Wie funktioniert Laserschneiden?
Das Laserschneiden ist eine bewährte und sich stetig entwickelnde Technologie, die in vielen Branchen zum Einsatz kommt. Moderne Laserschneidmaschinen ermöglichen den präzisen und schnellen Zuschnitt von unterschiedlichen Materialien. Das Schneiden von Aluminium bildet da keine Ausnahme. Sie benötigen ein 2D- oder 3D-Lasersystem? Dann sind Sie bei MicroStep genau richtig! Wir blicken bei der Entwicklung unserer CNC-Schneidmaschinen auf 30 Jahre Know-how zurück.
Laserschneiden – Alles Wissenswerte im Überblick
Beim Laserschneiden (englisch "laser cutting") handelt es sich um ein thermisches Trennverfahren. Im Zuge des Laserschneidens werden mithilfe eines Laserstrahls die zu trennenden Materialien verdampft oder geschmolzen. Laserquellen unterschiedlicher Wellenlänge ermöglichen es heute, Materialien nahezu aller Werkstoffgruppen millimetergenau und damit auf höchstem Qualitätsniveau zu schneiden – ganz gleich ob Papier, Kunststoff, Metall oder Glas, Holz und weitere Materialien. Das Laserschneidverfahren ist wegen seiner Präzision und Geschwindigkeit sowie seiner nachbearbeitungsarmen Schneidergebnisse äußerst effizient. Besonders bekannt und auch wirtschaftlich ist es in der Metallbearbeitung, wo beispielsweise Metall und Stahl in relativ dünnen Materialstärken mit höchster Präzision und größtmöglicher Bearbeitungsgeschwindigkeit geschnitten werden müssen. Mit der fortschreitenden Entwicklung der Laserquellen und immer größerer zur Verfügung stehender Laserleistungen ist es auch möglich, immer höhere Materialstärken wirtschaftlich bearbeiten zu können.
Wie funktioniert Laserschneiden? Der technische Vorgang.
Beim CNC-Laserschneiden wird der Laserstrahl mit Hilfe optischer Elemente, die sich innerhalb eines Schneidkopfs befinden, fokussiert. Um einen gezielten Laserschneidprozess zu starten, muss das zu schneidende Material punktförmig an einer vorher definierten Stelle durchdrungen werden. Dieser Vorgang wird auch als Einstechprozess bezeichnet. Ist dies geschehen, kann der eigentliche Schneidprozess starten. Dabei wird der Strahl an der Schneidfront absorbiert und erzeugt dort eine Schmelze (auch Metalldampf oder Materialdampf genannt), die unmittelbar nach ihrer Entstehung mittels eines Gasstroms nach unten ausgeblasen wird. Für den Laserzuschnitt ist zumeist ein Prozessgas notwendig. Je nach Schneidverfahren kommen dabei als Schneidgas üblicherweise Sauerstoff, Stickstoff oder Luft zum Einsatz. Zurück bleibt ein Schnittspalt (auch Schneidspalt genannt), der je nach eingesetztem Schneidverfahren, Materialstärke und je nach Auslegung des optischen Systems unterschiedliche Breiten annehmen kann. Das Lasersystem fährt die vorher festgelegte Geometrie ab und schneidet das Material.
Welche Laserschneidverfahren gibt es?
Grundsätzlich wird zwischen drei Laserschneidverfahren, nämlich dem Laserbrennschneiden, dem Laserschmelzschneiden und dem Lasersublimierschneiden differenziert. Als Unterscheidungskriterium hierfür gilt die Art und Weise, wie der zu schneidende Werkstoff aus der Schnittfuge entfernt wird, nämlich ob in Form von Dampf, als Oxidationsprodukt oder als Flüssigkeit.
Neben den drei genannten Trennverfahren werden zudem das Thermische-Laser-Separieren und das Ritzen als Laserschneidverfahren gewertet.
