
Laserschneiden | Infos zur Lasertechnik
Was ist Laserschneiden?
Das Laserschneiden (engl. Laser cutting) ist ein thermisches Trennverfahren. Mit Hilfe eines Laserstrahls schmilzt oder verdampft das Material, das unmittelbar nach seiner Entstehung mittels eines Gasstroms nach unten weg ausgeblasen wird.
Das Laserschneiden wird in drei verschiedene Varianten unterteilt: Laserstrahlschmelzschneiden, Laserstrahlbrennschneiden und Laserstrahlsublimierschneiden und wird vor allem dort verwendet, wo beispielsweise Metall und Stahl in relativ dünnen Materialstärken mit höchster Präzision und größtmöglicher Bearbeitungsgeschwindigkeit geschnitten werden müssen. Neben den unterschiedlichsten Metallen können aber auch zusätzliche unterschiedliche Materialien wie z.B. Holz oder Kunststoff mit dieser Technologie und mit hoher Schneidgeschwindigkeit bearbeitet werden.
- Was ist Laserschneiden?
- Vorteile Laserschneiden
- Alles auf einen Blick
- Aktuelle News
- Anwendungsbereich
- Pro und Contra Laserschneiden
- Vergleich Festkörperlaser und CO2-Laser
- Vor- und Nachteile des Faserlasers
- Ablauf Laserschneiden
- Schneidbereich
- Bestandteile eines Lasers
- Lasertechnik
- Mit Laser bearbeitete Bauteile
- FAQ
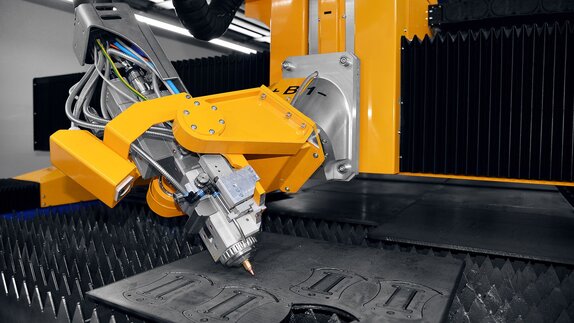
Alles auf einen Blick
- Beim Laserschneiden können Teile verschiedenster Materialien, wie bspw. Metall, Holz oder Gummi mit sehr hoher Präzision zugeschnitten werden.
- Die Laser-Schneidtechnik kommt bisher vorwiegend im kleineren und mittleren Stärkenbereich zum Einsatz – allerdings ermöglicht die kontinuierliche Weiterentwicklung der Lasertechnologie die Bearbeitung immer höherer Materialstärken.
- Es gibt verschiedene Arten von Hochleistungslasern – am häufigsten genutzt werden der CO2-Laser (Gaslaser) und der Faserlaser (Festkörperlaser).
- Entscheidende Vorteile des Faserlasers sind die Einsparung von Kosten für Betrieb und Wartung sowie höchst effektive Laserquellen.
- Der Laser besteht aus drei grundlegenden Teilen: Energiequelle, Lasermedium, Resonator.
- Das Laserschneiden findet in unterschiedlichen Branchen Anwendung, beispielsweise in der Automobilindustrie, im Maschinenbau oder in der Feinmechanik.
Laserschneidanlagen von MicroStep Europa
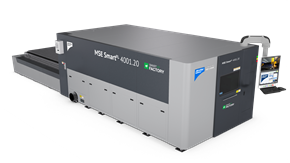
MSE SmartFL
High Power: Der MSE SmartFL ist ein leistungsstarkes und gleichzeitig preiswertes System für qualitativ hochwertiges 2D-Laserschneiden. Die Baureihe kann mit Laserquellen bis zu 60 kW ausgestattet werden und ist bereits heute bestens für die Fertigung der Zukunft gerüstet!
MSE SmartFL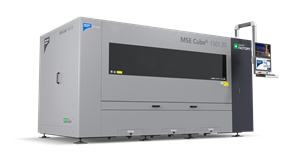
MSE CubeFL
Der MSE CubeFL vereint höchste Präzision und Effizienz bei minimalem Platzbedarf. Die Baureihe kann mit Laserquellen bis zu 12 kW ausgestattet werden und ist die ideale Lösung für das kompakte Laserschneiden.
