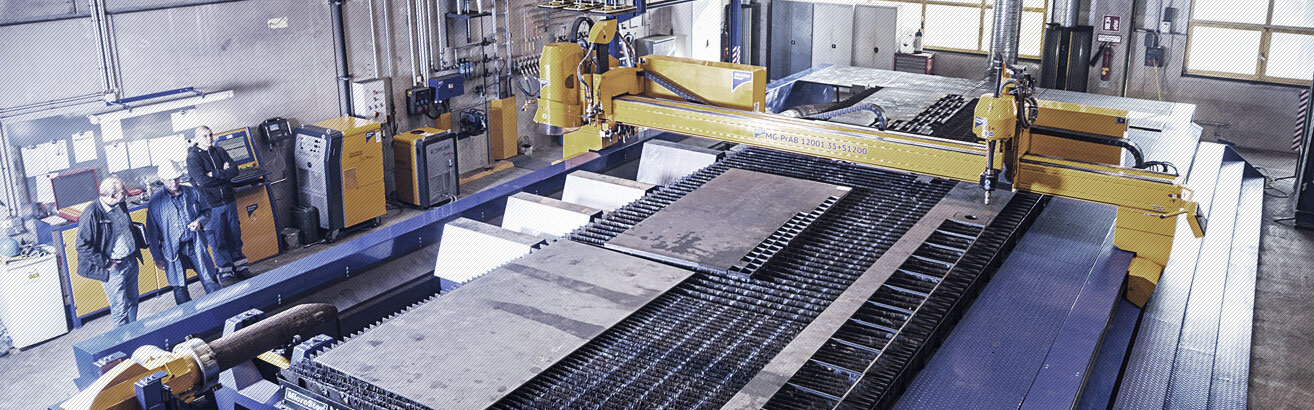
Predestined for a wide range of requirements for sheets, pipes and profiles: the MG at RW Montage
"We have chosen the best value for money"
RW Montage GmbH from Austria sets on the "everything in one solution" with technologies for bevel cutting, drilling and tapping on sheet metal, pipes and profiles
Published 28.11.2016 | Erich Wörishofer
Company profile:
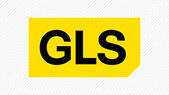
RW-Montage GmbH was founded in 1992 in Wels, Austria. The company is working nationally and internationally mainly in the fields of underground pipeline construction (gas, oil, district heating, drinking water and sewage), industrial plant construction, station construction, steel bridge construction, steel construction and track construction.
RW Montage GmbH invested in a plasma cutting system of the MG series. The system was equipped with a fully automatic drilling support, an oxyfuel torch, an R5 plasma rotator, a pipe cutting device and a cutting table with oscillating conveyor system. Photo: RW Montage / Alexander Firmberger
National and international construction projects are handled by RW-Montage GmbH. The Austrian steel and pipeline constructor uses the most modern machines and highest quality for production. The latest addition to the machine park is a multifunctional CNC machine from MicroStep. In addition to the possibility of 2D cutting with plasma and oxyfuel, the special plasma cutting machine of the MG series has technologies for bevel cutting, drilling, countersinking and tapping of sheets, pipes and profiles – as well as a modern oscillating conveyor table for the automatic discharge of slag and small parts.
With the most modern machines, highly trained employees, its own design office and production facilities, RW-Montage GmbH is able to handle projects of all sizes and degrees of difficulty. Since 1992, the Austrian company has been active nationally and internationally in a wide variety of projects in the fields of underground pipeline construction (gas, oil, district heating, drinking water and sewage), industrial plant construction, station construction, steel bridge construction, steel construction and track construction. About 30 kilometers east of Linz in Upper Austria, Perg and Ennsdorf are the two locations of the specialist company – here, administration and production buildings are located. In a 2,900 m² large, modern production hall with 20,000 m² storage space, the prefabricated parts for steel construction production and pipeline construction are processed using the latest technology.
Speed and multi-functionality decisive points for purchase
Since March, a multifunctional drilling plasma oxyfuel cutting machine of the MG series from MicroStep has been an important part of the machine park. The plasma cutting system is the all-rounder among the CNC machines – its multifunctionality was the decisive factor for RW-Montage GmbH. Numerous cutting and processing options were combined on the MG-PrAB 12001.35+S1200. Plasma cutting, oxyfuel cutting, bevel cutting, drilling, tapping, countersinking and marking are all possible on this high-tech version of sheet metal, pipes and profiles. The plate processing area is 12,000 x 3,500 mm. In addition, a modern vibratory conveyor table ensures the automatic discharge of slag and small parts.
Up to 50 skilled workers depend on the output of the cutting machine
With this, RW-Montage GmbH is entering new dimensions. Up to now, the company has relied on a plasma cutting system from MicroStep, which was built in 1998 and purchased second-hand. "The old system has served us well, but it is now getting on in years. It was time for a new purchase in order to be able to continue to work reliably and to be up to date," Jürgen Angerer, Division Manager for Steel Construction, looks back. After all, the plant was the first in the production chain, so it was crucial for operation. At peak production times, up to 50 people depend on the output of the cutting machine.
"We quickly realized that it can be profitable if you buy the everything in one solution. We decided on the best value for money".
