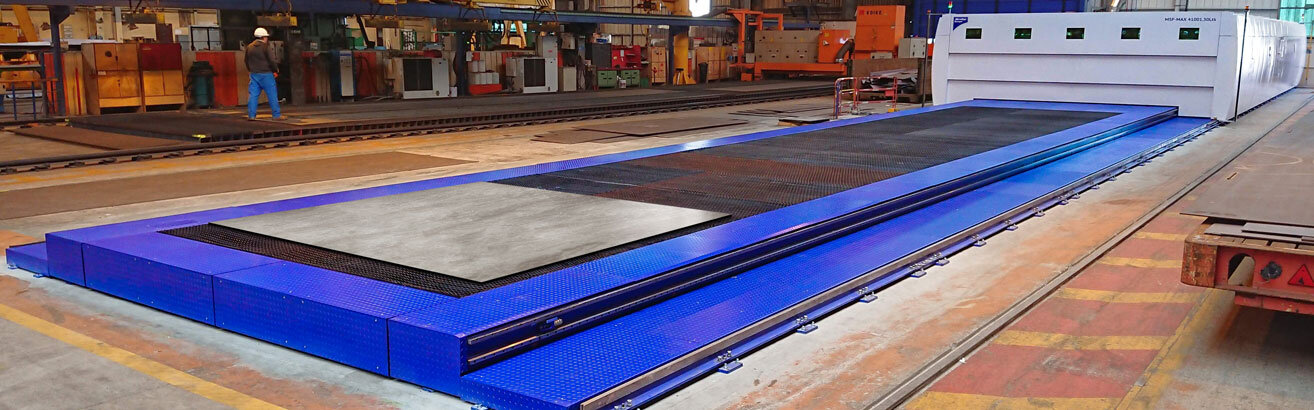
Highly satisfied: Shipbuilder Chantiers de l'Atlantique invests in the MSF Max
MSF Max: Successful maiden voyage at traditional shipyard
French cruise ship manufacturer Chantiers de l'Atlantique significantly increases its efficiency and cutting quality with the new laser giant from MicroStep
Published 23.05.2019 | Erich Wörishofer
Company profile:
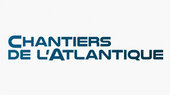
Avenue Antoine Bourdelle44613 Saint-Nazaire
France
Located in Saint-Nazaire on the French Atlantic coast for more than 150 years, Chantiers de l'Atlantique is a shipbuilding company dedicated to maritime construction and the operation of floating structures in general. Thanks to an extensive network of subcontractors and modern industrial facilities, the company is a leader in the design, construction, erection and commissioning of highly complex ships and maritime installations.
The 150-year-old company Chantiers de l'Atlantique relies on MicroStep technology. The renowned shipbuilding company invested in the MSF Max series. The picture shows a design for the ship MSC WORLDCLASS, which can take 6850 passengers on board.
The shipyards of Chantiers de l'Atlantique (formerly STX France) on the Atlantic coast have a long tradition of building cruise ships. Many of the ships were among the largest at the moment they were launched. The most recent testimony to the impressive architecture is the "Symphony of the Seas", completed in 2018, which bears the title "Largest cruise ship in the world" and impresses with ten-deck high water slides, climbing wall and imposing furnishings. More recently, the company has also focused on the production of offshore renewable energy systems. When it comes to machinery, the company has relied on the MSF Max series since 2018. With the new laser giant from MicroStep for large-format cutting tasks and a length of 41 meters, "efficiency has been significantly increased".
Until 150 years ago, Saint-Nazaire was only a small harbor village in western France on the Atlantic Ocean. Its strategic location close to the mouth of the Loire river proved to be extremely important with the beginning of the industrial revolution. In 1861 John Scott was commissioned by a Scottish shipyard to settle a new shipyard and to push ahead with the construction of the very first ship, the "Immpératrice Eugénie". Since that time, shipyards in Saint-Nazaire have carried out breathtaking projects, often requiring the most modern technologies to be able to be realized.
So it is not surprising that over the years this small French town has become the birthplace of some of the largest ships of their time. Among them the currently largest cruise ship in the world, the "Symphony of the Seas", built by the traditional shipyard Chantiers de l'Atlantique. A long way from the small beginnings over 150 years ago to the big shipyard: more than 2,700 employees and more than 500 subcontractors with 5,000 workers are at work every day to turn visions into reality.
"The idea was to optimize our production with a new and efficient system".
This requires full commitment of the workers but also of the machines. In order to build the largest cruise ships in the world, extraordinarily large parts are necessary. Many of these are needed, and they must also be cut with great precision. "We cut about 1,600 meters of material every day," says Silvere Destrem, project manager of the traditional company. The shipyard was intensively searching for the right solution for this demanding task - after careful consideration, Chantiers de l'Atlantique decided to invest in the MSF Max series. The working surface of the new MicroStep laser giant at the French specialist is 41 m long and has two 20 x 3 m cutting zones. The working area consists of a table with efficient sectional suction areas, which is recessed into the floor of the production hall to allow easy access during loading and unloading. The special feature: The safety cabin including cutting gantry required for a fiber laser is mobile and, as a result, there are always sufficient areas available on the system for parallel loading, cutting and unloading. No valuable processing time with the laser is lost for loading and unloading the system.

