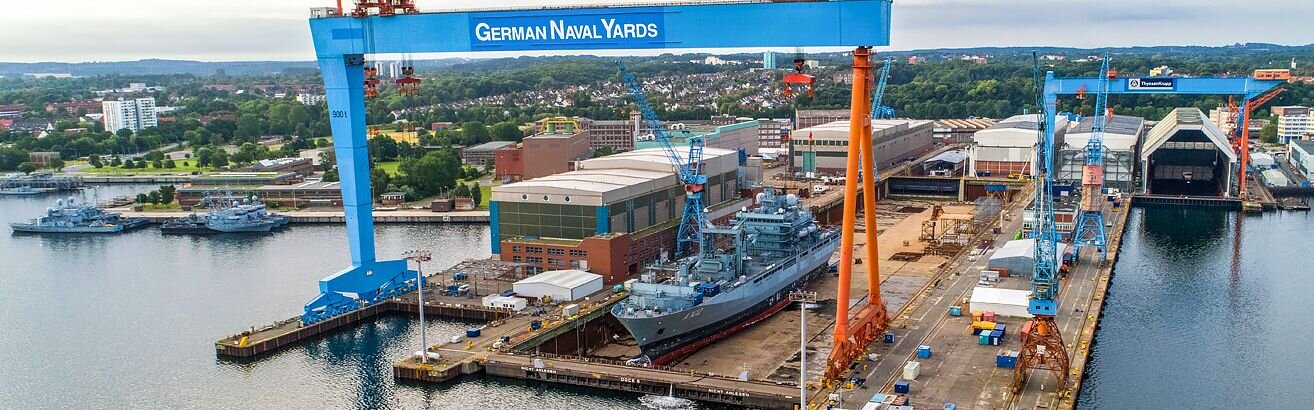
Unique shipyard infrastructure in Kiel at German Naval Yards. Three MicroStep plants are here in operation
Traditional shipyard trusts in cutting systems from MicroStep
Three cutting solutions from MicroStep are in operation at German Naval Yards Kiel. This company invested in different system types for plasma bevel cutting, oxyfuel cutting, marking, panel processing and more
Published 20.02.2020 | Melanie Lingemann
Company profile:
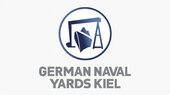
Werftstraße 11024143 Kiel
Germany
The landmark of Kiel and an important helper in shipbuilding: a 110-metre portal crane on the Kiel Fjord. Here German Naval Yards develops and produces maritime solutions on an area of more than 250,000 m².
More than 180 years of shipbuilding is in the DNA of German Naval Yards Kiel. In co-operation with other shipyards, the company is an expert in the production of naval ships – but also super yachts are launched within the group. When it comes to cutting, the company relies on solutions from MicroStep. The shipyard uses three types of systems. At the start of steel cutting, the focus is on the MG series with two gantries and an enormous working area. An indispensable part of the technology park for the traditional company.
The landmark of Kiel is also the figurehead of the shipyard German Naval Yards: a gantry crane with impressive dimensions. It is blue, 110 meters high, can lift 900 tons and has been a landmark of Kiel's cityscape since 1975. Like the Kiel Fjord, the traditional shipyard also belongs to the capital of Schleswig-Holstein. German Naval Yards continues more than 180 years of shipbuilding history. "Strong and reliable on all oceans of the world" is the motto of the high-tech company. The specialist for the design and construction of naval vessels such as frigates, corvettes and patrol boats as well as the construction of superyachts has a unique shipyard infrastructure: For example, one of the largest dry docks in Europe is in operation. The area on the Kiel Fjord covers more than 250,000 m². "The size of our shipyard facilities and the special features of our construction methodology enable us to use a quality-assured large block construction method with a high degree of pre-fitting," explains Jan Fust, Manager Steel Construction. In this way, many work steps can be shifted forward from the dock phase to the shipbuilding halls.
The infrastructural advantages also include the quality standard that German Naval Yards applies to every component. "We are the inventors of precision manufacturing – welding processes are coordinated in such a way that we operate a zero-defect tolerance. We use extremely stable processes," Fust continues. In order to be a leading company in the maritime industry, not only skilled workers but also appropriate technologies are required.