Jürgen Angerer
Division Manager for Steel Construction | RW Montage GmbH
Machine profile:
MG series- Working area 12,000 x 4,700 mm
- Cutting of pipes Ø 30 - 1,000 mm up to a length of 12,000 mm
- R5 rotator for weld preparation up to 45° with auto-calibration feature (ACTG®)
- Drilling up to 40 mm and tapping up to bis M33
- 2D oxyfuel
Fascinated by the new possibilities
"The system works just as we imagined it would. The flexibility is the big advantage of the machine. We are known for this flexibility and also for speed. Our customers expect this from us," Angerer explains. The company has now also acquired a small storage facility so that it can respond within hours. In the first weeks of operation, the system was in operation 24 hours a day on six days to process a large internal order. In the future, however, there will also be room for contract work. "We have a lot of parallel running projects, the parts are getting bigger and bigger and have to be produced faster and faster. So now it is simply perfect. You need the part and we finish it quickly. The operators and I are fascinated by what is possible with this system," says Gerhard Hinterreiter, Head of Steel Construction Production.
Various pipe cutting systems inspected, "MicroStep came closest to 100 percent"
However, it took about a year of intensive research to achieve this additional flexibility. At several exhibitions, the decision to invest in a plasma pipe cutting system matured. The manufacturers who had this processing option in their portfolio were closely scrutinized and their systems were inspected and tested for suitability at companies in Austria. Afterwards the exact requirements were defined. "We drew up a specification sheet and MicroStep came closest to 100 percent by far," emphasizes Wolfgang Gattringer, Head of Production. On the advice of Managing Director Edmund Wall, the cutting system was set up even more flexibly in addition to plasma cutting and pipe processing, with a support for oxyfuel cutting and a fully automatic drilling unit.
"We have chosen the best value for money"
"We quickly realized that it can be profitable if you buy the egg-laying wool-milk sow. We decided on the best value for money," says Steel Construction Division Manager Jürgen Angerer. In addition, RW-Montage GmbH invested in a fourth crane in the 100-meter-long hall in order to be able to work off the increasingly peaks and operate the cutting system. Almost 3,000 parts were cut and processed weekly in the initial months.
Gerhard Hinterreiter, Head of Production in the Steel Construction Division, is looking forward to many more orders: "I am very happy that we chose the MicroStep system. I like the service there, I know the people, there is always someone to reach quickly. I also like the online portal for ordering spare parts very much. I ordered on Thursday morning and on Friday I already had the part. It works without any problems."
OVERVIEW OF THE HIGHLIGHTS OF MG-PRAB 12001.35+S1200:
Plasma cutting and oxyfuel cutting on a working area of 12,000 x 3,500 mm
The plasma oxyfuel cutting system has a working area of 12,000 x 3,500 mm. A HiFocus 360i neo with automatic gas console and ContourCut Speed technology from Kjellberg Finsterwalde serves as plasma power source. For higher material thicknesses the CNC machine was equipped with a RHÖNA-FIT machine cutting torch for oxyfuel flame cutting. An OXYtrac 36120 from Tecloga, an extraction table system with oscillating conveyor, is integrated into the gantry cutting machine as a working area. The oscillating conveyor system allows small parts, molten material and slag to be directed into a designated collecting container. With the existing sectional suction chambers, the particles produced during cutting are collected. The chambers are connected to a Donaldson DFPRO 16 Cyclopeel 14000 series automatic filter cleaning system.
Precise and universal 2D and 3D processing of sheets, pipes and profiles
For bevel cutting, for example for weld edge preparation, the combination system is equipped with an endless rotating R5 rotator. This was developed by MicroStep for the 3D processing of flat material, pipes, profiles or domes. With it bevel cuts up to 50° are possible.
In addition to 2D and 3D cutting of sheets and tubes, MG has integrated a further technology at RW Montage GmbH: a fully automatic drilling unit with a sixfold tool magazine. With the 26 kW drilling spindle, drillings up to 40 mm, threads up to M33 and countersinks are possible. A pneumatic stabilization system for material fixation ensures stability and precision during drilling and tapping.
Thanks to the RSV 30-1000 pipe cutting device and a pipe shaft, all technologies can be applied to pipes and profiles with a maximum diameter of 1,000 mm.
For easy and intuitive operation of the numerous processing options for sheets, pipes and profiles, the drill-plasma cutting machine has been equipped with a comprehensive software package from MicroStep and from PROfirst Group TOL Computersysteme GmbH (ProFirst CAM Pro / plasma-oxyfuel).
Photos: RW-Montage/ Alexander Firmberger; MicroStep
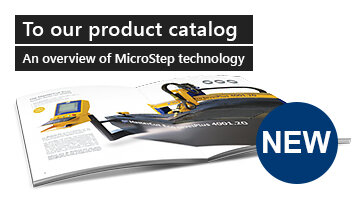
EXPERIENCE OUR SYSTEMS LIVE
in the CompetenceCenter South or North
- All four cutting technologies (laser, plasma, oxyfuel, waterjet)
- Innovative automation systems
- The latest solutions for bending and deburring
- Industry 4.0 demo factory
- Easy to reach: in the south and north of Germany
