
Plasmaschneiden | Infos zur Plasmatechnik
Ein Plasmaschneider erzeugt einen Lichtbogen zwischen einer Elektrode und dem Werkstück. Der Plasmabogen schmilzt das Metall und das Plasmagas entfernt die geschmolzenen Materialien.
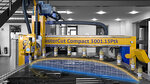
Die Funktion „Smart Z Movement“ schöpft das volle Potential Ihres Schneidsystems während des Schneidvorgangs aus und beschleunigt Ihre Produktion – auch nachträglich installierbar
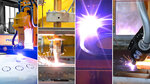
MicroStep hat eine Reihe von Technologien entwickelt, die es Kunden erlauben bei der Bearbeitung von Blechen, Rohren, Profilen oder Behälterböden noch effizientere und hochwertigere Ergebnisse zu erzielen.
Effizienteste Schnitte beim Plasmaschneiden
Mit der Plasmatechnologie können alle leitfähigen Materialien wie Baustahl, Edelstahl und Aluminium im mittleren Materialstärkebereich bearbeitet werden. Vorzüge moderner Plasmasysteme sind qualitativ hochwertige Schnittergebnisse, hohe Schneidgeschwindigkeiten, eine lediglich geringe Wärmeeinflusszone sowie das im Vergleich zu anderen Schneidtechniken konkurrenzlos günstige Kosten-Nutzen-Verhältnis. Systematisch gehört das Plasmaschneiden zu den thermischen Trennverfahren. Es wurde ursprünglich zum Trennen von Metallen, die durch ihre chemische Zusammensetzung nicht per Brennschneiden getrennt werden können, wie z.B. Aluminium oder Kupfer und deren Legierungen, hochlegierte Stähle, aber auch Hartmetalle, entwickelt. In der Industrie sind Plasmaschneidanlagen auch im Baustahlbereich aufgrund ihrer zahlreichen Vorteile gegenüber alternativer Schneidverfahren nicht mehr wegzudenken.
Vorteile Plasmaschneiden
- Hohe Schnittgeschwindigkeiten
- Qualitativ hochwertige Schnittergebnisse
- Günstige Schnittmeterkosten
- Schneiden aller elektrisch leitfähigen Materialien
- Vielseitig einsetzbar

CNC-Plasmaschneidanlagen überzeugen mit wirtschaftlichen und präzisen Schnitten und sind vor allem bei mittleren Materialstärken konkurrenzlos. Moderne Plasmaschneidmaschinen vereinen Effizienz, dauerhafte Leistungsfähigkeit und Multifunktionalität.
Kann ich Ihnen helfen? Ich stehe Ihnen bei Fragen gerne persönlich zur Seite:
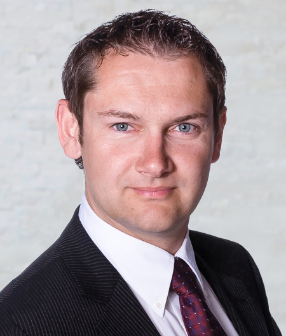
Marco Große-Schütte
Leitung Vertrieb
Telefon: +49 8247 96294 88
E-Mail: marco.grosse-schuette@microstep.com
Plasmatechnik
Ein Plasmaschneider erzeugt einen Lichtbogen zwischen einer Elektrode und dem Werkstück. Plasma wird auch als vierter Aggregatszustand bezeichnet. Es wird erzeugt, in dem elektrisch leitfähiges Gas durch eine Energiezufuhr (Hochspannung) ionisiert wird. Durch die hohe Energiedichte des dabei entstehenden Lichtbogens, der bis zu 30.000 Grad Kelvin erreicht, schmilzt das Metall und wird durch einen Gasstrahl ausgeblasen, wodurch die Schnittfuge entsteht.
