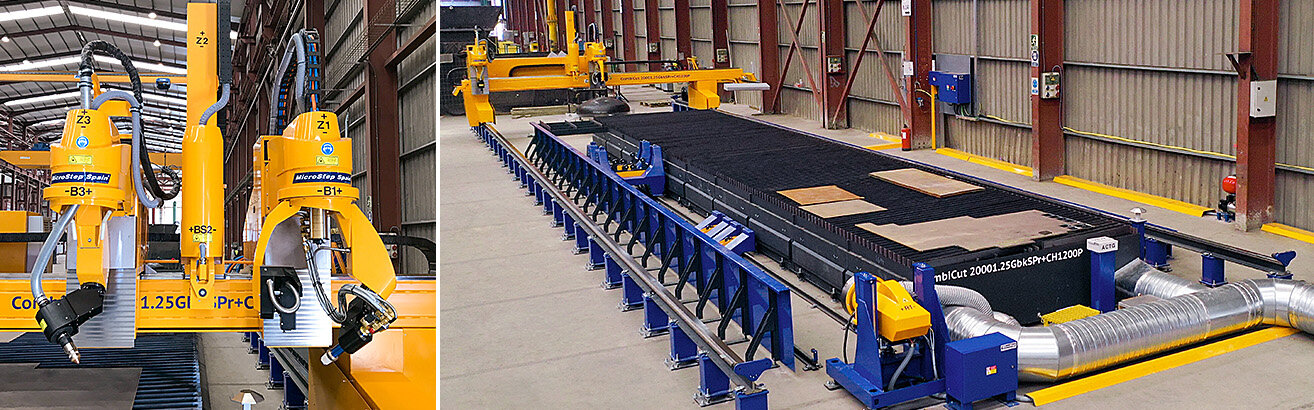
A cutting center with oxyfuel rotator, plasma rotator and more
Combined plasma cutting system for enormous efficiency and flexibility
The Spanish Caldererías Indalícas SL invested in a system for processing sheet metal, pipes and profiles with two bevel tools – a plasma rotator and an oxyfuel rotator.
Published 20.05.2020 | Erich Wörishofer
Company profile:
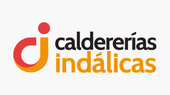
Ctra. Carboneras, N341, Venta del Pobre; 04114 Lucainena de las Torres, Almeria
Spain
The Spanish Caldererías Indalícas SL is specialized in metal construction, pressure vessel construction, boiler manufacturing and industrial plants and offers its customers, which now include renowned companies worldwide, an all-round service.
The Spanish metal construction company Caldererías Indálicas invested in a multifunctional system for 3D processing of plates, pipes and domes. Two rotators with different cutting technologies extend the possibilities for bevel processing.
The Spanish metalworking company Caldererías Indalícas SL specializes in metal structures, industrial plants and boiler construction. The company, which has 450 employees, invested in a MicroStep multifunctional cutting center, generating an enormous increase in efficiency and flexibility. The new technology includes a wide range of processing options – among other things, a plasma rotator and an oxyfuel rotator enable great possibilities for 3D cutting of plates, pipes and domes.
Narrow alleys, small white houses, gardens and palm avenues. Here in a Mediterranean bay lies the port city of Almeria in southern Spain. Where the main economic sector of the port exports agricultural products to distant countries, the Caldererías Indalícas SL is also at home. Founded in 1993, this limited liability company offers an all-round service – from design to manufacture, assembly and repair – and specializes in metal constructions, pressure vessel construction, boiler production and industrial plants. An enormous focus is placed on the topics of quality, environment and occupational safety in order to satisfy customers in the best possible way. The high standards pay off, the high-quality products are in demand. The company grew continuously and now counts renowned companies throughout Europe, South America and Africa to its customers. Today Caldererías Indálicas has a team of 450 employees in five divisions: Engineering & Projects, Production, Installation & Maintenance & Commissioning, Administration & Safety and Environment.
Objective of the acquisition: To automate processes
Last year, the metal construction company and container specialist invested in a new cutting technology to be able to meet the increasing and more individual customer requirements quickly and precisely. In doing so, the company relied on the exact analysis of the in-house processes and needs by MicroStep experts. "The customer needed to automate a number of very different processes," recalls Joan Alejo, responsible engineer for technology and marketing at MicroStep Spain. This included 2D and 3D cutting on flat material with fine plasma, pipe cutting of all types, and cutting of domes. "Dome processing, in particular, was previously a difficult, tedious and, above all, time-consuming task, given the number and complexity of the holes," says Joan Alejo.
