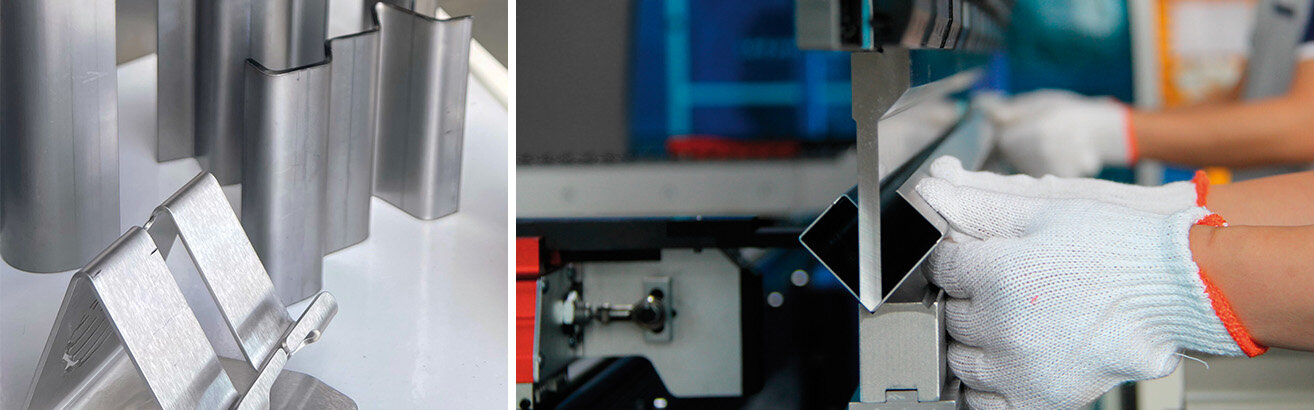
Sheet metal bending | Information on bending technology
The force of a mechanically, hydraulically or electrically driven press brake presses an upper tool into a sheet metal that has been positioned on a lower tool. The force exerted bends the sheet metal into the desired shape.
Sheet metal bending history
The first bending machines were developed in the early 1800s and were powered by steam engines. They were used to bend sheet metal for various purposes, for example in shipbuilding and construction. The demand for sheet metal components was boosted in particular by the industrial revolution. In the early 1900s, the first hydraulic bending machines were developed, which were more powerful than steam-powered press brakes and could therefore bend thicker sheets.
The first CNC (Computer Numerical Control)-controlled press brakes were developed in the late 1970s. Initially, however, they were very expensive and were only used by large manufacturers. Gradually, however, the cost of CNC press brakes has come down considerably, allowing them to be used by a wide range of manufacturers, from small workshops to large companies. In addition, automation in the field of press brakes is progressing steadily and allows, for example, automated material handling to reduce the workload of operating personnel.
Advantages of CNC bending
- Simple operability
- High accuracy and precision
- Fully automatable
- High production speed
- Cost efficient
- Versatile in use
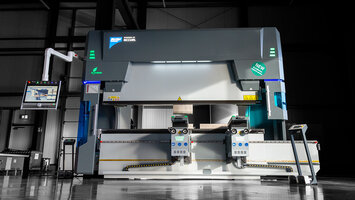
Economical, precise, reliable – a CNC press brake from the EUROMASTER series by MicroStep Industry
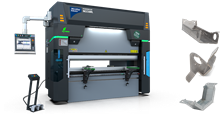
CNC press brakes from MicroStep Industry offer maximum precision and process reliability, are equipped with high-quality components throughout and can be almost completely automated.
Bending types
Press brakes differ depending on the function and the drive power of the machine:
- Pneumatic press brakes: They use compressed air to generate the bending force and are generally used for lighter tasks.
- Mechanical press brakes: These press brakes use a mechanical force to generate energy and apply force to the metal. They are suitable for bending applications with low to medium volumes.
- Electric press brakes: These machines use an electric motor for the drive, which allows for precise control and energy efficiency. Electric press brakes are characterized by low maintenance and quiet operation.
- Hydraulic press brakes: These press brakes use hydraulic fluid to generate power and are capable of exerting high force. They are therefore ideal for bending heavy materials and large material thicknesses.
