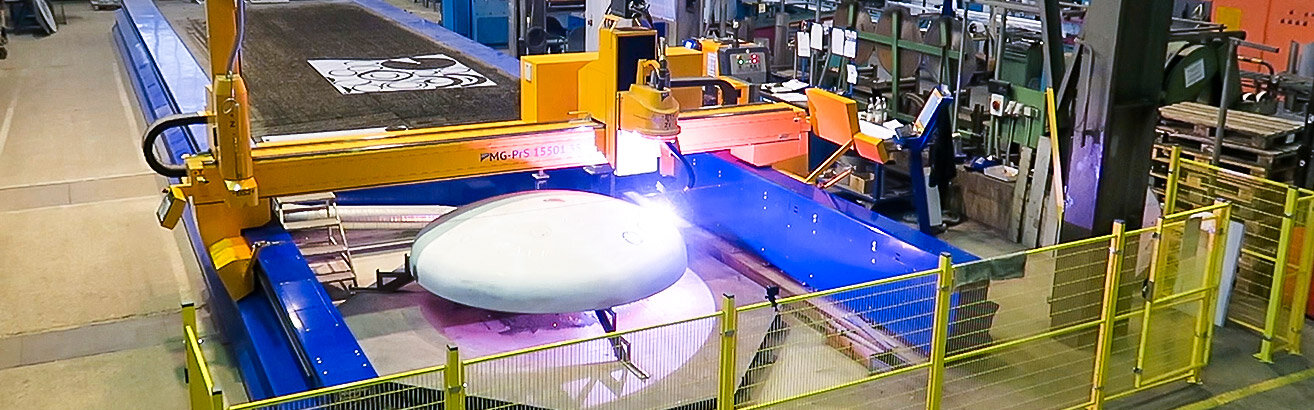
Ein Schneidsystem zur präzisen 3D-Bearbeitung von Flachmaterial und Behälterböden
Durchlaufzeit von eineinhalb Wochen auf einen Tag reduziert
Die GEA Brewery Systems GmbH in Kitzingen ist Spezialist für den Behälter- und Apparatebau und setzt auf ein kombiniertes Blech-Behälterbodenschneidcenter von MicroStep zur Produktion von kleinen Serien mit hohen Qualitätsstandards
Publiziert 08.04.2020 | Erich Wörishofer
Unternehmensprofil:

GEA Brewery Systems GmbH
Heinrich-Huppmann-Str. 197318 Kitzingen
Deutschland
Das international tätige Technologieunternehmen GEA ist einer der größten Systemanbieter für die nahrungsmittelverarbeitende Industrie und konzentriert sich auf Maschinen und Anlagen, Prozesstechnik und Komponenten. Am Standort in Kitzingen werden Behälter und Apparate für die Nahrungsmittel-, Pharmazie- oder Chemieindustrie gefertigt.
Die Baureihe MG bei der GEA Production Kitzingen wurde für präzise und flexible 3D-Bearbeitung von Blechen und Behälterböden ausgelegt. Der MicroStep R5 Rotator ermöglicht das Schneiden von Löchern, Konturen und Fasen an Flachmaterial und Klöpperböden.
Bei den Produkten der GEA Brewery Systems GmbH ist höchste Präzision elementar, das erwarten die Kunden von den Behältern und Apparaten des Systemanbieters für die nahrungsmittelverarbeitende Industrie. Dementsprechend sind Erfahrung, exaktes Arbeiten und moderne Maschinenlösungen bei der Fertigung gefragt. Auf Empfehlung von MicroStep entschied sich der Spezialist aus dem fränkischen Kitzingen für eine Plasmaschneidanlage der Baureihe MG zur 3D-Bearbeitung von Blechen und Behälterböden. Die Investition machte sich bezahlt: Die Durchlaufzeit bei der Herstellung von komplexen Behältern mit etlichen Stutzen hat sich von rund eineinhalb Wochen auf einen Tag reduziert. Für Eduard Sauter, Head of Production ein „riesen Benefit. Ich empfehle MicroStep bei unseren weiteren GEA Standorten, die ein ähnliches Produktportfolio haben.“
Die Behälter und Apparate, die die GEA Brewery Systems GmbH in Kitzingen für ihre Kunden baut, sind zum Teil wahre Giganten, die mit höchster Präzision und Hochtechnologie gefertigt werden. Die Produkte für die Prozessindustrie haben bis zu 70 Tonnen Leergewicht, bis zu 13 Meter Durchmesser und 17 Meter Länge. Sehr hohe Standards an Oberflächenrauigkeiten sowie höchste Genauigkeiten und enge Toleranzen sind gefragt, damit die Einzelanfertigungen passgenau eingebaut und eingesetzt werden können.
