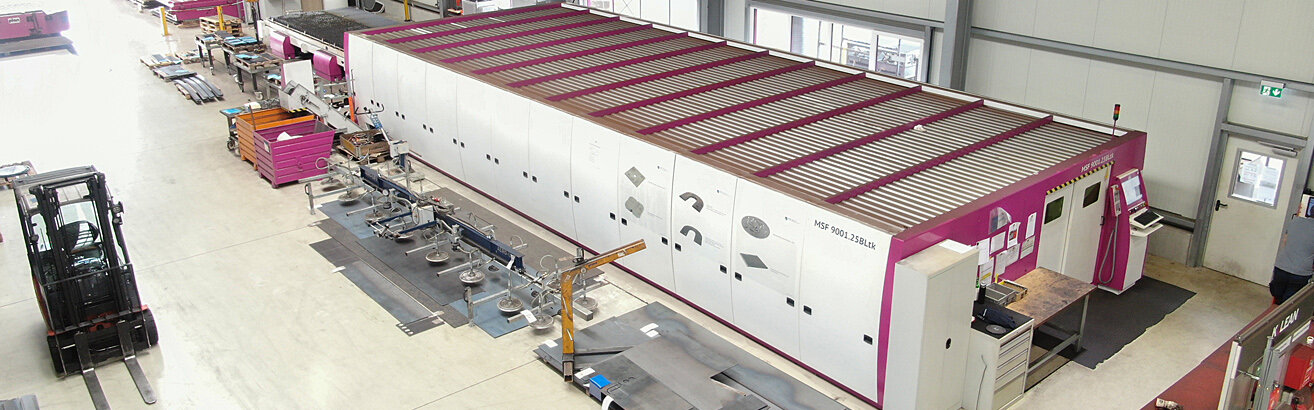
KTS Technologiepark Stahl is a real all-rounder in metal processing
"This is a service level on the highest scale"
With the fiber laser of the MSF series, the contract manufacturer KTS Technologiepark Stahl has found its dream laser and expanded its large machine park
Published 01.02.2022 | Erich Wörishofer
Company profile:
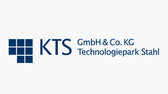
KTS GmbH & Co. KG
Technologiepark Stahl
Lußhardtstraße 4
76689 Karlsdorf-Neuthard
Germany
Founded in 2010, the family-owned company KTS GmbH & Co. KG Technologiepark Stahl offers the entire portfolio of metalworking and is a supplier as well as know-how partner in one. The service center produces high-quality steel products for industries ranging from construction machinery, heavy crane construction, agricultural machinery technology, heavy vehicle construction, classic mechanical engineering and energy technology to roller coaster construction.
The KTS GmbH & Co. KG Technologiepark Stahl has all the machines related to steel processing under one roof.
Machine profile:
MSF series- Working area 9,000 x 2,500 mm
- Laser rotator for weld preparation up to 45° with auto-calibration feature (ACTG®) + 6 kW fiber laser source
- Drilling upt to 20 mm and tapping up to M16
- Automatic shuttle table
When it comes to the processing of steel through to the creation of complete welded assemblies, the family-owned company KTS Technologiepark Stahl has all the necessary machinery under one roof. The German company, which is located close to the A5 near Karlsruhe, prides itself on being a versatile contact for customers when it comes to contract orders. Because delivery times for laser parts were too long and adherence to deadlines was too erratic, the steel manufacturer invested in a XXXL fiber laser from MicroStep's MSF series with the option for bevel cutting, drilling and tapping. This enables the very large customer demand to be served, especially for components in small batch sizes.
When it comes to processing steel, the company KTS Technologiepark Stahl is a true all-rounder. The family-managed company was founded in 2010 with the aim of combining all technologies for processing steel under one roof. The range of services is diverse: from flame-cut parts, mechanical processing and individual coating to the completion of complete welded assemblies. And thanks to a wide range of know-how, managing director Mario Koch's contracting company sees itself not only as a supplier, but also as a partner and provides customers with advice – for example on issues of process and cost optimization. "A fast turnaround time, quality and fair prices across the entire portfolio are what set us apart," says the managing director, describing his company's strengths. The company was thus able to grow from five to 55 employees within eleven years. In order to take into account the changing conditions and to act even more competitively, Mario Koch decided in 2018 to build a new production hall with around 2000 m² and to invest in a fiber laser MSF from MicroStep with an extraordinary working area, thus introducing laser cutting technology in the company.
Growth with existing machinery limited
The need for laser parts already existed earlier – nevertheless, the company did not initially want to create its own production capacities here. If a customer needed a laser part, it was purchased. However, the difficulties increased: Long waiting times for a quotation, unreliable delivery or the lack of necessary larger sheet metal panels characterized the business relationships with laser service providers. At the same time, the company's own plasma system was operating at almost full capacity. An in-house analysis came to the conclusion that 30 percent of the cutting time of the plasma system was utilized by orders with thin sheets below 12 mm – so the idea to invest in an own laser system was finally born.
Consistent technological development and commitment to Industry 4.0 convince
With the acquisition of the new laser system, emphasis was placed on a wide range of processing options. KTS regularly processes large-format sheet metal panels and also wanted to be able to apply automated weld seam preparations with the laser system. Against this background, a detailed analysis was carried out to find out who on the market could meet these specific requirements. A visit at the Swiss steel and facade manufacturer Rytz AG with a MicroStep reference machine finally convinced Mario Koch of the quality of a MicroStep system, and so the choice fell on the MSF series from MicroStep in a XXXL version. "The bevels had fit tip-top and that without any major adjustments. The precision of the machine is incredible," says the managing director about the laser that was demonstrated at that time.
