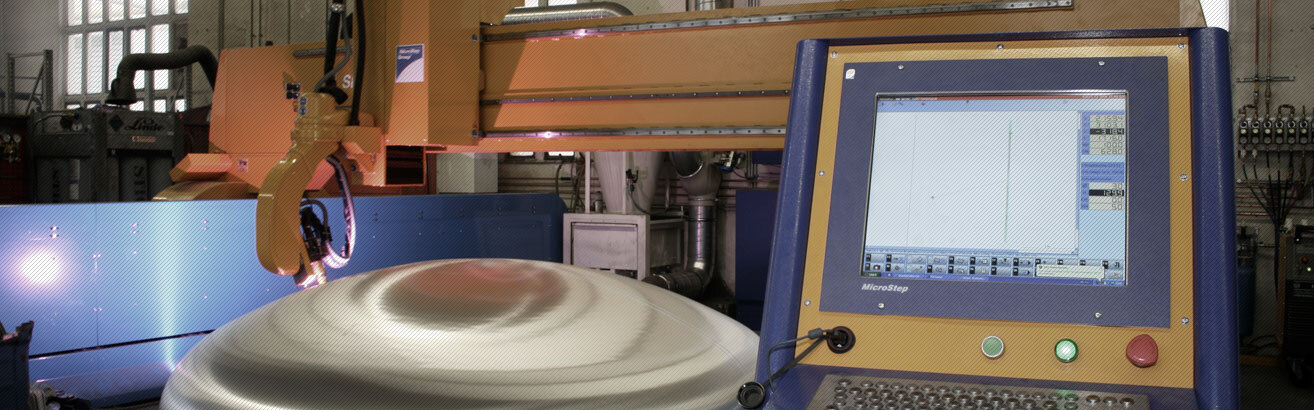
Feldbinder counts on machines from MicroStep and uses several systems in the production process
"Technical, innovative and commercial aspects spoke for MicroStep"
Feldbinder Spezialfahrzeugwerke GmbH has trusted in MicroStep for more than ten years and relies on special solutions for cutting, which are "irreplaceable"
Published 27.03.2017 | Erich Wörishofer
Company profile:
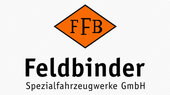
Feldbinder is one of the largest European manufacturers of special vehicles for the commercial vehicle industry. Founded in 1975, the company manufactures various silo vehicles and tank trucks, railroad cars and containers made of aluminum and stainless steel for the transport of liquid, granulated and powdery materials.
Machine profile:
DRM series- Cutting and trimming of domes Ø 500 – 3,200 mm up to a height of 760 mm
- 3D plasma rotator with tilting 90° for weld preparation on domes
PLS series
- Working area 9,000 x 2,500 mm
- 2D plasma
- Felt pen marking
PLS series
- Working area 9,000 x 2,500 mm
- Cutting of pipes Ø 30 – 300 mm and hollow sections up to a length of 9,000 mm
- Plasma with 90° automatic tilting in Y axis
MG series
- Working area 7,500 x 2,500 mm
- 2D plasma
- Drilling up to Ø 22 mm and tapping up to M16
MasterCut series
- Working area 8,000 x 2,500 mm
- 2D plasma
- Special marking via felt pen
.jpg?w=535&h=300)
The most important machine at Feldbinder is the SMG-PR, which has been in use since 2008. The plasma cutting machine, now sold as DRM series, is used for dome processing. Domes with a diameter of 500 to 4,000 mm can be processed, chamfers up to 90° are possible.
A coincidence was the inspiration for the partnership between Feldbinder Spezialwerkzeuge GmbH and MicroStep Europa GmbH. In the meantime, this cooperation has lasted for more than ten years and has produced many a new development from which both sides still benefit today. "We have achieved a lot together", says Heiko Kunze, responsible for maintenance. The manufacturer of special vehicles has five systems in use from the world market leader in automated plasma cutting. For Feldbinder, even after many years, they are "irreplaceable".
