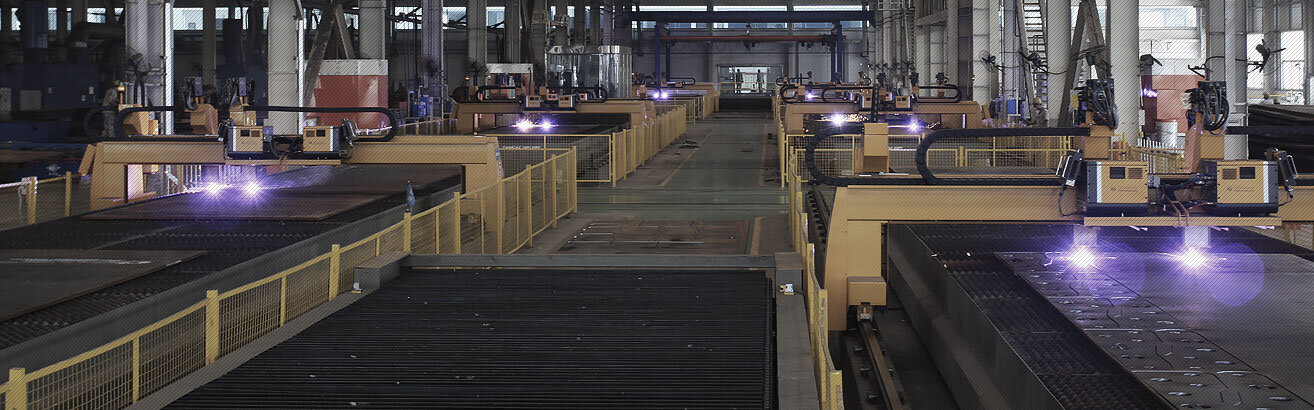
Automated manufacturing solution for ZMJ with plasma cutting systems and process crane
Automation: Pilot project with CNC plasma cutter leads to great efficiency gains
MicroStep and partner Terex increase the production output by 40 percent with an automated production line with six CNC plasma cutting machines and one Kjellberg HiFocus 360i each
Published 24.10.2016 | Erich Wörishofer
Company profile:
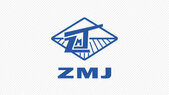
Zhengzhou
Henan Province
China
The 1958 established state-owned company ZMJ is China‘s leading manufacturer of coal mining and excavating
equipment with a domestic market share of over 45%. As one of the few manufacturers in China the company is able
to produce 3 of the 4 components of a complete coal mining system: hydraulic roof supports, armored-face conveyors
and roadheaders. ZMJ‘s client base includes the biggest names among Chinese coal mining companies as well as
foreign companies.
Machine profile:
- Fully automatic sheet cutting line consisting of 8 cutting
gantries, an automatic crane, an input wagon an 2 output
conveyors
- Working area 28,000 x 3,000 mm
- 2x 2D plasma
- Inkjet marking
- Automatic plate edge detection
2x CombiCut series
- Working area 28,000 x 3,000 mm
Each machine has two gantries with:
- 2x 2D plasma
- Inkjet marking
- Automatic plate edge detection
CombiCut series
- Working area 28,000 x 7,000 mm
- 2x 2D plasma
MG series
- Working area for sheets 2x 12,600 x 2,800 mm
- Plasma rotator for weld preparation up to 50° with auto-
calibration feature (ACTG®) - 2D plasma
- Scanner for Additional Beveling Process (ABP)
MicroStep and Terex MHPS GmbH (manufacturer of Demag industrial cranes) in a pioneering tandem: in close cooperation, the companies developed a material handling system for automated sheet metal processing for China’s leading coal mining equipment manufacturer Zhengzhou Coal Mining Machinery Group. In total, eight MicroStep plasma cutting machines are being fed with plates by an automated Demag process crane from Terex. As a result, immense efficiency gains are achieved in the production process.
The Chinese mining industry is booming and so is the mining equipment sector. The Zhengzhou Coal Mining Machinery Group is one of the market leaders both for stationary equipment for roof and long-wall supports as well as for mobile machinery that operates in mines. At its plant in Zhengzhou, the capital of Henan province, the company is running a production line for automated plate processing consisting of several double-gantry MicroStep cutting machines and a Demag process crane, which is responsible for storage and retrieval of the plates as well as the feeding of the cutting systems in a 24/7 operation. At the heart of the system is the production management software MPM from MicroStep, which controls the entire production process.
The investment has paid off for ZMJ: Every day, the cutting line is able to process up to 155 metal plates in three-shift operation, with one production cycle now taking only one to two hours, compared with the four to eight hours previously. The intralogistics system implemented for this solution also ensures that the machinery is utilized to a consistently high level. The impressive result of this pilot installation: production in the entire plant has been increased by 40% with a monthly machine output of 12,000 t.
General trend towards automation
This project reflects the current trends in the field of industrial mass production. Increasingly, solutions with central production management and a high degree of automation are in demand. The goals are: the highest possible efficiency, optimization of the production process and, of course, reduction of risks and costs. The whole production should be fast, smooth and transparent. In addition to material flow and material processing, the system should also be interconnected with the central warehouse, order management system and the customer‘s ERP system.
The automatic line installed at ZMJ consists of eight CombiCut gantries with cutting areas of 28 x 3 m, each equipped with two high-definition plasma sources and an inkjet marker. In addition, there is an automated overhead crane (9 t x 16.5 m), an input wagon with a load capacity of 15 t and two output conveyors for collecting the cut parts and removal of waste material. The entire line is fully automated via MicroStep‘s Machine Production Management (MPM) software, with integrated software modules from Demag for crane management and material handling. The crane is moving on a 120 m long track in the height of almost 13 m. In the beginning of the process, the crane transports one of the plates (up to 12 m long and 40 mm thick) by means of strong magnet spreaders onto a free machine or into one of two buffer zones assigned to each of the eight CombiCut machines. After the cutting process, the crane moves the cut plate onto an output conveyor belt. Here, the plates leave the automated area and proceed
to be sorted out manually.
An area measuring 120 x 18 m was fenced off within the production facility for the storage and processing of plates. Here, the customer not only benefits from a better organized flow of material, but also from improved safety at the workplace: a dedicated access concept prevents any personnel from entering the individual processing areas when they are automatically approached by the crane. When routine maintenance work is performed on one of the cutting systems, the automatic crane by-passes the danger zone in order to protect the personnel.
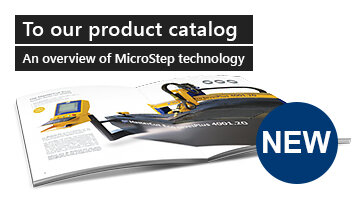
EXPERIENCE OUR SYSTEMS LIVE
in the CompetenceCenter South or North
- All four cutting technologies (laser, plasma, oxyfuel, waterjet)
- Innovative automation systems
- The latest solutions for bending and deburring
- Industry 4.0 demo factory
- Easy to reach: in the south and north of Germany