MSE CubeFL
MSE TubeFL
Qualitativ hochwertiges 2D- und 3D-Laserschneiden von Rohren, Profilen und Trägern. Mit dem MSE TubeFL können feinste Konturen und Durchbrüche sowie exakte Fasenschnitte realisiert werden. Je nach Ausführung verfügt das System dabei über einen extrem hohen Automationsgrad.
MSE TubeFL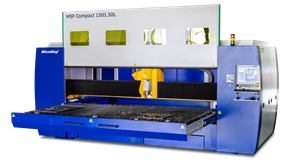
MSF Compact
Der MSF Compact vereint präzises 2D-Laserschneiden mit kompaktem Design. Die Baureihe überzeugt vor allem durch einen geringen Platzbedarf bei gewohnt hoher Schnittqualität der Laserschneidanlage. Ein manuell herausziehbarer Schneidtisch ermöglicht dabei ein einfaches und unkompliziertes Be- und Entladen.
MSF Compact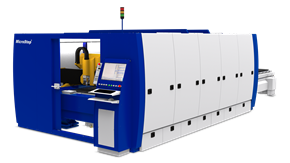
MSF Cut
Zuverlässig und prozesssicher: Das zeichnet die MSF Cut Baureihe aus. Der effiziente Produktionshelfer ist die ideale Lösung für 2D-Standardaufgaben und kann mit Laserquellen von bis zu 15 kW ausgestattet werden.
MSF Cut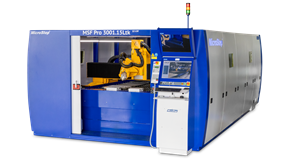
MSF Pro
Highspeed und Flexibilität in 3D: der präzise Allrounder MSF Pro ist Vorreiter bei den Laserschneidmaschinen in Sachen Multifunktionalität. Kein anderes Lasersystem bietet zur Blechbearbeitung ein solches Maß an Fertigungstiefe. Optional lassen sich auch Rohre und Profile schneiden.
MSF Pro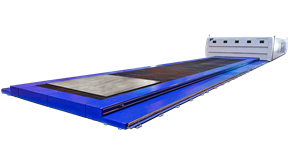
MSF Max
Der MSF Max ist der Gigant unter den Laserschneidanlagen. Entwickelt zur Bearbeitung von großformatigen Blechen für den Schiffsbau ermöglicht er die präzise 3D-Highspeedbearbeitung von Flachmaterial. Dank mitfahrender Sicherheitskabine steht eine Arbeitsfläche für die Lasermaschine von bis zu 50 m Länge und 6 m Breite zur Verfügung.
MSF Max
MSF Pipe
Der Rohr- und Profilspezialist: Optional zu der hochpräzisen 2D- und 3D-Bearbeitung von Rohren und Profilen von bis zu 12 Metern Länge, kann die MSF Pipe um eine Bearbeitung von Blechen erweitert werden.
MSF Pipe
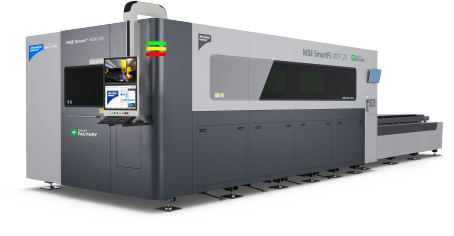
Welche Anwendungsbereiche hat Laserschneiden?
Der aufgrund der stark fokussierten Laserstrahlung und der hohen Verfahrgeschwindigkeit lediglich auf einen eng begrenzten Bereich beschränkte Wärmeeintrag in den Werkstoff führt dazu, dass während des Laserschneidens die thermische Belastung der Bauteile sehr klein ist und somit keine oder nur eine minimale Verformung stattfindet. Das Ergebnis sind Teile mit einer sehr hohen Präzision.
Das Laserstrahlschneiden findet zum einen im Bereich der Automobilindustrie, in der Feinmechanik, der Halbleiterindustrie oder bei den Herstellern von optischen Instrumenten Verwendung. Aber auch im Metallbau und ganz allgemein im Bereich der Lohnfertigung. Eingesetzt wird diese Technik in allen Industriezweigen, die sich mit Metallbearbeitung und ganz allgemein mit Trenntechnik beschäftigen. Die Bandbreite der zu bearbeitenden Werkstoffe reicht von Gummi bis hin zu Diamantgestein. Überwiegend zur Anwendung kommt diese Schneidtechnik bei Stahlblechen aller Sorten und Güten, bei rostfreien Edelstahlblechen und bei Nichteisen-Metallen (NE-Metalle) wie Aluminium und Messing. Geeignet für den Einsatz beim 2D- und 3D-Laserschneiden sind aber auch Materialien wie Titan, Plexi- oder Acrylglas, Holz oder Bronze.