Whether silo vehicles and tank trucks, railroad wagons or containers made of aluminium and stainless steel: the name Feldbinder stands for innovative and high-quality products throughout Europe. The manufacturer of special vehicles for the commercial vehicle industry supplies almost every sector under the company motto: We produce "lightest commercial vehicles with the largest possible volume and long service life".
The owner-managed company with its 950 employees manufactures at two locations: at the headquarters in Winsen (Luhe) near Hamburg, silo vehicles are produced from aluminum – at the plant in Lutherstadt Wittenberg, stainless steel is processed in addition to aluminum. The focus here is on the production of tank trucks, containers and rail wagons.
Customers from all over Europe rely on the German manufacturer's pressure vessel vehicles for the transport of liquid, granulated and powdery materials - from the mineral oil industry and food producers to chemical and building material manufacturers. In order to be able to offer the highest possible quality and individuality for the global market, Feldbinder relies on a high degree of in-house production using a great deal of know-how and advanced technology.
Trusting partnership right from the start
For more than ten years now, Feldbinder has been relying on MicroStep cutting systems for the cutting of its customer-specific special constructions. "Technical, innovative and commercial aspects spoke for MicroStep. The service fits, we have achieved a lot together", says Heiko Kunze, head of maintenance.
However, coincidence was helpful in 2004 when the two companies made their first contact. From the history the vehicle specialist had always worked with products of the company Kjellberg. During a cutting test in the demonstration center in Finsterwalde, Heiko Kunze, at that time a member of the prefabrication department, discovered the MicroStep reference system in an adjacent building. The cutting results were convincing and the then still unknown machine manufacturer came into focus. "We had two cutting machines in use and wanted to improve technologically. One manufacturer could not realize our wishes, the other had technical reservations and the special solution would have been much more expensive than MicroStep. The machines from MicroStep were already very flexible", Kunze looks back.
Cutting covered with five MicroStep machines
So MicroStep convinced itself of the possibilities in the construction of special machines in the production in Slovakia. The first CNC machine at Feldbinder, which is still in use today, is a plasma cutting machine of the PLS series with technology for 2D cutting, for pipe cutting and with a marking unit. "At MicroStep, everything was already cast from a single mold back then. Based on the experience gained with the first system, the others were then added," says Kunze. Investments were made in four more cutting machines between 2005 and 2012. Since then, MicroStep systems cover the entire plasma cutting needs of the vehicle manufacturer. Their primary task: precise and economical 2D cutting and pipe cutting.
CNC machines have paid off
The most important machine at Feldbinder is the SMG-PR, which has been in use since 2008. The plasma cutting machine, now sold as DRM series, is used for dome processing. On request and in close cooperation with the vehicle manufacturer, this machine type was designed and further developed by MicroStep. "We simply wanted to cut contours into the done. That's when we saw what basis MicroStep has in terms of engineering to realize special solutions". Domes with a diameter of 500 to 4,000 mm can be processed with the CNC system. The specially developed rotator allows bevel cutting for weld edge preparation up to an inclination of 90°.
The dome cutting system replaced a robot, which required a lot of time and know-how to operate. This was to be made easier and more effective – and it succeeded. "The systems run and do what they are supposed to do. They have paid for themselves without major downtimes. Especially the machine for dome processing is not outdated after eight years and simply cannot be replaced by anything," emphasizes Heiko Kunze.
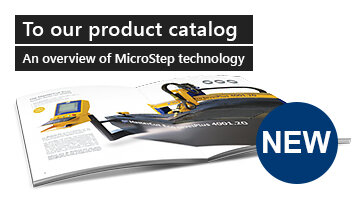
EXPERIENCE OUR SYSTEMS LIVE
in the CompetenceCenter South or North
- All four cutting technologies (laser, plasma, oxyfuel, waterjet)
- Innovative automation systems
- The latest solutions for bending and deburring
- Industry 4.0 demo factory
- Easy to reach: in the south and north of Germany
