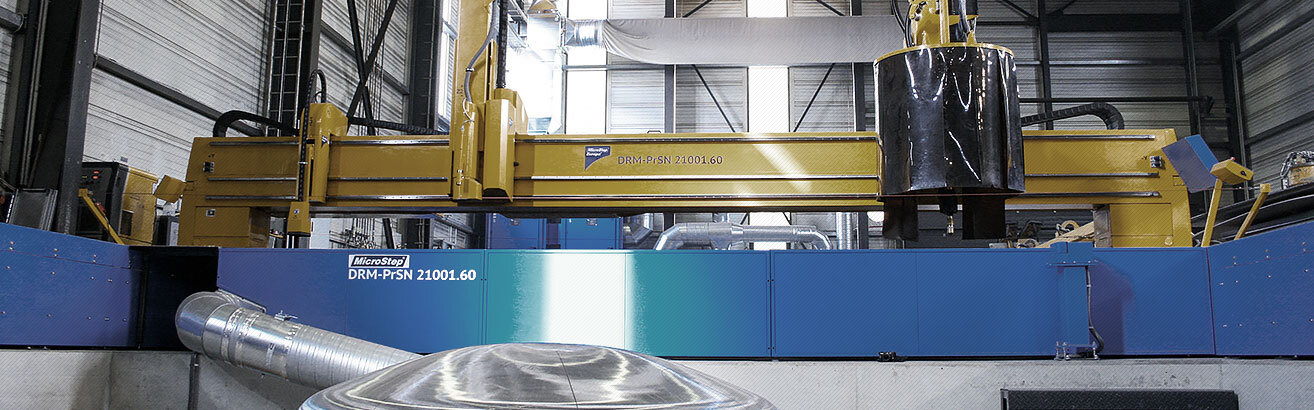
Cutting center at Slawinski: the DRM for processing domes and sheets
"The system replaces two machines, for us it's the optimum"
Slawinski's bottoms and special presses are in high demand throughout Europe - for the company's cutting, MicroStep implemented a multifunctional cutting center for extraordinary requirements
Published 01.06.2016 | Erich Wörishofer
Company profile:
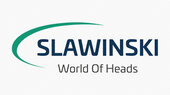
Being a specialist for domes and special pressed parts, Slawinski & Co. GmbH has been supplying tailored solutions
for small businesses as well as global corporations for more than 100 years. The company relies on its long-standing
experience and innovative production machinery. Each supplied dished end is a precisely manufactured original that finds
its application in nuclear power plant construction or in transport of chemical liquids.
Machine profile:
DRM series- Working area for sheets 14,000 x 6,000 mm
- Cutting and trimming of domes Ø 500 – 5,500 mm with a max.
height of 1,500 mm - 3D plasma rotator "pantograph" with tilting up to 120° for weld
preparation on domes and plates + auto-calibration
feature (ACTG®) - 3D scanner + mScan technology for compensation of the
production-related deviation of the dome shape by adjusting
the generated cutting paths according to the true scanned
shape of the dome - Micro-percussion marking
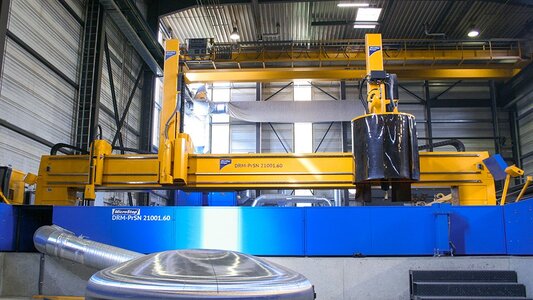
In cooperation with the company Slawinski, MicroStep developed an innovative system for the flexible and precise processing of sheets and container bottoms on a special scale. The DRM series has been extended by customized technologies for the container bottom specialist.
