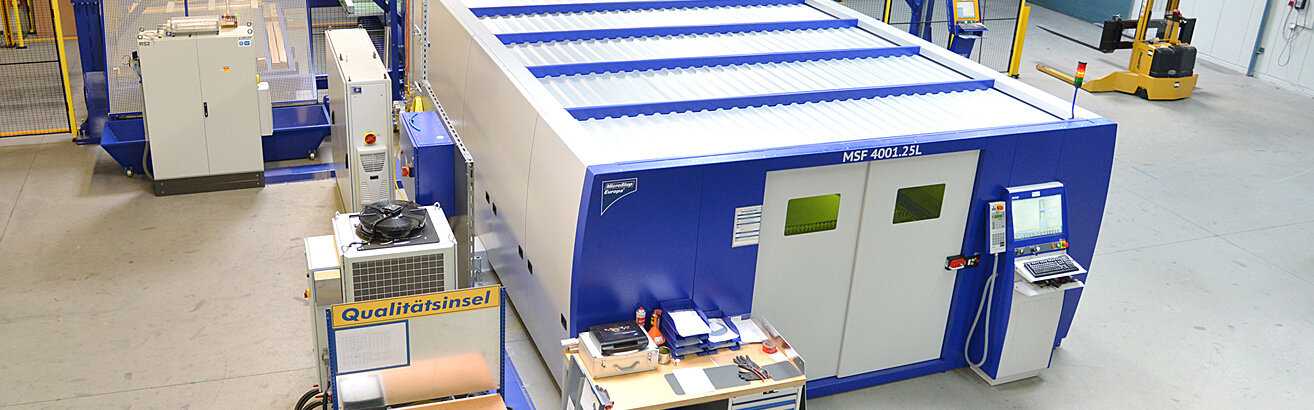
One laser, one automation system, many advantages
"Entering the 21st century at light speed"
Swarco Dambach, specialist for road signs and traffic signals, rejuvenates and strengthens its machinery with a 2D laser including the automatic material handling system MSLoad
Published 08.07.2022 | Erich Wörishofer
Company profile:
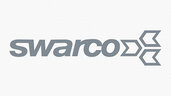
Swarco Dambach GmbH has been developing and producing innovative, individual solutions for securing, guiding and regulating road traffic for many decades. Founded in 1925 and located in Gaggenau, Germany, the company is now part of the international Swarco Group, the full-service provider of products, systems, services and solutions in road marking, signage, traffic signalization and traffic management.
The core competencies of Swarco Dambach GmbH today include development, production, assembly and after-sales service in the field of static signage systems (traffic signs, large and small signs of all types, gantries for all types of traffic signs, construction site systems and much more).
www.swarco.com
Swarco Dambach strengthens its machine park with a 2D laser of the MSF Pro series including the automatic material handling system MSLoad.
Machine profile:
MSF series
- Working area 4,000 x 2,500 mm
- 2D fiber laser – 4 kW
- Automatic shuttle table
- MSLoad for automatic loading/unloading of sheets and cut parts
Whether at construction sites, on the highway or at a town entrance: the traffic signs, road signs and gantries from Swarco Dambach GmbH regulate traffic in many places. The production in Gaggenau on the western edge of the Black Forest, relied for many years on the same machinery. With the investment in a modern 2D laser cutting system from MicroStep, including a material handling solution, an enormous leap towards more efficiency and flexibility was achieved. An important tool to continue to set the tone in a closely contested market.
Everyone knows the products of Swarco Dambach GmbH. Whether you are on foot, by car, bus or train: What comes from the company based in Gaggenau (Baden, Germany) and generally from the entire Austrian Swarco Group, guides our way and gives us direction in everyday life. This is because Swarco develops and produces solutions for securing, guiding and regulating road traffic, such as road markings, signage or traffic signals. "Swarco is a company that manufactures products under the highest quality standards, is always very close due to an extremely good customer relationship and knows what the market needs with the ability to react very quickly to changes. Our customers are spread all over the world and in the end all road users are our customers," says Andreas Flamm, strategic purchaser at Swarco.
Swarco has many different systems in its product range and is also developing new types of digital and automated components for even better and faster traffic management. The market for standard signage is highly competitive. In Germany alone, around 15 manufacturers are competing with each other. The sheet metal is specified, as is the foil coating and also the RAL color. A few factors are decisive in winning over federal, municipal or local authorities: "The minimum qualities are clearly defined, delivery times and the cost factor play a key role. Efficiency and flexibility in production are correspondingly important," emphasizes Bernard Frank, plant manager at Swarco Dambach in Gaggenau.
