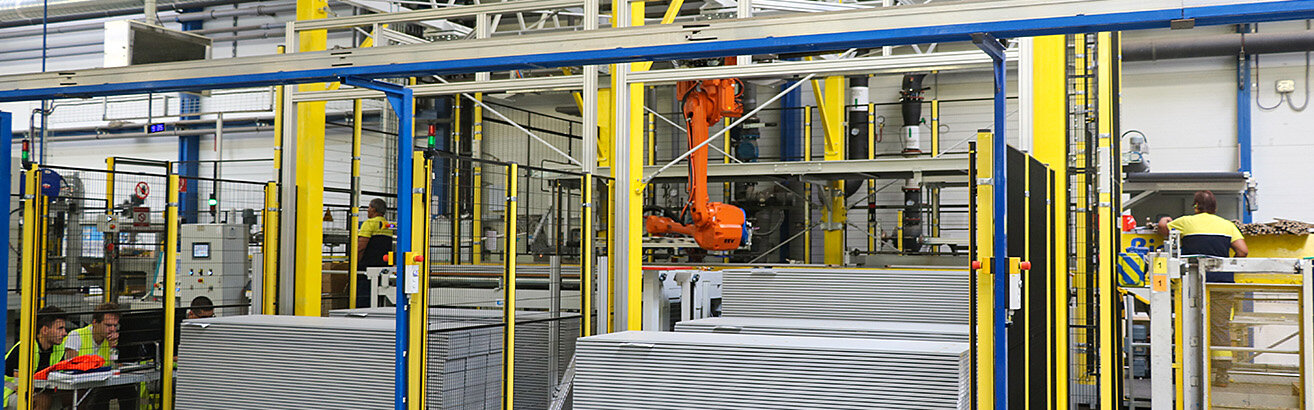
The production cell at IKEA with MicroStep technology
Exceptional automation solution for the IKEA furniture group
In a joint project with other partners (Photoneo, ABB) MicroStep realized a modular production cell with robot technology for the packaging of furniture
Published 09.09.2020 | Erich Wörishofer
Company profile:
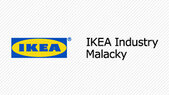
Továrenská 2614/19
901 01 Malacky
Slovakia
IKEA Industry is the world's largest manufacturer of wooden furniture and produces wood-based furniture for the global furniture group. The company maintains a production site in Malacky, Slovakia, near the Austrian border, among others.
Together with the partners Photoneo and ABB, MicroStep realized a modular production cell with robot technology for furniture packaging for the furniture group Ikea.
Ikea Industry, responsible for the production of furniture components at the global furniture giant, relies on ultra-modern automation systems. In 2019, an extraordinary robot solution went into operation, with which furniture parts can be packed automatically. MicroStep technology also played a decisive role in the joint project.
North of Bratislava, only a few kilometers east of the Austrian border, lies the Slovakian town of Malacky. This is where the globally active furniture group Ikea operates one of its production facilities under the label Ikea Industry and manufactures furniture components. The topics of efficiency and automation are given top priority. An extraordinary automation project for furniture packaging brought three different partners together. On board: the Slovakian company Photoneo, which develops state-of-the-art 3D optical systems for automation, the Swiss group ABB, one of the leading suppliers of industrial robots, and MicroStep, renowned manufacturer of CNC cutting machines and automation systems.
The mission: to develop and implement a modular production cell for furniture packaging – and to do so at correspondingly high speeds and with tight tolerances. "The aim of this pilot project was to research, develop and implement a modular and universal robot cell for the packaging of furniture parts. The challenge was to put the objects – in our case furniture parts – into boxes," says Anton Dvořák, Project Manager at Ikea Components, looking back. The furniture panels arrive in stacks, have to be taken over and transferred to a changing predefined position. An extremely high throughput of six seconds per cycle with a very high accuracy of ± 2 millimeters had to be achieved. "Right from the start, this project required the development of a localization system that did not yet exist in this form," says Dvořák. After all, the optical sensors had to recognize different material surfaces – from shiny to diffuse – in different colors. Photoneo achieved this by using two different scanning systems.
Like Photoneo, all three companies involved had to overcome different challenges. ABB supplied an industrial robot arm with a reach of 6,300 mm, MicroStep a modular robot transfer unit for reverse robot assembly including automatic lubrication. The positioning speed of the MicroStep technology is 2 m/s, the longitudinal traverse path within the production cell is 6,250 mm. The partnership bore fruit: the automation solution has been in successful operation since the end of 2019.
„Right from the start, this project required the development of a localization system that did not yet exist in this form.“ |
Anton Dvořák, Project Manager | Ikea Components |
Machine profile:
- Optical scanning system from Photoneo
- Industrial robot arm from ABB
- Modular robot transfer unit from MicroStep
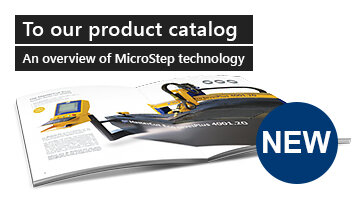
EXPERIENCE OUR SYSTEMS LIVE
in the CompetenceCenter South or North
- All four cutting technologies (laser, plasma, oxyfuel, waterjet)
- Innovative automation systems
- The latest solutions for bending and deburring
- Industry 4.0 demo factory
- Easy to reach: in the south and north of Germany
