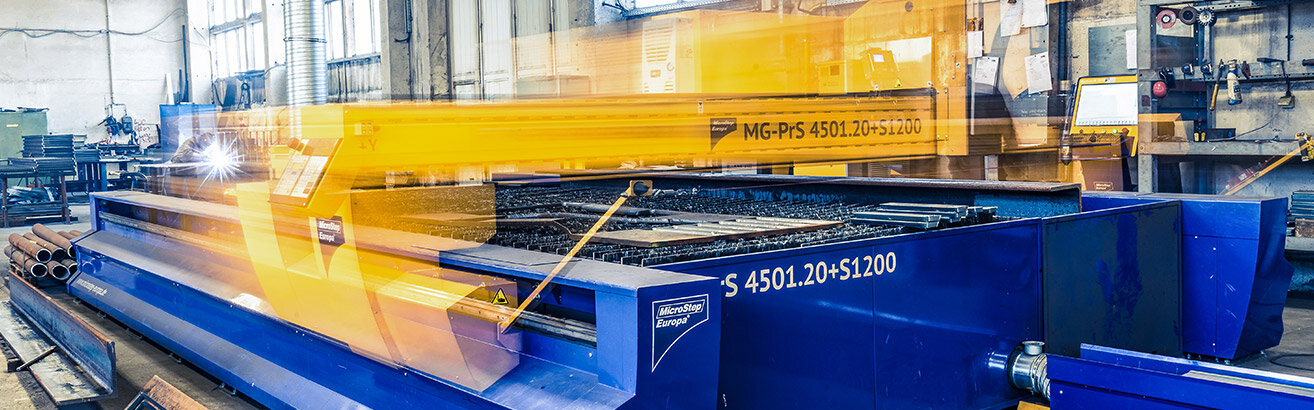
Die Plasmaschneidanlage bei AMS Alteno wurde konfiguriert mit Technologien zur 3D-Bearbeitung von Flachmaterial, Rohren und Profilen
„Bei MicroStep sind wir in guten Händen, da haben wir ein Rundum-Sorglos-Paket"
Die AMS Alteno UG, Spezialist für Metall- und Anlagenbau, spart mit einer neuen Schneidlösung 30 Prozent Zeit beim Materialhandling und fühlt sich bestens gerüstet für die Zukunft
Publiziert 22.03.2018 | Erich Wörishofer
Unternehmensprofil:

Altenoerstraße 715926 LuckauDeutschland
Die 2009 gegründete AMS Alteno bietet ihren Kunden individuelle Lösungen rund um den Anlagenbau, Metallbau und Stahlbau – von der Blechbearbeitung über die zerspanende Fertigung bis zu kreativen Sonderkonstruktionen. Mit seinen 30 Mitarbeitern fertigt das Job-Shop-Center rund 400 verschiedene Teile und Baugruppen.
Die Plasmaschneidanlage der Baureihe MG bei der Firma AMS Alteno wurde konfiguriert mit Technologien zur 3D-Bearbeitung von Flachmaterial und von Rohren und Profilen. Auf dem Plasma-Alleskönner können 2D-Zuschnitte wie auch 3D-Zuschnitte und nachträgliche Fasen zur Schweißnahtvorbereitung angebracht werden.
Die AMS Alteno UG im brandenburgischen Luckau steht für Anlagenbau, Metallbau und Stahlbau. Hier gefertigte Bauteilgruppen kommen in vielen Ländern der Erde zum Einsatz. Die Anforderungen des Marktes verlangten nach einem neuen Schneidsystem, mit dem die notwendige Flexibilität gegeben ist, exakte Wiederholgenauigkeit erreicht und ein Alleinstellungsmerkmal in der Region erzielt werden kann. Die Lösung: eine Plasmaschneidanlage der Baureihe MG von MicroStep mit Technologie zur 3D-Bearbeitung von Blechen, Rohren und Profilen.
