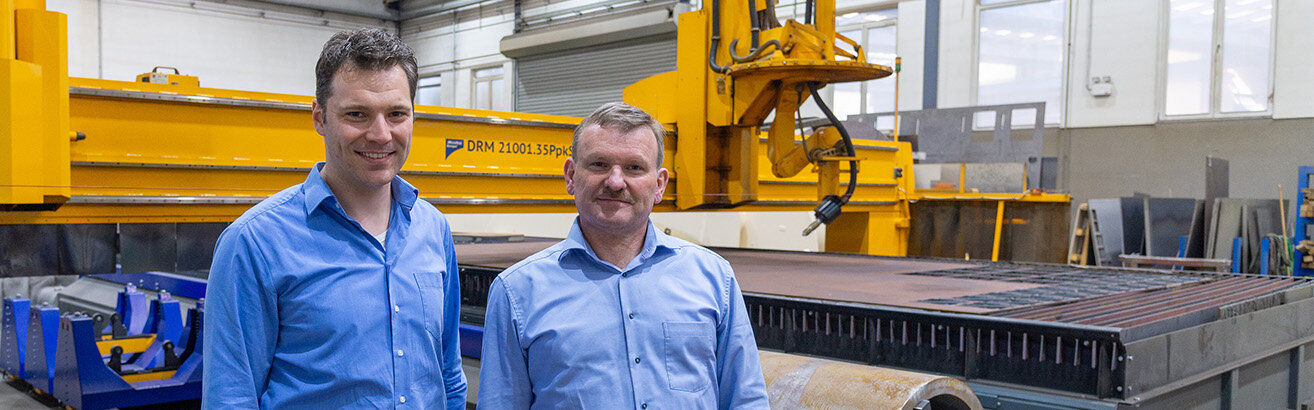
Schneller, effizienter und präziser: die DRM bei STF bringt viele Vorteile
Eine Schneidlösung für alle Anwendungen
Die Firma STF produziert großformatige Anlagenlösungen. Dank einer DRM können Bleche, Rohre und Träger automatisiert bearbeitet werden. Ein Quantensprung auf vielen Ebenen
Publiziert 15.02.2024 | Erich Wörishofer
Unternehmensprofil:
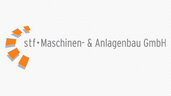
Die STF Maschinen- und Anlagenbau GmbH entwickelt und produziert für den weltweiten Markt Kunststoffrecycling-Anlagen. Systeme für die Verwertung von PET-Flaschen sind in Australien und Kanada wie auch in Ägypten, Tahiti oder Japan im Einsatz. Die rund 80 Mitarbeiter am Hauptstandort nahe Passau kümmern sich noch um ein zweites Geschäftsfeld: für große Kunden konstruiert und fertigt das Unternehmen Schwermaschinen und Sonderanlagen, beispielsweise Hafenanlagen, Grundrahmen und Gehäuse für Gas- und Wasserturbinen oder auch Prüfstände für Panzer und Hubschrauber.
Der Maschinen- und Anlagenbauer STF investierte in eine flexible 3D-Plasma-Autogenschneidanlage von MicroStep, mit der Bleche, Rohre und Träger automatisiert bearbeitet werden können. Für das Unternehmen aus Niederbayern ein Quantensprung bei der Bewältigung von großformatigen Aufgaben.