So funktioniert Laserschneiden: Relevante Laserschneidverfahren im Überblick
Welches Laserschneidverfahren zum Einsatz kommt, hängt maßgeblich vom zu verarbeitenden Material ab:
Brennschneiden
Das Laserstrahlbrennschneiden zählt zu den am häufigsten verwendeten Verfahren in der Technologie des Laserschneidens und wird überwiegend zum Schneiden von Baustahl verwendet. Bei diesen Laserschneidverfahren wird als Schneidgas Sauerstoff genutzt, wobei das Material beim Schneiden respektive Aufschmelzen den durch den Laserstrahl auf Entzündungstemperatur aufgeheizten Werkstoff durch die Reaktion mit dem Sauerstoff verbrennt. Die Reaktion des Sauerstoffs mit dem Werkstoff ist exotherm und führt somit dem Prozess zusätzliche Energie zu, die den Schneidvorgang begünstigt. Beim Brennschneiden ist es deshalb möglich, bei größeren Blechdicken deutlich höhere Schneidgeschwindigkeiten zu erzielen als beim Schmelzschneiden mit gleicher Laserleistung. An der Schnittkante entsteht durch den verwendeten Sauerstoff eine Oxidschicht. Diese Schicht kann bei nachfolgenden Fertigungsschritten wie Schweißen, Beschichten bzw. Lackieren o.ä. zu Problemen führen, wodurch eine Entfernung der Oxidschicht (Schreibweise abgeleitet aus dem griechischen: Oxydschicht) notwendig wird. Ein wichtiger Faktor für die Schnittkantenqualität und die Geschwindigkeit beim Laserstrahlbrennschneiden ist der Reinheitsgrad des Sauerstoffs. Um eine gleichbleibende und gute Schnittqualität zu erreichen, sollte dieser nicht kleiner als 3.5 sein. Dies bedeutet, dass er eine Reinheit von ≥ 99,95 % hat.
Schmelz- bzw. Hochdrucklaserschneiden
Beim Schmelzschneiden werden inerte Gase wie Stickstoff oder Argon mit Drücken bis zu 25 bar eingesetzt. Da diese Gase nicht mit dem Werkstoff reagieren, muss die gesamte Werkstoffdicke vom Laserstrahl geschmolzen werden. Der hohe Gasdruck bewirkt dann, dass das geschmolzene Material mit hoher Geschwindigkeit aus der Schnittfuge getrieben wird. Damit kann die Bildung eines Grates und das Anhaften von Schlacke an den Schnittkanten in einen großen Dickenbereich weitestgehend verhindert werden. Da keine exotherme Reaktion zwischen Material und Gas stattfindet, wird auch keine zusätzliche Energie zugeführt. Durch die Verwendung von inerten Gasen als Schneidgas bleibt die Schnittkante frei von Oxiden. Umgangssprachlich wird das Schneiden mit nicht reaktiven Gasen aufgrund des verwendeten und benötigten hohen Druckes auch als Hochdruckschneiden bezeichnet und meist dort eingesetzt, wo metallisch blanke Schnittflächen erzielt werden müssen. Haupteinsatzgebiet ist das Schneiden von Edelstahl und Aluminium sowie das Schneiden von dünneren Baustählen.
Sublimierschneiden
Der Prozess des Sublimierschneidens basiert auf dem Verdampfen und Ausblasen des Werkstoffs während des Schneidvorgangs. Das bedeutet, dass der zu verarbeitende Werkstoff an der Schnittfuge von einem festen Zustand, ohne flüssig zu werden, in einen gasförmigen Zustand übergeht. Neben anorganischen Materialien lassen sich mithilfe des Sublimierschneidens auch organische Materialien sicher und exakt schneiden. Zum Einsatz kommende Materialien für dieses Schneidverfahren sind z.B. Holz, Leder, Textilien sowie homogene und faserverstärkte Kunststoffe. Typisch für dieses Verfahren ist, dass eine zeitintensive mechanische Nachbearbeitung der angefertigten Sublimierschnitte entfällt, da beim Sublimierschneiden keine Gratbildung entsteht. Während des Schneidprozesses entstehen Dämpfe. Um zu vermeiden, dass es zu einer starken Rauchentwicklung oder einem Einflammen der zu schneidenden Materialien kommt, wird ein Schneidgas, beispielsweise Stickstoff, eingesetzt. Gleichzeitig verhindert das Schneidgas auch ein Kondensieren der Dämpfe an der Schnittkante.