Die Laserschneidtechnik ist prädestiniert für den Einsatz an einer CNC-Schneidanlage. Moderne Laserschneidanlagen vereinen die Vorteile des Lasers mit der Möglichkeit zur multifunktionalen Bearbeitung an einer CNC-Maschine. Heutige Lasertypen bieten eine Vielzahl von Ausstattungsoptionen zur Bearbeitung von Blechen, Rohren und Profilen. Somit ist Schneiden, Bohren, Gewinden, Senken, Markieren oder Fasenschneiden – zum Beispiel zur Schweißnahtvorbereitung – an einer Laserstrahlschneidmaschine möglich. Dank der Faserlasertechnologie ist auch ein Bearbeitungszentrum mit außerordentlicher Schnittfläche zur Blechbearbeitung – also ein Überformat – realisierbar. So ist beispielsweise ein Arbeitsbereich von bis zu 50 m Länge und 6 m Breite über eine mitfahrende Sicherheitskabine möglich. Bei modernen Maschinen sind zudem bereits etliche Prozesse automatisiert: die Einstellung von Fokuslage und Fokusdurchmesser, die Abstandskalibrierung und Reinigung der Schneiddüse oder auch der Düsenwechsel. Darüberhinaus gibt es noch viele weitere Optionen, um den Laserzuschnitt zu automatisieren. Sei es durch integrierte Materialhandlingsysteme zur Be- und Entladung des Werkstücks (Blech, Rohr, Profil), Sortiertechnologien für geschnittene Laserteile oder eingebundene Lagersysteme, um eine möglichst mannlose Fertigung zu ermöglichen.
Pro Laserschneiden
- Hohe Präzision und Qualität beim Schneiden von unterschiedlichen Materialien
- Schneiden von kleinen Löchern, spitzen Winkeln und komplexen Konturen
- Hohe Bearbeitungsgeschwindigkeit im Dünnblechbereich ermöglicht die Bearbeitung großer Stückzahlen
- Sehr gute Automatisierbarkeit
- Äußerst geringer Wärmeeintrag, nahezu kein Verzug der Werkstücke
- Sehr geringe Schnittfugenbreite
Contra Laserschneiden
- Nicht alle Materialien sind mit Laser schneidbar
- Materialgüten und Oberflächenbeschaffenheiten können Einfluss auf das Schneidergebnis haben
- Ungeeignet, wenn keine thermische Einwirkung auf das Material erfolgen darf
- Je nach Maschinenauslegung relativ hohe Anschaffungskosten
Vergleich Festkörperlaser und CO2-Laser
Es gibt verschiedene Arten von Hochleistungslasern, die beim Laserstrahlschneiden zum Einsatz kommen. Am häufigsten genutzt werden der CO2-Laser (Gaslaser) und der Faserlaser (Festkörperlaser). Der CO2-Laser war bis vor wenigen Jahren die am Meisten verwendete Laserstrahlquelle innerhalb des Laserschneidens und wurde viele Jahrzehnte erfolgreich eingesetzt. Mehr und mehr abgelöst wird der Gaslaser seit einigen Jahren durch den Faserlaser. Diese spezielle Form des Festkörperlasers überzeugt vor allem durch eine im Vergleich zum bekannten Schneidsystem hohe Wirtschaftlichkeit bei gleichbleibend guten Schneidergebnissen.
Faserlaser haben im Vergleich zu CO2-Lasern (Kohlenstoffdioxidlaser) deutlich geringere Betriebs- und Wartungskosten. Dank modernster und ausgefeilter Technologien sind sie auch hinsichtlich Präzision bei unterschiedlichen Blechstärken verschiedenster Werkstücke mindestens ebenbürtig zum bisher bekannteren CO2-Laser. Im Vergleich zu den CO2-Lasern punkten Festkörper-Faserlaser mit einer Reihe von Stärken – allen voran mit dem Kostenfaktor und der einfacheren Strahlführung innerhalb der Bearbeitungsmaschine. Dank dieser Eigenschaften hat sich der Faserlaser von einer attraktiven Alternative zum dominierenden Laser im Laserschneidmarkt entwickelt.