As a rule, CNC-controlled press brakes are driven by a hydraulic or electric system. Which system is best suited to your requirements can be determined in a needs-based consultation. In addition to the configuration of the drive power, press brakes can also be adapted to individual requirements with various equipment options in order to maximize productivity.
Bending technology and bending processes
In order to bend a sheet precisely with a press brake, it must first be positioned on the machine and aligned with the backgauge. The backgauge ensures precise positioning of the bending line on the sheet during the bending process. The desired bending angle and radius, the position of the backgauge and other parameters are set in the press brake's control system.
A distinction can be made between different processes in the subsequent bending process:
In many cases, the main application of a press brake is air bending (free bending). In this process, the upper tool (punch) presses the workpiece into the opening of the lower tool (die), but not all the way to the bottom of the die. The bending angle is determined by how deep the punch plunges into the die. This allows different angles to be bent without changing tools.
Another bending process is 3-point bending. Here, the punch presses the workpiece through to the bottom of the die. One advantage of this type of bending is the higher precision compared to air bending. However, the process places higher demands on the technology used, in particular the CNC control and the tools, and is therefore more cost-intensive.
A third process is coining. In this process, the material is pressed into the die until it lies against the walls of the die and takes on its angle. A separate set of tools is required for each angle. As the sheet metal is pressed into the die with great pressure from the punch, the pressing force required is around three times that of air bending.
Fields of application for bending
CNC press brakes are versatile and therefore widely used in different industries, including:
- Automotive industry: production of body parts, frames, brackets and other components for cars and trucks
- Aerospace: production of aircraft components such as fuselage and wings
- Electrical industry: production of metal cabinets and housings
- Construction industry: production of metal parts for buildings and other structures
- Manufacturing industry: production of various products, such as household appliances, furniture, medical devices and more
__
FAQ: We answer your questions about bending
What is a press brake?
A press brake is a machine used in the metalworking industry for bending sheet metal. The force of the press lowers an upper tool (punch) onto a sheet of metal that has been positioned on a lower tool (die) to bend it into a predetermined shape. Press brakes come in many different sizes and configurations, from small manual machines to large automated systems. This enables a wide range of possible applications.
What is a CNC press brake?
CNC press brakes bend sheet metal into the desired shape using CNC (Computer Numerical Control) technology. The computer control enables a fast, effective and precise bending process with exact angles and dimensions. A CNC press brake usually works with hydraulic or electric power and is suitable for the production of a small number of sometimes complex parts and components as well as for the production of a large number of identical parts. They are also highly customizable in terms of both the basic configuration and the choice of tools and can therefore process a wide range of material types and thicknesses.
What are the main components of a press brake?
Various components of a press brake must work together to ensure a functioning bending process:
- Machine frame: Structural support of the press brake made of high-strength steel to withstand the forces that occur during the bending process
- Upper beam with upper tool (punch): This hydraulically or electrically driven part is used to exert force on the metal in order to shape it
- Lower beam with lower tool (die): Depending on the opening angle of the die mounted on the lower beam, into which a sheet is pressed along the bending line by the upper tool (punch), different bending angles can be realized
- Backgauge: This device is used to precisely position the sheet metal for bending so that a bending line runs as desired relative to the outer edges or other bending lines.
- CNC control: Bending parameters, e.g. bending angle and position of the backgauge, can be programmed here
Are there differences in the beveling tools?
Bending tools are the punch, which is located on the upper beam of the press brake, and the die, which is located on the lower beam. They are made of high-strength, hardened steel to withstand the force exerted and are not permanently installed in the machine, but can be exchanged for different bending applications. Both the upper and lower tools are available in a wide variety of shapes and sizes. The selection of bending tools is crucial in order to achieve the best possible accuracy and precision. In particular, the type, thickness and length of the metal to be bent as well as the shape, radius and size of the bends must be taken into account. An incorrect, poor quality or incorrectly connected tool can cause damage to the machine or lead to faulty workpieces.
Can all materials be bent with a press brake?
Press brakes can be used to bend a wide range of materials, including steel, stainless steel, aluminum, copper, brass and more. Depending on the material type and thickness, different machine types are recommended and different tools and settings are required. The force that a press brake can apply is referred to as tonnage and varies depending on the machine. Hydraulic press brakes are required for high forces, e.g. for bending steel, while electric press brakes are generally suitable for lower forces, e.g. for bending aluminum.