Anlagenprofil:
DRM- Netto-Bearbeitungsfläche für Blechtafeln: 21.000 x 3.500 mm
- Rohrschneidvorrichtung zur Bearbeitung von Rohren mit 30 bis 700 mm Durchmesser und 10.000 mm Länge
- Trägerbearbeitung bis 1.000 mm Kantenbreite und 6.000 mm Länge
- Plasmarotator (120° schwenkbar) zur erweiterten Schweißnahtvorbereitung mit automatischer Kalibriereinheit2 x Autogenschneiden
- Laserscanner zur Erfassung der Oberflächengeometrie von Rohren, Profilen und Trägern
- Scanner ermöglicht nachträgliches Anarbeiten von Schweißnahtvorbereitungen (ABP-Technologie von MicroStep)
- Schwingfördertischsystem zum Austrag von Schlacke und Kleinteile
Beim Recycling von Kunststoff kommen große Automationssysteme zum Einsatz. Trennen, Zerkleinern, Sortieren sind Arbeitsschritte, bevor beispielsweise PET-Flaschen später wieder zu neuem Leben erwachen können. Große Lösungen für die ganze Welt kommen aus einer kleinen Ortschaft nahe Passau. Denn hier produziert die STF Maschinen- und Anlagenbau GmbH zum einen Kunststoffrecycling-Anlagen, zum anderen auch Sondermaschinen in außerordentlichen Dimensionen. Mit der Investition in ein vielseitiges Schneidcenter von MicroStep läuft der Zuschnitt von Blechen, Rohren und Trägern seit 2019 automatisiert ab. Für STF bedeutet dies eine Vielzahl von Vorteilen. Schneller, effizienter, präziser wird nun produziert. „MicroStep war der Hersteller, der das beste Gesamtpaket hatte. Das ist ein positiver Effekt, der sich durch die ganze Firma zieht.“
Wenn Kunden bei der STF Maschinen- und Anlagenbau GmbH nahe des niederbayerischen Passau Hilfe suchen, dann geht es meist um schwere, großformatige und komplexe Aufgaben. Die Produkte sind fast ausschließlich Maßanfertigungen und bringen zwischen 5 und 40 Tonnen auf die Waage. Denn das Unternehmen hat zwei Kernaufgaben und in beiden Bereichen wird am Ende aus einer durchdachten Idee ein großes Ergebnis, das weltweit im Einsatz ist. „Unser Hauptgebiet ist das Entwickeln und Fertigen von Kunststoffrecyclinganlagen. Unser zweites Standbein ist der Schwermaschinenbau, wo wir für große Kunden Sondermaschinen bauen mit hohen Qualitätsansprüchen. Das sind keine Serienprodukte, sondern eigentlich Einzelmaschinen“, sagt Reinhard Friedl, der Technische Betriebsleiter. „Unsere Kunden wissen: Wir sind flexibel, wir reagieren schnell. Wir gehen auf ihre Wünsche ein und hören zu.“
Nach intensiver Arbeit der 80 Mitarbeitenden verlassen die Erzeugnisse das Werk in Aicha vorm Wald und werden rund um den Globus montiert und in Betrieb genommen. Dabei handelt es sich um Kunststoffrecyclingmaschinen beispielsweise für PET-Flaschen aber auch um Hafenanlagen, Kräne, Panzer-Hubschrauber-Prüfstände oder Grundrahmen und Gehäuse für Gasturbinen und Wasserpumpen auf Bohrinseln. Alles geschieht dabei in Eigenregie: Zuschneiden, Kanten, Zusammenbauen, Schweißen, mechanisch bearbeiten, Lackieren, Endmontage, Probelauf und Lieferung. Dabei wachsen die Herausforderungen. Wo einst 1 Tonne pro Stunde verarbeitet wurden, sind es heute 3 Tonnen. Wo einst die Ansprüche an Qualität und Toleranzen der Halbzeuge und Produkte manuell zu erfüllen waren, sind heute höchste Standards vor allem bei den Kunststoffrecyclinganlagen einzuhalten. „Die Anlagen werden immer schneller, immer größer, der Durchsatz muss immer weiterwachsen. Das ist eine Herausforderung für Konstruktion, Programmierung, Produktion und Montage“, sagt Christian Kühberger, zuständig für die Arbeitsvorbereitung.
Alte Anlage wurde zu klein – Wunschlösung mit deutlich mehr Optionen gesucht
Zu dem Know-how, welches sich die Firma STF im Laufe der Jahre erarbeitet hat, benötigt es entsprechend maschinelle Unterstützung. Und wie in vielen Betrieben üblich macht der Zuschnitt den Anfang – mit den wachsenden Maschinen wuchsen auch hier die Probleme. Die genutzte 3D-Plasmaschneidanlage wurde älter, die Tischlänge reichte nicht mehr für alle Aufgaben aus. Entsprechend wurde immer mehr zusätzlich zugekauft. „Für unsere Bauteile mit 12 Meter und mehr hatten wir sehr lange Wartezeiten und sehr hohe Preise“, blickt Reinhard Friedl zurück. Diese Thematik gehört seit längerem der Vergangenheit an. Denn seit Mitte 2019 setzt STF beim Zuschnitt auf ein Schneidcenter mit einem enormen Maß an Multifunktionalität. Nach längerer Beratung investierte das Unternehmen in eine DRM von MicroStep, die mittels Plasmarotator neben Flachmaterial auch Rohre und Träger in größeren Dimensionen schneiden kann. Ein Autogenbrenner für dickere Bleche ist integriert, ein Laserscanner kommt bei Blechen, Rohren und Trägern zum Einsatz und bietet eine Fülle an Vorteilen.