CO2-Laser
Die CO2-Laser zählen zur Gruppe der Gaslaser und werden auch Kohlendioxidlaser oder Kohlenstoffdioxidlaser genannt. Sie basieren auf einem Kohlendioxid-Gasgemisch (N2, He und CO2), welches elektrisch angeregt wird. CO2-Laser punkten mit einer sehr guten Schnittqualität und werden vorwiegend bei metallischem Werkstoff (Stahl, Aluminium, Edelstahl) aber auch bei nichtmetallischen Werkstoffen wie Holz, Textilien, Kunststoffe, Folien, Acryl, Glas, Papier und Leder eingesetzt. Der CO2-Laser ist ein seit Jahrzehnten bewährter Lasertyp, der bei unterschiedlichsten Materialdicken hohe Qualität ermöglicht. Nachteil ist der zum Faserlaser vergleichsweise hohe Einsatz für Betriebs- und Wartungskosten sowie die Kosten für die benötigten Lasergase. Der Wirkungsgrad liegt bei rund 10 Prozent.
Faserlaser
Der Faserlaser, der eine spezielle Form des Festkörperlasers darstellt, ist mittlerweile der dominierende Laser auf dem Laserschneidmarkt. Er punktet mit hoher Wirtschaftlichkeit, geringen Betriebskosten und langer Lebensdauer der für den Laserprozess notwendigen Komponenten. Dank einer zehnfach kürzeren Strahlwellenlänge im Gegensatz zum CO2-Laser eignet sich der Faserlaser auch zum Durchtrennen von ansonsten für den CO2-Laser schwer oder gar nicht schneidbare Werkstoffe, insbesondere von Nichteisen-Metallen (NE-Metalle wie z.B. Kupfer und Messing). Die Laserquellen sind dabei höchst effektiv und verbrauchen bei gleicher Leistung deutlich weniger Eingangsstrom. Der sogenannte Steckdosenwirkungsgrad beträgt beim Faserlaser circa 40 Prozent.
Nd:YAG-Laser
Nd:YAG-Laser zählen wie die Faserlaser zu den Festkörperlasern und sind auch unter den Bezeichnungen Kristalllaser oder Vanadat-Laser bekannt. Nd:YAG-Laser ist die Abkürzung für Neodym-dotierter Yttrium-Aluminium-Granat-Laser. Als Wirtskristall wird ein YAG-Kristall eingesetzt. Diese Technologie wird weniger beim Laserstrahlschneiden verwendet, sondern vielmehr bei der Gravur, beim Schweißen und bei Mikrobohrungen. Metalle, Metalle mit Beschichtung und Kunststoffe werden mit diesem Festkörperlaser bearbeitet. Im Gegensatz zum Faserlaser hat diese Technik allerdings einen hohen Verschleiß an Pumpdioden bzw. Pumplampen. Zudem ist die Lebensdauer des Neodym-dotierten YAG-Kristalls im Gegensatz zum Faserlaser geringer.
Kann ich Ihnen helfen? Ich stehe Ihnen bei Fragen gerne persönlich zur Seite:
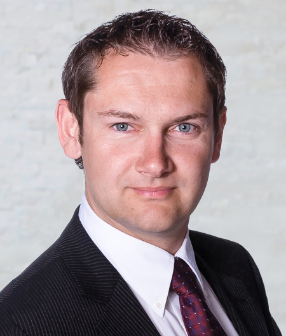
Marco Große-Schütte
Leitung Vertrieb
Telefon: +49 8247 96294 88
E-Mail: marco.grosse-schuette@microstep.com
Welche Vor- und Nachteile hat der Faserlaser?
Der entscheidende Vorteil der Faserlaser liegt auf der Hand: Mit diesem Festkörperlaser können über die Hälfte der Kosten für Betrieb und Wartung der CNC-Laserschneidanlage eingespart werden. Diese Tatsache ist natürlich maßgeblich für die steigende Popularität dieser Technologie. Nicht nur, dass bei dieser Technik keine Gase für Strahlgänge und Strahlerzeugung (bei schnellgeströmten Systemen) notwendig sind, auch die Laserqellen sind höchst effektiv: die Nennleistung eines 4 kW-Faserlasers (mit einer Kühlvorrichtung) liegt etwa bei 14 kW im Vergleich zu 57 kW Laserleistung für einen 4 kW-CO2-Laser. Auch etliche Wartungskosten eines Kohlenstoffdioxidlasers entfallen: die Kosten, die vom Lebenszyklus der Entladungsröhren abhängen oder von der Turbine im Gaskreislauf der Lasergase oder der Vakuumpumpe. Diese machen einen enormen Teil der vergleichsweise hohen Wartungskosten beim CO2-Laser aus.