Laserschneiden Anwendungsbereiche
Aufgrund der Tatsache, dass das Schneiden von unterschiedlichen Materialien mit Hilfe einer Laserschneidanlage trotz der relativ hohen Anschaffungskosten sehr produktiv und äußerst wirtschaftlich ist, sind die Anwendungsbereiche breit gefächert; und zwar nicht nur in Industrie und Produktion, sondern auch in alltäglichen nicht-industriellen Einsatzgebieten. Das Laserschneiden kommt im Fahrzeug- und Flugzeugbau, in der Elektroindustrie, im Kunsthandwerk, in der Medizintechnik, zur Schmuckherstellung, im Automatenbau ebenso zum Einsatz wie zur Stempelherstellung und in der Textil- und Modeindustrie sowie in vielen anderen Bereichen.
Fakt ist, dass die Anwendungsbereiche und Anwendungsmöglichkeiten des Laserschneidens kontinuierlich erweitert werden und in Wissenschaft und Forschung Gegenstand vieler Projekte sind. Fakt ist auch, dass die Möglichkeiten der Laserschneidtechnik bis dato keinesfalls als ausgereizt gelten. Vor allem im Bereich der Faserlasertechnologie können mit den sich stetig weiterentwickelnden Laserquellen immer größere und innerhalb eines Systems variablere Materialstärken geschnitten werden. Durch den parallel stetig zu steigernden Grad an Automatisierung, beispielsweise durch die Nutzung der Potentiale innerhalb des Materialhandlings, lassen sich die Vorteile von immer kürzeren Bearbeitungszeiten durch den Einsatz von Laserschneidanlagen bestens auszunutzen.
Laserschneiden Industrie – Materialien
Beim Laserschneiden sprechen wir von sogenannten Industrielasern, welche sich bereits in vielen Bereichen etabliert haben und in puncto Effizienz mittlerweile nahezu konkurrenzlos sind. Die hoch entwickelte Technologie der Industrielaser löst andere Werkzeuge ab, da die Präzision und die Schneidqualität der Laserzuschnitte so gut wie keine Nachbearbeitung mehr erfordert. Mit Laser werden vorrangig folgende Metalle geschnitten:
- Baustahl
- Edelstahl
- Aluminium
- Kupfer
- Messing
Das Schneiden mittels CO2-Laser wird mehr und mehr nur noch für spezifische Anwendungen eingesetzt, wie zum Beispiel beim Zuschnitt von Holz, Plexiglas oder bei Kunststoffen.
Der Grund hierfür liegt in der unterschiedlichen Eignung der verschiedenen Wellenlängen der Laserstrahlung für das jeweilige Material. Die Auswahl des idealen Lasers (Art des Lasers / Wellenlänge und dessen Leistung) ist der wichtigste Faktor für eine optimale Produktion bei möglichst minimalen Kosten.
Aufbau von Laserschneidanlagen
Eine Laserschneidanlage besteht grundsätzlich immer aus mehreren Komponenten, die im Folgenden einmal kurz aufgezählt werden:
- Laserstrahlquelle: Eine Strahlquelle besteht im Wesentlichen aus einer Energiequelle, einem Lasermedium und einem Resonator, wobei die unterschiedlichen Lasertypen sich hier im Aufbau und in der Ausführung der einzelnen Komponenten stark unterscheiden.
- Laserstrahlführung: Die Strahlführung hat die Aufgabe den Laserstrahl von der Strahlquelle, mit möglichst wenig Verlusten zum Bearbeitungskopf zu transportieren.