Die Geschichte der AMS Alteno UG und der Wolffkran GmbH ist eng verwoben. Denn der Spezialist für Anlagen-, Metall- und Stahlbau und der international tätige Hersteller von Turmdrehkränen pflegen im brandenburgischen Luckau eine enge Partnerschaft – von der beide Seiten profitieren, seitdem der Kranexperte 2009 einen Produktionsstandort in unmittelbarer Nachbarschaft zur AMS Alteno UG errichtet hat.
„Wir sind mit der Firma Wolffkran schnell gewachsen. Wir haben angefangen mit sechs Arbeitern und drei oder vier Produktgruppen, die wir für Wolffkran produzierten“, blickt Steffen Hein zurück. „Heute fertigen wir mit 30 Mitarbeitern bis zu 1000 sich wiederholende Teile für die Firma mit Losgrößen von zwei bis zehn Stück“, sagt der Geschäftsführer der AMS Alteno. Dabei können Wolffkran und weitere Unternehmen auf die Stärken des Job-Shop-Centers vertrauen. „Wir arbeiten beinahe just-in-time, haben ein unglaubliches Maß an Flexibilität, haben ein sehr großes Blechlager, können schnell reagieren. Viele Sachen liefern wir innerhalb von 24 Stunden“, so Hein.
Kunden verlangen nach mehr Präzision, schnelleren Liefer-zeiten und Flexibilität
Als Basis des Leistungsportfolios dient dabei der in den letzten Jahren modernisierte Maschinenpark, der das Unternehmen fit für die Zukunft machte. Denn mit dem Wachstum an Mitarbeitern und Produkten wurde die AMS Alteno UG im Laufe der Zeit auch vor Probleme gestellt. Die Lieferzeiten der eingesetzten Lohnschneidbetriebe waren nicht vereinbar mit den Anforderungen der Produktion, eine lange zufriedenstellende Schneidlösung mit einem Handplasmaschneider hielt den Ansprüchen nicht mehr Stand – Bauteile wurden komplexer mit vielen langen Löchern und zahlreichen Schweißnahtanarbeitungen. Zudem verlangte der Hauptauftraggeber höhere Qualitätsstandards, eine bedeutend höhere Wiederholgenauigkeit und noch schnellere Liefertermine, um die Fertigungszeiten von Kränen zu beschleunigen.
Modernisierung oder Reduzierung der Mitarbeiter und der Produkte
„Wir haben gesehen, dass wir einen wahnsinnigen Aufwand betreiben mit viel Manpower. Viele Leute waren nur mit Materialhandling, Dokumentation oder manuellen Arbeiten beschäftigt“, sagt Steffen Hein, der vor der Entscheidung stand: Portfolio und Mitarbeiter reduzieren wegen zu hoher laufender Kosten oder in CNC-Technologie investieren. So schaute sich das Entscheidungsgremium auf Messen und im Internet um, welche Schneidtechnologien auf dem Markt verfügbar sind, welche die notwendige Präzision mit der geforderten Leistungsfähigkeit und Flexibilität kombinieren kann. Hier half ein Besuch im nur 30 Kilometer entfernt gelegenen Kjellberg Technologiezentrum in Finsterwalde.
