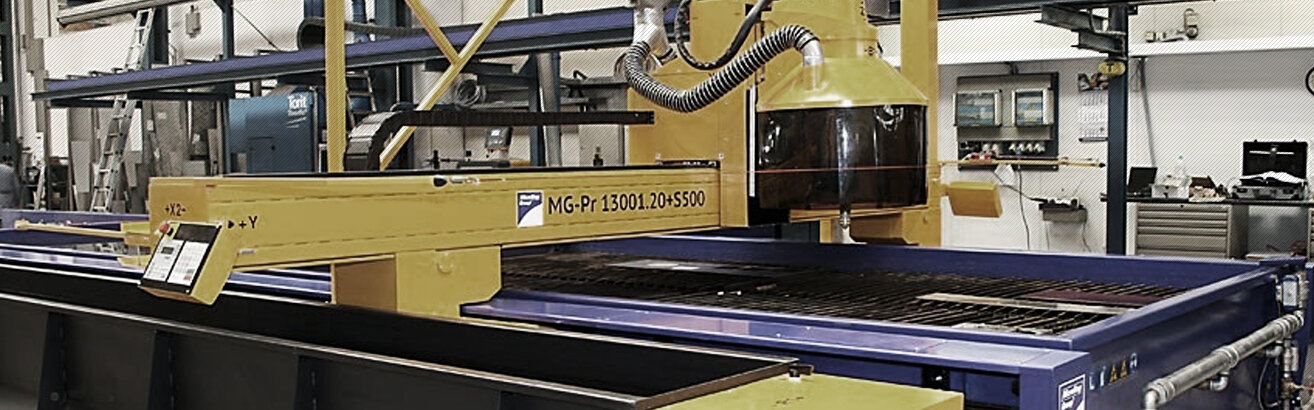
Rohrschneiden ohne Schlackeproblem dank CNC-Plasmaschneider von MicroStep
Plasmaschneiden mit Schlackelösung beim Rohrschneiden
Ob beim Faserlaser oder beim Plasmaschneiden: CNC-Plasmaschneidanlagen-Hersteller spart seinen Kunden mit innovativer Lösung Zeit und Geld bei der Nachbearbeitung
Publiziert 26.05.2019 | Erich Wörishofer
Bei der Bearbeitung von Rohren mit der Plasma- oder Laserschneidtechnik stellt das Einbringen und die Anhaftung von Schlacke im Rohrinneren ein großes Problem dar: Um zu einem sauberen Ergebnis zu kommen, ist eine zeit- und häufig auch kostenintensive Nachbearbeitung notwendig. Für eine westfälische Firma* hat MicroStep eine einzigartige Lösung für dieses Problem entwickelt – Plasmarohrzuschnitt unter Wasser.
Die MicroStep Group wurde von einem westfälischen Maschinenbauer mit einer kompletten Systemlösung für seine spezifischen Plasmaschneidanwendungen beauftragt. „Mit unserer alten Plasmaschneidanlage hatten wir Probleme mit der Maßhaltigkeit beim Fasenschneiden und die Kalibrierung des Brenners war mit einem hohen Aufwand verbunden“, erklärt der Fertigungsleiter des Unternehmens*.
Gewünscht wurde eine qualitativ hochwertige Plasmaschneidanlage, die Blechformate von 2000 x 4000 mm unter Wasser in zwei trennbaren Tischbereichen bearbeiten kann. Zudem sollte ein von der Firma eigens gebauter Bodenbearbeitungstisch integriert werden, bei dem ein besonderes Augenmerk auf die Bearbeitung von Behälterböden (Klöpperboden) – mit Spezial-Sprühdüsen für eine saubere Unterseite – gelegt wurde.
Darüber hinaus gab es eine weitere, zentrale Anforderung an die neue CNC-Maschine: „Rohrzuschnitt ist für uns sehr wichtig“, erklärt der Fertigungsleiter. Früher setzte man bei der Bearbeitung von Rohren auf die Schneidtechnik Laserschneiden, was aber einige Nachteile mit sich gebracht habe. „Die Rüstzeiten bei unserer Laserschneidanlage sind recht hoch und gleichzeitig kommt es auch beim Laserschnitt zu Anhaftungen im Rohrinneren, die nur mit einer aufwändigen Nachbearbeitung entfernt werden können. Das Schlackeproblem haben wir auch beim Rohrzuschnitt mit unserer alten Plasmaschneidanlage, mit der wir an einem anderen Standort produzieren.“ Gesucht wurde daher nach einer effektiven Lösung für die Schlackeentfernung bei der Rohrbearbeitung. Denn da die Schlacke beim Schneiden ins Rohrinnere fällt und dort schnell anhaftet, muss sie anschließend mit einer meist äußerst aufwändigen Nachbearbeitung entfernt werden.
