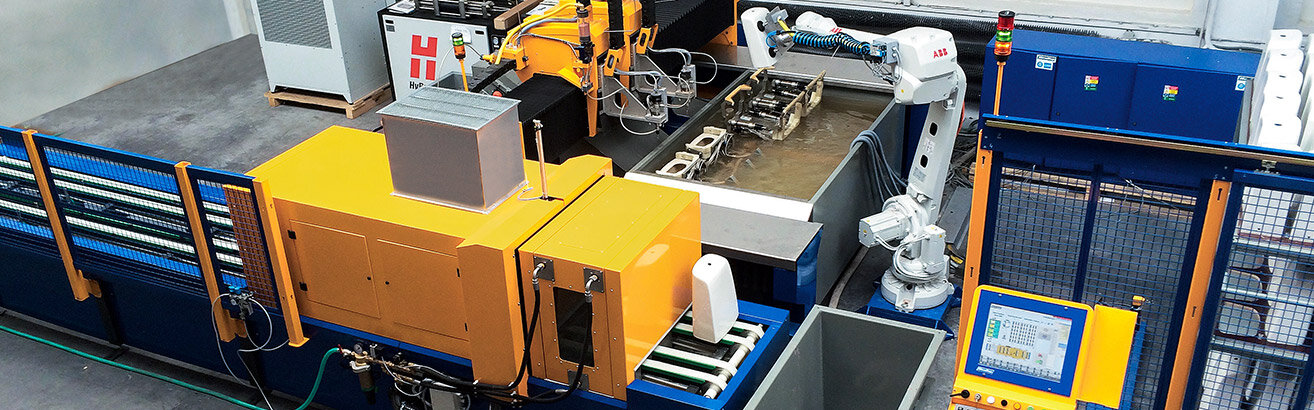
300,000 ceramic cisterns are produced annually with the automatic production cell
300,000 ceramic cisterns annually with automatic production cell
For the premium manufacturer Villeroy & Boch, MicroStep developed an automation solution with a waterjet cutting system and a robot
Published 13.06.2018 | Erich Wörishofer
Company profile:

SC Mondial AG335500 LugojRomania
Villeroy & Boch AG, producer of high-quality tableware or timelessly elegant bathroom equipment, is one of the most famous premium brands in the world. Several sub-brands exist under the name of the traditional company. One of them is the company Mondial, based in western Romania. For the processing of sanitary products, this company relies on a special solution from MicroStep for the automated mass production of cisterns.
https://www.villeroy-boch.info/en.html
For the processing of ceramic tanks, MicroStep developed a production line for the Mondial brand, which belongs to Villeroy & Boch AG. Using a high-pressure waterjet cutting system and a robot manipulator, the ceramic products are cut, cleaned and dried in a single system – all fully automatically.
Villeroy & Boch AG, producer of high-quality tableware or timelessly elegant bathroom equipment, is one of the most famous premium brands in the world. Several sub-brands exist under the name of the traditional company. One of them is the company Mondial, based in western Romania. For the processing of sanitary products, this company relies on a special solution from MicroStep for the automated mass production of cisterns. This includes a waterjet cutting system of the AquaCut series with a robot manipulation. Several 100,000 tanks are processed with it every year.
From the pottery to a full-scale ceramics manufacturer. From plate to lifestyle producer. From Mettlach in the Saarland to the whole world. Villeroy & Boch AG, whose roots go back to 1748, has an impressive history behind it and is one of the most famous brands in the world today. Tableware, bathroom equipment, kitchen products or tiles belong to the widely ramified portfolio of the ceramic producer, selling its products in 125 countries and achieving an annual turnover of more than 800 million euros with about 7500 employees. Even after more than a quarter of a century of history, the company is still largely owned by the families of the two company founders François Boch and Nicolas Villeroy. "Villeroy & Boch literally brings over 265 years of tradition, innovation and outstanding design quality on the table," emphasizes board member Nicolas Luc Villeroy, representative of the 7th generation.
Special solution for ceramic manufacturer in operation since 2015
In order to offer high-quality products and a comprehensive portfolio to customers around the world, the premium brand relies on additional brands and production facilities in 14 countries. Under the name Mondial, the company produces sanitary ceramics for the Romanian market. Since 1996, the Lugoj site in western Romania has been part of the listed corporation.
