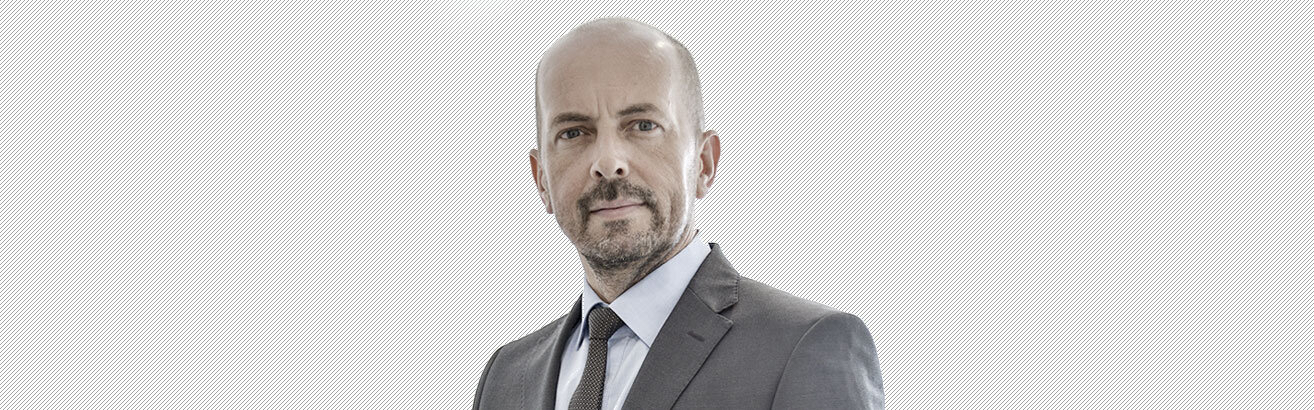
Igor Mikulina, Geschäftsführer der MicroStep Europa GmbH, blickt auf die Entwicklungen bei Doppelmayr zurück
„Bei Doppelmayr haben wir Pionierarbeit geleistet“
Igor Mikulina äußert sich im Interview zu den Besonderheiten und Herausforderungen der engen und langjährigen Zusammenarbeit mit dem Marktführer für Seilbahnbau
Publiziert 01.10.2015 | Erich Wörishofer
Herr Mikulina, wie ist der Kontakt zu Doppelmayr seinerzeit zustande gekommen?
Igor Mikulina: MicroStep war im Jahr 2000 auf der Handwerksmesse in München mit einem Stand vertreten – da ist Walter Eberle von Doppelmayr auf uns gestoßen. Wir sind gut ins Gespräch gekommen und er hat von Beginn an großes Interesse an unseren technologischen Lösungen gezeigt. Kurz darauf haben wir uns bei einem Termin in der damaligen Produktion von Doppelmayr gemeinsam ein Bild von den konkreten Anforderungen gemacht. Einen Großteil des Zuschnitts wickelte der bekannte Seilbahnbauer über einen externen Dienstleister ab. Und mit der Qualität des Zuschnitts, den man selbst vor Ort vornahm, war man alles andere als zufrieden – die verwendete Technologie war auch für damalige Verhältnisse alles andere als auf dem neusten Stand. Zwei Optionen lagen zu dieser Zeit bei Doppelmayr auf dem Tisch: Entweder eine grundlegende Modernisierung der eigenen Fertigungsmöglichkeiten inklusive des Bereichs Zuschnitt. Oder aber im Zuge der Modernisierung eine komplette Auslagerung des Zuschnitts an einen externen Dienstleister. Beides war allerdings nicht ohne weiteres möglich: Denn die Anforderungen von Doppelmayr waren für die damalige Zeit wirklich sehr speziell.
Welchen Anforderungen meinen Sie – können Sie ein paar konkrete Beispiele geben?
Mikulina: Es ging zum Beispiel um die Beschriftung von Teilen für die spätere Montage. Da diese nach dem Zuschnitt allesamt bestrahlt werden, kam eine damals gebräuchliche Tintenstrahlmarkierung nicht in Frage. Nadelmarkieren war noch viel zu langsam. Und Plasmamarkierungen bargen das Risiko von Gefügeveränderungen – diese mussten aber komplett ausgeschlossen werden, da das verbaute Material später beim Seilbahnbetrieb zum Teil extremen Kräften und immensen Temperataturschwankungen ausgesetzt ist.
Wir haben das Problem dann gelöst, indem wir eine Beschriftung per Wasserstrahl ermöglicht haben – und zwar ohne dass dafür ein Wassertisch oder eine spezielle Absaugung erforderlich wurde. Die eingesetzten Wassermengen sind so gering, dass diese selbst im Dauerbetrieb in die Hallenluft verdunsten. Das Ergebnis: Die Beschriftung hat genau die richtige Tiefe und ein thermischer Einfluss auf das Material existiert nicht. Das war revolutionär, zumal die Technik auf einem Portal mit weiteren Bearbeitungsoptionen kombiniert installiert wurde.
Von welchen weiteren Bearbeitungsoptionen sprechen Sie da?
