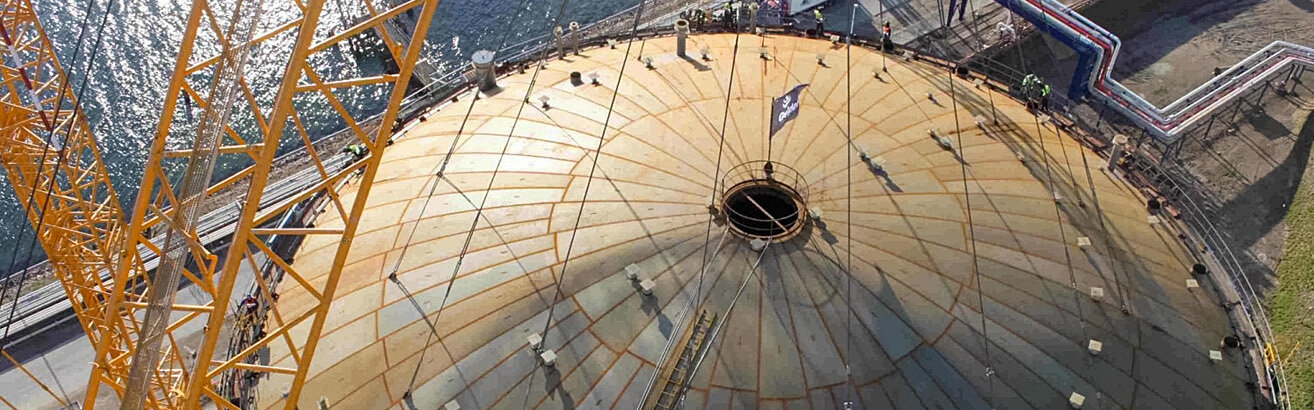
The specialist for bulk material containers manufactures complex solutions such as storage tanks or pressure vessels
Tank and pressure vessel specialist invests in modern and flexible cutting solution
Engicon nv (Geldof) built a new custom-fit hall especially for the new cutting system – the 3D plasma cutting system from MicroStep with Tecloga shuttle table saves a lot of time and optimizes production thanks to the plasma rotator and other technologies
Published 18.09.2022 | Erich Wörishofer
Company profile:
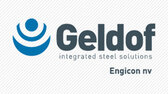
Engicon nv (Geldof)
Broelstraat 20
8530 Harelbeke
Belgium
Engicon nv (Geldof) is a leading European supplier of integrated steel solutions for the storage, handling and processing of bulk liquids, solids and gases. The company has a strong reputation in the realization of storage tank projects, pressure vessels, dry bulk storage and handling installations, as well as various other engineered solutions that often require a combination of wide-ranging technical know-how.
www.geldof.be
Engicon nv (Geldof), with direct access to the major ports of Ghent and Antwerp, is known for its technically complex solutions. The Belgian company specializes, among other things, in the manufacturing of storage tanks, pressure vessels or equipment for the storage and handling of bulk materials.
Machine profile:
MG series- Working area 14,000 x 4,500 mm
- Plasma rotator for weld preparation up to 45° with auto-calibration feature (ACTG®)
- 2D oxyfuel
- Micro-percussion marking
- Automatic shuttle table
Engicon nv (Geldof) is known for its technically complex solutions, which often require a combination of wide variety of know-how. The Belgian company specializes, among other things, in the production of storage tanks, pressure vessels or equipment for the storage and handling of bulk materials. When an outdated plasma cutting system had to be replaced, Engicon was looking for a modern solution including a bevel cutting tool. They found what they were looking for with MicroStep and its all-rounder MG including a plasma rotator and oxyfuel torch as well as a Tecloga shuttle table system.
Engicon nv (Geldof) located in Harelbeke, Belgium, is a leading European supplier of integrated steel solutions for the storage, handling and processing of bulk liquids, solids and gasses. The strategic location on the bank of Leie River with direct access to the major ports of Ghent and Antwerp provides Engicon with easy access to the worldwide market. Engicon's own quay facility enables the loading onto barges of items up to 300 tons, 150 m length and 15.5 m diameter. Large constructions can be transported trouble‐free by ship or by a truck.
Plasma rotator required to reduce costly post processing
The purchase of a new CNC cutting solution became a necessity after the old plasma machine needed to be replaced after 31 years of service. Engicon saw this also as an opportunity to expand their manufacturing possibilities and raise precision and quality to a new level. Most notably, the company wanted to incorporate bevel cutting into their production since beveled edges are ready for welding without requiring any further machining thereby significantly reducing the processing time and workforce requirements.
After careful deliberations, Engicon nv chose to purchase a MicroStep machine from the MG series. The company was looking for a stable and permanently precise solution that would ensure consistent quality even in multi-shift operation. Engicon usually produces in two shifts and cuts around 10,000 to 15,000 tons of steel per year. The new system went into operation in spring 2018. With a working area of 14 x 4 meters and an integrated technology combination of a plasma rotator for 3D sheet metal processing and an oxyfuel torch for higher material thicknesses, Engicon relies on a versatile CNC cutting center capable of producing a wide range of parts from sheets of different sizes and thicknesses.
Parts marking ensures traceability of sensitive components
In addition, a micro-percussion marking unit has been integrated which applies the batch number of the original plate to the individual cut parts. This ensures traceability of production – an important option especially in the production of sophisticated tanks for sensitive goods. In the event of a possible part defect, all parts of the same plate batch can thus be identified and potential problems rectified at an early stage.
Another factor in the configuration of the new 3D cutting system was the integration of a shuttle table. After careful analysis and intensive exchange, Engicon and MicroStep decided to use a system from the German cutting table specialist Tecloga due to the planned size of the table. The 14 x 4 meter shuttle table was designed in such a way that after cutting, the grid with the finished cut parts moves to a separate room and only there the parts are unloaded. This solution makes unloading as well as subsequent loading with the new material much safer.
Several measures for the safety of employees
For the protection of their employees, Engicon has implemented high safety, health and environmental standards. For this reason, a separate hall was even built for the new machine, specifically for the requirements of plasma and oxyfuel cutting. In addition to the separated premises for the cutting process and the loading and unloading process, other measures were implemented. "Special light barrier protection and an ergonomic operating system were installed around the machine. There is even a separate control room for the operator," says Dieter Vandeputte, maintenance & facility manager at Engicon.
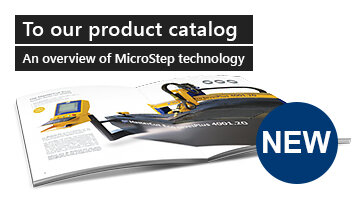
EXPERIENCE OUR SYSTEMS LIVE
in the CompetenceCenter South or North
- All four cutting technologies (laser, plasma, oxyfuel, waterjet)
- Innovative automation systems
- The latest solutions for bending and deburring
- Industry 4.0 demo factory
- Easy to reach: in the south and north of Germany