Vielzahl an Möglichkeiten und Prozesssicherheit überzeugt
Ein Quantensprung bei der automatisierten Produktion im Betrieb. Doch der Weg zum Multifunktionssystem war weit. Der erste Impuls war eine neue und lediglich längere 3D-Plasmaschneidanlage zu kaufen. Erst im Zuge der Recherche und den späteren Beratungsgesprächen kristallisierte sich der Wunsch nach einer Maschine für mehr als nur Flachmaterial heraus. „Wir haben mehrere Hersteller angefragt und geschaut: was können die Maschinen eigentlich, wo ist die Range. Zwei Hersteller blieben übrig, bei denen wir auch Vorführungen hatten“, blickt Kühberger zurück. Eine Analyse der zu bearbeitenden Teile im Unternehmen brachte die Gewissheit: „MicroStep war der Hersteller, der das beste Gesamtpaket hatte. Wir haben gesehen: Wir können Rohre bearbeiten, wir können Träger bearbeiten, wir können an großen Blechstärken Fasen anarbeiten, wir können auch nachträgliche Fasen anarbeiten – auch dafür haben wir viele Anwendungen. Die MicroStep-Maschine hatte die größten Möglichkeiten“, so der für den Zuschnitt zuständige Arbeitsvorbereiter.
Automatisierung statt zeitraubendes manuelles Fasen, Trägerausklinken und Rohrbearbeiten
Und diese werden immer weiter ausgeschöpft. STF verarbeitet Bleche von 3 bis 180 mm (hauptsächlich Baustähle vom S235 bis S690), Träger von HEB 200 bis HEB 1000 und Rohre von 50 mm bis 700 mm Durchmesser mit Wandstärken von 3 bis 50 mm. Wo früher Rohre und Träger manuell zugeschnitten und ausgeklinkt wurden, ist STF heute um ein Vielfaches schneller und genauer. Auch die große Anzahl an automatisierten Schweißnahtvorbereitungen bringen eine enorme Zeitersparnis. Lagerhaltung gibt es nur in geringfügigem Maße bei Blechen, der größte Teil wird auftragsbezogen bestellt und just-in-time verarbeitet.
„Ein positiver Effekt, der sich durch die ganze Firma zieht“
„Wir sind sehr zufrieden. Die Maschine läuft gut. Es ist uns nichts versprochen worden, was nicht funktioniert. Wir können unser gesamtes Spektrum selbst abdecken und sogar noch erweitern“, betont Reinhard Friedl. „Das ist ein Meilenstein von der alten auf die neue Maschine. Wir versuchen die Maschine bis ins letzte Detail auszureizen“, so der Betriebsleiter. Sein Kollege Christian Kühberger ergänzt: „Und das Beste ist, wir haben immer noch Luft nach oben. Uns fällt immer noch mehr Blödsinn ein, was wir mit der Maschine machen können.“ Der Markt werde immer enger, die Preise müssten immer härter kalkuliert werden. Für Kühberger eine Schneidlösung, die sich auf vielen Ebenen bezahlt gemacht hat. „Logisch, weil wir jetzt ganz am Anfang viel automatisiert machen können, sparen wir uns sehr viel Zeit und haben anschließend mehr Manpower für den Zusammenbau, das Schweißen und weitere Nacharbeiten. Zudem haben wir eine deutlich höhere Bauteilgenauigkeit. Das sind lauter positive Effekte, die sich durch die ganze Firma ziehen.“
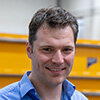
"Weil wir jetzt ganz am Anfang viel automatisiert machen können, sparen wir uns sehr viel Zeit und haben anschließend mehr Manpower für den Zusammenbau, das Schweißen und weitere Nacharbeiten. Zudem haben wir eine deutlich höhere Bauteilgenauigkeit. Das sind lauter positive Effekte, die sich durch die ganze Firma ziehen."
