
More flexibility is (almost) impossible: EGS uses the entire DRM spectrum for its compressor solutions
Goal accomplished: "Better quality products in less time and at better cost"
Euro Gas Systems, a modern European manufacturer of compressor solutions, invested in a multifunctional DRM machine for cutting sheets, pipes, beams and domes
Published 06.12.2021 | Erich Wörishofer
Company profile:

Euro Gas Systems S.R.L.
Industrial Park 1C
Chirileu 547551
Romania
Euro Gas Systems S.R.L., located in the north of Romania, is an ISO 9001 certified packager of natural gas compressors. EGS management has over 30 years of experience in packaging reciprocating compressors for a wide variety of producers in Europe, the Middle East, Africa, Asia and the CIS countries.
Euro Gas Systems develops and produces versatile compressor solutions. Here in the picture is the Ariel KBK4 two-stage compressor unit. The production of such units is a great challenge. MicroSteps DRM with an enormous processing range is fully used here.
Machine profile:
DRM series- Working area for sheets 6,000 x 2,500 mm
- Cutting and trimming of domes Ø 500 – 2,000 mm
- Cutting of pipes Ø 100 – 2,000 mm and hollow sections up to a lengths of 6,000 mm
- Cutting of U, L IPE, and HEA beams up to HEB 1000 and a length of 12,000 mm
- 3D plasma rotator "pantograph" with tilting up to 120° for weld preparation on domes, beams, pipes, and plates + auto-calibration feature (ACTG®)
- Oxyfuel rotator for weld preparation up to 65° with auto-calibration feature (ACTG®)
- Plasma rotator for weld preparation up to 45° with auto-calibration feature (ACTG®)
- Laser scanner for measuring of the real shape of pipes, profiles, and beams
Located in the heart of Romania’s Transylvanian Basin, the city of Chirileu is home to Euro Gas Systems (EGS), a manufacturer of gas compressor packages. EGS is an ISO 9001 certified packager and official packager/distributor for Ariel, ‘Platinum Solution Provider’ for Waukesha and OEM for Caterpillar and other major equipment brands, providing world-class compression to the European, Middle Eastern, Africa, Asia and CIS markets. With a background of more than 30 years of experience in the field, the company operates three production plants with a total area over 9,000 square meters and a 1,300 sqare meters office space. Here, a comprehensive machine park comes into action including CNC cutting, welding, drilling and rolling machines, a press brake, vertical and horizontal machining centers as well as own dyeing and sandblasting chambers.
Besides packaging of reciprocating gas compressors EGS’s product portfolio also covers gas-to-power solutions for the oil and gas industry, air-cooled heat exchangers (ACHE) and pressure vessels with PED and ASME certifications. Having decades of experience, broad in-house resources, and world-class facilities, the products offered by EGS are tailor made with a wide flexibility of integrating also custom specs. The focus on building up the in-house engineering capabilities and services has also been a driving force for EGS in new machinery acquisitions.
One of our company’s goals is to increase efficiency in all the production processes so that we can build better quality products, in less time and at better cost“ says Roger Wachter, General Manager for EGS, who took the decision to invest into in a multi-functional CNC cutting machine in the course of 2020. The choice fell on MicroStep, as the company was able to offer a machine for processing all required types of semi-products and also proved experience with similar multi-functional cutting solutions. „This investment checked all of the three objectives, making it an easy decision, looking also at the potential ROI,“ states Wachter.
Universal machine for EGS
According to EGS’ technical requirements, a universal and robust CNC cutting center MicroStep DRM has been tailored. The machine consists of three separate zones: a sheet and dome cutting zone, a pipe/closed profile cutting zone and a beam cutting zone. Above each of the zones, a heavy-duty gantry operates equipped with three tool stations: a 3D plasma rotator with tilting up to 120°, an oxyfuel rotator with tilting up to 65° and a 3D laser scanner. The machine combines plasma and oxyfuel bevel cutting with intelligent scanning functions. “With the laser-based scanner, the machine automatically adjusts its cutting path to account for any variation of product shapes due to mill tolerances,“ explains Wachter. “Final cuts are remarkable with clean bevels that require limited further preparation prior to fit up and welding.“
A typical example of the benefits that such a machine brings to producers like EGS is one of the characteristic products: a two-stage compressor unit Ariel KBK4. Its production requires precise cutting with welding preparation on sheets, pipes, domes as well as various types of open profiles.

