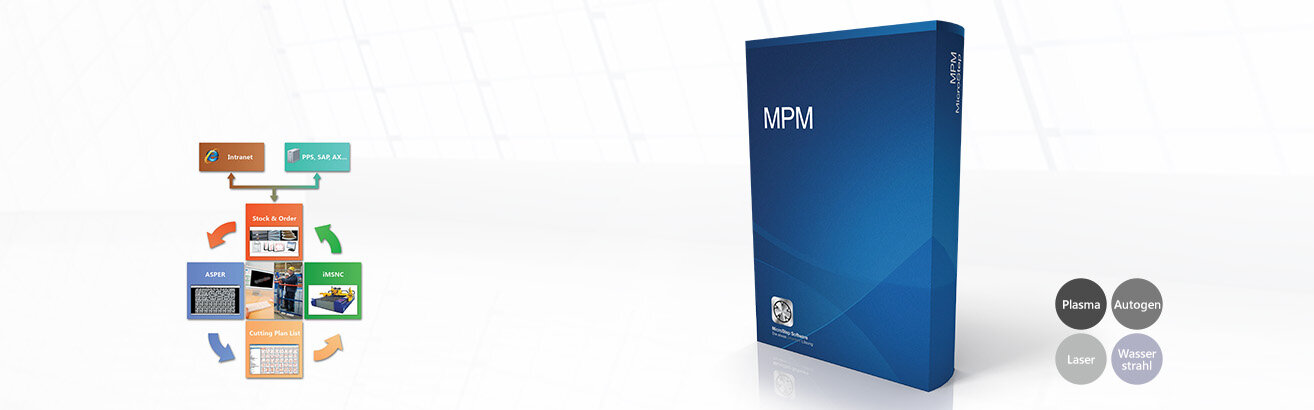
For order management , production analysis and more: Machine Production Management MPM
Production management with MPM: control and efficiency in all processes
The software system facilitates planning and coordination of cutting and helps reduce costs. Manage orders with MPM, connect material warehouses, evaluate production and more
Published 29.07.2019 | Erich Wörishofer
Machine Production Management (MPM) software suite provides computer-aided process planning (CAPP) features for automation of the workflow on CNC machine(s) or production lines. It is an integrated system of order processing, nesting, stock management, machine operation planning and evalution which interconnects pre-production data, control systems of CNC machines and MicroStep‘s automatic nesting software AsperWin®. It helps to reduce work-in-progress, to save material, and to eliminate operator errors.
A substantial part of MicroStep‘s product portfolio is focused is on high-end customers with large production facilities, who put emphasis on efficiency and a high level of automation. Complying with these requirements, MicroStep offers an in-house developed CAPP application called MPM (Machine Production Management), which is an integration platform for different areas of the business – material storage, order management, creation of cutting plans, and CNC machines operators, allowing automation of information flow among them.
MPM software is primarily aimed at facilitating efficient machine use. Used to its full potential, the machine‘s interface offers the operator a cutting plan together with the location of the specific material (plate, pipe…) in the warehouse. Operator‘s task is to place the material in the working zone of the machine, synchronize the coordinate system with the semi-product‘s spatial orientation (which can be automated by finding of the material edge by a laser sensor), install the required consumables and start the cutting process. All necessary parameters are selected automatically, based on the information contained within the cutting plan. When using an integrated loading system, the machine also loads the semi-product into the cutting area and can also facilitate the unloading of finished parts.
Although designed for MicroStep machines with AsperWin® CAM and iMSNC® control systems, MPM also offers possibilities of cooperation with third party machines. Naturally, the production data can be shared with customer‘s ERP system (e.g. SAP, AXAPTA). For effective production planning, the system provides weight analysis of particular orders along with weight reports of actual stock resources.
The primary target group for MPM application are businesses with multiple cutting machines, e.g. job shops or large steel processors in various industries (shipyards and offshore, energy, agricultural, automotive and others). One of the main benefits of this system is the automated task allocation for multiple machines based on priorities and technology availability.
The system offers a unique feature of providing feedback to the database after cutting: if specific parts have been cut incorrectly, the operator can identify them directly on the control screen. These parts are automatically returned to the order database and assigned the highest priority in the next nesting so that the order is completed as soon as possible. Processing status of each order or part can be monitored in the database in real time. This feedback feature is unique to MPM; it is not present in comparable systems on the market and is possible only due to the integration of the control software iMSNC® with the CAM software AsperWin® or mCAM, all in-house developed by MicroStep.
Integration with material loading systems
MPM features also a direct link to automated material loaders. The machine compares the cutting plans with the inventory of the warehouse and determines what is going to be cut. Based on the information received, it requests the needed types and amounts of material from the storage. A warehouse operator brings the material to the machine where it is loaded to the loading position and the rest of the process is fully automated: The loader loads the sheet into the machine. The machine can then check whether it is the required material by using a built-in thickness sensor or by scanning a barcode or QR code printed on the material. After the cutting process is complete, the machine sends information about what was cut to the MCP module (Management of Cutting Plans) and information about what kind and amount of material was used is forwarded to the storage database.
MPM and loaders are universal systems that can be configured to suit the specific manufacturing process exactly according to the customer‘s needs.
MPM is a comprehensive system of automation of the production cycle on cutting machines. Along with MicroStep machines, it has been already deployed in more than thirty businesses in Europe, Asia and South Africa.
Find out more about MPM here
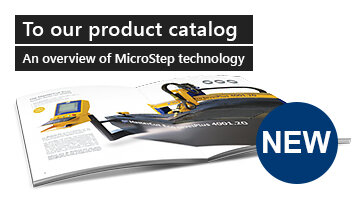
EXPERIENCE OUR SYSTEMS LIVE
in the CompetenceCenter South or North
- All four cutting technologies (laser, plasma, oxyfuel, waterjet)
- Innovative automation systems
- The latest solutions for bending and deburring
- Industry 4.0 demo factory
- Easy to reach: in the south and north of Germany