Der Schneidprozess wird durch einen sogenannten Pilotlichtbogen, der per Zuführung eines Zündgases zwischen Elektrode und Düse durch Hochfrequenzspannung gezündet wird, ausgelöst (nicht übertragbarer Lichtbogen). Dieser relativ energiearme Pilotlichtbogen ionisiert die Strecke zwischen Elektrode und Anode (Werkstück). Das Plasmagas wird zugeschaltet, sobald der Pilotlichtbogen Kontakt mit dem Werkstück erhält. So entsteht der Hauptlichtbogen bei gleichzeitig automatischer Erhöhung des Stroms (übertragender Lichtbogen). Der Werkstoff wird durch die thermische Energie des Lichtbogens aufgeschmolzen und mit Hilfe der kinetischen Energie des Schneidgases aus der Fuge getrieben.
Der zu schneidende Werkstoff muss beim Plasmaschneiden elektrisch leitfähig sein, da das Werkstück ein Teil des Stromkreises ist (Anode). Die Erdung sollte daher möglichst gleichmäßig sein. Und damit immer optimale Schnittergebnisse erzielt werden können, ändern sich in Abhängigkeit des Materials die Art der Verschleißteile und Plasmagase.
Elektrode und Plasmadüse sind beim Plasmaschneiden hohen Strömen und damit auch hohen Belastungen ausgesetzt – es handelt sich dabei also um Bauteile mit begrenzter Lebensdauer. Die Standzeit der Elektrode wird wesentlich durch die Höhe des Schneidstroms, die Anzahl der Zündungen und die Art des Plasmagases bestimmt. Darüber hinaus spielen das Gas- und Strommanagement am Schnittanfang und -ende sowie die Wärmeabfuhr von der Elektrode eine entscheidende Rolle. Wesentliche Einflussfaktoren der Düsenstandzeit sind:
- Durchmesser, Masse und Wärmeleitfähigkeit der Düse
- Verwendete Leistung (Strom x Spannung)
- Einschaltdauer des Lichtbogens
- Anzahl der Zündungen
- Lochstechablauf
- Idealer Abstand von Brenner zum Werkstück (intelligente Höhensteuerung)
- Reinheit der Schneid- und Wirbelgase: das Gas "Luft" muss trocken, öl- und partikelfrei sein
- Intensität der Kühlung
- Verwendung von geprüften Original-Verschleißteilen
Per Hand oder automatisiert
Man unterscheidet zwischen Hand-Plasmaschneidern oder dem automatisierten Plasmaschneiden mit einer CNC-Maschine oder einem Roboter.
Hand-Plasmaschneider (auch manuelle Plasmaschneider genannt) werden vor allem dort eingesetzt, wo es weniger auf Präzision, Genauigkeit und Reproduzierbarkeit ankommt, sondern vielmehr darum geht, einen schnellen Trennschnitt durchzuführen. Eingesetzt werden Hand-Plasmaschneider daher nicht nur in der metallverarbeitenden Industrie, sondern beispielsweise kommt die mobile Variante des Plasmaschneiders häufig auch bei Bergungsarbeiten von THW oder Feuerwehr zum Einsatz.
Plasmaschneidmaschinen werden am häufigsten in der metallverarbeitenden Industrie eingesetzt. Sie punkten im CNC-geführten 2D-Schneidbereich bei dünnen und mittleren Blechstärken mit sehr guter Schnittqualität und sehr hohen Schneidgeschwindigkeiten bei vergleichsweise günstigen Schnittmeterkosten. Auch im 3D-Bereich zeigen moderne CNC-Maschinen dank ausgefeilter Drehaggregate zum Fasenschneiden ihre Stärke: Einer äußerst präzisen Schweißnahtvorbereitung mit Fasenwinkeln bis zu 50° steht heutzutage nichts mehr im Wege.
