
EBAWE relies on a combined CNC drilling and cutting center
A custom MicroStep machine doubled the productivity at EBAWE
EBAWE Anlagentechnik GmbH: Manufacturer of complex production systems relies on a combined CNC drilling and cutting center from MicroStep – „The machine does exactly what it is supposed to“
Published 01.09.2021 | Erich Wörishofer
Company profile:

Dubener Landstraße 5804838 EilenburgGermany
EBAWE has more than 60 years of experience in designing, developing, manufacturing and installing of complete production systems for various concrete elements. The company from Eilenburg (Germany) provides tailor-made solutions for the manufacture of precast concrete parts.
Die Bearbeitungsfläche ist insgesamt 5,50 Meter breit und 50 Meter lang und ermöglicht somit die Be- und Entladung sowie die Bearbeitung von Bauteilen gleichzeitig.
A system that can reliably mark, cut, drill and tap – and all of this with extreme precision, even on particularly large workpieces: EBAWE Anlagentechnik GmbH, based in Eilenburg in Saxony, has chosen MicroStep as the right partner for this challenge.
Concrete is trending these days and is considered as a versatile material with a rough charm. Its usage worldwide, ton for ton, is twice that of steel, wood, plastics, and aluminium combined. The customers of EBAWE Anlagentechnik GmbH benefit from this trend greatly. With help of the company's technological know-how they manufacture walls, ceilings, stairs and much more from this highly flexible and durable material. For more than 60 years, EBAWE has been developing, manufacturing and installing complete production systems for the industrial manufacture of a wide variety of precast concrete elements.
EBAWE production systems for concrete processing are in world-wide demand and extremely complex. Their installation often requires several thousand square meters of space. At the same time the machinery needs to work with utmost precision since production of prefabricated concrete elements requires high levels of accuracy. “In order to be able to cast concrete parts, we have to produce a so-called mold palette for it. This is basically a base plate onto which the side formworks are applied to make a mold for the casting process,” explains Pierre Winkler, Production Manager of EBAWE.
These mold palettes are usually made from 8 mm thick special metal sheet, which in some cases have dimensions up to 18 meters in length and 4.80 meters in width depending on how large the finished concrete part should be.
At MicroStep, the needs of the customer were taken seriously from the beginning
“In the past, we have already used a thermal cutting system to produce all the different molds. However, the productivity of the old machine has reached its limits in recent years,” says Winkler. Therefore, EBAWE has started looking for a new, faster and more efficient alternative for the production of mold palettes. "We were not sure if we could find a suitable partner who can fulfil our requirements and implement it the way we imagine it," says Winkler. In the end, after a comprehensive internet research and multiple exhibition visits, the choice fell on MicroStep. “From the beginning, we had the feeling that our needs were taken seriously and that our special requests were also taken up.”
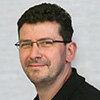
„Drilling speed has significantly increased compared to the old system – and now, we can also cut threads with the same system, which is another great advantage.“
Pierre Winkler
Production Manager | EBAWE Anlagentechnik GmbH
Machine profile:
DRM series- Working area 50,000 x 5,500 mm
- 2D plasma cutting
- Drilling up to Ø 40 mm and tapping up to M33
"Drilling speed has significantly increased compared to the old system"
EBAWE has decided for a solution that can handle several tasks at once. The work area is 50,000 mm x 5,500 mm and it has two gantries, enabling loading, unloading and processing of several components simultaneously. The first gantry was supplied by a company that specializes in grinding solutions. In the first step of the process, it ensures that the surface of the mold pallete is smoothly grinded – as for the exposed parts of the concrete cast it is important to have a uniform surface structure. Afterwards, the second gantry – MicroStep – marks the processed part with plasma, indicating the spots where the side formworks should be welded on. The same gantry can also drill holes with threads, another option to attach formwork elements. “The drilling speed has increased significantly compared to the old system and the fact that we are now able to do the tapping on the same machine is another great advantage,” says Winkler.
A satisfied customer: "The entire process with MicroStep went really well."
In the end, the parts are finally cut by plasma. Especially with particularly large mold palettes which can have an edge length of 10 meters and more, it is extremely important that the deviations from the set zero point do not exceed a maximum of ± 0.5 mm over the entire length. And that was achieved thanks to innovative solutions from MicroStep. With this new system, EBAWE has doubled its productivity in the manufacture of mold palettes. "Everything worked out right from the beginning and the cooperation with MicroStep ran very smoothly," says Pierre Winkler. The machine does exactly what it is supposed to.
DIE HIGHLIGHTS DER PLASMASCHNEIDANLAGE DRM 50001.50PB IM ÜBERBLICK
Große Bearbeitungsfläche von 5.500 x 50.000 mm
Die EWABE Anlagentechnik GmbH entschied sich für ein Plasmaschneidsystem der DRM Baureihe mit einer Arbeitsfläche von 5.500 x 50.000 mm zur Blechbearbeitung. Neben dem Schneid- und Bohrportal von MicroStep wird der Arbeitsbereich auch von einem Schleifportal genutzt. U.a. vor diesem Hintergrund handelt es sich bei dem Tisch um eine Sonderkonstruktion, die beim Schneiden eine effiziente und sektional gesteuerte Absaugung entstehender Stäube gewährleistet.
Plasmabrenner kann auch für einfache Fasenschnitte verwendet werden
Der Plasmasupport ist prinzipiell für den 2D-Zuschnitt ausgelegt, kann jedoch manuell in Y-Richtung um 45° justiert werden, um in X-Richtung eine Schweißnahtvorbereitung am Blech anzubringen. Als Plasmaquelle dient eine HiFocus 161i neo von Kjellberg Finsterwalde mit automatischer Gaskonsole sowie Contour Cut Speed Technologie.
Vollautomatische Bohrspindel bis 40 mm Durchmesser (26,8 kW) und Gewinde bis M33
Mit der vollautomatischen und 26,8 kW starken Bohrspindel können auch präzise Bohrlöcher bis 40 mm, Senkungen sowie Gewinde bis M33 angebracht werden. Die Bohrspindel hat einen vollautomatischen Werkzeugträger und ist mit einem Werkzeugmagazin für bis zu sechs Werkzeuge ausgestattet. Zudem ist ein vollautomatisches, pneumatisches Stabilisierungssystem in der Schneidanlage integriert, das den Support sowie die Portalbrücke mit einem Klemmsystem auf den Linearführungen während des Betriebes der Bohrspindel fixiert.
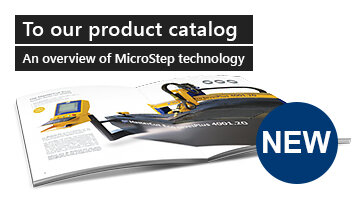
EXPERIENCE OUR SYSTEMS LIVE
in the CompetenceCenter South or North
- All four cutting technologies (laser, plasma, oxyfuel, waterjet)
- Innovative automation systems
- The latest solutions for bending and deburring
- Industry 4.0 demo factory
- Easy to reach: in the south and north of Germany
