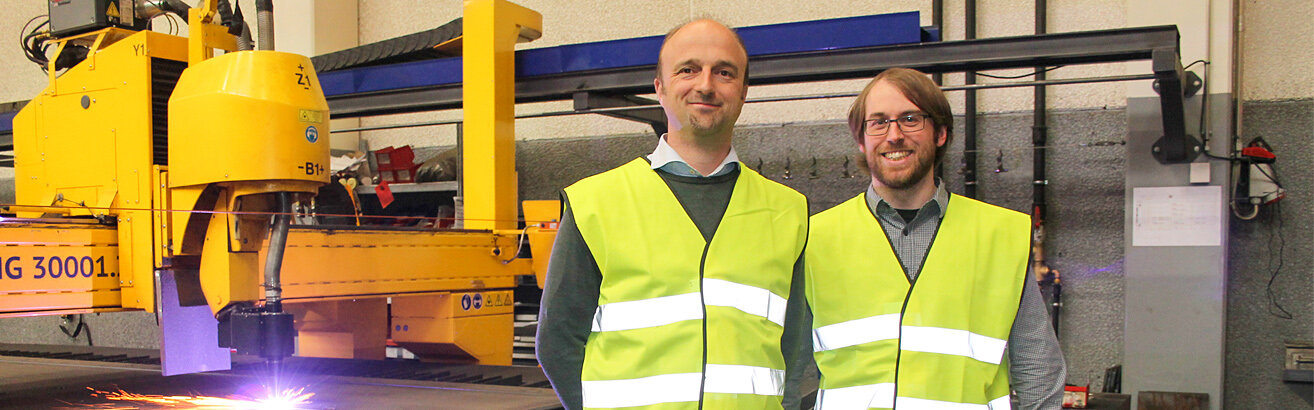
The special vehicle manufacturer Faymonville, based in Luxembourg
Cut with MicroStep: Special vehicles for the whole world
The Faymonville Group produces solutions for heavy load and special transport. For sheet metal processing, the family-owned company relies on MicroStep systems
Published 02.11.2021 | Erich Wörishofer
Company profile:
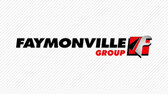
15, Op der Bréimicht
9779 LentzweilerLuxembourg
The Faymonville Group, based in Luxembourg, is an independent family business with more than 1,100 employees. The group specializes in transport solutions from 15 to 15,000 tons, produced at various locations in Luxembourg, Poland, Belgium, Italy and Russia on a total production area of approximately 150,000 square meters. More than 3,000 vehicles are produced annually and used in 125 countries. In 2020, sales amounted to 245 million euros.
At the Faymonville Group's largest production site in Luxembourg, the center also focuses on technology development. Two MicroStep plasma cutting systems are in operation at this location.
When heavy or really big things need to be transported, the special vehicles from Faymonville come often into play. The group, based in Luxembourg, is a family business and exports to 125 countries. For cutting at its largest production site near the Belgian border, the company relies on two 3D plasma cutting systems from MicroStep with identical processing technologies.
Based in the Grand Duchy of Luxembourg, just a stone's throw from the Belgian border, the Faymonville Group is today the leading manufacturer of a complete range of special vehicles for heavy and specialized transport. From low-bed trailers to extra-low-bed trailers, flatbed vehicles, modular vehicles and self-propelled vehicles, the company manufactures anything exceptionally heavy, long, wide or high. With payloads ranging from 15 tons to 15,000 tons and beyond. The Faymonville Group produces vehicles in standard or custom formats.
The standard size vehicles are manufactured in Poland under the name MAX Trailer. Thanks to standardized components and an adapted production process, it is possible to manufacture a high-quality product at optimum cost. And then there are the vehicles manufactured at the Luxembourg site. With a modular construction system, Faymonville offers its customers specific solutions that meet any requirements outside the usual standards. "Our customers appreciate our reliability and flexibility in offering suitable transport solutions even for major challenges. Our vehicles are characterized by their technical quality and our sustainable production methods," says Carsten Faber, process engineer at Faymonville.
Produced actively at several locations in accordance with local road traffic regulations
The entire production of the vehicles takes place in-house, whether in Luxembourg, Poland, Belgium, Italy or Russia. This starts with the cutting of the sheet metal and continues through to final assembly and finishing in accordance with the various road traffic regulations. Production levels and effective quality and process controls are put to the test every day.
About two years ago, the Lentzweiler plant in Luxembourg was equipped with two new MicroStep cutting systems. Faymonville opted for the MG series – as a 3D plasma cutting system with additional oxyfuel technology and an enormous working area. One system has a working area of 30,000 x 3,000 mm, the other 21,000 x 3,000 mm.
„The reliability of these machines and the follow-up service are very important for us, because the smallest incident affects the production time and a prolonged downtime is to be avoided at all costs.“
Carsten Faber,
Process Engineer | Faymonville Group
Machine profile:
MG series- Working area 30,000 x 3,000 mm
- Plasma rotator for weld preparation up to 50° with auto-calibration feature (ACTG®)
- 2 x 2D oxyfuel
MG series
- Working area 21,000 x 3,000 mm
- Plasma rotator for weld preparation up to 50° with auto-calibration feature (ACTG®)
- 2 x 2D oxyfuel
A new hall of around 3,000 square meters was specially built for the larger of the two machines. Thanks to the enormous length, one sheet can be prepared or cleared while another is being processed simultaneously. Nic Wouters, managing director of MicroStep specialist dealer Wouters Cutting & Welding, explains: "The high-end MG machine series is designed for continuous industrial use and meets the highest demands for precision, performance and operating comfort. The machines are customized: from plasma to oxyfuel cutting, from 2D cutting to bevel cutting. With the special extended version it is possible to cut up to 250 mm with oxyfuel."
Stable and precise cutting result crucial
When selecting the right technology, Faymonville placed an emphasis on process reliability and stability. "The reliability of these machines and the follow-up support (training & support, editor's note) are very important for us, because the smallest incident affects the production time and a prolonged downtime must be avoided at all costs," emphasizes Carsten Faber, "and we know that we can count on the responsiveness of our supplier, which is the most important thing for us."
OVERVIEW OF THE HIGHLIGHTS OF THE PLASMA CUTTING SYSTEMS MG:
Two plasma cutting systems with plasma rotator and oxyfuel torch for sheet metal processing
For cutting, Faymonville relies on the MG series: two 3D plasma cutting machines for processing sheet metal are in operation. One MG has a working area of 30,000 x 3,000 mm, the other 21,000 x 3,000 mm. MicroStep's endless rotating plasma rotator for weld seam preparation up to 50° has been integrated in both cutting systems. The automatic, patented ACTG® calibration unit ensures permanently precise results. A Hypertherm XPR300 is connected to each as plasma power source. Also available are two extended oxyfuel torches on each system for processing higher material thicknesses up to 250 mm.
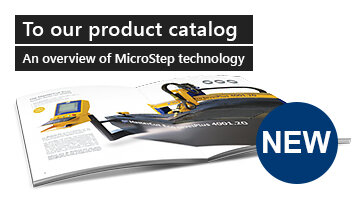
EXPERIENCE OUR SYSTEMS LIVE
in the CompetenceCenter South or North
- All four cutting technologies (laser, plasma, oxyfuel, waterjet)
- Innovative automation systems
- The latest solutions for bending and deburring
- Industry 4.0 demo factory
- Easy to reach: in the south and north of Germany