„Im Vergleich zu anderen Maschinen haben wir hier ein Rundum-Sorglos-Paket. Es gibt natürlich immer irgendwo Verbesserungsbedarf: aber ich merke, dass MicroStep kontinuierlich daran arbeitet und immer ein offenes Ohr hat. Deswegen sind wir komplett zufrieden. Der Versand mit den Verschleißteilen klappt wunderbar und auch bei der Service-Hotline haben wir festgestellt, dass man sich unseren Fragen schnell widmet.“
Steffen Hein,
Geschäftsführer | AMS Alteno UG
Anlagenprofil:
MG-PRS 4001.20 + S880- Netto-Bearbeitungsfläche 4.000 x 2.000 mm
- Rohrbearbeitung bis 500 mm Durchmesser
- R5 Rotator für die Schweißnahtvorbereitung bis 50°
mit automatischer Kalibriereinheit - 2D-Plasmaschneiden
Nach der Sichtung der dort ausgestellten Schneidanlagen fiel die Entscheidung schnell auf MicroStep, wie Steffen Hein berichtet. Ausschlaggebend war das endlosdrehende Fasenaggregat, der MicroStep R5 Rotator, zur 3D-Bearbeitung von verschiedenen Materialien und Werkstücken. „Wir hatten uns außerdem mit dem Thema Rohrbearbeitung ein Alleinstellungsmerkmal in der Region herausgesucht. Bei Kjellberg haben wir dann Versuche durchgeführt, um zu sehen, ob es mit dem endlosdrehenden Fasenaggregat so funktioniert, wie wir uns das vorstellen.“ Es funktionierte, die Kaufentscheidung war gefallen. Seit Mitte 2017 hat die Firma AMS Alteno nun eine Plasmaschneidanlage der Baureihe MG von MicroStep im Einsatz mit der Technologie zur 3D-Bearbeitung von Blechen, Rohren und Profilen. Zudem entschied sich das Unternehmen für die Installation der ABP®-Technologie, mit der an bereits geschnittenen Bauteilen nachträglich Fasen zur Schweißnahtvorbereitung angebracht werden können.
Zeiteinsparung im Materialhandling um 30 Prozent, Kapazitäten noch frei
Die Investition hat sich für AMS Alteno gelohnt: Wo früher viele Teile auf verschiedenen Maschinen mit Scheren geschnitten, gestanzt und manuell bearbeitet wurden, wird heute der gesamte Auftrag an einer Maschine abgearbeitet. „Alleine bei den Handlingzeiten haben wir mit dem Brennautomaten Einsparungen von 30 Prozent.“ Bearbeitet wird beim Metall- und Anlagenbauer vorrangig Baustahl, aber auch Edelstahl und Alu-Riffelblech von 1,5 bis 60 mm Stärke – rund 50 Tonnen Material werden monatlich auf der Anlage vorbereitet. Sogar Kunden, die Laserteile anfragen, werden je nach Anforderung mit der Plasmaschneidanlage bedient. Betrieben wird die Anlage in zwei Schichten mit einem Auslastungsgrad von rund 70 Prozent. Kapazitäten, die auf dem Markt für Lohnzuschnitt frei werden und bereits angeboten werden.
Rund neun Monate nach der Inbetriebnahme der MG Plasmaschneidanlage fällt das Urteil von Steffen Hein durchwegs positiv aus: „Durch die Vielseitigkeit der Anlage können wir alles aus einer Hand anbieten. Wir haben bei MicroStep das Gefühl wir sind in guten Händen – mit denen kann man reden. Auch bei der Service-Hotline haben wir festgestellt, dass man sich unseren Fragen schnell widmet.“
DIE HIGHLIGHTS DER PLASMASCHNEIDANLAGE MG-PRS 4501.20 + S1200 IM ÜBERBLICK
Plasmaschneidanlage der Baureihe MG mit einer Arbeitsfläche von 4.500 x 2.000 mm
Die Baureihe MG ist ein Plasmaschneidsystem, das in Sachen Präzision, Leistungsfähigkeit und Zuverlässigkeit speziell für die Anforderungen der Industrie und des Mehrschichtbetriebs entwickelt wurde. „Wir betreiben die Anlage in zwei Schichten, rund 50 Tonnen Material werden monatlich mit der Anlage bearbeitet“, sagt Geschäftsführer Steffen Hein. Die Plasmaschneidanlage verfügt über eine Netto-Arbeitsfläche von 4.500 x 2.000 mm. Die energiesparende Sektionsabsaugung am CNC-Brennschneidtisch wird durch eine Absauganlage des Typs DFPRO 12 Cyclopeel von Donaldson gewährleistet. Als Plasmaquelle ist eine HiFocus 360i neo von Kjellberg mit automatischer Gaskonsole und Contour Cut Speed Technologie im Einsatz.