Es gibt aber noch weitere physikalische Eigenschaften, die dem Faserlaser zum Vorteil gereichen: dank einer zehnfach kürzeren Strahlwellenlänge können Faserlaser einen kleineren Strahldurchmesser (d.h. eine höhere Energiedichte) im Fokuspunkt des Schneidkopfs erreichen – damit kann dünnes Material schneller geschnitten werden als mit dem CO2-Laser. Je dicker das Material, desto mehr kann diese Eigenschaft ein Nachteil werden, da aufgrund der sehr dünnen Schnittfuge die Gefahr einer Schnittfugen-Verfüllung mit dem Austragsmaterial (Schlacke) besteht. Entsprechend ausgelegte optische Systeme und Schneidköpfe sind mittlerweile in der Lage diesen Nachteil fast vollständig zu beseitigen.
Es ist notwendig, einen größeren Fokusdurchmesser zum Durchtrennen von stärkeren Materialen zu haben. Im Interesse des industriellen Einsatzes sollte der Laserschneidkopf den Fokus automatisch ändern können (Änderungen der Fokuslage zum Material aber auch Änderungen des Fokusdurchmessers). Und das ohne den Eingriff durch Bedienpersonal, z. B. durch manuelle Schneidlinsenwechsel oder manuelle Fokuslagenveränderungen. Um die vielseitigen Anforderungen des Marktes erfüllen zu können – das heißt, das Schneiden über den gesamten Materialstärkenbereich zu ermöglichen – benutzt MicroStep passgenau auf die Anforderungen der Kunden Laserschneidköpfe von führenden Herstellern wie Highyag, Precitec und Thermacut für maximale Produktivität beim 2D-Laserschneiden und Fasenschneiden von Blechen, Rohren oder Profilen. Als Laserstrahlquelle verwendet MicroStep Modelle von innovativen Produzenten wie IPG Photonics und nLight. Durch die mögliche vollautomatische Steuerung von Fokusposition und Fokusdurchmesser in Kombination mit schnellen Fokusbewegungen auf dem Werkstoff können abhängig von der Laserquelle Materialien bis 50 mm Stärke und deutlich mehr mit einem einzigen Faserlaser bearbeitet werden. Die Schneidköpfe sind frei von Schneidlinsenwechseln – lediglich die Reinigung und der Austausch des Schutzglases gehört zu den Aufgaben des Betreibers.
Die Qualität der Faserlaser-Technologie und mögliche Einsatzbereiche haben sich in den vergangenen Jahren erheblich verbessert und erweitert. Moderne Faserlaser können abhängig von Laserleistung und Werkstoff heute Materialien bis 50 mm Dicke und weit darüberhinaus bearbeiten. Beispielsweise ermöglicht ein 20 kW Laser den präzisen Zuschnitt von Baustahl mit mehr als 40 mm, Edelstahl bis 40 mm, Aluminium bis 40 mm, Messing bis 25 mm und Kupfer bis 15 mm schneiden. Die verfügbaren Laserleistungen wachsen aber konstant weiter.
Wie sieht der Ablauf beim Laserschneiden aus?