Die international tätige Unternehmensgruppe GEA ist einer der größten Systemanbieter für die nahrungsmittelverarbeitende Industrie. Im Jahr 2019 erwirtschaftete GEA einen Konzernumsatz von rund 4,9 Milliarden Euro. Am Standort in Kitzingen werden Behälter und Apparate für die Nahrungsmittel-, Pharmazie- oder Chemieindustrie gefertigt. Rund 240 ausnahmslos gelernte Fachkräfte produzieren hier mit modernsten Maschinen und viel Know-how auf dem 63.000 qm großen Betriebsgelände, davon entfallen 9.000 qm auf die Produktion. „Wir sind zuverlässiger Partner, was die Liefertreue verbunden mit Qualität angeht. Wir machen möglich, was der Kunde sich wünscht“, sagt Eduard Sauter, Head of Production in Kitzingen.
Nachfolger für Plasmaschneidanlage gesucht – 2D-Lasersystem für Bleche im Blick
Und diese Kunden verlangen eine immer schnellere Lieferung bei mindestens gleichbleibend hohen Qualitätsstandards. Um dies zu erreichen ist die GEA Gruppe immer auf der Suche nach neuer Technologie, die am besten mehrere Vorteile vereint: „Wir müssen jede Technologie für uns prüfen, doch nicht jede Technologie ist anwendbar – vor allem nicht in unserer Art von Produktion mit vielen Einzelanfertigungen. Es gibt am Markt Technologien, die die bisherigen Produktionsabläufe sicherer gestalten – hier geht es um Prozesssicherheit –, eine Steigerung der Qualität herbeiführen und wenn es zu einer absoluten Reduzierung der Durchlaufzeiten führt, dann ist das eine absolute Win-Situation für uns“, so Sauter. Unter diesen Gesichtspunkten war es 2015 an der Zeit, eine Plasmaschneidanlage auszutauschen. „Ich dachte Plasma ist ein alter Hut. Deswegen wollten wir einen CO2- oder einen Faserlaser“, blickt Eduard Sauter zurück. So wurden Investitionssumme und technische Möglichkeiten geprüft, der Mehrwert eines gewünschten 2D-Lasers für Bleche identifiziert. „Wir haben dann mit sehr vielen – auch namhaften – Herstellern gesprochen und uns Angebote geben und uns auch Lösungen vorstellen lassen.“ Die präsentierten Technologien trafen aber nicht genau die Wünsche der Bearbeitungsoptionen.

"Mit der aufwendigen manuellen Arbeit war die Durchlaufzeit, also die Produktionszeit mit Unterbrechungen, bei einem komplexen Behälterboden mit mehreren Stutzen bei eineinhalb bis zwei Wochen – heute sind wir bei einem Tag. Das ist ein riesen Benefit. Wenn wir eineinhalb Wochen schneller liefern können in unserem Geschäft – so kann es ausschlaggebend für eine Beauftragung sein. Ich empfehle MicroStep bei unseren weiteren GEA Standorten, die ein ähnliches Produktportfolio haben.“
Eduard Sauter (rechts),
Head of Production | GEA Brewery Systems GmbH
Anlagenprofil:
MG Baureihe- Netto-Bearbeitungsfläche 12.000 x 3.500 mm
- Bearbeitung von Behälterböden von 500 bis 3.500 mm Durchmesser
- Plasmarotator zur Schweißnahtvorbereitung bis 50° mit automatischer Kalibriereinheit und Behälterbodenbearbeitung mit automatischer Kalibriereinheit
- mScan-Technologie von MicroStep zur präzisen Erfassung und Bearbeitung von Behälterböden (Ermittlung der Oberfläche des Behälterbodens mit einem Laserscanner, Kompensation der produktionsbedingten Abweichungen zur Idealkontur, Korrektur der Parameter und exaktes Setzen der Schneidpfade anhand des 3D-Scans)
Beratung von MicroStep nach intensiver Analyse von Produktion und Portfolio
So gab Sauter der Plasmatechnologie eine Chance und wurde von MicroStep überzeugt. „Man sagte mir: Vieles was sie denken, dass sie mit dem Laser machen müssen, ist heutzutage auch mit moderner Plasmatechnologie möglich“, sagt Sauter. Sein Interesse war geweckt. MicroStep nahm sich Zeit und die Produktion genau unter die Lupe. „Wir haben die MicroStep-Spezialisten die Produktion besichtigen lassen, um zu evaluieren, welche Technologie uns anhand unseres Portfolios den meisten Benefit liefern würde.“ Auch die Bedenken bei der Plasmatechnologie in Sachen Lautstärke und Staubbelastung haben sich schnell zerschlagen. „Das ist für den industriellen Bereich absolut im grünen Bereich“, betont Eduard Sauter.
