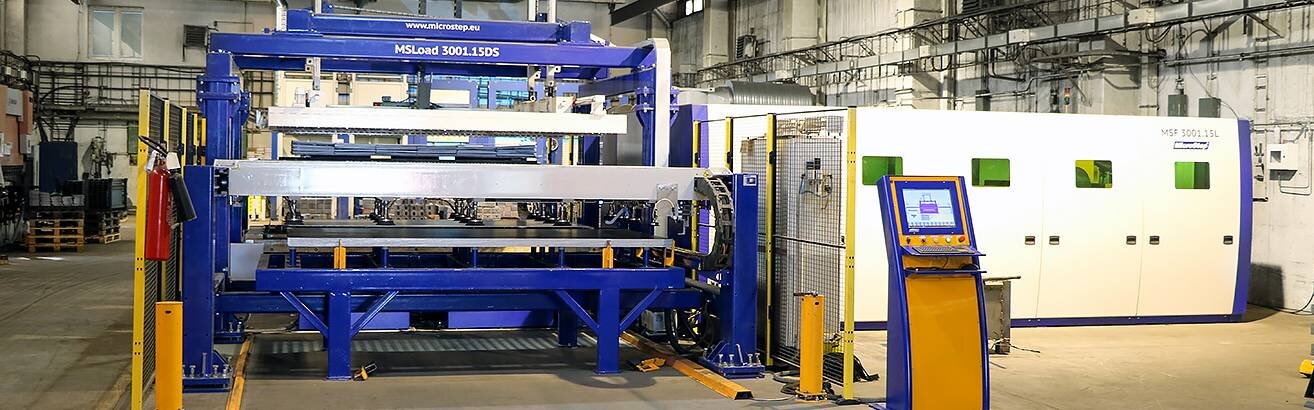
Fiber laser cutting system with automated material handling
Automation solution: efficiency boost for production
Fully satisfied: Slovakian steel manufacturer Hykemont invests in fiber laser solution with automatic material handling system
Published 07.02.2020 | Erich Wörishofer
Company profile:
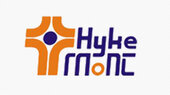
Považská 18
940 01 Nové Zámky
Slovakia
The Slovak steel construction company Hykemont spol. s r.o. concentrates on forming of large-sized steel sheets and welding of steel structures. Originally a pure manufacturer of steel storage containers, the company was later expanded to include component production and its entire history was marked by an exclusive contract with the Austrian steel shipping and storage container manufacturer CONTAINEX.
Since 2018, the Slovakian steel construction company Hykemont has relied on a fiber laser cutting system of the MSF series from MicroStep, including the material handling system MSLoad. The integrated 2D laser cutting system enables sheet metal processing on a working area of 3,000 x 1,500 mm.
For more than 25 years Hykemont spol. s r.o. has been producing steel construction elements. Almost the entire history of the company located in the southern Slovak town of Nové Zámky was "enriched" by an exclusive contract with the Austrian steel shipping and storage tank manufacturer CONTAINEX. This mutually beneficial relationship has brought stability to Hykemont and ensured continuous growth. In 2018 Hykemont invested in a fiber laser cutting system of the MSF series from MicroStep including the material handling system MSLoad. For production, this meant an eminent efficiency boost. The steel constructor took his time for searching.
Originally, Hykemont’s production was focused solely on steel warehouse containers and only later extended to component production. The decision to invest in a brand new cutting and material handling equipment has been a part of the company’s long-term growth plan. Hykemont wanted to innovate the production process and be less dependent on third-party suppliers. Since the company’s production is highly specialized, requiring large numbers of the same parts with minimal variability, an automated solution was preferable. Therefore, Hykemont was looking for a system able to cut 6 mm mild steel plates in two
shifts per day and to automatically load the raw material and unload the cut parts. After careful deliberation, Hykemont opted to buy MicroStep’s fiber laser machine MSF with a working area of 3,000 x 1,500 mm, equipped with a 4kW IPG laser source capable of cutting mild steel up to 20 mm thick.