3D-Bearbeitung an Blechen, Rohren und Profilen mit dem MicroStep R5 Rotator
Ein entscheidendes Kriterium bei der Wahl des Schneidanlagenherstellers war für die Firma AMS Alteno UG die Technologie zur 3D-Bearbeitung der Werkstücke. Konfiguriert wurde die Schneidanlage mit dem MicroStep R5 Rotator, der Fasenschnitte bis zu 50° beispielsweise zur Schweißnahtvorbereitung ermöglicht – an Blechen, Rohren und Profilen. Mit dem endlosdrehenden Fasenaggregat können V-, X-, Y- oder K-Nähte ans Material angebracht werden. „Die Entscheidung fiel schnell auf MicroStep durch den endlosdrehenden Rotator“, betont Geschäftsführer Steffen Hein.
Mobile Rohrschneidvorrichtung RSV 30-500 zum Bearbeiten von Rohren und Profilen | Exakte Schneidergebnisse bei Profilen mit neuer Technologie von MicroStep
Ein weiterer bedeutender Punkt bei der Konfiguration der neuen CNC-Maschine war die Möglichkeit außer Flachmaterial auch Rohre zu bearbeiten. Mit diesem Alleinstellungsmerkmal punktet das Unternehmen nun in der Region. In das System integriert wurde eine mobile Rohrschneidvorrichtung, mit der Rohre bis 500 mm Durchmesser und einem Gewicht von bis zu 10.000 kg präzise bearbeitet werden können. Zudem wurde ein Schacht mit einer Breite von 880 mm im Brennschneidtisch implementiert, um flexible unterschiedliche Werkstücke schneiden und fasen zu können. Hochpräzise Ergebnisse bei der Profilbearbeitung erzielt das Unternehmen durch den Einsatz innovativer Technologie von MicroStep. Die Rohrschneidvorrichtung dreht das Profil in Position, ein am Portal installierter Laserscanner erfasst die Oberflächengeometrie im Schneidbereich des Werkstücks. Die 3D CAM-Software mCAM® kompensiert die produktionsbedingten Abweichungen zur Idealkontur, korrigiert die Parameter anhand des 3D-Scans und setzt dementsprechend die Schneidpfade, was zu einer signifikanten Verbesserung der Schneidqualität führt.
ABP®-Technologie für die nachträgliche Schweißnahtvorbereitung an geschnittenen Bauteilen
Die ABP®-Technologie von MicroStep wurde entwickelt, um auf einem Schneidsystem die nachträgliche Anbringung von Fasen zur Schweißnahtvorbereitung zu realisieren. Mittels des Multifunktions-Laserscanners, der auch bei der 3D-Erfassung der Profile zum Einsatz kommt, werden bereits geschnittene Bauteile eingescannt und flexible Fasen angebracht. Damit entfällt aufwendiges Materialhandling auf einem zusätzlichen (Roboter-)arbeitsplatz und es besteht die Möglichkeit auch bei höhere Materialstärken im Nachgang Schweißnahtvorbereitungen anzubringen.

ist Content Creator bei MicroStep Europa. Er hat jahrelange Erfahrung als Redakteur in den Bereichen Tageszeitung und im PR und lebt nun seine Leidenschaft für Wortakrobatik und ausführliche Recherche bei MicroStep aus. Er ist im ständigen Austausch mit unseren Technologieexperten und besucht für Interviews und Videos unsere Kunden vor Ort.
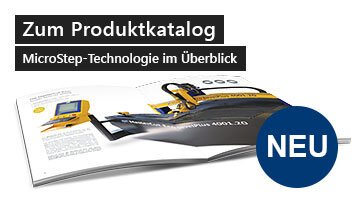
ERLEBEN SIE UNSERE ANLAGEN LIVE
im CompetenceCenter Süd oder Nord
- Alle vier Schneidtechnologien (Laser, Plasma, Autogen, Wasserstrahl)
- Innovative Automationssysteme
- Neuste Lösungen zum Biegen und Entgraten
- Industrie 4.0 Demofabrik
- Gut zu erreichen: im Süden und Norden Deutschlands
