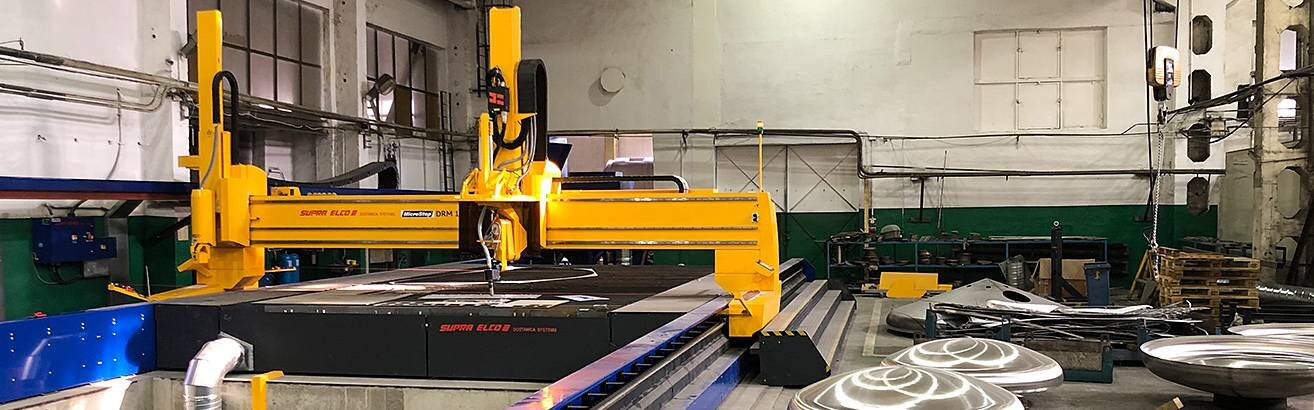
A step towards the digital workshop: DRM at Schwarte Group Sp. z o.o.
A leap to high precision and quality
Schwarte Processing, a producer of stainless steel tanks and apparatus for sensitive liquids, has invested into a MicroStep CNC plate and dome cutting machine intended predominantly for the processing of tank ends
Published 10.12.2020 | Erich Wörishofer
Company profile:

Al. Obrońców Tobruku 3A
10-092 Olsztyn
Poland
Schwarte Group covers the entire spectrum of transport, analysis, storage and processing of liquid food and substances throughout Europe. The group of companies also includes Schwarte Processing, which, at several locations in Germany and Poland, takes care of tank and apparatus engineering for dairies, the beverage or food industry, and the pharmaceutical and chemical industries, among others.
The sheet metal/tank end cutting center of the DRM series enables 3D processing of flat sheets as well as various tank end shapes at Schwarte's Polish site in Olsztyn.
SCHWARTE GROUP with its two brands SCHWARTE PROCESSING and SCHWARTE JANSKY specializes in the production of stainless steel containers for food, pharmaceutical and chemical industries as well as milk collection technology and vehicle construction. The company has recently achieved a significant leap in precision and quality by acquiring a state-of-the-art CNC cutting solution for 3D processing of sheets and tank ends – the multi-functional DRM cutting center from MicroStep which has been put into operation in autumn 2019 in Schwarte's production site in Poland. “The machine is efficient and accurate, it is a quality product," says Head of Maintenance Department Michał Liberacki.
Anyone who works at a dairy, a beverage or a food factory, or in pharmaceutical or chemical industries – whether small, medium-sized or large-scale – knows the name Schwarte Group. The company has been operating for more than 75 years and is in demand throughout Europe. With its two companies, Schwarte Processing (container construction) and Schwarte Jansky (milk collection technology and vehicle construction) it covers a wide range of products for transport, storage and processing of foods and sensitive liquids. The product portfolio ranges from milk collection vehicles and beer storage systems to measuring technology and various technologies for the collection, transport and storage of liquids. All this with an extensive service and maintenance coverage. Around 420 employees work at Schwarte's locations in Germany, Poland and Austria.
Tight tolerances and process reliability required
Schwarte Processing which is active in the area of container construction puts high demand on precision and reliability while following tight process tolerances in its production. One of Schwarte's main sites is located in the north-east of Poland, in the city of Olsztyn. Since late 2019 the company makes use of a special sheet and dome cutting machine here, with a 120° 3D plasma rotator and MicroStep's innovative mScan dome mapping technology that ensures high precision of tank end processing. “The investment in new machinery improves our production process and overall workflow. The flexible plasma bevel head expands greatly our possibilities. All bevel cutting of sheets is now automated, thus achieving great accuracy, avoiding errors and manual rework," says Michał Liberacki. At the time of purchase, the company was already thinking a few steps ahead, because the DRM series is capable of achieving the prerequisite precision of the digital workshop standard for tank end processing. "In the future, we will be able to use welding robots for the processing of tank ends."
