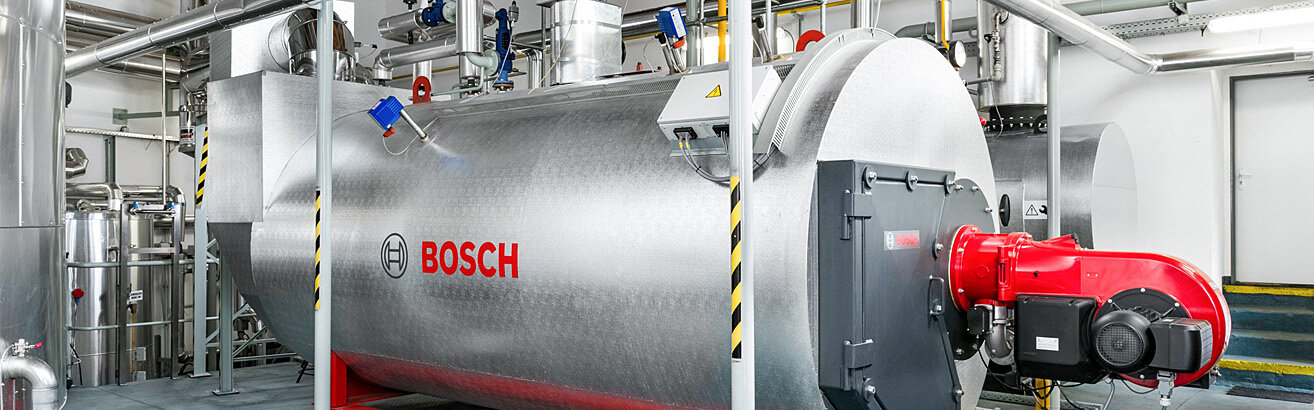
Bosch Industriekessel manufactures system solutions for thermal and process heat with MicroStep cutting technology
Bosch goes for MicroStep: Good experience and precision are the key factors
Since 2015, Bosch Industriekessel has relied on two cutting systems for the processing of sheet metal and dished heads, achieving many advantages.
Published 10.01.2022 | Erich Wörishofer
Company profile:
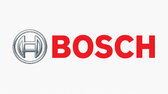
Bosch Industriekessel GmbH
Nürnberger Str. 73
91710 Gunzenhausen
Deutschland
For over 150 years, Bosch Industriekessel has been developing and manufacturing customized system solutions for thermal and process heat. Forward-looking innovations such as the digital efficiency assistant and consistent optimization of products form the foundation for outstanding efficiency and sustainability. To date, more than 120,000 steam, hot water and heating boiler systems have gone into operation in over 140 countries. Industrial and commercial companies in particular, but also energy suppliers and operators of large buildings and public facilities, count on Bosch boilers from Germany and Austria.
Bosch Industriekessel GmbH has been relying on MicroStep technology since 2015. Two different system types for processing sheet metal and dished heads are reliably in use.
Machine profile:
MG series- Working area 24,000 x 5,000 mm
- Cutting of domes Ø 300 – 4,000 mm up to a height of 1,000 mm
1. Gantry
- Plasma rotator for weld preparation up to 50° with auto-calibration feature (ACTG®)
- Console for manual oxyfuel torch
2. Gantry
- Plasma rotator for weld preparation up to 50° with auto-calibration feature (ACTG®)
- 2D oxyfuel
- Console for manual oxyfuel torch
- 3D scanner + mScan technology for compensation of the production-related deviation of dome shape by adjusting the generated cutting paths according to the true scanned shape of dome
CombiCut series
- Working area 24,000 x 3,500 mm
- Plasma rotator for weld preparation up to 50° with auto-calibration feature (ACTG®)
- Automatic plate edge detection
If things need to get hot in the home or in the company, for example, Bosch Industriekessel has been a sought-after partner for decades. When the German production site in Gunzenhausen, was looking for modern cutting solutions for existing CNC systems, it opted for two 3D plasma cutting machines from MicroStep. In the end, good experience already gained at another location and meeting required tight tolerances when cutting holes and bevels were convincing factors.
For more than 150 years, Bosch Industriekessel GmbH, a Bosch Thermotechnik GmbH company, has been developing and manufacturing project-specific thermal and process heating systems. With "technology for life", Bosch Industriekessel designs sustainable energy systems. The steam and hot water boilers improve energy efficiency in production, buildings, and district heating networks – with the help of sustainable energy use and seamless Industry 4.0 integration. CO2-neutral thermal and process heat solutions with hydrogen and electrification support the path to climate neutrality. Bosch Industriekessel offers its customers worldwide a consistent product portfolio as well as planning support, project management, and after-sales services such as maintenance and 24/7 support – all from a single provider.