Several advantages combined with automated laser cutting system
Productivity of this machine is further augmented by MicroStep’s automated plate loading system MSLoad – a stack of plates just needs to be placed on a designated position and the rest of the process is fully automated. Vacuum pads pick up a plate and a sensor measures its thickness. Based on this information, a corresponding cutting program is selected by the MPM software (Machine Production Management). The previously cut parts are meanwhile being unloaded from the cutting table onto a pallet using a fork unloading unit. The vacuum loader deposits the plate onto the cutting table and the cutting may begin. The pallet with the cut parts is moved to the unloading position of MSLoad where it is processed. “The new solution enables us to meet the market’s high demands in regards to both the quantity of ordered parts and their quality, which is vital since the cut parts are further being processed at a robotic welding station,” says Kristína Kolláriková Kulichová, CEO of Hykemont spol. s r. o. “Apart from these major advantages, there are also others like lower costs for a unit of production, higher utilization of resources, increased safety of our
orkers and a lower amount of manual labor.”
"The new solution enables us to meet the market’s high demands in regards to both the quantity of ordered parts and their quality, which is vital since the cut parts are further being processed at a robotic welding station.“
Ing. Mgr. Kristína Koláriková Kulichová
Managing Director | Hykemont spol. s r.o.
Machine profile:
MSF series- Working area 3,000 x 1,500 mm
- 2D fiber laser – 4 kW
- Automatic shuttle table
- MSLoad for automatic loading/unloading of sheets and cut parts
Four to five tons of structural steel in two-shift operation
The production manager Pavol Stromček also acknowledges the production boost: “Using this machine, two shifts are now able to process 4 to 5 tons of mild steel per day. The solution greatly saves the time that would be otherwise needed for manipulation with material.” Since Hykemont has opted for nitrogen laser cutting, they faced a new logistical problem. Even though nitrogen cutting is better for thin plates, it also consumes much more gas than oxygen cutting. The standard solution would require building a nitrogen tank and very frequent gas deliveries in order to maintain the nitrogen supply necessary for the production. But Hykemont preferred a more efficient option: the company purchased a nitrogen generator. Though the cost is substantial, it makes Hykemont self-sufficient in this regard and the investment should return within 5 years.
OVERVIEW OF THE HIGHLIGHTS OF THE LASER CUTTING SYSTEM MSF INCLUDING MSLOAD:
2D fiber laser cutting system with a working area of 3,000 x 1,500 mm
Hykemont spol. s r.o. relies on a fiber laser cutting system from MicroStep. The MSF series is a high-speed solution for precise cutting tasks and exact repeatability. The steel construction company invested in a laser system with a 2D laser cutting head and a working area of 3,000 x 1,500 mm. The 4 kW fiber laser source IPG YLS-4000 enables cutting of mild steel up to a material thickness of 20 mm. The Hykemont company mainly processes 6 mm mild steel sheets in two-shift operation.
Automatic material handling system MSLoad
MSLoad is a modular system for automatic loading of raw material and unloading of cut parts in combination with the laser cutting system MSF. The material handling system ensures that the material to be cut is transported from the pick-up station to the shuttle table by means of a vacuum lifter. From the shuttle table, the workpiece is automatically moved into the cutting cabin of the fiber laser, processed and then automatically removed again. The unloading fork removes the cut components and places them on the unloading station, while the vacuum lifters already place a new sheet on the cutting table. The cutting system can thus be continuously loaded and operated. System downtimes are minimized considerably.
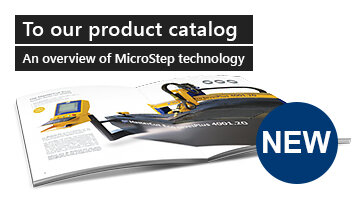
EXPERIENCE OUR SYSTEMS LIVE
in the CompetenceCenter South or North
- All four cutting technologies (laser, plasma, oxyfuel, waterjet)
- Innovative automation systems
- The latest solutions for bending and deburring
- Industry 4.0 demo factory
- Easy to reach: in the south and north of Germany