Since installation the multi-functional CNC machine has been working daily in a two-shift operation. It is used to produce stainless steel containers. "Currently, the machine is used for cutting of parts for the construction of containers with a wall thickness of 2 up to 30 mm and for cutting of holes into tank ends with weld preparations with a wall thickness between 2 and 20 mm,” explains Liberacki.
MicroStep's experience convinces
When considering the right solution, the company was gradually convinced by MicroStep's experience in the field of tank end processing and bevel cutting. "MicroStep was selected because the company has a large database of similar applications developed and delivered to the German market," says Liberacki.
He is very satisfied with the investment, which paid off from day one: "The implementation of the system went smoothly. The machine meets our expectations and operates efficiently, with high accuracy and quality."
The implementation of the system went smoothly. The machine meets our expectations and operates efficiently, with high accuracy and quality. This will allow us to use welding robots for further processing of tank ends in the future.
Michał Liberacki,
Head of Maintenance Department | Schwarte Processing/ Schwarte Group Sp. z o.o.
Machine profile:
DRM series- Working area for sheets 14,000 x 6,000 mm
- Cutting and trimming of domes Ø 500 – 4,500 mm
- 3D plasma rotator "pantograph" with tilting up to 120° for weld preparation on domes and plates + auto-calibration feature (ACTG®)
- 3D scanner + mScan technology for compensation of the production-related deviation of the dome shape by adjusting the generated cutting paths according to the true scanned shape of the dome
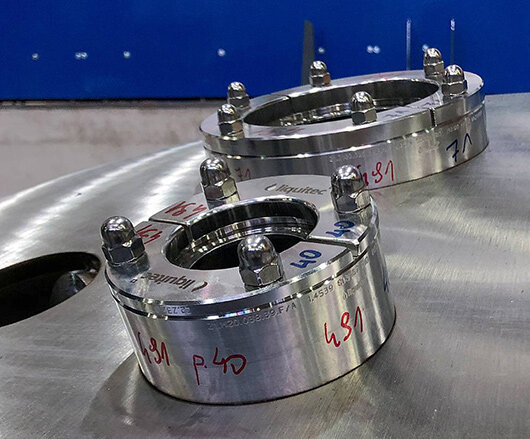
OVERVIEW OF THE HIGHLIGHTS OF THE CNC PLASMA CUTTING MACHINE DRM
3D sheet processing – work area 9,500 x 4,500 mm
The sheet and dome cutting center of the DRM series at Schwarte enables flexible 3D processing of flat sheets on a work area of 9,500 x 4,500 mm. The machine features a state-of-the-art plasma source XPR300 from Hypertherm with OptiMix gas console.
Complex processing of tank ends with diameters from 500 mm to 4,500 mm
Thanks to the 120° 3D bevel head, which can be tilted on one side up to 120°, the DRM series allows flexible bevels and holes to be cut in the tank ends of various shapes. A special table for dome cutting allows processing of tank ends with diameters between 500 mm and 4,500 mm. The machine's bevel tool station has an extended Z-axis stroke for processing of a wide range of dome heights. For cutting of different types of domes, the fume extraction is ensured from above the cutting head as well as through slots in the dome cutting table.
120° 3D bevel head for 3D processing of sheets and domes
The integrated 3D bevel head allows to achieve bevel angles of up to 90° (and on other side up to 120°). The bevel equipment with endless rotation enables precise automated weld preparation not only on flat sheets, but also on tank ends – including trimming of domes and processing of the whole dome surface.
MicroStep's mScan technology for precise scanning and processing of tank ends
MicroStep's mScan technology ensures the highest precision and best cutting results: In combination with the 120° 3D bevel head and a laser scanner, Schwarte generates high-quality results and saves a great deal of rework. The system determines the 3D geometry of each dome, compares the real contour to the ideal contour, automatically compensates for production-related deviations and sets the cutting paths exactly.
Even easier to achieve accurate results with ABC in mCAM
An additional function has been integrated into MicroStep's 3D CAM software mCAM: The process-limiting angle deviation of the plasma arc is compensated for by MicroStep's ABC (Adaptive Bevel Compensation) function. This function is implemented in the bevel head controls as a standard. At Schwarte, the ABC function has been additionally connected with the CAM software mCAM – it allows bevel corrections to be applied in mCAM after the scanning process of a particular dome. The system then generates a program adapted to the real contour. A highly precise result is achieved with a few simple operations!
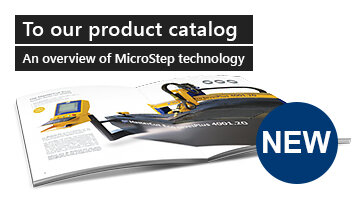
EXPERIENCE OUR SYSTEMS LIVE
in the CompetenceCenter South or North
- All four cutting technologies (laser, plasma, oxyfuel, waterjet)
- Innovative automation systems
- The latest solutions for bending and deburring
- Industry 4.0 demo factory
- Easy to reach: in the south and north of Germany