Christian Kühberger
Arbeitsvorbereitung | STF Maschinen- und Anlagenbau GmbH
DIE HIGHLIGHTS DER PLASMA-AUTOGENSCHNEIDANLAGE DRM IM ÜBERBLICK:
3D-Schneidcenter mit Plasmarotator zur Blechbearbeitung auf 21.000 x 3.500 mm
Die Firma STF entschied sich wegen der Kombination aus Vielseitigkeit und Robustheit für MicroSteps starken Spezialisten, die Baureihe DRM. Integriert wurde anstatt des standardisierten CNC-Brennschneidtischs ein Tecloga Schwingfördertisch des Typs OXYtrac 35205 1050 HD. Der Vibrationstisch mit Schwingfördereinrichtung ermöglicht den Austrag von Kleinteilen und Schlacke in ein vorgesehenes Auffangbehältnis. Zur 3D-Blechbearbeitung ist eine Arbeitsfläche von 21.000 x 3.500 mm verfügbar. „Wir haben viele unterschiedliche Kunden mit unterschiedlichen Anwendungen, mit sehr vielen Fasen und verschiedene Winkeln“, sagt Christian Kühberger.
Plasmarotator „Pantograph“ zur 3D-Bearbeitung von Blechen, Rohren und Profilen
Mit dem integrierten Plasmarotator „Pantograph“ können Neigungswinkel von bis zu 90° (einseitig bis zu 120°) erzielt werden. Durch das endlosdrehende Fasenaggregat ist eine erweiterte 3D-Bearbeitung an Blechen, Rohren und Profilen möglich. Als Plasmastromquelle ist eine leistungsstarke Kjellberg HiFocus 440i neo angeschlossen.
Zwei vollautomatische Autogenbrenner für höhere Materialstärken
Bis zu 180 mm dicke Bleche müssen bei STF beim Schwermaschinenbau zugeschnitten werden. Für die höheren Materialstärken wurden in die DRM zwei vollautomatische Autogenbrenner integriert, um schnell und effizient auch im Parallelschneidbetrieb zuschneiden zu können.
3D-Bearbeitung von Profilen bis 1.000 mm Kantenlänge
Beim Bau der Schwermaschinen sind oftmals Träger als Rahmenkonstruktion oder als Podest gefragt. Mittels des 120°-Rotators können in einer separaten Zone an einem Ende der Anlage präzise und automatisiert H-, U- und L-Profile bis HEB 1000 zugeschnitten und ausgeklinkt werden. Größtmögliche Präzision bei der Profilbearbeitung erzielt STF durch den Einsatz innovativer Technologie von MicroStep. Die Rohrschneidvorrichtung dreht das Profil in Position, ein am Portal installierter Laserscanner erfasst die Oberflächengeometrie im Schneidbereich des Werkstücks. Die 3D CAM-Software mCAM® kompensiert die produktionsbedingten Abweichungen zur Idealkontur, korrigiert die Parameter anhand des 3D-Scans und setzt dementsprechend die Schneidpfade. „Durch die Kombination aus Brenner und Laserscanner haben wir eine höhere Bauteilgenauigkeit und eine immense Zeitersparnis“, sagt Christian Kühberger
Vollautomatische Bearbeitung von Rohren von 50 bis 700 mm Durchmesser
Rohre von 50 bis 700 mm Durchmesser mit Wandstärken von 3 bis 50 mm und Längen bis 10.000 mm: Die Integration einer Zone zur automatisierten Rohrbearbeitung wird bei STF regelmäßig genutzt und führte zu enormen Vorteilen in der Produktion. Wo einstmals mit Behelfsmitteln händisch zugeschnitten und Aussparungen mit und ohne Fase angebracht wurden, wird dies nun von der DRM effizient vollzogen. Das Ergebnis: Mit der neuen Lösung ist das Unternehmen fünf Mal schneller beim Zuschnitt von Rohren.

ist Content Creator bei MicroStep Europa. Er hat jahrelange Erfahrung als Redakteur in den Bereichen Tageszeitung und im PR und lebt nun seine Leidenschaft für Wortakrobatik und ausführliche Recherche bei MicroStep aus. Er ist im ständigen Austausch mit unseren Technologieexperten und besucht für Interviews und Videos unsere Kunden vor Ort.
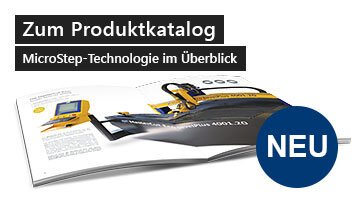
ERLEBEN SIE UNSERE ANLAGEN LIVE
im CompetenceCenter Süd oder Nord
- Alle vier Schneidtechnologien (Laser, Plasma, Autogen, Wasserstrahl)
- Innovative Automationssysteme
- Neuste Lösungen zum Biegen und Entgraten
- Industrie 4.0 Demofabrik
- Gut zu erreichen: im Süden und Norden Deutschlands