Durch optionale Ergänzungen können moderne Schneidanlagen nicht nur zur Bearbeitung von Blechen, sondern zum Beispiel auch zur Bearbeitung von Rohren, Profilen und Behälterböden verwendet werden. An multifunktionalen Plasmaschneidmaschinen gibt es darüber hinaus weitere Optionen zur Bearbeitung der Materialien: Die Anlagen können mit Modulen ausgerüstet werden, um Bohren, Senken, Gewinden, Markieren, Körnen und Beschriften zu ermöglichen. Zudem kann die Plasmatechnik kombiniert werden mit Autogenschneiden bzw. Brennschneiden, mit Laserschneiden oder mit Wasserstrahlschneiden.
Roboter-Schneidanlagen
Roboter gelten weithin als unverzichtbar, wenn es um das Anarbeiten nachträglicher Schweißnahtvorbereitungen an bereits geschnittene Bauteile geht. Allerdings gibt es mittlerweile eine ungleich effizientere Alternative, die diese vermeintliche Gewissheit gewaltig ins Wanken bringt: Das neue Verfahren heißt ABP® - Additional Beveling Process – und ermöglicht äußerst präzises nachträgliches Anfasen auf Portalschneidanlagen.
Schneidbereich
Der typische Schneidbereich beim modernen Plasmaschneiden liegt zwischen 1 mm und 50 mm – hier werden qualitativ sehr gute und wirtschaftlich äußerst effiziente Schneidergebnisse erreicht. Für höhere Materialstärken werden CNC-Schneidanlagen mit Plasmagas in der Regel mit Technologien zum Brennschneiden kombiniert. Folgende Materialien werden üblicherweise unter anderem mit der Plasmaschneidtechnologie bearbeitet: Baustahl (Feinkornstahl, Hardox), Edelstahl (V2A), Chrom-Nickel-Stahl (V4A), Aluminium, Kupfer, Messing, Titan, Panzerstahl.
Anwendungsbereich vom Plasmaschneiden
Das Schneiden mit Plasma findet in den unterschiedlichsten Branchen Anwendung: Zum Beispiel werden Plasmaschneidanlagen im Metallzuschnitt (Lohnschneiden oder Lohnfertigung), im Maschinenbau, beim Anlagen- und Behälterbau, beim Schiffsbau, im Lüftungsbau, im Rohrleitungsbau, beim Prototypenbau oder beim Fahrzeugbau eingesetzt. Also in all denjenigen Industriezweigen, die sich mit Metallverarbeitung und Trennverfahren beschäftigen.
ERLEBEN SIE UNSERE ANLAGEN LIVE
im CompetenceCenter Süd oder Nord
- Alle vier Schneidtechnologien (Laser, Plasma, Autogen, Wasserstrahl)
- Innovative Automationssysteme
- Neuste Lösungen zum Biegen und Entgraten
- Industrie 4.0 Demofabrik
- Gut zu erreichen: im Süden und Norden Deutschlands
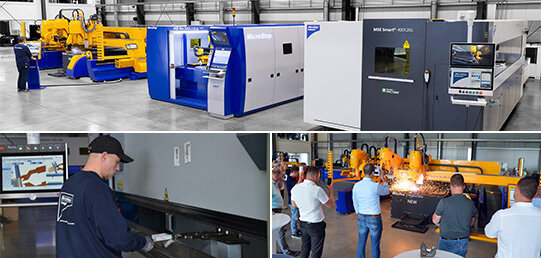
FAQ: Wir beantworten Ihre Fragen zum Plasmaschneiden
Was ist ein CNC-Plasmaschneider?
Mit der Plasmatechnologie können alle leitfähigen Materialien wie Baustahl, Edelstahl und Aluminium im mittleren Materialstärkebereich effizient bearbeitet werden. Ein CNC-Plasmaschneidanlage – auch Plasmabrenner genannt – ist ein präzise CNC-gesteuertes Tool mit dem Metalle und verschiedene Geometrien (u.a. Bleche, Rohre, Träger, Behälterböden) geschnitten werden können.
Wie funktioniert ein Plasmaschneider?
