel format can be processed. Due to the high-performance power source HiFocus 360i from Kjellberg Finsterwalde, bevel cuts up to a material thickness of 40 mm in mild steel can be realized at any time. Not only flat sheets, but also geometric workpieces such as pipes, profiles as well as domes can be provided with V-, Y- and K-bevels but also variable bevels which are necessary for a multitude of welding processes.
Bevel cutting
The automatic MicroStep calibration system ACTG® is used for absolutely precise bevel cuts. The entire calibration process runs automatically and eliminates deviations in the hundredth of a millimeter range. The automatically retensioning torch holder of the bevel cutting head already ensures that the deviation is no more than 0.5 mm even after a torch collision. The rest is done by the control of the calibration station: For this purpose, the exact end points of the torch tip are measured at different rotation (X, Y and Z coordinates). Based on the measured deviations, the control system calculates all the necessary correction values, which are automatically applied during the next cutting process. This automatic calibration system ensures a completely new quality with regard to bevel cutting. It significantly improves the precision and dimensional accuracy of the cutting process, eliminates the need for time-consuming mechanical adjustments and significantly increases the productivity of the system.
Pipe and profile processing
The same applies, of course, to pipes, which can easily be longer than 6,000 mm. The processing of round or polygonal profiles is carried out on this machine in a specially designed pipe processing shaft and enables the cutting of pipes with a diameter of 30 to 700 mm (round pipes). The advantage of this design is the flexibility to process both pipes and plates. If required, the pipe shaft integrated in the cutting table can be covered with frame elements and used over its entire surface as a vacuumed cutting table. For loading and unloading of pipes, the machine gantry moves into the parking position. Pipes can thus be securely placed on the support stands by crane and clamped in the jaw chuck.
Machine profile:
MG series
- Working area 6,000 x 3,700 mm
- Cutting of pipes Ø 30 to 700 mm up to a length of 6,000 mm
- Cutting of domes Ø 500 to 2,500 mm
- R5 rotator for weld preparation up to 50° with auto-calibration
feature (ACTG®) - Drilling up to Ø 40 mm and tapping up to M33
Dome processing
A real highlight and unique selling point is the equipment of the system with a special table, which allows the processing of domes up to 2,500 mm diameter. Relatively high deviations from one dome to the other – even within a single batch – are not unusual and require an intelligent cutting system that takes this factor into account and can compensate for it. In order to determine all deviations in curvature and shape, the MicroStep® cutting system automatically carries out a series of measurements on the domes when the program is started. The control system calculates the individual measurement data with the general geometric formula of the dome and integrates it into the current cutting plan. The system thus reacts intelligently and autodidactically to deviations and ensures maximum precision on the finished product, both for individual custom-made products and for large series. Even with alternative processing with robots, deviations cannot be compensated for to this extent, since robots merely repeat the instructed work sequence exactly each time. Completely apart from manual processing methods, where every cutout must first be calculated, designed, cut and finally laboriously reworked.
Drilling, tapping, countersinking
Drilling, tapping and countersinking as well are indispensable for Metallbau Steg AG. This was also the opinion of the production team that was involved in the decision for the new cutting system. The drilling application can also drill, thread (up to M33) and countersink in the thickest materials up to 40 mm Ø. Naturally, everything is also combined in one cutting program, so that the operator can remove the perfectly drilled and cut component directly from the cutting table. The advantages: No time-consuming component handling to the next system, no further clamping and no reprogramming of the component on the machining center – the entire processing takes place on one system. Including tapping and countersinking. An 8-fold tool magazine is available for fast process and tool changes, in which the tools are safely protected from cutting dust and damage. After drilling, for example, it is possible to change automatically to a tapping or countersinking tool. After the processing is complete, the system switches to the plasma torch and cuts all protruding contours (2D as well as 3D). All cutting kerfs are of course automatically compensated for to ensure optimum dimensional accuracy of the finished component.
Ruedi Seiler and his team are proud of their investment in the new, intelligent multifunctional system. In the meantime, the system has been put into operation and handed over on time, as discussed in the project planning phase. 100% productivity – that was the common goal and is the goal we have now reached!
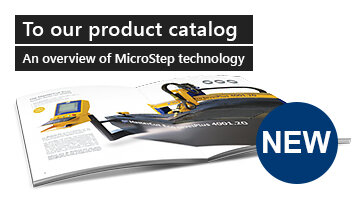
EXPERIENCE OUR SYSTEMS LIVE
in the CompetenceCenter South or North
- All four cutting technologies (laser, plasma, oxyfuel, waterjet)
- Innovative automation systems
- The latest solutions for bending and deburring
- Industry 4.0 demo factory
- Easy to reach: in the south and north of Germany