Mikulina: Neben der Markierung mussten die Teile für eine spätere Montage auch mit Bohrlöchern unterschiedlicher Durchmesser und zum Teil sogar mit Gewinden versehen werden. Diese beiden Arbeiten erfolgen bei Doppelmayr noch vor dem eigentlichen Zuschnitt auf einer einzigen Portalanlage – diese Multifunktionsfähigkeit war zur damaligen Zeit einzigartig!
Konkret geht es dabei bei Doppelmayr um die Herstellung von Kopfplatten, die später verschraubt werden müssen.
Damals waren Löcher für Schraubverbindungen mit Plasma nicht präzise genug schneidbar bzw. musste das Schneidergebnis aufwändig nachgearbeitet werden – extrem kleine Löcher waren bei größeren Materialstärken schlichtweg nicht realisierbar. Mit unserer Lösung, direkt auf einer Portalanlage entsprechende Bohraggregate zu integrieren haben wir eine effiziente, höchst präzise und im Vergleich unglaublich schnelle Lösung gefunden. Und das Ganze mit einem automatischen Wechsel von bis zu 16 verschiedenen Werkzeugen zum Bohren und Gewinden!
Gab es auch Neuerungen beim eigentlichen Schneidprozess? Nachdem die Bleche mit Markierungen und Bohrungen versehen werden, kommt dann ja der Zuschnitt – oder?
Mikulina: Ja, genau so ist es. Und auch hier gibt es tatsächlich eine Besonderheit, die in dieser Form einzigartig ist. Dazu muss man sich folgendes vor Augen führen: Doppelmayr verarbeitet im Jahr rund 15.000 Tonnen Material. Bei dieser Menge macht es Sinn, den Rohstoff so günstig wie irgend möglich einzukaufen. Daher verarbeitet Doppelmayr an seiner Produktionsstätte im österreichischen Wolfurt Bleche mit sehr großen Abmessungen – 12 Meter Länge sind die Regel. Diese Bleche werden zunächst mit Markierungen und Bohrungen versehen und dann zwischengelagert. Je nach Kapazität in der Montage erfolgt nämlich erst später der Zuschnitt. Das bedeutet: Auf einer Anlage erfolgt Markieren und Bohren, auf zwei weiteren MicroStep-Anlagen erfolgt – häufig mit zeitlichem Verzug – der eigentliche Zuschnitt. Die Herausforderung: Wie ermittelt man auf den Anlagen, die für den Zuschnitt verantwortlich sind, die exakte Lage des Blechs sowie die exakte Lage der Bohrungen? Schließlich muss das Material ja in einer genau definierten Relation zu den angebrachten Bohrungen geschnitten werden. Unsere Lösung: Eine CCD-Kamera ermittelt die exakte Lage bestimmter Bohrlöcher auf dem Blech – diese dienen als Referenzpunkte, an denen sich dann die gewünschte Verschachtelung automatisch ausrichtet. Eine äußerst effiziente Lösung, die sowohl höchst präzise als auch mit relativ geringen Investitionskosten verbunden ist.
Wie bewerten Sie die Zusammenarbeit mit Doppelmayr?
Mikulina: Im Rückblick zählt unsere Zusammenarbeit mit Doppelmayr sicherlich zu den herausragenden Projekten, die wir um die Jahrtausendwende herum realisiert haben. Bei Doppelmayr haben wir damals eindrucksvoll bewiesen, dass wir in der Lage sind, komplexe multifunktionsfähige Anlagen zu bauen, die die Produktivität bei unseren Kunden um ein Vielfaches steigern und gleichzeitig die Qualität in der Bearbeitung auf ein Maximum heben. Diese damalige Pionierarbeit hat aus meiner Sicht entscheidend dazu beigetragen, dass die MicroStep Group heute Weltmarktführer im automatisierten Plasmaschneiden ist. Dass Doppelmayr seinen Weg nach 15 Jahren intensiver Zusammenarbeit mit uns als Partner im Bereich Zuschnitt auch künftig weitergeht, freut uns ungemein. Wir sind sehr dankbar für dieses große Vertrauen. Es zeigt, dass wir auf dem Markt nicht nur die besten technologischen Lösungen anbieten, sondern auch in der engen Betreuung unserer Kunden im Bereich Service, Support und After-Sales die Weichen richtig gestellt haben.

ist Content Creator bei MicroStep Europa. Er hat jahrelange Erfahrung als Redakteur in den Bereichen Tageszeitung und im PR und lebt nun seine Leidenschaft für Wortakrobatik und ausführliche Recherche bei MicroStep aus. Er ist im ständigen Austausch mit unseren Technologieexperten und besucht für Interviews und Videos unsere Kunden vor Ort.
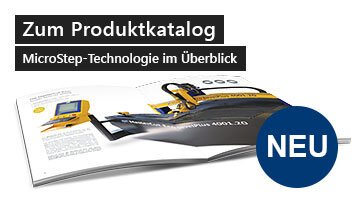
ERLEBEN SIE UNSERE ANLAGEN LIVE
im CompetenceCenter Süd oder Nord
- Alle vier Schneidtechnologien (Laser, Plasma, Autogen, Wasserstrahl)
- Innovative Automationssysteme
- Neuste Lösungen zum Biegen und Entgraten
- Industrie 4.0 Demofabrik
- Gut zu erreichen: im Süden und Norden Deutschlands