Kombinierte Plasmaschneidlösung für Behälterböden und Bleche statt Laserschneidanlage
Aus der anfänglichen 2D-Laseranlage für Flachmaterial wurde somit ein kombiniertes Blech-Behälterbodenbearbeitungszentrum für 3D-Schneidaufgaben. Die Entscheidung fiel auf die Baureihe MG, den multifunktionalen Plasma-Alleskönner von MicroStep: die Vorteile eines Rotators und die Möglichkeit Fasen an Behälterböden anzubringen überzeugten. Eine vergleichbare Laserlösung gab es nicht auf dem Markt. Die Entscheidung für die Plasmatechnologie erwies sich als sinnvoll: Denn die GEA Production Kitzingen hat keinen Bedarf an großen Serien, meist werden Materialstärken von 3 bis 15 mm bearbeitet aber auch viele stärkere. Um Lieferzeiten zu verkürzen muss im Ausnahmefall auch ein Trennschnitt an 90 mm dickem Material durchgeführt werden.
Seit Juni 2017 ist die Anlage nun in Betrieb. Flachmaterial auf einer Arbeitsfläche von 12.000 x 3.500 mm und Behälterböden mit einem Durchmesser bis zu 3.500 mm können bearbeitet werden. Der Großteil der Behälterboden hat einen Durchmesser von 500 bis 2.200 mm. Die Erfahrungen, die der Spezialist mit der neuen Technologie gemacht hat, sind positiv: „Die Art der Anlage macht auf mich den Eindruck, dass sie grundsolide ist. Ich empfehle MicroStep bei unseren weiteren GEA Standorten, die ein ähnliches Produktportfolio haben.“
Suche nach prozesssicherem System für höhere Qualität und kürzere Produktionszeit erfolgreich
Die anfängliche Suche nach einer Maschine, die prozesssicher arbeitet, die Qualität erhöht und die Produktionszeiten reduziert, hat sich für die GEA Production Kitzingen gelohnt. Vor allem die Hinzunahme der Technologie zur Bearbeitung von Behälterböden gestaltete sich als richtiger Weg. Dank der mScan-Technologie von MicroStep, die bei der Präzision im Behälterbodenbau Maßstäbe setzt, hat das fränkische Unternehmen keine Probleme mit den geforderten Toleranzen – zudem entfällt ein Großteil der extremen Handarbeit früherer Zeit.
Vorher musste ein umfangreicher Bearbeitungskatalog an jedem Behälterboden durchgeführt werden: Der Umfang wurde gezogen, Winkel eingeteilt, im Vier-Augen-Prinzip durch die Qualitätssicherung überprüft und dann mit manuellem Plasmaschneider die Aussparungen durchbrochen. Schweißkantenvorbereitungen, die im Behälterbau zwingend notwendig sind, wurden im Anschluss manuell vorgeschliffen. Je nach Anzahl der Stutzen, die in den Behälterboden eingebaut werden mussten, betrug auf diese Weise die Durchlaufzeit eineinhalb Wochen. Und solche komplexen Erzeugnisse mit bis zu 20 Stutzen sind keine Seltenheit. Nun entfallen viele der handwerklichen Vorgänge und das Materialhandling von Arbeitsplatz zu Arbeitsplatz – die Durchlaufzeit vom Auftrag bis zur Auslieferung reduzierte sich bei aufwendigen Produkten auf bis zu einen Tag. „Das ist ein riesen Benefit. Wenn wir eineinhalb Wochen schneller liefern können in unserem Geschäft – so kann es ausschlaggebend für eine Beauftragung sein“, freut sich Eduard Sauter, der seit 15 Jahren im Unternehmen tätig ist.