Three machine types for the 3D cutting of sheets from 3.5 to 200 mm
Since 2016, MicroStep systems have been involved in the construction of ships as German Naval Yards Kiel relies on solutions from MicroStep in the field of cutting. The supporting pillar at steel cutting start, so to say the hour of birth of the ship with the cutting of the first individual part from a steel plate, is the plasma cutting system of the MG series. The system has a working area of 52,500 x 3,500 mm – two gantries are used on this line. Both gantries are equipped with a plasma rotator for 3D processing of sheet metal. One gantry is also equipped with an inkjet marking unit, the other gantry with a laser marker. Mild steel but also high-alloy steels are cut with the versatile cutting system, which replaced a plasma cutting system from another supplier. The reason for the investment in the MG series was the precision in 3D cutting. For example, the width and length of a 12-meter cut must not deviate by more than 0.5 mm. "The accuracy is excellent, the dimensional stability of the machine is unbeatable", says Fust, who has gained experience at various shipyards over the years.
Since mid-2019, the EasyCut from MicroStep has been taking care of cutting jobs in the higher material thickness range at German Naval Yards Kiel. The flame cutting system is equipped with four oxyfuel torches. Among other things, flanges with blind holes for mechanical engineering are cut on it. Together with the MG plasma cutting machine, cutting tasks in the thickness range from 3.5 to 200 mm are processed. A DRM-PL gantry, which was built on top of an existing panel line, is also available for the processing of large-format sheets. Panels form the basic framework of decks and external skin and reach a size of up to 16 x 18 m. The MicroStep gantry of the panel cutting line has a width of more than 18 m with technologies for bevel cutting using an oxyfuel rotator, for primer removal with a sandblasting system and for marking.
"The accuracy is excellent, the dimensional stability of the machine is unbeatable"
Jan Fust
Manager Steel Construction | German Naval Yards Kiel
Machine profile:
DRM-PL series- Working area 18,000 x 16,000 mm
- Plasma rotator for weld preparation up to 45° with auto-calibration feature (ACTG®)
- Sandblasting unit for primer removal + plasma marking
- Operator platform with MMI console on the gantry
- Inkjet marking
MG series
- Working area 52,500 x 3,500 mm
1. Gantry
- Plasma rotator for weld preparation up to 45° with auto-calibration feature (ACTG®)
- Inkjet marking
2. Gantry
- Plasma rotator for weld preparation up to 45° with auto-calibration feature (ACTG®)
- Laser marking
OVERVIEW OF THE HIGHLIGHTS OF THE PLASMA CUTTING SYSTEM MG:
Plasma cutting system with two gantries and a working area of 52.500 x 3.500 mm
A cutting system of the MG series was installed at the shipyard in two phases. Since then, the plasma all-rounder at German Naval Yards provides a working area of 52,500 x 3,500 mm and two gantries with different processing technologies. The system is designed for permanently accurate results in multi-shift operation. The automatic, patented ACTG® calibration unit from MicroStep ensures precise results throughout the machine life. To extract the dust generated during cutting, the company relies on two 18.5 kW ZPF 9H series filter units from Teka for indoor installation.
1. Gantry with plasma rotator and laser marking system
Plasma supports were integrated on both gantries for the cutting of medium material thicknesses. Each gantry is equipped with a MicroStep plasma rotator, an endlessly rotating bevel unit, which enables bevel cutting up to 45° for weld edge preparation, for example. A powerful plasma system from Kjellberg, a HiFocus 440i neo, serves as power source at each gantry. In addition, a laser marker was implemented on one of the two gantries, an extremely precise solution for the marking of components.
2. Gantry with plasma rotator and inkjet marking unit
On the second gantry there is also a plasma rotator for high-precision and flexible bevel application available, which is operated by a Kjellberg HiFocus 440i neo, too. An inkjet marking unit for automatic inkjet marking was also integrated in the system.
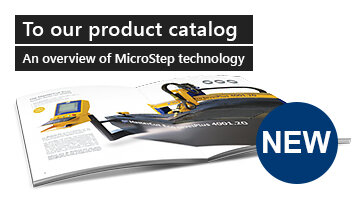
EXPERIENCE OUR SYSTEMS LIVE
in the CompetenceCenter South or North
- All four cutting technologies (laser, plasma, oxyfuel, waterjet)
- Innovative automation systems
- The latest solutions for bending and deburring
- Industry 4.0 demo factory
- Easy to reach: in the south and north of Germany