- Fokussierung des Laserstrahl mit Hilfe optischer Elemente innerhalb des Schneidkopfs
- Einstechprozess: Punktförmige Durchdringung des zu schneidenden Materials
- Start des Schneidprozesses: Absorbierung des Strahls an der Schneidfront, wodurch eine Schmelze erzeugt wird
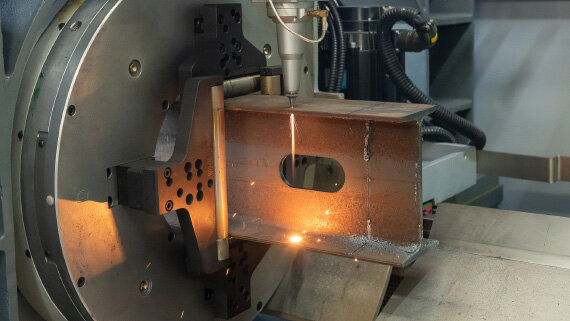
Schneidbereich
Die Laserschneidtechnik erfuhr in den vergangenen Jahren eine enorme Entwicklung. Nach wie vor kommt sie vorwiegend im kleineren und mittleren Stärkenbereich zum Einsatz. Der Schneidbereich beim modernen 2D- und 3D-Laserschneiden liegt je nach Werkstoff und Leistung der Laserstrahlquelle bei optimalen Umgebungsvariablen ab 0,5 bis 50 mm und deutlich mehr. Es gibt verschiedene Parameter, die die Qualität der geschnittenen Laserteile moderner Laserschneidsysteme beeinflussen. Dazu zählen die Fokuslage, die Vorschubgeschwindigkeit, die Laserleistung oder auch der Druck des eingesetzten Schneidgases und die eingesetzte Schneiddüse. Eine Gratbildung an Laserteilen kennt man zumeist nur vom Hochdruckschneiden bestimmter Materialien mit Stickstoff. Diese Gratbildung lässt sich durch verschiedene Parameter beeinflussen und / oder eliminieren. Bei entsprechender Gratbildung (Grat wird auch Bart genannt) muss ein weiterer Bearbeitungsschritt erfolgen – die Entgratung: je nach Gratstärke mittels einer eigenen Maschine.
Welche Bestandteile hat ein Laser?
Ein Laser besteht aus drei grundlegenden Teilen:
- Energiequelle
- Lasermedium
- Resonator
Die Energiequelle, auch als Pumpe oder Pumpquelle bezeichnet, hat die Aufgabe Energie in das System zu "pumpen". Dadurch wird eine Besetzungsinversion erzeugt. Die Quelle kann elektrisch, aber auch Lichteinstrahlung, Wärme oder sogar ein anderer Laser sein. Es muss genügend Energie in das Lasermedium übertragen werden, um eine Besetzungsinversion zu erreichen – das bedeutet, dass die Anzahl der Teilchen im angeregten Zustand höher sein muss als die Anzahl der Teilchen im Grundzustand. Das Licht des Lasers entsteht durch spontane Emission im angeregten Lasermedium und wird durch stimulierte Emission verstärkt. Der Resonator besteht zumeist aus zwei gekrümmten Spiegeln, von denen einer teilweise transparent ist. Strahlung, die aus der spontanen Emission stammt und die richtige Wellenlänge, Phase und Richtung hat, wird zwischen ihnen hin- und her reflektiert. Ein Teil der Strahlung entweicht als Laserstrahl durch den teildurchlässigen Spiegel und der andere Teil wird zur weiteren Verstärkung zurückreflektiert.
Schematische Darstellung vom Laserschneiden
Lasertechnik
Beim CNC-Laserschneiden wird der Laserstrahl mit Hilfe optischer Elemente, die sich innerhalb eines Schneidkopfs befinden, fokussiert. Der Laserstrahl wird an der Schneidfront absorbiert und erzeugt dort eine Schmelze und / oder Metalldampf, der unmittelbar nach seiner Entstehung mittels eines Gasstroms nach unten ausgeblasen wird. Für den Laserzuschnitt ist zumeist ein Prozessgas notwendig. Je nach Schneidverfahren kommen dabei als Schneidgas Sauerstoff, Stickstoff oder Luft zum Einsatz. Zurück bleibt ein Schnittspalt (auch Schneidspalt genannt), der je nach eingesetztem Laserschneidverfahren, Materialdicke und je nach Auslegung des optischen Systems unterschiedliche Breiten annehmen kann. Übliche Werte liegen hierbei zwischen 0,1 und 2 mm.