- Führungsmaschine Die Führungsmaschine beinhaltet alle Achsen, Motoren, Servos, Regler sowie Steuerungen und Software, die benötigt werden, um den späteren Bewegungs- und Regelablauf des Schneidprozesses gewährleisten zu können. Bei den Achsen unterscheidet man in X, Y (Verfahrachsen des jeweiligen Arbeitsbereiches) und Z (Zustellachse des Schneidkopfes).
- Schneidkopf: Im Schneidkopf wird die ankommende Laserstrahlung fokussiert und entsprechend der Applikationsdaten für den jeweiligen Schneidprozess zur Verfügung gestellt. An der Austrittsöffnung des Schneidkopfes tritt zusätzlich zur fokussierten Laserstrahlung auch noch das Schneidgas für den jeweiligen Schneidprozess aus. Die Formung des Schneidgases erfolgt dabei innerhalb der Schneiddüse, welche zumeist aus Kupfer besteht.
- Gasversorgung: Eine Gasversorgung stellt die für den Schneidprozess benötigten Gase zur Verfügung sowie Hilfsgase, die für die Funktion des Lasers oder der Maschine benötigt werden.
- Absaug- und Filtersystem: Die Absaugung entzieht die beim Schneidprozess entstehenden Gase und Partikel und trennt diese. Materialpartikel und Stäube werden dabei in einem Container gesammelt, die gereinigte Luft wird der Umgebung wieder zugeführt.
- Kühlung: Um Überhitzung oder Zerstörung einzelner Komponenten zu vermeiden, werden diese mit Hilfe eines Kühlkreislaufes gekühlt. Dies betrifft im Wesentlichen die Laserstrahlquelle, die Laserstrahlführung und den Schneidkopf der Anlage.
- Einhausung: Zur Einhaltung aller Sicherheitsstandards sind Laseranlagen mit einer Einhausung und einem Sicherheitsbereich versehen; um die Mitarbeiter vor den Gefahren von sich schnell bewegenden Teilen und vor eventueller Laserstrahlung zu schützen.
Für das 3D-Laserschneiden werden spezielle Schneidköpfe und zusätzliche Bewegungsachsen eingesetzt. Diese können in 3D geschwenkt werden, also zu beiden Seiten wie auch zum Portal und vom Portal weg. Dies ermöglicht eine flexible und räumliche Bearbeitung des Materials bis zu Winkeln von 45°.
Kann ich Ihnen helfen? Ich stehe Ihnen bei Fragen gerne persönlich zur Seite:
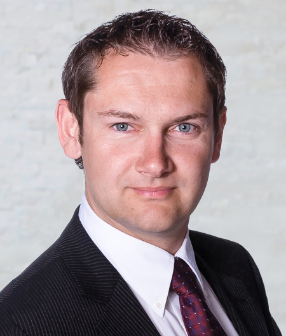
Marco Große-Schütte
Leitung Vertrieb
Telefon: +49 8247 96294 88
E-Mail: marco.grosse-schuette@microstep.com
FAQ: Wir beantworten Ihre Fragen zu "Wie funktioniert Laserschneiden?"
Welche Schnittbreiten sind beim Laserschneiden möglich?
Hier muss man zuerst einmal unterscheiden, um welche Art des Laserschneidens es sich handelt. Denn in der Regel entstehen beim Laserbrennschneiden größere Schnittfugen als beim Laserschmelzschneiden. Zusätzlich ist die Schnittbreite auch abhängig von der optischen Auslegung des Systems und der zu schneidenden Materialstärke. Grundsätzlich gilt dabei, dass bei dünneren Materialien der Schnittspalt kleiner ist als bei dickeren Materialien. Im Feinschneidbereich und in der Mikrobearbeitung sind Schnittspalten im unteren Mikrometerbereich realisierbar. In der industriellen Metallbearbeitung von Blechen oberhalb 1 mm sind Schnittspalten von etwa 0,3 mm bis 3 mm durchaus möglich. Ein generelles Merkmal eines Laserschnittes ist dabei der nahezu senkrechte Verlauf der Schnittkante.
Laserschneiden vs. Plasmaschneiden – welche Vorteile?