The metal manufacturer was particularly impressed by the fully automatic ACTG® calibration function, which is part of the standard equipment of MicroStep's 3D cutting solutions and ensures the best possible precision for bevel cutting in the long term. The option to integrate an automatic nozzle changer was also an important purchase criterion. MicroStep's pioneering position on the subject of digitization and the company's commitment to the Industry Business Network 4.0 and the IndustryFusion Foundation also impressed: "MicroStep thinks about what a customer needs and starts developing it. Others wait until the customer whines and complains. It's nice when someone thinks the other way around," says Mario Koch, describing MicroStep's commitment to research and development.
"We are very satisfied with the laser cutting technology we have invested in and are very happy having MicroStep as a partner," says Mario Koch about his decision for MicroStep. The broad processing spectrum includes combined 2D and 3D cutting, drilling, tapping, countersinking and marking. Bevels up to 45° can be realized, and the drilling spindle enables drilling up to 20 mm in diameter and tapping up to M16. MicroStep also implemented the desired color of the machine in traffic purple.
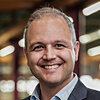
"We are very pleased with the laser cutting technology we have invested in and are very happy having MicroStep as a partner. I would make the same decision for this MicroStep system all over again."
Mario Koch
Managing Director | KTS GmbH & Co. KG Technologiepark Stahl
"The quality of the drilling is excellent!"
The necessary documentation for the in-house production control can also be provided easily and effortlessly with the machine. This is because CNC machines from MicroStep are generally capable of digitally providing the parameters used for cutting. Compared to manual documentation with pen and paper, this saves a lot of work in the production process. At the same time, perfect and complete traceability of the manufactured parts, e.g. in crane construction, is an important quality feature of KTS.
The bevel unit is very heavily utilized at the metalworking company and is pushed to its limits. "About 20-25 percent of our components are beveled parts and all possible combinations (V, A, X, Y, K bevel) are handled by the machine just fine. With the new laser, we have also been able to massively reduce the manufacturing time," says Mario Koch, describing the advantages of the new system. Today, for example, a component with a six-meter chamfer is cut on the laser with very little effort. "The quality of the drilling is excellent," says Mario Koch about the drilling unit. Drilling is used weekly for five to ten percent of orders and saves a lot of rework, as this manufacturing process previously had to be done labour-intensively by hand. In the view of the managing director, the entire project process and also the implementation of the new laser system worked great. "No matter at what time, MicroStep has always taken care of emerging challenges with mega power! It's really top level service and when we call, we know that the problem is always taken care of very promptly. I would make the decision for this MicroStep system all over again!", says Mario Koch.
OVERVIEW OF THE HIGHLIGHTS OF THE FIBER LASER CUTTING SYSTEM MSF 9001.25 BLtk:
MSF series laser cutting machine with a working area of 9,000 x 2,500 mm
KTS GmbH & Co. KG Technologiepark Stahl invested in the MSF series from MicroStep, a fiber laser cutting system for process-safe multifunctionality with a high level of automation. The company relies on a XXXL version for sheet metal processing with a working area of 9,000 x 2,500 mm. The automated shuttle table ensures optimum loading and unloading of the system. This allows simultaneous processing inside the cutting booth as well as loading and unloading outside. A conveyor belt for scrap disposal transports small parts and cutting waste from the cutting area into a container for manual disposal.
Laser rotator for weld seam preparation up to 45° and IPG fiber laser source of the YLS series with 6.0 kW power
A laser rotator for bevel cutting, for example for weld seam preparation up to 45°, has been integrated in the fiber laser cutting system. The excellent beam quality ensures high cutting speeds and small kerfs as well as low heat input, which prevents distortion of the components. The robust rotator system can be used to apply simple V and X seams as well as complex Y or K seams with micro joints to the flat material. MicroStep's patented ACTG® automatic calibration unit enables accurate and process-reliable results for the entire machine life. To be able to realize high-quality cuts in thin and medium material thicknesses at high cutting speeds, KTS relies on the IPG fiber laser source of the YLS series with 6.0 kW power.
Fully automatic drilling spindle up to 20 mm diameter and tapping up to M16
The fully automatic drilling spindle can be used to drill precise holes up to 20 mm, countersinks as well as taps up to M16. The drilling spindle has a fully automatic tool holder and is equipped with a tool magazine for up to six tools. In addition, a fully automatic pneumatic stabilization system is integrated in the cutting system, which fixes the support as well as the gantry bridge with a clamping system on the linear guides during operation of the drilling spindle and ensures a high stability and precision of the system.
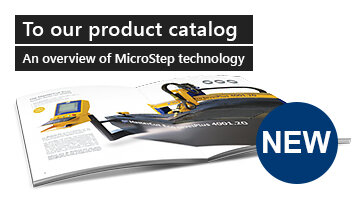
EXPERIENCE OUR SYSTEMS LIVE
in the CompetenceCenter South or North
- All four cutting technologies (laser, plasma, oxyfuel, waterjet)
- Innovative automation systems
- The latest solutions for bending and deburring
- Industry 4.0 demo factory
- Easy to reach: in the south and north of Germany