Here, the company has relied on a unique MicroStep solution for cut-outs and contours of sanitary products since 2015. MicroStep has developed a fully automated production cell for this purpose, consisting of a laser manipulator, a waterjet cutting machine and a washing and drying system for mass production in sanitary technology.
300,000 ceramic tanks are processed annually on the production line
The system carries out a large number of processing steps. A robot with a vacuum pick-up tool removes the ceramic tanks individually from a rack cart and fills four existing cutting zones of the CNC waterjet cutting system with its two waterjet cutting heads. In connection with the CNC machine, two ceramic tanks can be processed in parallel and contours can be cut out. After processing and unloading the remaining parts, the products are loaded by a robot onto a conveyor belt for cleaning and drying and then unloaded manually. The automation of the production process bears fruit. Since its implementation in 2015, around 300,000 ceramic tanks have been processed annually on the production line. "The design and development of this unique waterjet robot line was a challenge that we enjoyed solving. We have already been able to successfully implement several cutting machine-robot combinations in recent history. This has enabled our customers to achieve a great leap in efficiency in each case. This was also our mission with this automation solution for Mondial", says Alexander Varga, Ph.D., co-founder of MicroStep and responsible for Research & Development.
"We have already been able to successfully implement a number of cutting system-robot combinations in recent history. This has enabled our customers to achieve a major leap in efficiency in each case. This was also our mission with this automation solution for Mondial".
Alexander Varga, Ph.D.
Head of R&D| MicroStepp |
Machine profile:
MicroStep AquaCut series
- Fully automatic working cell
- Working area: 4 cutting zones with rotary hydraulic holders
for positioning of products - 2D waterjet cutting simultaneously with two tool stations
- Robotic manipulator
- Automatic waste removal via conveyor in water tank
- Rinsing chamber for washing of products
- Drying chamber for wahing of products by air blow
- 50 HP high pressure pump
OVERVIEW OF THE HIGHLIGHTS OF THE PRODUCTION CELL
AquaCut waterjet cutting system with two cutting heads and conveyor system for the disposal of small parts
The basis of the production cell at Mondial is a robot and a waterjet cutting system. The company relies on the AquaCut series from MicroStep. The exclusive solution for high-precision 3D cutting was developed to process almost any material with pure water or abrasive additives without thermal impact. Mondial uses a system configuration with two 2D waterjet cutting heads for simultaneous processing of two workpieces; Hypertherm's HyPrecision high-pressure pump is used as the waterjet pump – the cutting heads are equipped with a dosing device and cut with an abrasive medium. The working area of the cutting basin is 1,000 x 2,000 mm and includes four cutting zones. These have rotary hydraulic holders for positioning during cutting. Thanks to the two cutting heads, the ceramic cisterns can be processed in two zones and the finished workpieces can be removed in the other two zones.
Manipulation with ABB robots
The second elementary component is a robot coupled with the cutting system from ABB, the Zurich-based energy and automation technology group, which has placed more than 300,000 industrial robots on the market worldwide. The robot at Villeroy & Boch is used to manipulate the ceramic workpieces. The robot arm has an integrated adaptive pneumatic gripper that guides the tanks from the removal station to the cutting zone. After processing, it empties the residual parts that are produced during cutting from the tank into a container and then manipulates them on a conveyor belt for final processing.
Conveying system including rinsing and drying chamber
Before the machined ceramic tanks are removed and stored manually, they pass through two final processes within the production cell. On a conveyor system placed in the immediate vicinity of the cutting machine, two tanks are transported in parallel first through an automatic rinsing chamber for cleaning and then through a further chamber for drying by means of air pressure.
Control unit outside the safety area
The networked processes are controlled via a console outside the production zone, which is enclosed by a safety fence, on the basis of a stand-alone solution. Additional security and monitoring measures ensure a smooth production cycle.
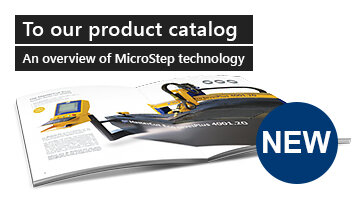
EXPERIENCE OUR SYSTEMS LIVE
in the CompetenceCenter South or North
- All four cutting technologies (laser, plasma, oxyfuel, waterjet)
- Innovative automation systems
- The latest solutions for bending and deburring
- Industry 4.0 demo factory
- Easy to reach: in the south and north of Germany