Sowohl das Laserschneiden als auch das Plasmaschneiden haben spezifische Vorteile. Abhängig vom Anwendungsgebiet kann beides das optimale Mittel der Wahl sein in Sachen Wirtschaftlichkeit, Genauigkeit und Effizienz. So lassen sich mittlere Materialstärken von 20 bis 50 mm mit Plasma qualitativ gut und wirtschaftlich effizient und mit höheren Schneidgeschwindigkeiten schneiden. Auch die Anforderungen an das zu bearbeitende Material und dessen Oberfläche sind bei Plasma generell geringer, genauso wie die Anforderungen an das Arbeitsumfeld. Im Gegensatz zum Laser hat Plasma dagegen Einschränkungen beim Schneiden von kleinen Konturen und einen relativ breiten Schnittspalt. Dazu kommt ein hoher Lärmpegel beim Plasmaschneiden und die Tatsache, dass nur elektrisch leitfähige Stoffe geschnitten werden können. In der Anschaffung sind Plasmaanlagen günstiger als Laseranlagen, wobei sich dieser Unterschied in den letzten Jahren deutlich verringert hat.
Vor allem im dünneren Blechdickenbereich bis 10 mm sind die Vorteile des Lasers deutlich sichtbar. Die Schneidgeschwindigkeit ist teilweise erheblich schneller, die Schnittqualität besser, es können wesentlich genauere Konturen geschnitten werden und dies bei einer wesentlich geringeren Lärmbelästigung und bei kleineren Schnittspalten. Die Automatisierbarkeit einer Laseranlage ist zudem wesentlich höher.
Die Kostenbetrachtung zwischen Plasmaschneiden und Laserschneiden pro Schnittmeter hängt von sehr vielen Faktoren ab und ist deshalb immer von dem jeweiligen Anwendungsfall abhängig. Prinzipiell sind die Schnittkosten im Dünnblechbereich mit Laser geringer und im Dickblechbereich mit Plasma. Durch die stetig zunehmende Laserleistung zum Schneiden und die geringer werdenden Preise pro kW Laserleistung verschiebt sich auch der Schnittpunkt dieser beiden Kurven.
Wie viel Zeit benötigt eine Laseranlage bis der Schneidvorgang gestartet werden kann?
Wenn alle Einzelkomponenten der Anlage eingeschaltet sind, alle Hilfsmedien zur Verfügung stehen (Schneidgase, Druckluft), das auszuführende Programm geladen ist, alle Parameter korrekt eingestellt, die Anlage referenziert und der Laser strahlbereit ist, dann kann der Schneidvorgang ausgeführt bzw. gestartet werden. Die Zeit bis zur Strahlbereitschaft des Lasers ist dabei zwischen Faserlaser und CO2-Laser sehr unterschiedlich. Während es sich bei einem Faserlaser um einen rein elektronischen Laser handelt, der sofort nach Einschalten und Hochfahren der internen Steuerung strahlbereit ist, muss ein CO2-Laser erst einen längeren Startzyklus durchlaufen, bis dieser Strahlbereitschaft meldet. Ein solcher Startzyklus kann zwischen 5 bis 20 Minuten dauern; bei längeren Stillstandszeiten auch noch länger. Bei modernen Faserlaseranlagen vergehen nach Einschalten des Hauptschalters teilweise weniger als 5 Minuten bis zum ersten Schnitt.
Welche Schriftart eignet sich für das Beschriften mittels Laser?
Grundsätzlich kann jede Schriftart bei Laseranlagen, sei dies zum Schneiden oder zum Beschriften, verwendet werden, da es sich um eine CNC-Programmierung handelt und die einzelnen Schriftarten entsprechend in ein Schneidprogramm umgewandelt werden können. Des Weiteren bietet MicroStep aber auch CNC-Schneidanlagen an, die mit sogenannten Beschriftungslasern ausgestattet sind. Diese separaten Systeme bieten bei speziellen geforderten Beschriftungsaufgaben (QR-Code etc.) eine deutlich höhere Flexibilität und Geschwindigkeit beim Markieren und Beschriften.