Ein Plasmaschneider erzeugt einen Lichtbogen zwischen einer Elektrode und dem Werkstück. Plasma ist ein elektrisch leitfähiges Gas mit einer Temperatur von etwa 30.000 °C. Durch die hohe Energiedichte des Lichtbogens schmilzt das Metall und wird durch einen Gasstrahl ausgeblasen, wodurch eine Schnittfuge entsteht.
Was versteht man unter Plasma?
Plasma ist ein elektrisch leitfähiges Gas mit einer Temperatur von etwa 30.000 °C. Es wird auch als vierter Aggregatszustand bezeichnet.
Was benötige ich zum Plasmaschneiden?
Um mittels Plasmatechnologie Metalle und verschiedene Körper zu schneiden, sind folgende Bestandteile notwendig: eine Plasmaquelle (oder auch Plasmastromquelle: größte Hersteller sind Kjellberg und Hypertherm), ein Schneidkopf, Strom und das entsprechende Schneidgas.
Was für ein Gas benutze ich zum Plasmaschneiden?
Für einfaches Plasmaschneiden reicht Luft aus. Für das präzisere Feinplasmaschneiden empfiehlt sich für Baustahl in der Regel Sauerstoff als Schneidgas und Luft als Wirbelgas (zum Einschnüren des Lichtbogens). Edelstahl und Aluminium wird vorwiegend mit Stickstoff, Formiergas oder Argon/Wasserstoff geschnitten. Die genaue Zusammensetzung des Gasgemisches richtet sich dabei nach der zu bearbeitenden Materialstärke.
Welche Vorteile hat Plasmaschneiden gegenüber Laserschneiden?
Mit Plasma lassen sich auch mittlere Materialstärken bis 50 mm qualitativ gut und wirtschaftlich effizient schneiden. Plasmaschneiden hat geringere Anforderungen an das zu bearbeitende Material und dessen Oberfläche. Außerdem sind die Anschaffungskosten einer Plasmaschneidanlage deutlich niedriger als die Investition in eine Laserschneidanlage.
Welcher Unterschied besteht zwischen dem Plasmaschneiden und dem autogenen Brennschneiden?
Plasma kann alle metallisch leitfähigen Werkstoffe schneiden, Autogen (auch autogenes Brennschneiden genannt) nur unlegierte oder niedriglegierte Stähle. Außerdem ist Plasma im dünnen bis mittleren Blechdickenbereich schneller und flexibler, sowie speziell im dünnen Blechdickenbereich qualitativ besser.
Welche Vorteile und Nachteile hat das Plasmaschneiden?
Vorteile und Stärken der Technologie Plasma:
- Höchste Flexibilität beim Schneiden aller elektrisch leitfähigen Werkstoffe
- Geringste Anforderungen an Materialbeschaffenheit und Arbeitsumfeld
- Hohe Schneidgeschwindigkeiten und gute Qualität im dünnen und mittleren Blechdickenbereich
- Schneiden hochfester Baustähle mit geringer Wärmeeinbringung
- Sehr gute Automatisierbarkeit
- Unterwasser-Plasmaschneiden für sehr geringen Wärmeverzug der Werkstücke und geringen Schallpegel im Arbeitsumfeld
Nachteile und Einschränkungen der Technologie Plasma:
- Breite Schnittfuge im Vergleich zum Laserschneiden und Wasserstrahlschneiden
- Feine Konturen mit Qualitätseinbußen
- Relativ hoher Schallpegel
Welche Geometrien und Konturen können beim Plasmaschneiden geschnitten werden?
Generell ist die Geometrie der Kontur von der jeweiligen Bearbeitungsmaschine abhängig. Während mit Flachbett-Portalanlagen nur Bleche bearbeitet werden können, sind Roboter oder Mehrachsaggregate auch in der Lage 3D-Körper wie Rohre, Profile oder Klöpperböden zu bearbeiten. Für eine Bauteilgröße unter ca. 10 mm wird aber üblicherweise auf andere Schneidverfahren gesetzt (Laser, Wasserstrahl).