Für Sauter hat sich die Entscheidung für die neue Anlage mehr als bezahlt gemacht, das Fazit fällt positiv aus: „Das ist keine stand-alone-Maschine, man muss sie auch bedienen können. Auch wenn Fragen aufkommen, erreicht man schnell den Telefonsupport und dann wird das gelöst. Ich werbe innerhalb der GEA für diese Art der Maschine.“
DIE HIGHLIGHTS DER CNC-PLASMASCHNEIDANLAGE MG-PRS 15501.35 IM ÜBERBLICK
Plasmaschneidanlage zur 3D-Bearbeitung von Blechen und Behälterböden
Die Anlagenkonfiguration der Baureihe MG bei der GEA Production Kitzingen wurde für präzise und flexible 3D-Bearbeitung von Blechen und Behälterböden ausgelegt. Integriert wurde der MicroStep R5 Rotator – mit dem endlosdrehenden Fassenaggregat werden präzise und zuverlässig Schneidaufgaben zur Fasenanarbeitung beispielsweise für die Schweißnahtvorbereitung bis 45° am Flachmaterial durchgeführt. Als Plasmaquelle dient eine HiFocus 360i neo von Kjellberg mit automatischer Gaskonsole und Contour-Cut Speed Technologie, als Filteranlage ist ein Absaugsystem des Typs ZPF 9H von Teka mit einem zusätzlichen Funkenvorabscheider TK-FVS 7000 – 12000 im Einsatz. Für die exakte Wiederholparkeit der Arbeitsschritte sorgt die vollautomatische patentierte Kalibriereinheit ACTG®. Für die Kalibrierung bei der Behälterbodenbearbeitung wurde noch eine Scanner Calibration Station angebracht.
3D-Blechbearbeitung auf einer Netto-Arbeitsfläche von 12.000 x 3.500 mm
Bestandteil des MG Schneidsystems bei der Firma GEA ist ein CNC-Brennschneidtisch mit energiesparender Sektionsabsaugung zur Bearbeitung von Flachmaterial. Als Netto-Arbeitsfläche steht ein Ausmaß von 12.000 x 3.500 mm für großformatige Bleche zur Verfügung.
3D-Behälterbodenbearbeitung mit einem Durchmesser bis zu 3.500 mm
Als weiteres Element der Multifunktionsanlage ist ein Behälterbodentisch integriert. Auf diesem können mit dem Plasmarotator präzise Löcher und Konturen mit Fasen in Behälterböden mit einem Durchmesser von bis zu 3.500 mm angebracht werden.
Präzise Erfassung und Bearbeitung von Behälterböden mit der MicroStep mScan®-Technologie
Für die hochpräzise Bearbeitung der Behälterböden setzt die GEA Prodction Kitzingen auf die mScan-Technologie von MicroStep. Bei der MG Plasmaschneidanlage wurde ein Laserscanner integriert, der die Oberläche des Behälterbodens ermittelt. Dabei werden Behälterbodenhöhe, Behälterbodendurchmesser, Wölbungsradius und Eckradius erfasst. Die Geometriedaten werden in der Software mScan eingelesen, das System kompensiert die produktionsbedingten Abweichungen zur Idealkontur, korrigiert die Parameter anhand des 3D-Scans und setzt entsprechend die Schneidpfade. Der Einsatz dieser Technologie führt somit zu einer signifikanten Verbesserung der Schneidqualität bei der Bearbeitung der Werkstücke.
Umfangreiches Softwarepaket zur Steuerung und Überwachung der Produktionsprozesse
Außer der einzigartigen mScan®-Software verfügt die Anlage bei GEA über ein umfangreiches Softwarepaket, welches die einfache, intuitive Bedienung der Technologien ermöglicht und zusätzlich die Überwachung der Produktionsprozesse. So können unter anderem die Maschinendaten ausgewertet werden. Im Tool ausgelesen werden können auch Angaben zur Gesamtlaufzeit, Gesamtschnittlänge, Schneidzeiten, Schneidkosten oder auch die Verschleißteilausnutzung.

ist Content Creator bei MicroStep Europa. Er hat jahrelange Erfahrung als Redakteur in den Bereichen Tageszeitung und im PR und lebt nun seine Leidenschaft für Wortakrobatik und ausführliche Recherche bei MicroStep aus. Er ist im ständigen Austausch mit unseren Technologieexperten und besucht für Interviews und Videos unsere Kunden vor Ort.
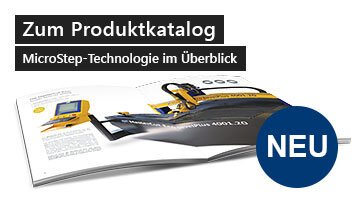
ERLEBEN SIE UNSERE ANLAGEN LIVE
im CompetenceCenter Süd oder Nord
- Alle vier Schneidtechnologien (Laser, Plasma, Autogen, Wasserstrahl)
- Innovative Automationssysteme
- Neuste Lösungen zum Biegen und Entgraten
- Industrie 4.0 Demofabrik
- Gut zu erreichen: im Süden und Norden Deutschlands
