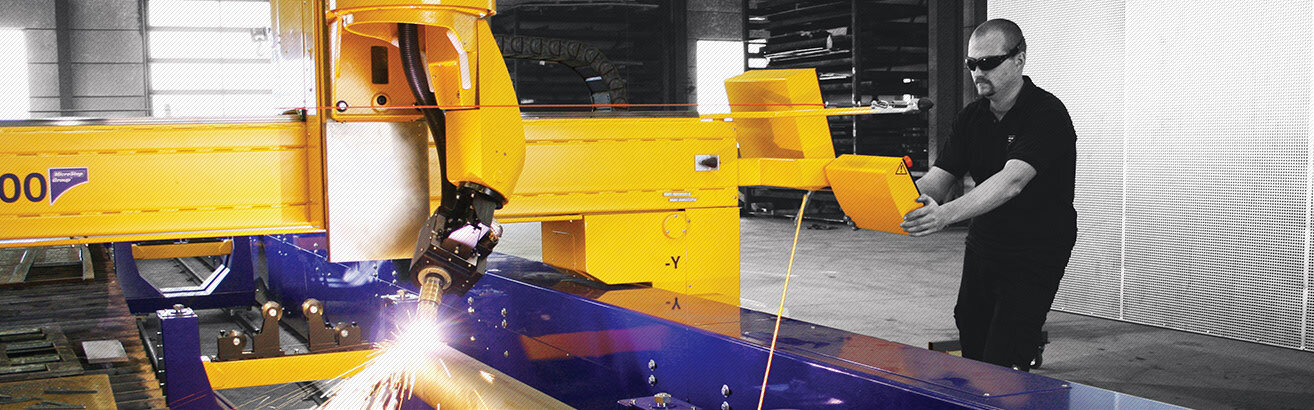
Pipe & profile processing
Pipe processing and profile processing with CNC cutting systems
Pipes and profiles are used to manufacture a wide range of products in industrial production today: From simple spirit levels to nozzles, tubes and containers for apparatus engineering or complete piping systems for ocean-going freighters – sometimes numerous different pipes and profiles are required simultaneously for complex constructions. Basically, two types of machine designs are used for processing pipes and profiles: either systems with a cantilever arm or gantry systems with an integrated pipe shaft.
Cantilever arm
The version with an eccentric cantilever is a pure pipe and profile processing solution. The entire machine concept is designed to clamp, scan, cut and finally unload pipes as quickly and economically as possible. In conjunction with the corresponding automation components, such as an automatic loading unit, the cutting system can be loaded fully automatically with the correct profile from the material store according to the cutting plan – the same applies to the removal and storage of finished components. Thanks to the flexible cantilever design, pipe diameters of up to 3,000 mm can be realized.
Processable profile shapes: Round pipes, square profiles, I, H, T, L, U profiles (also complete separation) and elbow pieces.
Gantry system with integrated pipe shaft
The major advantage of this design is the flexibility to process both pipes and flat sheets. The pipe shaft integrated into the cutting table can be covered with frame elements on MicroStep cutting systems if required and used as a full-surface extracted cutting table. The machine gantry moves into the parking position for loading and unloading the pipes. This allows pipes to be safely placed on the support blocks by crane and clamped in the jaw chuck.
Processable profile shapes: Round pipes, square profiles, I, H, T, L, U profiles (also complete separation) and elbow pieces.
Possible cutting technologies:
- Plasma: Depending on the power source, pipe and profile processing with plasma is suitable for wall thicknesses of 2 to 50 mm and all electrically conductive materials. In this cutting range, plasma impresses with high cutting speeds, economy and a very clean cut quality. In combination with the MicoStep R5 rotator, bevel cuts on the pipe are also possible.
- Oxyfuel: The best solution for extremely thick-walled pipes with wall thicknesses of up to 200 mm is oxyfuel cutting. Despite the relatively low feed rates, oxyfuel technology is very low-wear, cost-effective and also suitable for using the MicroStep R5 rotator.
- Laser: The pipe laser impresses with very high cutting speeds in the thin-walled range from 0.5 to 15 mm. The cuts are very delicate and the heat input into the material is also relatively low.
- Waterjet: This cutting process enables extremely precise cuts to be realized on almost any material – and all without heat input.