Machine profile
CombiCut series- Working area 16,000 x 2,500 mm
- Cutting of pipes up to a length of 1,000 mm
- Cutting of domes Ø 500 to 4,500 mm
- Plasma rotator for weld preparation up to 45° with auto-calibration feature (ACTG®)
- Oxyfuel rotator for weld preparation up to 65° with auto-calibration feature (ACTG®)
- 3D scanner + mScan technology for compensation of the production-related deviation of dome shape by adjusting the
generated cutting paths according to the true scanned shape of dome - Scanner for Additional Beveling Process (ABP)
The solution: One system instead of different manual processing steps
For Caldererías Indálicas, the MicroStep solution represented a radical change in the manufacturing method. Whereas in the past, different workers used to draw contours by hand and cut with several machines, today a combined fine plasma cutting machine from the CombiCut series automatically does the job. The system was equipped with a plasma rotator and an oxyfuel rotator for 3D processing of different material thicknesses and geometries.
The multifunctional system enables 3D sheet metal processing on an area of 16,000 x 2,500 mm, flexible pipe processing of 3D geometries with a length of 12,000 mm and a diameter of up to 1,000 mm as well as the processing of domes up to 4,500 mm in diameter on a separate dome cutting table at one end of the system.
The system is equipped with a laser scanner and other technologies to significantly increase the cutting results during dome cutting (mScan®) or to apply weld seam preparations to already cut components afterwards (ABP®).
THE HIGHLIGHTS OF THE PLASMA OXYFUEL CUTTING SYSTEM:
This flexible system at the Spanish metalworking company features two rotators with different cutting technologies for 3D processing of sheet metal, pipes and domes. A plasma rotator enables variable bevels, with an XPR 300 from Hypertherm as the plasma power source. MicroStep has also transferred and adapted the principle of the endlessly rotating bevel unit to oxyfuel cutting technology. For Caldererías Indalícas, the installed oxyfuel rotator, which allows chamfers of up to 65°, brings an enormous gain in production possibilities for 3D processing of thicker material.
The complex CNC cutting system enables flexible 2D and 3D processing of sheet metal on a working area of 16,000 x 2,500 mm.
A pipe cutting device was integrated in the CombiCut at the Spanish company, which automatically rotates the workpieces into position. This automatic device is designed for pipes up to 12,000 mm long and up to 1,000 mm in diameter.
In addition to plate and pipe processing, it is also possible to apply contours and bevels to domes Thus, on a special dome cutting table, which was installed at one end of the plant, the processing of bottoms up to 4,500 mm in diameter is possible. MicroSteps mScan® technology ensures unparalleled precision in dome processing: the surface of the dome is determined in advance using a laser scanner. Height and diameter of the dome, curvature radius and corner radius are detected. . The geometric data is imported into the mScan® software, the system compensates for production-related deviations from the ideal contour, corrects the parameters using the 3D scan and sets the cutting paths with the appropriate precision.
Subsequent bevel processing with ABP® technology
Another component of the CombiCut version at Caldererías Indalícas SL is MicroStep's ABP® (Additional Beveling Process) technology: this system was developed to enable subsequent beveling on a cutting machine for weld edge preparation. Using the multifunction laser scanner integrated on the gantry, components that have already been cut are scanned and flexible chamfers are applied. This eliminates costly material handling on an additional (robot) workstation. Thus, even with higher material thicknesses, weld edge preparations can be applied subsequently and material can be saved.
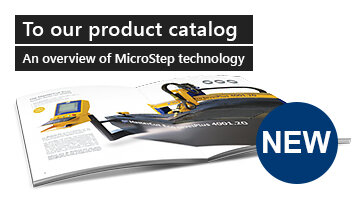
EXPERIENCE OUR SYSTEMS LIVE
in the CompetenceCenter South or North
- All four cutting technologies (laser, plasma, oxyfuel, waterjet)
- Innovative automation systems
- The latest solutions for bending and deburring
- Industry 4.0 demo factory
- Easy to reach: in the south and north of Germany
