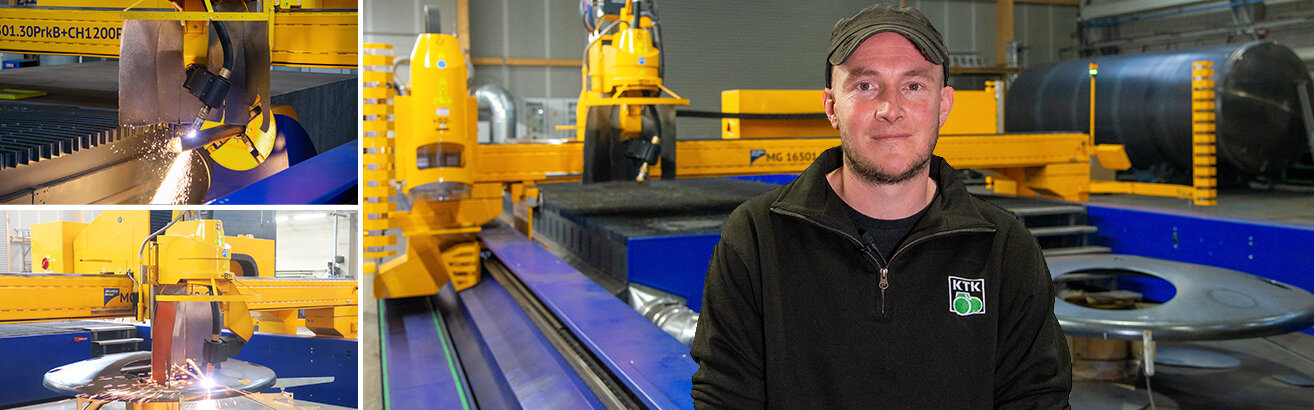
Fully satisfied with flexible line for cutting sheet metal, pipes and domes
"The package simply fit" for the versatile 3D plasma cutting system
Thanks to the investment in a multifunctional CNC cutting center from MicroStep, Kammerer Tankbau GmbH, based in South Tyrol, can act faster and more efficiently in its tank production.
Published 01.06.2023 | Erich Wörishofer
Company profile:

Kammerer Tankbau GmbH, founded in 1946 as a plumbing company, is located in the Puster Valley in South Tyrol. With around 50 employees, the company produces tanks made of mild steel as well as stainless steel for customers from industry, gastronomy, trade or construction among others, throughout Europe. The tanks are used for the storage of fuels, drinking water, pellets or also as buffer storage.
Kammerer Tankbau invested in a 3D plasma cutting system of the MG series with a working area for sheets of 12,000 x 3,000 mm as well as systems for pipe and dome processing and technologies for bevel cutting, drilling, countersinking and tapping.
Machine profile:
MG series- Working area for sheets 12.000 x 3.000 mm
- Cutting of domes Ø 500 – 3,600 mm
- Cutting of pipes Ø 30 – 500 mm up to a lenght of 12,000 mm
- Plasma rotator for weld preparation up to 50° and for dome processing with auto-calibration feature (ACTG®)
- Drilling up to Ø 40 mm and tapping up to M30
At its headquarters in Kiens in the Pustertal Valley, Kammerer Tankbau GmbH mainly produces tanks made of mild and stainless steel for the storage of various media such as gasoline, oil or water. Due to the continuously strong order situation combined with the growing need for independence from suppliers, the company decided to invest in its own cutting system. When comparing several offers, the MG series plasma cutting system from MicroStep was quickly convincing: "The package simply fit". The system now brings a number of advantages in the production of true giants.