Welche Bauteile kann man mit einem Laser bearbeiten? Hier einige Beispiele:
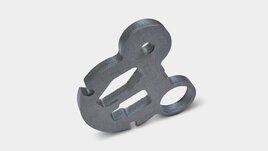
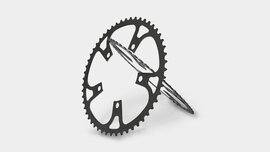
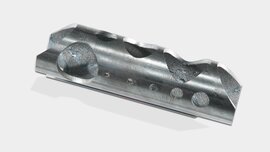
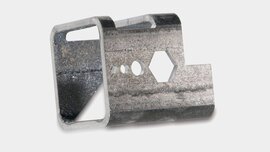
Das könnte Sie auch interessieren:
ERLEBEN SIE UNSERE ANLAGEN LIVE
im CompetenceCenter Süd oder Nord
- Alle vier Schneidtechnologien (Laser, Plasma, Autogen, Wasserstrahl)
- Innovative Automationssysteme
- Neuste Lösungen zum Biegen und Entgraten
- Industrie 4.0 Demofabrik
- Gut zu erreichen: im Süden und Norden Deutschlands
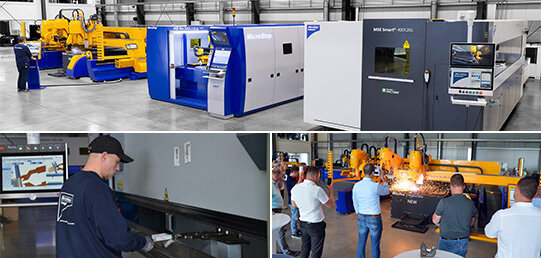
FAQ: Wir beantworten Ihre Fragen zum Laserschneiden
Welche Vorteile hat Laserschneiden gegenüber Plasmaschneiden?
Mit Laser können dünne Materialien wesentlich schneller und mit viel höherer Präzision geschnitten werden, als dies mit Plasma möglich ist. Schnitte mittels Laser sind generell nahezu senkrecht und haben eine gegenüber Plasma wesentlich geringere Wärmeeinflusszone. Scharfe Ecken, spitze Winkel und komplexe Konturen sind ebenso schneidbar wie Löcher oder Innenkonturen mit einem Verhältnis von weit kleiner 1 (Lochdurchmesser: Materialstärke).
Aus welchen Hauptbestandteilen besteht eine Faserlaserschneidanlage?
Die Hauptkomponenten einer Faserlaserschneidanlage sind:
- Portalanlage mit mindestens 3 gesteuerten Achsen (xyz)
- Laserstrahlquelle mit Strahlführung (Bearbeitungsfaser)
- Laserschneidkopf
- Absaugung mit Filtertechnik
- geeignete Sicherheitseinrichtungen (Sicherheitskabine, Schutzschalter etc.)
- Gase für den Schneidprozess (meist N2, O2 oder Luft)
Welche Geometrien und Konturen können beim Laserschneiden geschnitten werden?
Bei den möglichen Geometrien sind beim Laserschneiden nahezu keine Grenzen vorhanden. So können kleine Löcher, schmale Stege, spitzwinklige Geometrien, gerundete oder geschwungene Konturen mit immer nahezu perfekten rechtwinkligen Schnittkanten geschnitten werden. Begrenzender Faktor ist die optische Auslegung der Anlage, die Anlage selbst, sowie das verwendete Laserschneidverfahren.
Welche anderen Schneidverfahren kann man mit Laserstrahlschneiden kombinieren?
Prinzipiell sind Kombinationen mit allen CNC-steuerbaren Schneidverfahren denkbar (Plasmaschneiden, Brennschneiden, Wasserstrahlschneiden), jedoch gibt es nur wenige Kombinationen, die industriell auch umgesetzt wurden. Die Ursache hierzu liegt meist in den grundsätzlichen Eigenschaften der jeweiligen Schneidverfahren. So benötigt eine Wasserstrahlschneidanlage ein Wasserbecken, was bei einer Laserschneidanlage störend ist usw. Die Verwendung eines Wassernebels beim Laserschneiden ist hingegen eine bekannte Möglichkeit, um das Material während des Schneidprozesses zu kühlen.
Welche Materialien und Materialstärken eignen sich für das Laserschneiden?
In der Metallindustrie wird heute eine große Bandbreite an unterschiedlichsten Werkstoffen (Baustahl, Edelstahl, Aluminium, hochlegierte Stähle, Messing, Kupfer u.a.) geschnitten. Durch den Einsatz von Strahlquellen mit immer höheren Laserleistungen ist es möglich immer noch höhere Blechdicken zu schneiden. Mit High-Power-Laserquellen lassen sich somit auch 50 mm und mehr durchtrennen. Das Hauptanwendungsgebiet für Laserschneidanlagen liegt dabei in einem Materialstärkenbereich von 1 mm bis 25 mm.
Welche Schnittbreiten sind beim Laserschneiden möglich?