As a specialist for container bottoms and specialized pressure-vessel parts, Slawinski & Co. GmbH has been providing tailor-made solutions for a wide variety of customers for more than 100 years. The products of the family-owned company are used by small enterprises and global corporations alike. Slawinski relies on state-of-the-art machine solutions. The company counts on a MicroStep plasma cutting machine with an extraordinary configuration for 2D and 3D cutting to process their plates and domes.
in demand when customers ask for solutions from Slawinski & Co. GmbH from Siegen in the north west of Germany. The tailor-made container bottoms and
specialized pressure-vessel parts are known to manufacturers of pressure vessels and containers throughout Europe and beyond because of their quality. The fourth generation of the approximately 130 employees use their experience and state-of-the-art technology to create customized products. The range of end products is large, each one a unique piece. Circles are cut out of metal plates and, after dishing, flanging, spinning, edge- and surface-processing, turned into container heads and bottoms, arched floors and much more. “We supply important components for construction of pressure vessels for power plants, tanks for chemical industry and high-pressure containers. There, the quality has to fit exactly,” explains technical director Rainer Jurreit.
Demand for openings in domes could not be met to
satisfaction
Despite the high quality of production, company‘s specialists were looking for new and better ways of meeting the transforming demands of customers. “Demands for openings in domes have been growing and we have not been able to satisfy it,“ says managing director Konstantin Slawinski. “We‘ve been searching for 10 years, looking at many manufacturers and technologies, including robots. However, due to the dimensions of the domes, they could not meet our vision,“ says Konstantin Slawinski. After all, the company produces domes with diameters of up to 5,400 mm.
At EuroBlech 2014 in Hanover, the company came across MicroStep. “There, we were looking for a machine for dome cutting, we wanted to cut radial holes. With our machine, we could not cut what we envisioned. That‘s when we noticed MicroStep, which we did not even know before,“ says Alexander Fries, head of production planning responsible for preliminary selection of technology. Managing director Konstantin Slawinski adds: “We have seen that it works. For the first time in our ten-year search we had a feeling that there is someone who wants to sell something they actually master.“
MicroStep has developed an innovative system for flexible and precise processing of metal plates and domes with exceptional dimensions. The DRM series, a multi-functional plasma cutting machine for the toughest jobs, has been expanded to include customized technologies for the container bottom specialist. A special dome cutting table can process domes from 500 mm to 5,500 mm in diameter The "pantograph" plasma rotator, with a tilt up to 120°, enables weld edge preparation also on the bottom edge of a dome. Plate cutting is possible with the same gantry on a work area of 14,000 x 6,000 mm, replacing the original plate cutting machine.
New standard for precision of contours and bevels on
domes
A brand new feature on the Slawinski machine was the mScan technology for measuring of the true surface shape of a particular dome. Following a 3D laser
scanning process to scan the dome entirely, advanced algorithms are used to adjust the movement of the cutting tool according to the real shape of a dome and compensate so for the measured deviations from its ideal shape. “Based on our ABP technology, we developed the mScan technology specifically for dome processing and our engineers and programmers adapted it to the needs of Slawinski. This technology sets new standards for precision of contours and bevels cut on domes,“ says MicroStep‘s co-founder and head of research & development Alexander Varga, Ph.D.
Konstantin Slawinski is very satisfied with the solution: “Cutting of both plates and domes is the optimal solution for our limited space. This system replaces two machines.“
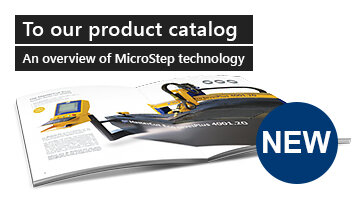
EXPERIENCE OUR SYSTEMS LIVE
in the CompetenceCenter South or North
- All four cutting technologies (laser, plasma, oxyfuel, waterjet)
- Innovative automation systems
- The latest solutions for bending and deburring
- Industry 4.0 demo factory
- Easy to reach: in the south and north of Germany