Multifunktionale und individuell auf die Bedürfnisse des Kunden abgestimmte MicroStep-CNC-Plasmaschneidanlage der MG-Baureihe mit Rohrbearbeitungsmöglichkeit unter Wasser.
Mit all diesen Anforderungen im Blick wurde in Zusammenarbeit mit dem Kunden eine Rohrbearbeitungsmöglichkeit unter Wasser entwickelt. Das Ergebnis ist eine multifunktionale und individuell auf die Bedürfnisse des Kunden abgestimmte MicroStep-CNC-Plasmaschneidanlage der MG-Baureihe, die folgende Bearbeitungsmöglichkeiten bietet:
Rohrschneiden unter Wasser:
Eine Rohrschneidvorrichtung ermöglicht das Plasmaschneiden von Rohren mit einem Durchmesser von 30 bis 300 mm und einer Länge von max. 8000 mm (zentriert). Die Vorrichtung zum Rohrschneiden steht außerhalb des Schneidbeckens und eine wasserdichte Verbindung zum innenliegenden Vier-Backenfutter sorgt für einen sauberen Arbeitsplatz. Die Rohre werden unter Wasser geschnitten, das Wasserniveau kann automatisch angehoben und gesenkt werden. Im Backenfutter befindet sich eine Strömungsdüse die während des Schneidens die richtige Menge an Wasser durch das Rohr strömen lässt. Durch das Rohrschneiden unter Wasser bzw. die integrierte Strömungsvorrichtung kann die Schlacke bereits beim Schneiden ausgetragen und abtransportiert werden, was eine äußerst effektive und auch kosteneffiziente Alternative zu einer sonst sehr aufwändigen Nachbearbeitung darstellt. „Das ist ein großer Vorteil gegenüber der alternativen Bearbeitung von Rohren mit unserem Laser. Die Qualität ist beim Plasmaschneiden von Rohren unter Wasser entschieden besser“, sagt der Fertigungsleiter des MicroStep-Kunden.
Plasmaschneiden unter Wasser:
Auf einem Wasserschneidtisch mit einer Bearbeitungsfläche von bis zu 8000 x 2000 mm ist das Unterwasser-Plasmaschneiden mit bis zu 440 A und einer maximalen Materialstärke von bis zu 100 mm möglich.
Behälterbodenbearbeitung:
Durch eine verlängerte Z-Achse und eine angepasste Maschinenkonstruktion können mit der Anlage Behälterböden mit bis zu 2850 mm Durchmesser bearbeitet werden.
Fasenschneiden:
Dank des endlos drehenden Rotators können zusätzlich bei allen Bearbeitungsarten Fasenschnitte bis zu 50° vorgenommen werden. „Für uns ist beispielsweise die Möglichkeit, Schweißnahtvorbereitungen für Stutzenlöcher in Mantelbleche von Druckbehältern einbringen zu können, sehr wichtig. Mit der neuen Plasmaschneidanlage ersparen wir uns das manuelle Anschleifen und damit jede Menge Lärm und Dreck“, so der Fertigungsleiter des Unternehmens. Zudem ist der Rotator einfach zu kalibrieren, was im Produktionsablauf erheblich Zeit spart.
„In der Praxis hat sich das neue Schneidsystem bei uns bewährt“, bestätigt der MicroStep-Kunde*. Alle gewünschten Bearbeitungsschritte seien in einer Schneidmaschine vereint. Damit verfüge das Unternehmen über ein effektives und kosteneffizientes System zur Bearbeitung von Blechen, Rohren und Behälterböden.
*Hinweis der Redaktion: Namentlich will das Unternehmen nicht öffentlich in Erscheinung treten, da es seine Marktbegleiter nicht aktiv darüber informieren will, wie Rohre mit der einzigartigen MicroStep-Lösung viel effizienter und nahezu ohne Nacharbeit zugeschnitten werden können.

ist Content Creator bei MicroStep Europa. Er hat jahrelange Erfahrung als Redakteur in den Bereichen Tageszeitung und im PR und lebt nun seine Leidenschaft für Wortakrobatik und ausführliche Recherche bei MicroStep aus. Er ist im ständigen Austausch mit unseren Technologieexperten und besucht für Interviews und Videos unsere Kunden vor Ort.
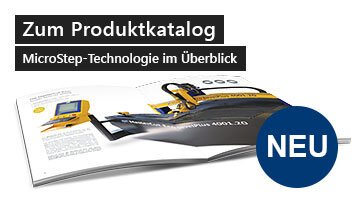
ERLEBEN SIE UNSERE ANLAGEN LIVE
im CompetenceCenter Süd oder Nord
- Alle vier Schneidtechnologien (Laser, Plasma, Autogen, Wasserstrahl)
- Innovative Automationssysteme
- Neuste Lösungen zum Biegen und Entgraten
- Industrie 4.0 Demofabrik
- Gut zu erreichen: im Süden und Norden Deutschlands