“The quality of the cut pieces is better than with our old machine. The efficiency has increased. We have the
opportunity to develop new products in the manufacturing.”
Silvere Destrem
Project Manager | Chantiers de l’Atlantique
Machine profile:
MSF Max series- Working area for sheets 2x 20,000 x 3,000 mm, total effective length 41,000 mm
- Laser bevel head for weld preparation up to 45° with auto-calibration feature (ACTG®)
- 8 kW fiber laser source
- Mobile safety cabin with
2x DRM-PL series
- Working area 20,500 x 20, 500 mm
- Plasma rotator for weld preparation up to 50° with auto-calibration feature (ACTG®)
- Sand blasting unit for primer removal + plasma marking
- Operator platform with MMI console on the gantry
- Automatic plate edge detection
- Inkjet marking
The older CNC laser machine at the shipyard was a CO₂ type. Even though CO₂ lasers have certain advantages, such as the ability to cut different materials and deliver smoother cut surface especially in bigger thicknesses, they are less efficient and require regular maintenance of the laser beam path, with the setup and alignment of the mirrors in the beam path limiting the maximum length of the machine setup. For larger-scale applications, the CO₂ laser source needs to travel with the gantry while maintaining beam path geometry at a required
precision. That brings several design and production challenges – the more complicated the system, the more demanding it is in terms of maintenance and the higher is the probability of downtimes. “The idea was to improve our workshop with a modern and efficient machine,” explains Mr. Destrem. Fiber laser
technology eliminates several of CO₂’s setbacks. Its efficiency is much higher and the optical fiber that guides the laser beam is not limited by length and requires almost no maintenance. “An easy-to-use-and-maintain concept was an
important criterion in our decision process.”
The machine is equipped with a 3D bevel cutting with an 8 kW laser source that allows Chantiers de l’Atlantique to make weld edge preparation on parts up to 20 meters long and up to 16 mm thick with bevel angles ranging up to 45°. The system is easy to use and maintain: accuracy and long-term stability of the machine’s geometry that is essential for accurate bevel cutting is ensured by MicroStep's patented auto-calibration system ACTG®. All the operator needs to do is to swap the cutting nozzle with a calibration jig and initiate the automatic calibration process – if any inaccuracies are detected, the machine will automatically adjust its movements to compensate for the measured mechanical
deviations.
Because of the large machine size in this particular case, the ACTG calibration station is placed in a combined technological station that is mounted directly on the gantry and is ejected during the calibration process. The station also contains other equipment – a pad for calibration of the capacitive height sensor inside the laser head, as well as a nozzle cleaning system consisting of a camera and a wiping brush. In addition, high absolute accuracy of the machine (approx. 0.2 mm at room temperature) has been ensured by a positioning tolerance compensation feature, based on precise initial machine measurement with a laser tracker device.
After a few months in production the feelings are positive. “The quality of the cut pieces is better than with our old machine. The efficiency has increased. We have the opportunity to develop new products in the manufacturing,” concludes Mr. Destrem.
OVERVIEW OF THE HIGHLIGHTS OF THE LASER CUTTING SYSTEM MSF MAX
Laser giant with two working zones over a total length of 41,000 mm
The MSF Max system, which was specially developed for the needs of the shipbuilding industry, has a total length of 41,000 mm at the French cruise ship manufacturer, which can be entered via a safety cabin. Two working zones, each with a working area of 20,000 x 3,000 mm, can be used effectively for processing the material as well as for parallel loading and unloading.
Laser rotator for weld edge preparation up to 45° with automatic calibration unit integrated on the gantry
The cutting system at Chantiers de l'Atlantique is equipped with a laser rotator for cutting simple V and X seams, as well as complex V or K seams with a micro joint. The endless rotating bevel unit allows bevel cuts up to 45°. Chantiers de l'Atlantique thus applies weld preparations to parts up to 20 m long with thicknesses up to 16 mm.
The process reliability and lasting precision of the machine is guaranteed by the patented automatic calibration system (ACTG) developed by MicroStep. The ACTG station has been integrated together with the calibration pad for the capacitive height sensor and a nozzle cleaning system in a combined technological station, which is mounted directly on the gantry and is extended in case of calibration.
Mobile safety cabin with integrated laser source and control console
The laser source and the control console were integrated in the moving safety cabin, which with a size of 20,000 x 3,000 mm forms the cutting zone, for smooth and uncomplicated handling of the fiber laser cutting system. As laser source an IPG fiber laser with 8 kW cutting power was integrated.
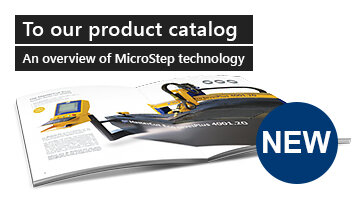
EXPERIENCE OUR SYSTEMS LIVE
in the CompetenceCenter South or North
- All four cutting technologies (laser, plasma, oxyfuel, waterjet)
- Innovative automation systems
- The latest solutions for bending and deburring
- Industry 4.0 demo factory
- Easy to reach: in the south and north of Germany