Modern 2D laser replaces ten machines thanks to precision and automation system
For more production speed and efficiency in the processes, the long-established company has recently begun to invest more in the modernization of the clearly aging technology park. The most important new addition is a fiber laser system of the MSF Pro series from MicroStep, including the automatic sheet material handling system MSLoad. The new solution replaces ten systems in production, formerly consisting of punching-nibbling machines, laser machines and milling machines. "We are now more flexible, faster, more efficient, produce more cost-effectively and with more quality. We have arrived in the 21st century at the speed of light," says Andreas Flamm about the 2D laser cutting system installed in spring 2021 with a working area of 4,000 x 2,500 mm. The main part of the cutting task is the processing of aluminum in the thin sheet range (2 and 3 mm). The reworking of earlier days is completely eliminated here. Only in a few cases slightly thicker sheets and rarely steel are cut. Just as required by the standards on this world' s roads.
A lot of planning and preparation for the implementation of key technology
When searching for the right solution, Andreas Flamm and Bernard Frank took their time. After all, they had to define a new system and install a groundbreaking key technology in the company. From the very beginning, it was clear that it had to be a 2D laser cutting machine; 4 x 2 meters of standard sheet metal with the additional challenge that no scratches should be made on the material during the entire process. It was not until the market was evaluated that the idea of a loading system was born, and in the later planning process, an additional unloading technology. "Not all manufacturers have this technology with automation. Some might offer it, but then would have to develop it. MicroStep had the system and it works. That's why I'm satisfied. The concept of picking up the sheets without leaving scratches also works," says Bernard Frank.
Yet the decision-making process was a long journey that also demanded a lot from the manufacturers. "We are definitely a demanding customer. We sent an incredible number of samples around, tested and lasered them. Played with different laser powers, played with different sheet thicknesses. Because this is a huge investment for us, and it has to work exactly the way we need it to. MicroStep spared no effort," Andreas Flamm looks back.
Contract cutting services possible as well
For the two people responsible, intensive planning and many extra rounds were necessary. In the end, a solution was found that covered all requirements. Flamm estimates the return on investment at around two years. Capacities for additional contract cutting operations are available. "If all projects went like this, we would all be happy," says the strategic purchaser.

"We are now more flexible, faster, more efficient, produce more cost-effectively and with more quality. If all projects went like this, we would all be happy."
Andreas Flamm
Strategic Purchase | Swarco Dambach GmbH
OVERVIEW OF THE HIGHLIGHTS OF THE LASER CUTTING MACHINE MSF WITH AUTOMATION SYSTEM MSLOAD:
MSF Pro 2D laser cutting machine with a working area of 4,000 x 2,500 mm
Swarco uses the MSF Pro series (formerly MSF series) for cutting flat material. The exclusive high-speed solution for demanding laser cutting sets standards in terms of multifunctionality and process reliability and has a high degree of automation (including shuttle table, cleaning and calibration station, automatic nozzle change). Swarco opted for a version with the EX-TRABEAM® PRO 2D laser cutting head and a YLS 4000 IPG fiber laser source with 4 kW cutting power. The working area of the automatic shuttle table system is 4,000 x 2,500 mm. For filtration, an extraction technology from Donaldson is used (DFPRO 8-R Cyclopeel filter system).
MSLoad: Perfect production helper for maximum efficiency
For even greater efficiency and productivity, Swarco invested in an additional automation solution in combination with the MSF fiber laser: MSLoad is a modular system that is used to automatically load raw material and unload cut parts. It can be used with MicroStep laser and plasma cutting systems that have an automatic shuttle table system. The material handling system ensures that the material to be cut is transported from the pick-up station to the shuttle table by means of a vacuum lifting device. From the shuttle table, the flat sheet is automatically moved into the cutting cabin of the fiber laser, processed and then automatically transported out again. The unloading fork removes the cut components and deposits them on the unloading station, while the vacuum lifters already deposit new material on the cutting table. In this way, the cutting system can be continuously fed and operated. In order to keep scratches on the raw sheets adhering to each other to a minimum, Swarco has integrated yet another technology: During the loading process, only a single suction plate is initially lifted to separate sheets that are sticking together. In the next step, a sensor measures the material thickness and then – if the parameters from the loaded cutting program match – the software gives the go-ahead to move the sheet to the shuttle table.
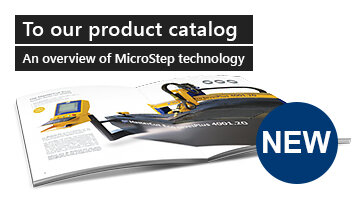
EXPERIENCE OUR SYSTEMS LIVE
in the CompetenceCenter South or North
- All four cutting technologies (laser, plasma, oxyfuel, waterjet)
- Innovative automation systems
- The latest solutions for bending and deburring
- Industry 4.0 demo factory
- Easy to reach: in the south and north of Germany