When it comes to cutting, the traditional company based in Gunzenhausen – south of Nuremberg – has relied on MicroStep technology since 2015. The company has since been using 3D plasma cutting systems in two plants at the site, mostly in two-shift operation, sometimes also in three-shift operation. These are an MG series with double gantry, which is used for both sheet metal and dished end processing, and a CombiCut series, which is used purely for sheet metal processing. The company uses it to cut steels in thicknesses ranging from 8 to 45 mm, mostly batch size 1 to small series. The investment ended an intensive period of searching in 2015.
Many tests and development work convince
"Before that, we had a plasma cutting system in Plant 1 and an oxyfuel cutting system in Plant 2. The main focus was on the cutting speed, and the oxyfuel system was also too small and not what we wanted in terms of precision and heat input. We intended to add dished end machining as an additional process," says Christian Loschmidt, head of technical planning, looking back. In order to create redundancies and simplify the work in the work preparation department and at the plant, the decision was made to exchange both systems and to purchase two new systems from only one manufacturer. Loschmidt had already been involved two years earlier when Bosch Heating Systems LLC, responsible for the Russian market, also needed a 3D plasma cutting system and chose MicroStep's MG series. "By then, we had already gained experience and broad knowledge of the market." Among other things, research was conducted on the internet and at exhibitions. Now a new set of specifications was created with a focus on meeting the tightest tolerances for hole and bevel cutting. "We cut a lot of special parts, have many ignitions and also special geometries," explains Loschmidt. Many cutting tests were performed, and MicroStep did additional development work to meet the required accuracies. The technological component coupled with the good experience gained in Russia ultimately made the decision.
Automated dished heads processing: "A leap in quality, a different world"
Since then, both machines have been in continuous operation. "This was a profitable investment. It's clear that this is not a cordless screwdriver that you get ready out of the box, but a highly complex technology. We have always found a good solution and worked together constructively. The service has always worked great, we've always had someone on site quickly who has helped us competently," says Loschmidt. An additional advantage came with the decision to rely on a combined sheet metal and dished heads cutting system. Dished heads were previously supplied semi-finished and then finished by hand. An enormously time-consuming process with accuracies that were difficult to achieve. Problems that are now in the past. Holes and bevels are now applied automatically. "It's a super thing, a leap in quality, a different world."
"This was a profitable investment. We have always found a good solution and worked together constructively. The service has always worked great, we've always had someone on site quickly who has helped us competently."
Christian Loschmidt
Head of Technical Planning | Bosch Industriekessel GmbH
OVERVIEW OF THE HIGHLIGHTS OF THE PLASMA AUTOMATIC CUTTING SYSTEM MG:
Plasma oxyfuel cutting system with two gantries for 3D processing of sheet metal and dished heads
For cutting, Bosch Industriekessel relies, among other things, on the MG series including two gantries with different technology options for processing sheet metal and dished heads. The 3D plasma cutting system has a working area for flat material of 24,000 x 5,000 mm and a working area for dished heads of 300 to 4,000 mm diameter. MicroStep's endless rotating plasma rotator for weld edge preparation up to 50° has been integrated on both gantries. The automatic, patented ACTG® calibration unit enables permanently precise results. A Kjellberg HiFocus 440i neo was integrated as the plasma source. A 3D laser scanner integrated in one of the two gantries detects the dished heads to be cut in advance and thus contributes to precise, process-reliable results. An oxyfuel torch for processing higher material thicknesses is also available, among other features.
OVERVIEW OF THE HIGHLIGHTS OF THE PLASMA CUTTING SYSTEM COMBICUT:
Plasma cutting machine with a working surface of 24,000 x 3,500 mm
Bosch Industriekessel invested, among other things, in the CombiCut series, an extremely resistant and robust flame cutting system for enormous process safety and reliability even in three-shift operation. The flame cutting table is designed for a working area of 24,000 x 3,500 mm – the existing cutting table of the previous system was used here. The MicroStep plasma rotator for weld edge preparation up to 50° including the ACTG® calibration unit and a Kjellberg HiFocus 440i neo as plasma power source are integrated.
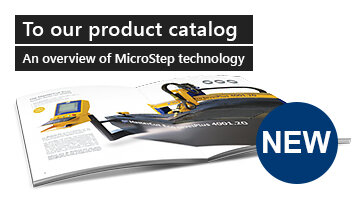
EXPERIENCE OUR SYSTEMS LIVE
in the CompetenceCenter South or North
- All four cutting technologies (laser, plasma, oxyfuel, waterjet)
- Innovative automation systems
- The latest solutions for bending and deburring
- Industry 4.0 demo factory
- Easy to reach: in the south and north of Germany