"On the pressure vessel nozzle cuts we managed to reduce the actual layout/cutting/weld preparation time by at least 70%. Similar results are seen in cutting I beams."
Roger Wachter
General Manager | Euro Gas Systems
Bevel cutting of sheets and domes with plasma and oxyfuel
The sheet and dome cutting zone of the machine consists of a cutting table with work area 6 x 2.5 m that enables plasma cutting of sheets in a thickness range 2 – 80 mm and oxyfuel cutting between 10 – 150 mm. It also allows to place a dome on the table up to a diameter of 2,000 mm and a height of 600 mm which can be cut with both plasma and oxyfuel. Thanks to the 5-axis pantographic bevel head with Hypertherm’s HPR400xD (400A) plasma technology, the machine can cut contours into the entire dome surface and also trim dome edges for weld preparation. After cutting, the domes are welded onto pipes to produce pressure vessels, for example compressor expansion tanks.
Since real domes usually have deviations from the underlying (ideal) shapes of their 3D models used for CAM programming, the key to precise machining is to identify the true shape and dimensions of each dome a machine is going to cut. For this purpose, MicroStep has developed a unique 3D laser scanning process involving point cloud mapping (technology MicroStep mScan) which allows to measure the true shape of a dome and use this measurement for subsequent adjustment of the generated cutting program to follow dome’s surface precisely. To enable this, the scanner is placed in a tiltable rotary holder on a separate tool station with a Z stroke as long as 1.5 m. Besides domes, it is used also for scanning pipes, profiles and beams.
Cutting of pipes up to 2,000 mm in diameter
EGS manufacture their pipes with a diameter of over 900 mm by rolling them from sheets. Pipes produced this way tend to have slight deviations in roundness, which could result in an inaccurate position of the cut contours caused by the rotary positioning of pipe around its longitudinal axis. In any case, the machine can ensure accurate cutting results by scanning the pipes with the laser scanner and subsequently compensating the measured deviations. In addition to plasma, the machine also enables bevel cutting of pipes with oxyfuel.
Beam cutting and deviation compensation
Along the cutting table is a reserved area for cutting beams up to a length of 12 m and web width of 1,000 mm. Beams are placed onto cantilever supports with spikes, under which a suction channel is located. The machine can process a wide range of beam types – U, L, IPE and HEA. The beams are cut by moving the gantry with cutting tool along the statically placed profile, while the 5-axis rotary head with a torch tilt of up to 120° covers the profile surface from three sides and thus ensures not only cutting of holes, but also dividing profiles and cutting contours in its cross section with weld preparation. Real beams can deviate from standard dimensions and from certain lengths are prone to twisting around longitudinal axis. To achieve the required accuracy and avoid deviations, each beam is scanned in the area of the cut before actual cutting.
mCAM also significantly contributes to the overall efficiency of production preparation at EGS. Not only is it importing and processing complex 3D models of parts and assemblies at once and breaking them down automatically to cuttable shapes, it also automatically loads technological parameters from the connected cutting machine to generate dedicated cutting plans. It is especially convenient for the processing of HEA and IPE beams that can have different thicknesses of webs and flanges and thus require adjustment of cutting speed on transitions. Thanks to communication with the control system, mCAM is able to generate cutting plans for a particular semi-product automatically, including cutting speed change when transitioning between different material thicknesses in one beam.
Significantly more speed in production
“The machine allows our team to streamline production time with increased accuracy throughout all stages of the manufacturing process,“ assesses Roger Wachter. “On the pressure vessel nozzle cuts we managed to reduce the actual layout/cutting/weld preparation time by at least 70%. Similar results are seen in cutting I beams for manufacturing of base skids and sub skids (compressor/driver modules). The CAD/CAM software interface between our 3D design department and the cutting center eliminates potential mistakes by removing the need for human interaction between the processes,” adds Wachter.
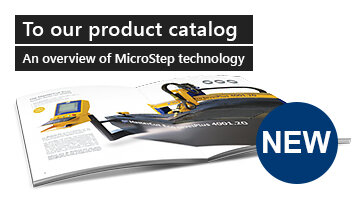
EXPERIENCE OUR SYSTEMS LIVE
in the CompetenceCenter South or North
- All four cutting technologies (laser, plasma, oxyfuel, waterjet)
- Innovative automation systems
- The latest solutions for bending and deburring
- Industry 4.0 demo factory
- Easy to reach: in the south and north of Germany