Die Schnittbreite bzw. der erreichbare Schnittspalt hängt von der Auslegung des optischen Systems und vom verwendeten Laserschneidverfahren ab (Laserstrahlschmelzschneiden, Laserstrahlbrennschneiden und Laserstrahlsublimierschneiden). Beim industriellen Schneiden von metallischen Blechen hat man meist Schnittspalte von etwa 0,1 mm bis 2 mm.
Welche Schnittgeschwindigkeiten kann ich beim Laserschneiden erzielen?
Die erreichbaren Schneidgeschwindigkeiten beim Laserstrahlschneiden sind im Wesentlichen abhängig von der verwendeten Laserleistung und dem verwendeten Schneidverfahren. Generell gilt: Je dicker das zu schneidende Material wird, desto geringer ist die maximal zu erreichende Schneidgeschwindigkeit. Im Dünnblechbereich (1 mm) sind mit den heute zur Verfügung stehenden Laserschneidanlagen Geschwindigkeiten bis etwa 100 m/min (Laserstrahlschmelzschneiden) möglich. Bei 20 mm ist die Geschwindigkeit mit etwa 1 m/min (Laserstrahlbrennschneiden) deutlich geringer.
Wie stark (in kW) muss ein Laser sein, um Metall zu schneiden?
Bei einer entsprechenden Auslegung des Laserschneidsystems kann man bereits mit weit weniger als 100 W dünne metallische Materialien schneiden. Maschinen, die heute in der Industrie zum Schneiden von Metallblechen eingesetzt werden, sind im Durchschnitt mit Strahlquellen ausgestattet, die eine Laserleistung zwischen 1 und 6 kW haben. Die maximale Laserleistung, die derzeit zum Schneiden eingesetzt wird, liegt bei etwa 20 kW.
Welche Materialien sind ungeeignet für das Laserschneiden?
Prinzipiell ungeeignet zum Schneiden sind Materialien, deren Absorptionsverhalten für die jeweilige Wellenlänge des Lasers zu gering ist. So kann man mit CO2-Lasern Holz und Plexiglas schneiden und mit Faserlasern nicht, auf der anderen Seite ist es mit Faserlasern möglich Kupfer und Messing zu schneiden, was mit CO2-Lasern nicht oder nur schwer möglich ist. Ebenfalls ungeeignet zum Laserschneiden sind Materialien bei denen während des Laserschneidens giftige Stäube und Gase entstehen.
Was gibt es beim Laserschneiden von Stahl zu beachten?
Das Schneidergebnis an einer Laseranlage hängt im großen Maße von den Werkstoffeigenschaften des Stahls ab. Wesentlichen Einfluss auf die Schnittqualität haben dabei materialspezifische Eigenschaften wie: Legierungselemente (Kohlenstoff, Zink, Magnesium, Nickel, Silizium und Chrom), Gefügestruktur (Körnigkeit des Gefüges), Materialoberfläche (z.B. geölt, gebeizt, Zunderschicht), Oberflächenbehandlung (Folie, Schichten aus Zink, Lack oder Primer). Die speziellen Werkstoffeigenschaften des jeweiligen Stahls können dabei einen positiven aber auch einen negativen Einfluss auf das Schneidergebnis und somit auf die Schnittkante haben.
Was ist der Unterschied von autogenen Brennschneiden zum Laserbrennschneiden?
Beim Laserbrennschneiden ist die Wärmeeinflusszone an der Schnittkante deutlich kleiner und somit ist auch eine Gefügeänderung im Schnittkantenbereich wesentlich geringer. Je nach geschnittener Materialstärke liegt dieser Bereich bei einigen Zehnteln. Ein Materialverzug durch den Schneidprozess kann beim Laser fast vollständig ausgeschlossen werden. Die Schnittkante ist beim Laserbrennschneiden gratfrei und senkrecht, es kann nahezu jede beliebige Kontur konturgetreu (ohne Verrundungen) geschnitten werden. Aufgrund der Tatsache, dass immer größere Laserleistungen beim Laserbrennschneiden zum Einsatz kommen, verschiebt sich auch die Grenze der Materialstärke bis zu der Laserbrennschneiden üblicherweise eingesetzt wird. Waren es bisher 30 mm, so sind heute durchaus Materialstärken von 40 mm oder 50 mm möglich. Autogenes Brennschneiden wird ab einer Materialdicke von 30 mm eingesetzt.