Founded as a plumbing company, Kammerer Tankbau GmbH has developed into a sought-after company in the field of tank and cistern production in its more than 75-year history. Throughout Europe, customers from industry, gastronomy, trade and construction, among others, rely on the products of the South Tyrol-based company: metal tanks for fuels, stainless steel tanks for drinking water, bullet-proof tanks and much more. By using innovative technologies, the family-owned company, now in its third generation, is also constantly developing new products, such as pellet or AD Blue tanks, thus expanding its broad portfolio. Up to 260,000 liters capacity, up to 4 meters in diameter and up to 30 meters in length are not uncommon for Kammerer Tankbau's tanks. The mostly green fiberglass coating makes the products particularly durable and robust and is a real unique selling point.
Sheet metal, pipe and dome processing on one system
With around 50 employees, Kammerer Tankbau produces on more than 12,000 m² at its headquarters in Kiens. In addition to standard products, the company also designs and manufactures customized components according to specific requirements. For decades, sheet metal required for the tanks was cut by hand or outsourced to contract cutters. "Constantly full order books and ever longer delivery times from suppliers made it necessary to purchase our own cutting system," Hannes Engl, production and plant manager at Kammerer Tankbau GmbH, looks back. Through various exhibition visits, internet research and discussions with different manufacturers, the company set out to find a suitable universal machine for sheet metal, pipe and dome processing. When comparing several offers, MicroStep was quickly able to convince with its MG plasma cutting system, "because MicroStep offers the whole system and can meet all our requirements with the machine. The package simply fit," says Engl.
"Working much faster, more efficiently, and more flexibly"
The investment in the plasma cutting system has led to newfound flexibility and speed at Kammerer Tankbau: "When producing a tank end, we have a time saving of one day compared to the previous manual cutting," Engl reports with satisfaction. Since commissioning in January 2022, the multifunctional 3D cutting system has been in continuous use in single-shift operation, with two-shift operation planned. Precise weld seam preparation is particularly important for Kammerer Tankbau when cutting sheet metal for buffer tanks – thanks to the integrated plasma rotator, this can now be produced precisely and reliably on different workpieces and semi-finished products. The system is supplemented by a drilling unit for drilled holes, threads and countersinks for sheet metal processing. "We are absolutely satisfied with the technology. The acquisition of the machine has been profitable for us, as we can now work much faster, more efficiently and more flexibly." And the cooperation with MicroStep also convinces the production and plant manager: "Everything works smoothly. Good service is particularly important for us – and it works excellently."

"We are absolutely satisfied with the technology. The acquisition of the machine has been profitable for us, as we can now work much faster, more efficiently and more flexibly. Everything works smoothly. Good service is particularly important for us – and it works excellently."
Hannes Engl
Production and Plant Manager | Kammerer Tankbau GmbH
OVERVIEW OF THE HIGHLIGHTS OF THE PLASMA CUTTING SYSTEM MG:
3D plasma cutting machine with a working area of 12,000 x 3,000 mm
For cutting, Kammerer Tankbau GmbH relies on MicroStep's all-rounder, the MG series. The cutting system was configured for 3D processing of sheet metal with a working area of 12,000 x 3,000 mm. The machine can also process domes from 500 to 3,600 mm in diameter and, with the addition of a pipe cutting device, pipes from 30 to 500 mm in diameter and 12,000 mm in length. A plasma rotator is integrated for bevel cutting, for example for weld seam preparation up to 50°. As plasma source, a Q 3000 plus from Kjellberg is in use. The patented, automatic ACTG® calibration unit ensures permanently precise cutting results. By integrating a fully automatic drilling spindle, Kammerer Tankbau can drill holes up to 40 mm in diameter, threads up to M30 as well as countersinks in components.
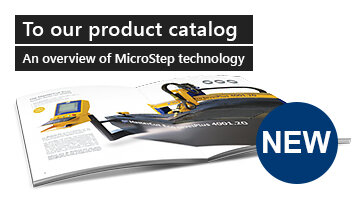
EXPERIENCE OUR SYSTEMS LIVE
in the CompetenceCenter South or North
- All four cutting technologies (laser, plasma, oxyfuel, waterjet)
- Innovative automation systems
- The latest solutions for bending and deburring
- Industry 4.0 demo factory
- Easy to reach: in the south and north of Germany
